industry insights
Featured Articles
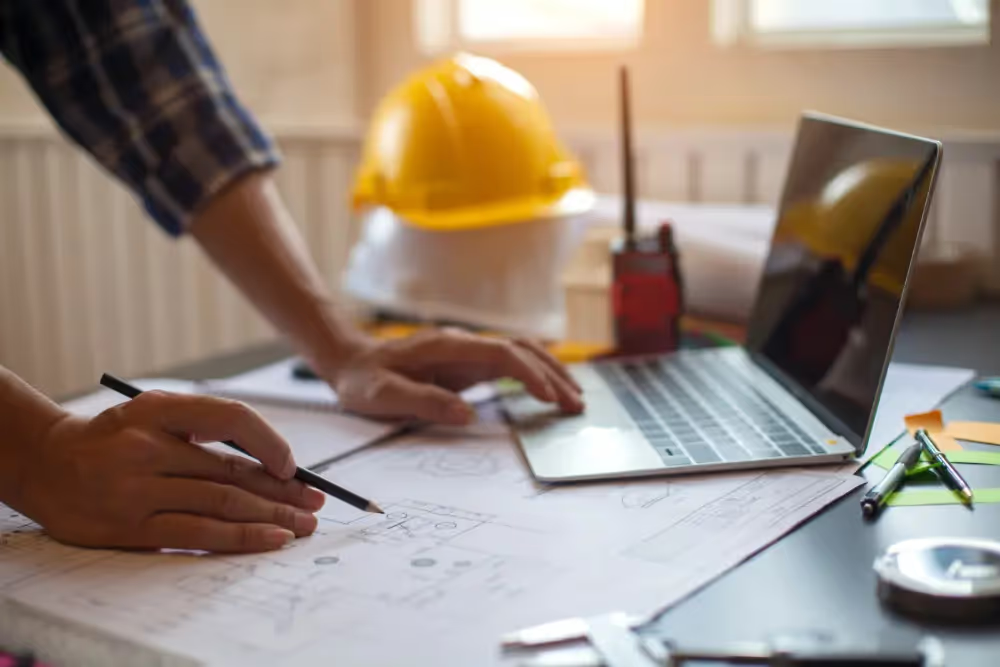
Why Do You Need Updated As-Builts on Your Next Project?
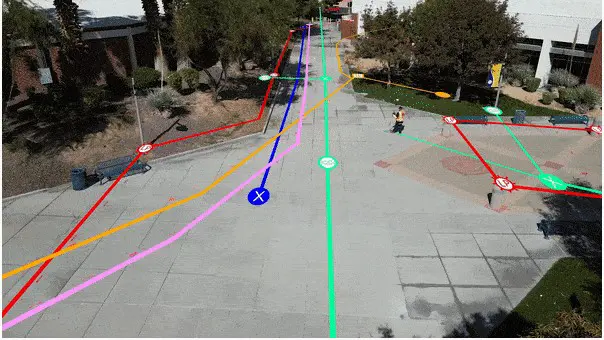
Is Utility Mapping Worth the Cost?
industry insights
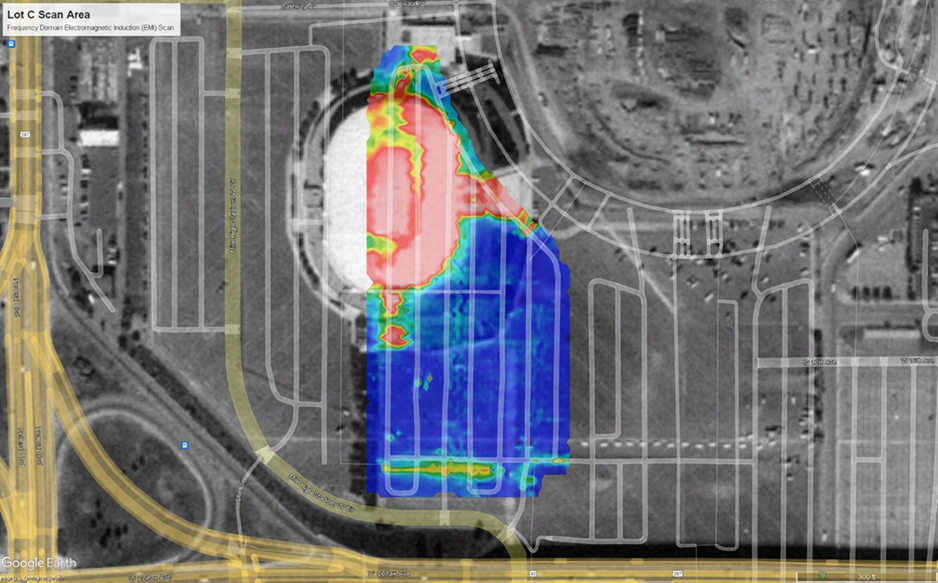
GPRS Helps Mile High Stadium Tackle Parking Lot Issue in Colorado
GPRS helped their client in Denver, Colorado tackle an issue that has been plaguing them for years. GPRS Project Manager Matthew Pudimott and Area Manager Ryan Shannon were tasked with scanning a seven-acre parking lot outside of Empower Field at Mile High, the home stadium of the Denver Broncos.
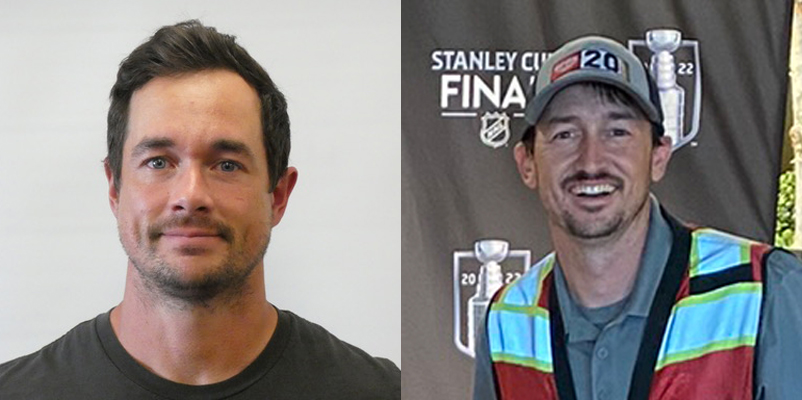
The pavement in the parking lot had been continuously cracking despite repeated attempts to repair it.
The parking lot was built where a former Denver arena once stood, McNichols Sports Arena was built in 1975. It held hundreds of concerts and was the home of the Denver Nuggets from its inaugural year until it officially closed in 1999. McNichols was also the home of the Colorado Avalanche for the final four years it was in operation. In January of 2000, it was demolished to make way for the construction of Empower Field at Mile High.
The initial purpose of the project was to search for underground tunnels or possible buried remains from the former arena. Pudimott and Shannon got to work and began scanning the area using ground penetrating radar (GPR).
The results were not as conclusive as they expected, so they implemented one of the main guidelines of Subsurface Investigation Methodology (SIM): the use of multiple complimentary technologies. They scanned the same area using electromagnetic (EM) locators and found what they were looking for.
“We initially were searching for voids, so we ran the GPR cart, took a whole day to get all the data together, and there was just no evidence of voids,” Pudimott explained. “We started to get worried that we actually weren't going to have meaningful results for the client, but the next day we ran EMI and that was kind of interesting. Same thing, collected the whole result, took a full day, and I was hoping we'd have something for him. And when the post processing data came back, I mean, it blew up.”
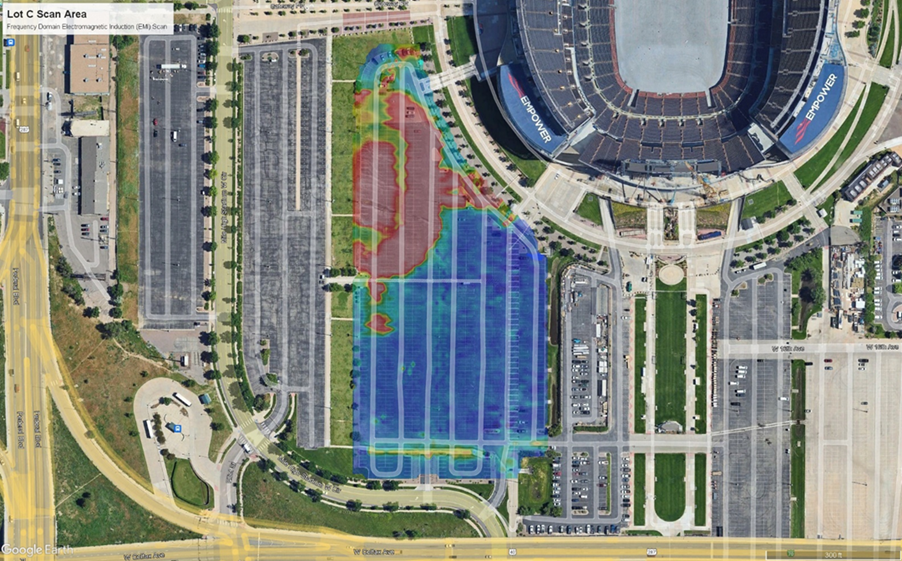
EM locators are used to detect electromagnetic signals radiating from metallic pipes and cables. Signals are created by the current flowing from the EM locator’s transmitter which travels along the conductive materials and back to the transmitter. Signals can be created and registered by the equipment when:
- The EM locator’s transmitter applies current to the pipe
- An electrical cable is live with current flow
- A conductive pipe acts as an antenna and re-radiates signals from stray electrical fields and communication transmissions
Once they saw the unusual results from the scan data, Shannon had an idea that allowed them to properly tell the data’s story.
“We definitely found a huge reaction and I knew that [McNichols] stadium was built there and that's probably the reason why we were scanning out there. So I just figured I would look at the old Google Earth data,” Shannon explained. “Sure enough, that popped up there, and then I thought to overlay that data over the historical data. It was most likely old foundations or possibly different backfill. The red, white, and orange reactions on the EMI typically indicate conductive reactions.”
Once Shannon overlayed aerial imagery from October of 1999, the EM data appeared to align with the footprint of the former arena.
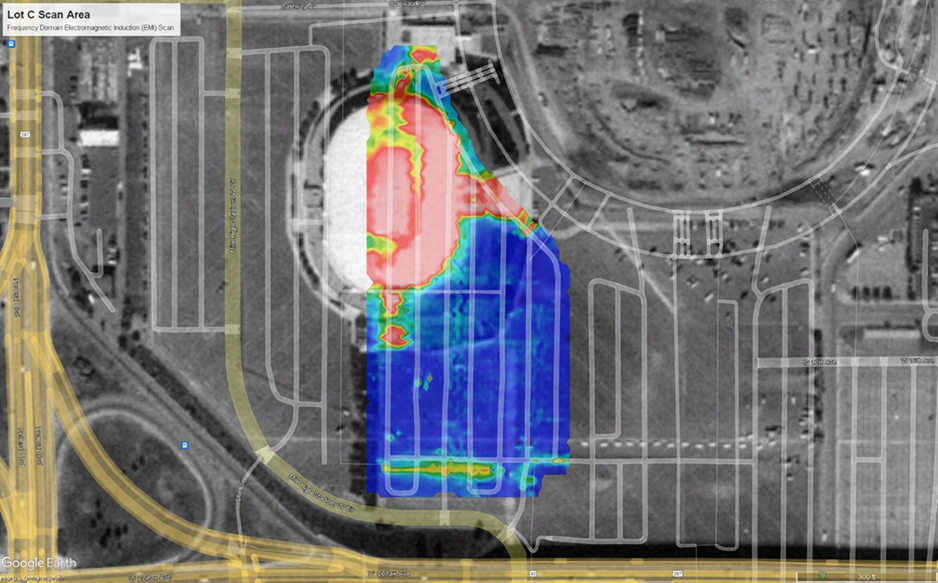
Despite being with GPRS for over a decade, Shannon couldn’t help but be amazed at the uniqueness of this job and the capabilities of utility locating equipment.
“This is definitely once-in-a-lifetime data, for sure,” Shannon said. “It’s not a common example, but a great example of what the EMI can do to get this data consistently. To find a building footprint like this? Yeah, I've never heard of this before or seen it before.”
With these results now at the client’s fingertips, they can make educated decisions on how to fix the parking lot without wasting more time and money on renovations year after year.
From stadiums to sewer lines, GPRS Intelligently Visualizes the Built World® to keep your projects on time, on budget, and safe.
What can we help you visualize?
FREQUENTLY ASKED QUESTIONS
What is Subsurface Investigation Methodology?
Subsurface Investigation Methodology (SIM) is a standard operating procedure and set of professional specifications that work as a guide for utility locating experts when scanning for buried utility lines. All GPRS Project Managers are required to achieve SIM 101 certification, which requires 80 hours of hands-on training in a classroom setting and 320 hours of mentorship in the field. For reference, the American Society for Nondestructive Testing’s (ASNT) minimum training recommendation includes eight hours for training and 60 hours practicing GPR to achieve NDT Level 1 certification in ground penetrating radar (GPR) scanning.
SIM requires the use of multiple, complementary technologies, like GPR scanning and electromagnetic (EM) locating, when locating buried utilities or scanning a concrete slab.
What are the Benefits of Underground Utility Mapping?
Having an updated and accurate map of your subsurface infrastructure reduces accidents, budget overruns, change orders, and project downtime caused by dangerous and costly subsurface damage.
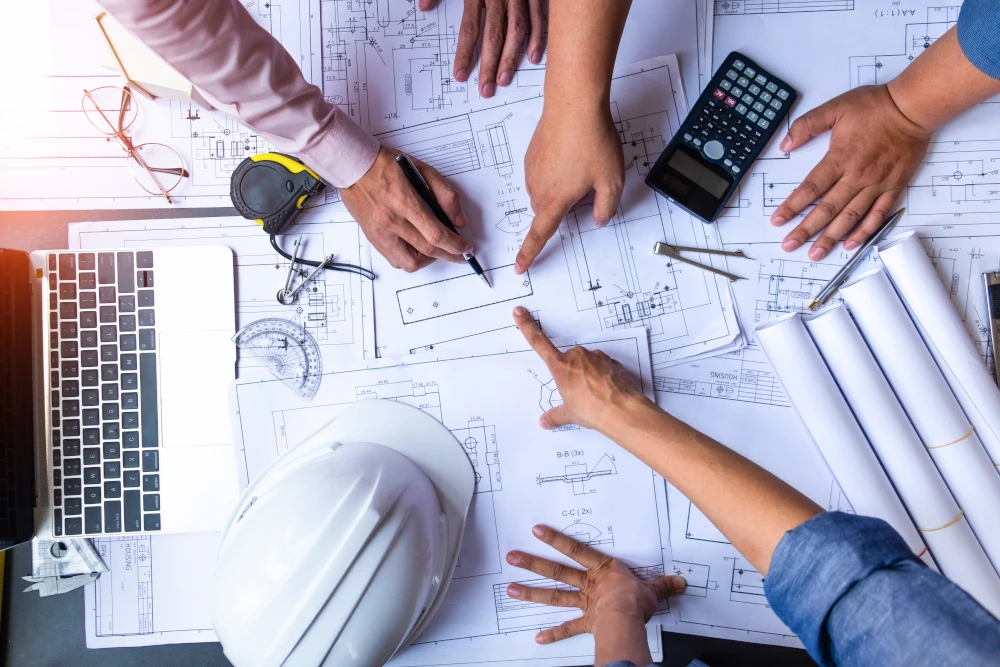
Survey of Construction Professionals Highlights the Need for Better Communications and Data Management
To better understand why and how construction technology decisions are made, Autodesk and FMI Corporation partnered to survey 600 construction professionals about how their teams spend time on the jobsite. The study revealed that the construction industry continues to suffer from outdated data and communication practices.
Autodesk provides software solutions for the architecture, engineering, and construction industries. FMI Corporation is a management consulting and investment firm focused exclusively on engineering, construction, infrastructure, and the built environment.
The data was compiled in an industry report titled Construction Disconnected. Key findings include:
1. Construction workers lose nearly two full working days each week resolving avoidable issues and searching for project information.
On average, each professional spends 14 hours weekly dealing with conflict, rework, and other tasks that detract from higher-priority activities. Respondents reported spending:
- Five and a half hours locating project data, such as revised drawings, material cut sheets, and other information relevant to the job.
- Nearly five hours resolving conflicts among stakeholders, including general contractors, owners, and subcontractors.
- Four hours managing rework, including identifying mistakes, assessing costs, and determining causes.
2. Nearly half of all rework stems from poor communication and inaccurate project data.
- Miscommunication and unreliable data account for 48% of all rework on U.S. construction sites.
- Respondents attributed 26% of rework to poor communication, citing unresponsiveness, ineffective collaboration, and the absence of a shared platform as the top causes.
- Another 22% was linked to poor project data, including incorrect information, limited access, and difficulty sharing updates across teams.
The article emphasizes that many contractors lack the tools needed to effectively manage every aspect of a construction project. Outdated communication and data collection methods fail to deliver centralized, real-time, and reliable information. This leads to inefficiencies, time-consuming tasks, and costly rework.
Reduce Rework and Improve Efficiency in Construction with GPRS and SiteMap
GPRS helps construction professionals overcome data and communication challenges by delivering accurate subsurface information, along with detailed above-ground architectural, structural, and MEP documentation.
All project data is centralized in SiteMap®, a GIS platform that integrates directly into project workflows to support informed decision-making and reduce costly surprises. SiteMap is the solution construction professionals need to centralize real-time site information and reduce rework.
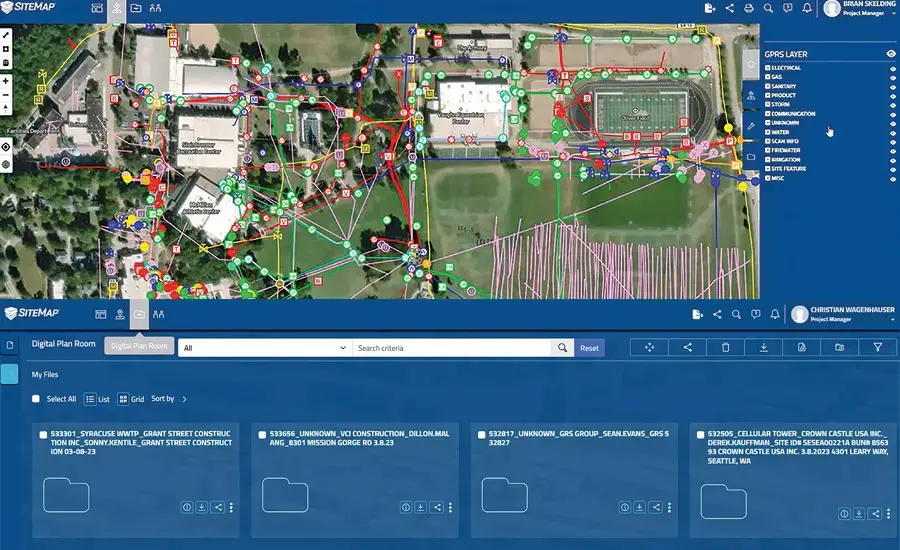
Suite of Aboveground and Below As-Built Solutions
GPRS provides a suite of services that include utility locating, concrete scanning, reality capture, video pipe inspection, and leak detection. These services are supported by advanced digital mapping and modeling solutions that help project teams mitigate risk, improve communication, and streamline construction across all phases.
Utility Locating Solutions
Fact: A utility strike occurs approximately every 90 seconds in the United States, resulting in thousands of injuries and deaths over the past 20 years. These strikes, often caused by inadequate utility locating before digging, cost communities millions of dollars annually according to a report from Michigan Technological University. In 2022 alone, over 163,000 utility strikes were reported according to the Common Ground Alliance.
Accurate utility locating is critical to preventing costly and dangerous utility strikes. GPRS uses ground-penetrating radar (GPR) and electromagnetic (EM) locators to identify underground utilities before construction or excavation. SIM-certified Project Managers mark the location and depth of both public and private utilities, including gas lines, electrical cables, telecommunication lines, sewer lines, and other buried infrastructure using standardized color codes and symbols.
GPRS utility locating provides verified field data, information that is critical during pre-construction planning and excavation. It ensures that crews avoid damaging existing utilities, which can lead to project delays, safety incidents, and regulatory fines.
SiteMap stores geolocated, layered, and securely shareable interactive utility maps, and PDF utility maps. Users can export utility data into drawings, maps, and models to enable seamless communication and collaboration across project teams.
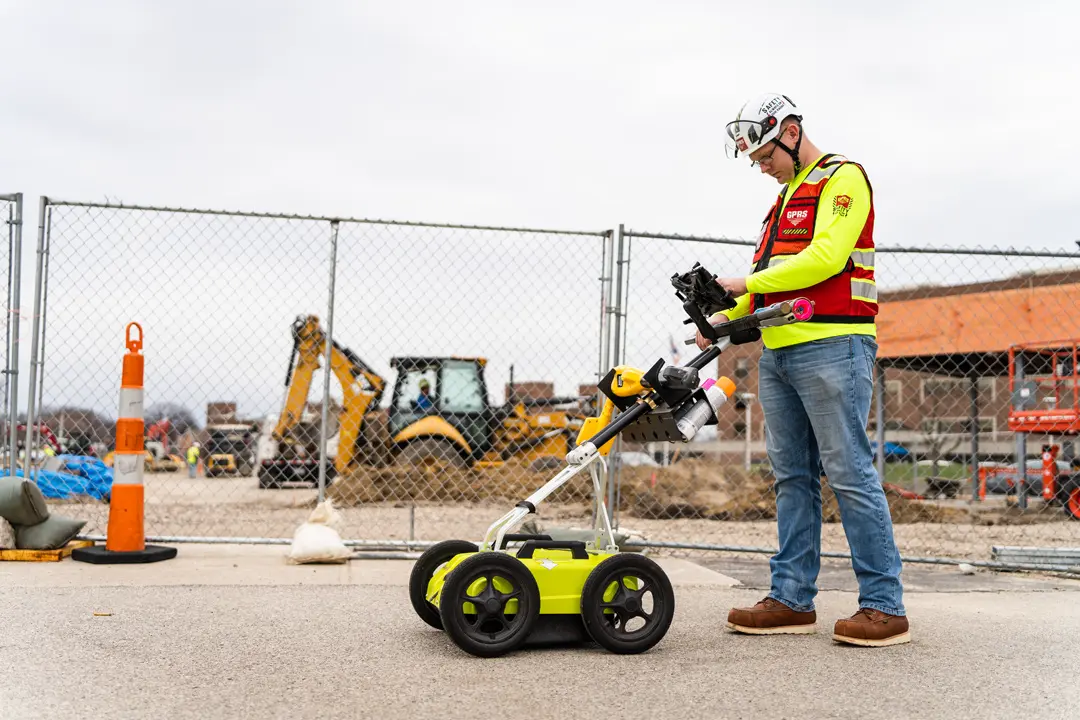
Concrete Scanning & Imaging Solutions
Fact: A single severed post-tension cable can cost upwards of $20,000 to repair/replace, and it can also lead to structural failure that endangers the lives of not only those completing the work, but anyone in the immediate area.
Before renovation, build-out, or excavation begins, existing concrete structures must be scanned to ensure safety and prevent damage. GPRS uses GPR to scan slabs, walls, and columns to detect embedded features such as rebar, post-tension cables, conduits, and potential voids. This concrete scanning service provides precise detection and mapping, helping teams avoid structural damage and maintain compliance with engineering standards.
SiteMap stores LiDAR-captured field markings, 2D CAD files, 3D models, and detailed analysis reports for easy access and integration.
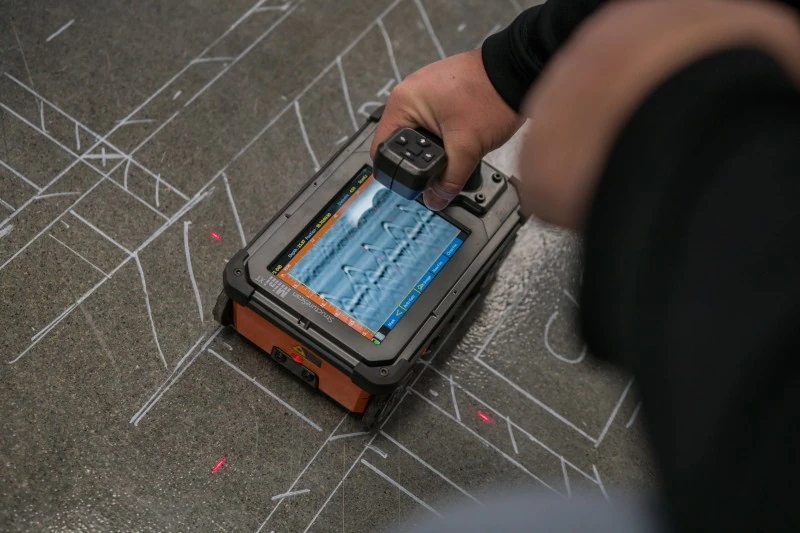
Reality Capture Solutions
Fact: A study from Dodge Data and Analytics, “Measuring the Impact of BIM on Complex Buildings,” found these results from AEC pros:
- 93% said BIM improved the quality and function of the final design
- 88% said BIM led to accelerated job completion
- 85% said BIM resulted in a reduction in the final construction cost
GPRS Reality Capture Services deliver precise as-built documentation of buildings and infrastructure using 3D laser scanning and photogrammetry. Deliverables include point clouds, 2D CAD drawings, 3D BIM models, mesh models, TruViews, and virtual tours that support accurate planning and construction.
Reality capture enhances collaboration by creating a digital twin of the physical site, accessible to all stakeholders. This shared access improves communication, supports better decision-making, and reduces errors. All reality capture data is uploaded to SiteMap, giving clients 24/7 access to verified documentation for planning, building, and facility management.
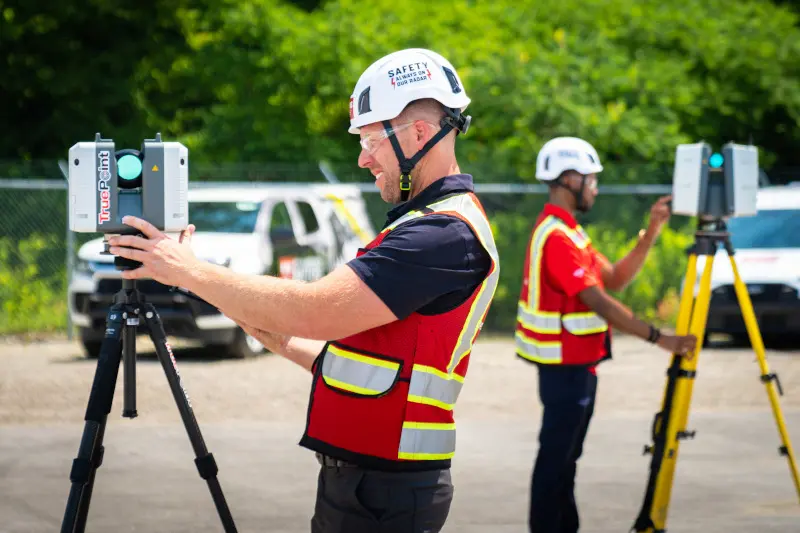
Video Pipe Inspection Solutions
Fact: Video pipe inspection can lead to substantial cost savings by identifying problems early, preventing them from escalating into expensive repairs. Some companies have reported a 90% reduction in maintenance costs after implementing video inspections according to 1st Choice Pro Services.
Most sewer pipe defects occur in buried infrastructure that cannot be inspected without excavation or specialized equipment. GPRS uses robotic crawlers and lateral launch CCTV cameras to inspect water and sewer systems. These video pipe inspections produce high-resolution video and defect mapping, documented in NASSCO-certified WinCan reports. Each defect is located, classified by severity, and integrated into a digital map.
SiteMap includes interactive sewer maps by segment, detailing entry and exit points, pipe condition, flow, length, material, images, and video. Hyperlinks to WinCan reports and footage allow clients to easily locate and assess sewer line conditions and defects.
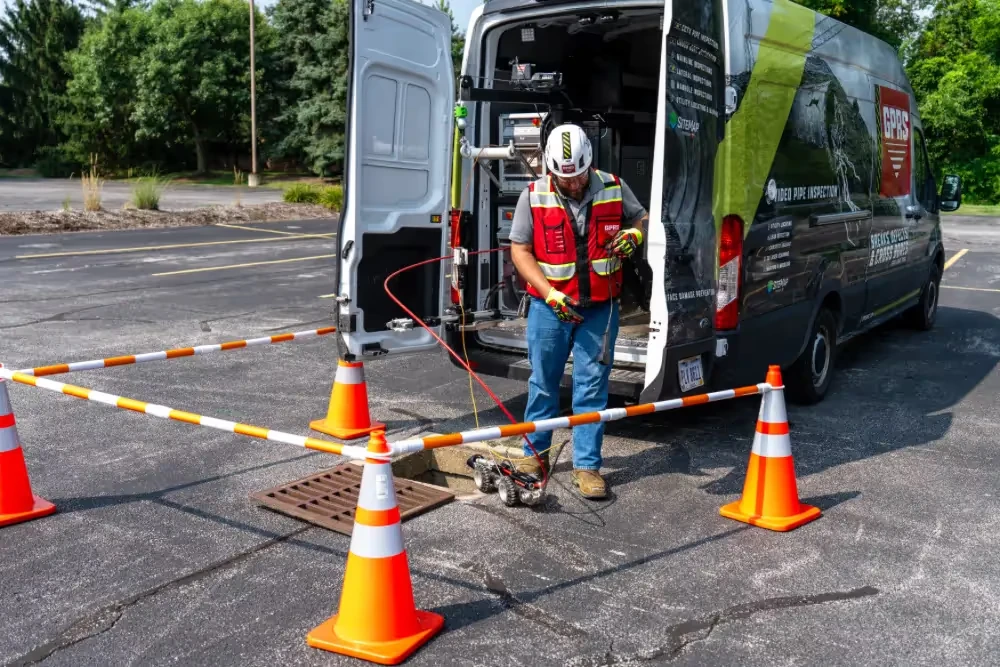
Leak Detection Solutions
Fact: According to the Report Card for America’s Infrastructure, 6 billion gallons of treated water are lost daily to untreated leaks. 2.5 trillion gallons of water are lost annually to pipe defects. That's enough to fill 3.75 million Olympic-sized swimming pools.
Undetected water leaks can cause extensive damage to structures and utilities. GPRS uses acoustic and tracer gas technologies to locate leaks in pressurized water systems without excavation. These methods allow technicians to pinpoint leak sources quickly and accurately.
GPRS leak detection services provides detailed reports and recommendations to help clients resolve issues efficiently and minimize disruption.
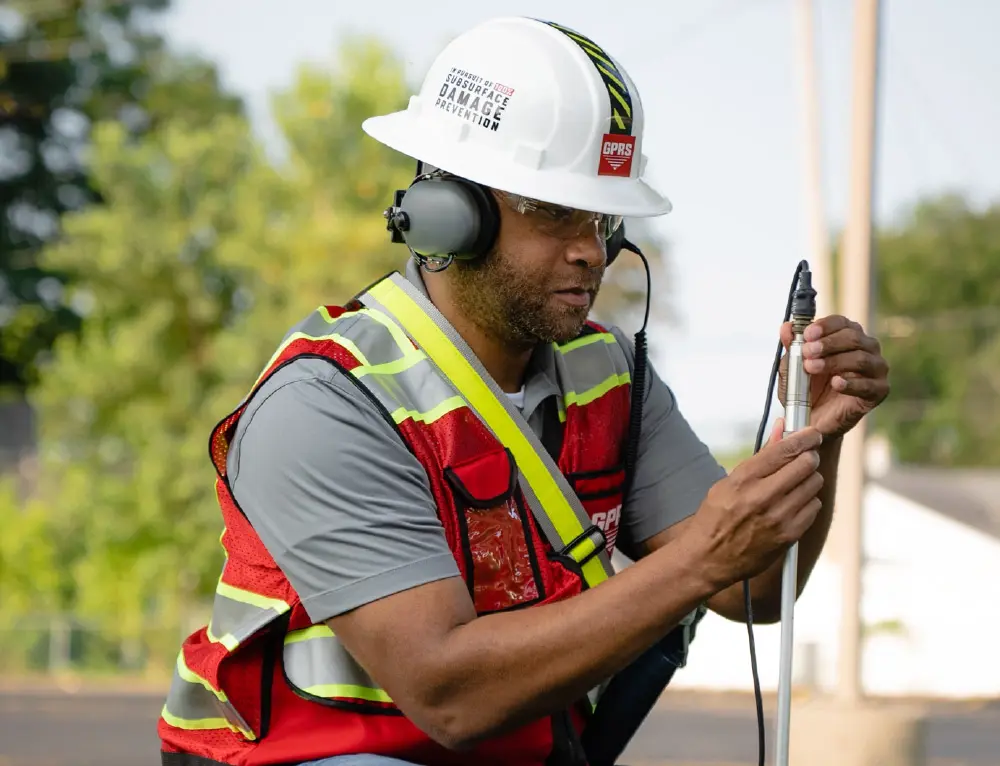
Data Management Solutions: GPRS SiteMap GIS Platform
To unify and deliver the data collected through its services, GPRS developed the SiteMap GIS platform. This cloud-based system stores and visualizes utility, concrete, structural, architectural, MEP system information and VPI reports in a centralized, interactive software. SiteMap allows users to access accurate site information from any device, at any time.
The platform supports project planning, risk management, and compliance documentation. It integrates with CAD and BIM software, enabling seamless data exchange between field and office. SiteMap also includes tools for annotation, measurement, and version control, ensuring that teams always work from the most current information.
By consolidating data into a single source of truth, SiteMap eliminates the confusion and inefficiencies caused by fragmented communication. It empowers project teams to collaborate more effectively, reduce rework, and deliver projects on time and within budget.
How can GPRS help you centralize site data and reduce rework?
Click here to schedule a SiteMap demonstration.
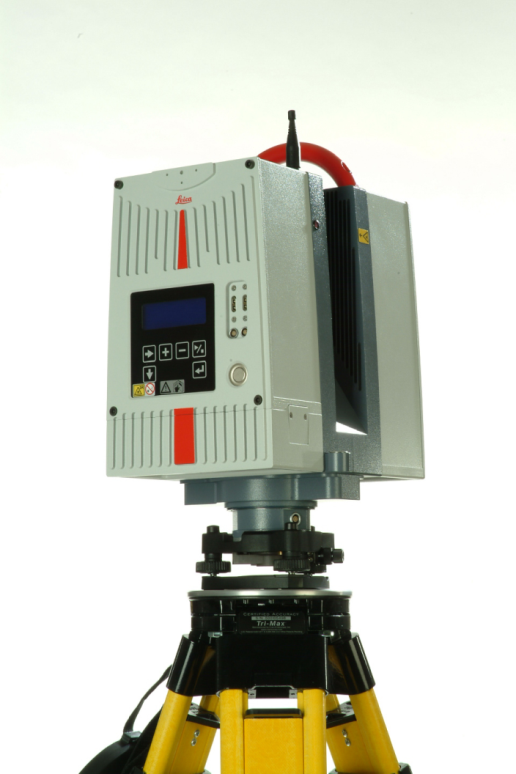
The History of 3D Laser Scanning Technology
From early LiDAR experiments to today’s precise BIM modeling, discover how 3D laser scanning evolved into a crucial element of architecture, engineering and construction
Before 3D laser scanning existed, building drawings were created through a meticulous and manual process that relied heavily on human skill, precision, and time. Surveyors and draftsmen would physically walk through a building or site, using tape measures and levels to manually record dimensions. Rough sketches were made on-site in field notebooks. Drawings were then created at standard architectural scales using graph paper and drafting tools. Once finalized, they were reproduced using blueprint machines. Physical copies were stored in archives and shared among architects, engineers, and contractors. Manual building measurements were often prone to human error, especially when dealing with irregular or hard-to-reach areas, and the process was typically slow and time-consuming.
The Early Days of 3D Laser Scanning
According to the "Timeline of 3D Laser Scanners | By Scantech International," in the 1960s, 3D laser scanning technology was in its infancy and primarily used for experimental purposes to explore how lasers could be applied to capture the profile of surfaces. These early systems used lights, projectors, and cameras to scan objects, but they were extremely slow and produced low accuracy results due to the limitations of the technology. The main goal during this period was to develop a method for automated spatial data collection.
The initial 3D laser scanners were large and bulky, often the size of a desk or small cabinet due to their heavy optical components, separate computing units, and manual setup requirements. These systems were typically mounted in fixed positions and used in labs or field stations, reflecting the technological limitations of the time. These scanners laid the groundwork for what would become a transformative technology.
By the 1980s, 3D laser scanners were still large, stationary, and in the early stages of development. They operated slowly, often taking minutes or hours to scan a single object, and produced low-resolution point clouds that lacked fine detail. While relatively accurate for their time, these systems were limited by computing power and sensor technology, requiring substantial post-processing on powerful workstations to make the data usable.
Military and Scientific Roots
Laser technology saw significant growth in the 1980s, particularly in military and scientific research. As detailed in Robert W. Seidel’s 1987 article "From Glow to Flow: A History of Military Laser Research and Development", scientists used early laser systems for measuring distances, terrain analysis, and geological surveys, to help understand landforms and surface features.
Laser scanners also played a role in space science, helping measure distances to celestial bodies and satellites. In the military, laser scanners were used for rangefinding, providing precise distance measurements for artillery, missile guidance, and battlefield awareness. They were also explored for laser-based radar systems used in aerospace and submarine warfare.
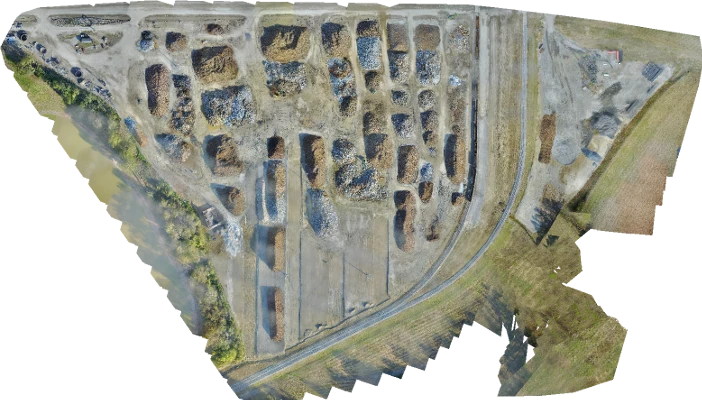
Cyra Technologies Introduces Cyrax
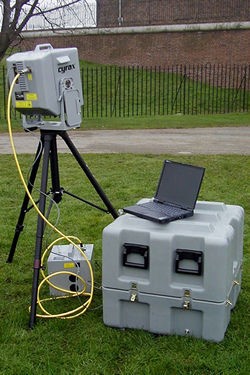
Geoffrey Jacobs wrote about how terrestrial laser scanning gained more traction in the 1990s in The Early Days of 3D Scanning.
Cyra Technologies was founded in 1993 by Ben Kacyra with the goal of developing a high-precision 3D laser scanner. The company introduced Cyrax, one of the first commercially available laser scanners specifically designed for surveying and engineering applications.
The Cyrax 3D laser scanner helped to address the "as-built documentation problem” in industrial plant retrofits. Traditional measurement methods were slow, prone to errors, and sometimes hazardous. Cyrax offered a faster, safer, and more accurate alternative.
The Cyrax system featured advanced components, including a microchip laser from MIT Lincoln Labs and nanosecond timing electronics from Los Alamos National Lab, with Cyra Technologies securing exclusive licenses for both.
Designed as a portable unit powered by a battery and a laptop, it weighed approximately 88 pounds. The scanner could capture data at 1,200 points per second within a 40° x 40° field of view and had a range of up to 50 meters against a flat white surface. Its success relied on precise time-of-flight measurements, requiring picosecond-level timing to detect laser reflections from nearby objects. These innovations gave Cyra a strong proprietary position in the emerging 3D laser scanning market.
Cyra Technologies faced a major hurdle when existing CAD software couldn’t handle the massive point cloud data from its scanner. With guidance from UC Berkeley’s Carlo Sequin, the company shifted to a computer graphics-based approach and developed its own software, Computer Graphics Perception (CGP), gaining a competitive edge as no similar solution existed at the time.
Chevron Field Testing the Cyrax
Chevron was among the early beta testers. The company used the Cyrax laser scanner in oil and gas fields in Kazakhstan. The purpose of this test was to evaluate how well the Cyrax system could capture detailed spatial data of industrial infrastructure.
The Cyrax scanner produced both camera images and point cloud data of vessels and other equipment in the field. This allowed for precise digital representations of the physical environment. The point cloud data helped Chevron create accurate as-built models of the site, which were essential for planning retrofits, maintenance, and safety assessments.
By using 3D laser scanning instead of manual measurements, Chevron reduced the need for personnel to enter potentially hazardous areas, improving safety, and speeding up data collection.
Leica Geosystems Acquired Cyra Technologies
In 2001, Cyra Technologies was acquired by Leica Geosystems, which rebranded the Cyrax as the HDS 2400. This marked the beginning of widespread adoption of 3D laser scanning in both industrial and civil engineering sectors.
Over the next decade, scanners became more compact, faster, and more accurate, with improved range and data quality. Leica introduced new 3D laser scanners like the HDS 2500 (2002) and HDS 3000 (2004), which increased scanning speed, accuracy, and field of view. By 2009, the Leica P20 could capture 1 million points per second, drastically reducing scan times.
Software platforms like Leica Cyclone and Autodesk ReCap also began to streamline point cloud processing and integration with CAD workflows, making reality capture technology more accessible to engineers, architects, and surveyors.
New Companies and Portable Scanners
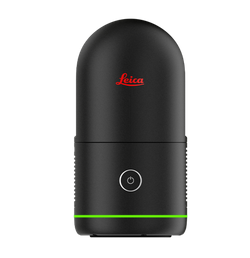
Other companies also played major roles in advancing the 3D laser scanning market. FARO Technologies introduced the FARO Focus series, which brought portability and ease of use to the forefront; Trimble entered the market with high-precision scanners tailored for construction and geospatial applications; and RIEGL developed high-performance LiDAR systems known for their speed and accuracy, especially in airborne and mobile mapping.
By the 2010s, the introduction of mobile mapping systems like the NavVis VLX and handheld scanners, such as the Leica BLK360 and FARO’s handheld Freestyle, made the technology more accessible and easier to use for a wider range of people and industries.
Released in 2018, the Leica RTC360, is capable of capturing up to 2 million points per second, with a range of up to 130 meters, and features VIS technology for automatic in-field scan registration and HDR imaging for detailed point clouds in under two minutes.
SLAM and the Next Generation of Scanning
The integration of SLAM technology enabled real-time mapping in complex environments such as construction sites and complex facilities.
SLAM (Simultaneous Localization and Mapping) is a method used to create a digital map of a space while simultaneously tracking the scanner’s position within it. In simple terms, localization determines where the scanner is, while mapping builds a layout of the environment. In 3D scanning, SLAM uses a LiDAR sensor to monitor the scanner’s movement and position as it moves through an area. This data allows the software to accurately place and align the scanned information, known as a point cloud, within the digital map.
Recent Advances in 3D Laser Scan Technology
From 2020 to 2025, 3D laser scanning technology has advanced rapidly, driven by innovations in hardware, software, and integration across industries. Scanners have become significantly smaller, faster, and more accurate, with many systems now offering real-time data capture and cloud-based workflows.
According to AVEVA’s March 2025 article “The Future of Reality Capture: What’s Next for Laser Scanning?”, the market size for laser scanning surpassed $3 billion in 2020 and is projected to reach $16.66 billion by 2030.
This growth is fueled by several trends. First, the technology is maturing, becoming more powerful, user-friendly, and affordable. Second, the need to modernize aging infrastructure, industrial plants, and other built environments is becoming increasingly urgent as many facilities face structural wear, outdated systems, and rising safety and efficiency demands.
3D laser scanning offers a powerful solution by capturing highly accurate, detailed digital representations of existing buildings and sites quickly and safely. These scans enable engineers and facility managers to create precise “as-built” models, streamline renovation planning, reduce downtime, and improve safety. As industries push toward modernization and sustainability, 3D laser scanning is becoming an essential tool for informed decision-making and long-term resilience.
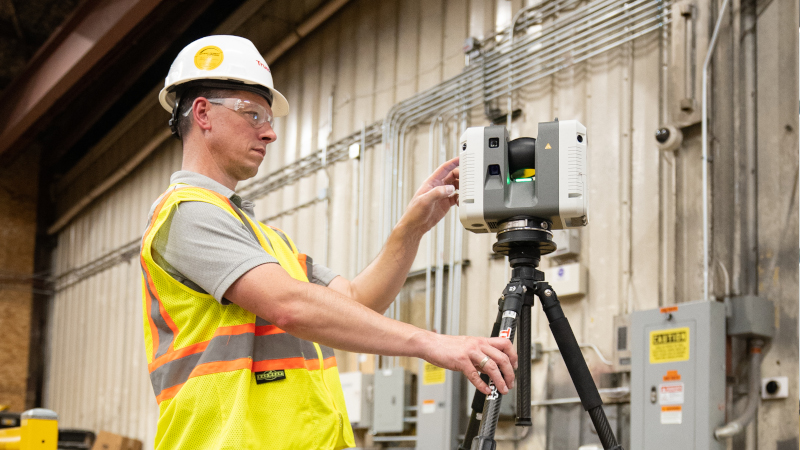
GPRS 3D Laser Scanning Services
GPRS is a leading 3D laser scanning company in the United States, helping clients to successfully complete their most complex architecture, engineering and construction projects. We've been providing reality capture services and excellent customer service for over 2 decades.
GPRS’ elite team of Project Managers efficiently 3D laser scans the exterior and interior of each site with professional-grade Leica laser scanners, capturing the exact layout, dimensions, and locations of your specific project requirements, such as architectural, structural, and MEP features, walls, windows, doors, stairs, roof, railings, exposed columns, beams, equipment, piping, ducts, and more.
Our Mapping & Modeling Team registers and processes the point cloud, removing noise and setting the coordinate system to provide the most precise measurements. Data is then compiled into custom 2D CAD drawings and 3D BIM models and delivered via SiteMap®. SiteMap® is GPRS’ secure GIS platform that delivers point cloud data, 2D CAD drawings and 3D BIM models, giving clients 24/7 access to verified as-built documentation to help them plan, build, and manage better.
What can we help you visualize?
Frequently Asked Questions
How has 3D laser scanning evolved in construction?
In the 1960s, 3D laser scanning technology was in its infancy and primarily used for experimental purposes to explore how lasers could be applied to capture the profile of surfaces. These early systems used lights, projectors, and cameras to scan objects, but they were extremely slow and produced low accuracy results due to the limitations of the technology. Laser technology saw significant growth in the 1980s, particularly in military and scientific research. By the 1990s, LiDAR (Light Detection and Ranging) and ground-based laser scanners became more available and began to integrate with CAD software for design, engineering, and the creation of 2D and 3D models. The first commercial scanners emerged in the early 1990s, improving accuracy and adoption in various industries, such as construction and manufacturing.
Why is 3D laser scanning important in modern construction?
It provides highly accurate, real-world data for design, renovation, and facility management, reducing errors, saving time, and improving coordination across trades through tools like BIM (Building Information Modeling).
What are the benefits of 3D laser scanning?
- Fast, Accurate Data Collection: A single laser scan captures millions of 3D data points per second, providing incredibly rich detail of a building or project site. Datasets are dimensionally accurate, measurable and shareable, expediting project planning and execution.
- Eliminates Revisits and Disruption: Sites are captured in high detail the first time, eliminating the need for return visits. High speed data collection expedites projects that require minimal disruption.
- Reduces Costs and Change Orders: Accurate design plans are produced from the start expediting field work and reducing change orders, delays and costs.
- Safe and Non-Contact: 3D laser scanners collect data on tripods from a distance in hard-to-reach or hazardous locations, keeping workers out of harm’s way. The non-intrusive nature keeps historic sites and artifacts untouched.
- Improves Communication: Communication is improved, teams can discuss plans while each has access to the same information, creating a more dynamic working environment.
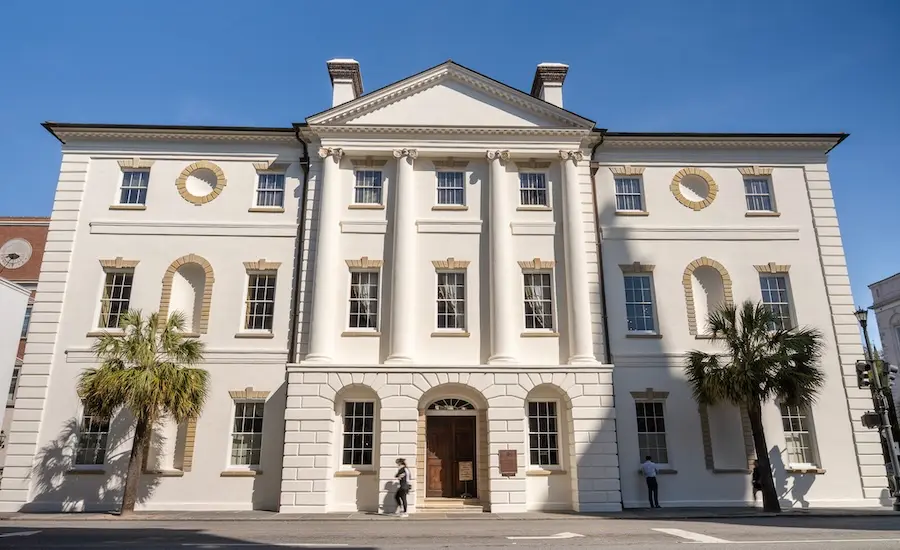
Charleston County Courthouse Undergoes $2.5M Restoration
One of Charleston, South Carolina’s famed “Four Corners of Law” was recently restored to its former glory.
The nearly 275-year-old Charleston County Courthouse underwent extensive stucco repair, waterproofing and masonry work as part of a roughly $2.5-million restoration that took 13 months and was completed in February. According to an article in Engineering News-Record, Greensboro, N.C.-based restoration contractor WxTite oversaw the work and even sourced period brick from a nearby project via Facebook Marketplace.
Constructed in 1753 at the intersection of Broad and Meeting Streets, the courthouse joins the other three buildings located at the intersection and representing the “Four Corners of Law”: municipal, county, federal, and ecclesiastical (church law).
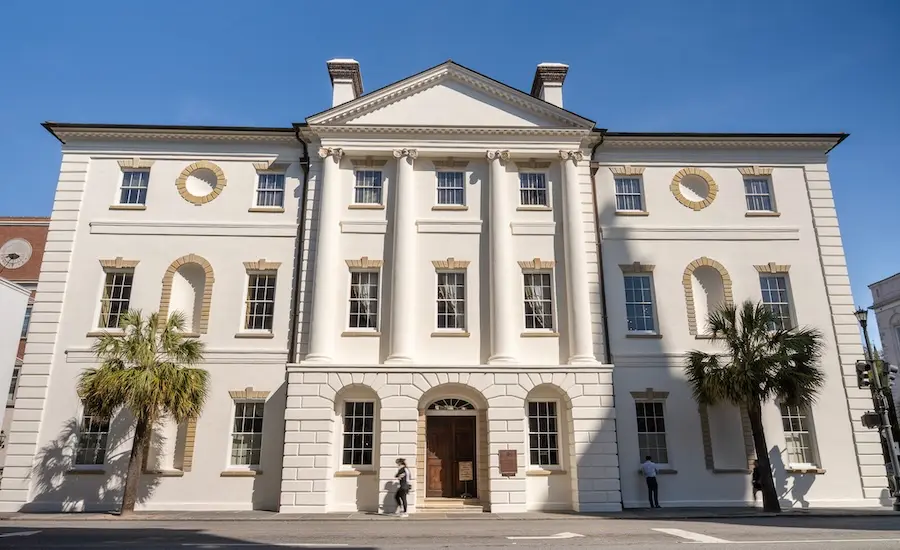
The other three “Corners” are Charleston City Hall, the U.S. Post Office and Courthouse, and St. Michael’s Episcopal Church. According to the Library of Congress, the nickname for the four buildings is believed to have been coined by Robert Ripley, the name and brains behind the Believe It or Not! franchise.
The county courthouse was originally used as a statehouse for the British Royal government for the South Carolina colony. It was partially destroyed in a fire in 1788, but was reconstructed with a third-floor addition and update in 1792.
The courthouse underwent numerous other changes and additions over the decades, before being restored to its historical 1792 Neoclassical appearance in 2001. It currently houses the Charleston County Probate Court.
When WxTite began its work, the courthouse was suffering from extensive stucco delamination, water intrusion, and other issues associated with its advanced age.
“Part of the process of figuring out how to restore this building, it was trying to figure out what has been done in the past,” WxTite Regional Manager Jamie Donaldson said in a video the company released about the restoration project. “That was a big part of our project was trying to figure out what was done, why they did it, how they did it, what they messed up during the process of the original renovation. Because the reason we’re here is because it wasn’t done perfectly, and our goal is to do this renovation perfectly.”
To address the water intrusion, the project team removed bluestone pavers around the building to install subgrade waterproofing installation. The pavers were then returned to their exact previous locations.
700 s.f. of stone surfaces were carefully repaired and cleaned to bring the exterior of the courthouse back to life. And all 83 of the building’s fenestrations – windows, doors and other openings – were restored to preserve the architectural uniqueness of the structure.
To help protect the courthouse from Mother Nature, 3,000 new hurricane anchors were installed.
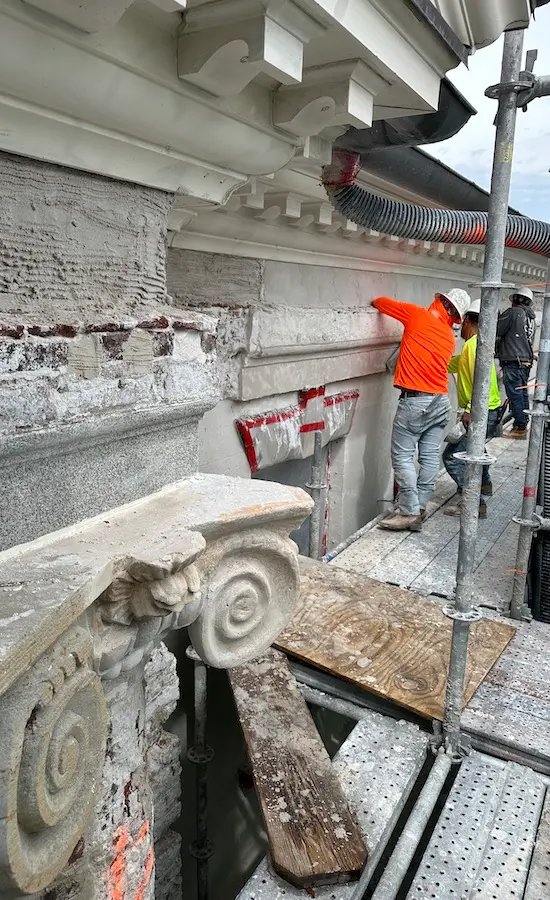
“We had a lot of assumptions about what needed to be done,” said WxTite Superintendent Cole Anderson. “But until we really started with the demolition portion of the stucco, we didn’t know how intense the brick repair was going to need to be. It was a lot of kind of opening things up to find out what depth of repair would be needed.”
Donaldson told ENR that the restoration project presented different challenges throughout the project lifecycle – but safety remained of paramount concern from the first day to the final day on-site.
“It’s a famous, busy intersection, arguably one of the busiest intersections in Charleston,” he explained. “Keeping everybody safe was paramount with what we were having to do out there, and still allowing the courthouse to be open and operational during the whole construction.”
At GPRS, safety is always on our radar. We’re committed to helping you ensure the safety of every project you undertake. Whether you’re restoring a historic structure, building a new facility, or managing the buried infrastructure on a site, we’re with you every step of the way – providing solutions to your problems from initial planning to O&M with our subsurface damage prevention, existing conditions documentation, and construction & facilities project management services.
GPRS Intelligently Visualizes The Built World® to keep your projects on time, on budget, and safe.
What can we help you visualize?
Frequently Asked Questions
Does GPRS Perform S.U.E. Work?
No, we do not. We use SUE Level 2-equivalent methodology and equipment to locate underground utilities with an accuracy rate of 99.8%. While we don’t conduct SUE work ourselves, our services allow a SUE Level 1 investigation to be performed more efficiently, eliminating the need to waste thousands of dollars on exploratory potholing.
What Type of Informational Output is Provided When GPRS Locates Utilities for Me?
Our Project Managers flag and paint our findings directly on the surface. This method of communication is the most accurate form of marking when excavation is expected to commence within a few days of service.
GPRS also uses a global positioning system (GPS) to collect data points of findings. We use this data to generate a plan, KMZ file, satellite overlay, or CAD file to permanently preserve results for future use.
GPRS does not provide land surveying services. If you need land surveying services, please contact a professional land surveyor.
Please contact us to discuss the pricing and marking options your project may require.
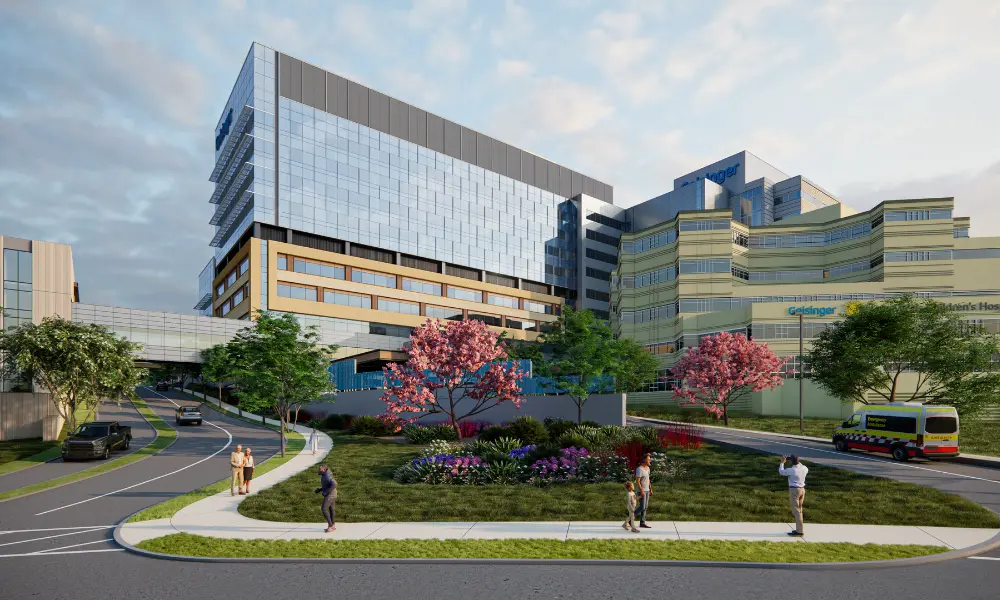
Pennsylvania Medical Center Expansion Highlights Ongoing Industry Trends
Architect EwingCole and general contractor Whiting-Turner are designing and building the $880 million expansion of Geisinger Medical Center in Danville, Pennsylvania.
The Philadelphia-based architect and Baltimore-based GC are working to modernize the hospital campus and the emergency department as part of the most significant expansion in the medical center’s nearly 110-year history, according to a press release issued by EwingCole.
The project includes an 11-story tower with an associated parking deck and renovation to the existing main entrance and drop-off sequence. The tower will feature 192 patient rooms to transition to campus to 100% private rooms on the hospital’s adult medical-surgical units; an expanded emergency department that will double the current space’s square footage; and a new, state-of-the-art operating suite.
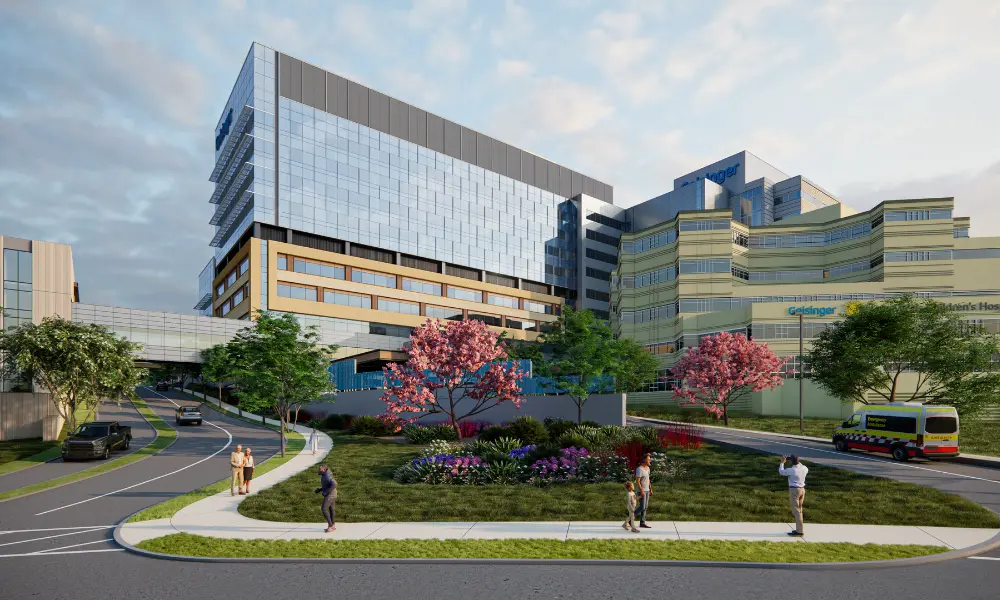
Construction began in May and is expected to be complete and open to patients by 2029, according to reporting by Construction Dive. The medical center’s old Dickey Clinic was demolished earlier in the year to make room for the new tower.
“Our community has depended on Geisinger for world-class health care for more than a century,” Terry Gilliland, M.D., president and CEO of Geisinger said in a press release issued by the healthcare consortium. “We’re continuing that legacy today as we announce the largest expansion project in the nearly 110-year history of Geisinger Medical Center. This project will truly transform care. It’s proof of our commitment to making better health easier for our communities today and into the future.”
The expansion project is part of a larger regional investment initiative Geisinger is currently undertaking. Geisinger Behavioral Health Center Danville, a 96-bed inpatient facility in Mahoning Township, is expected to open this summer, and an expansion similar to the Medical Center project is currently underway at Geisinger Wyoming Valley Medical Center near Wilkes-Barre.
“This project will completely reimagine the Geisinger Medical Center campus to strengthen collaboration among our staff and units for better patient care,” said Megan Brosious, chief administrative officer for Geisinger’s central region. “Our patients will have a modern care environment where they can continue receiving expert care right here in Danville, as they’ve come to expect from us over the past century. And our teams will have the space they need to provide that care.”
Trends in Healthcare Builds
Earlier this month, Construction Dive reported on how healthcare was one of the industries driving growth in construction planning amid struggles in other sectors.
Healthcare-related planning continued to accelerate in June along with warehouse activity and data center planning, according to data from the Dodge Construction Network’s Dodge Momentum Index, which tracks nonresidential projects entering the planning stage.
The $340 million Cleveland Clinic Avon campus expansion in Avon, Ohio was the largest institutional project to enter the planning stage in June, with the next largest project in that category – the McKinney Amphitheatre Building in McKinney, Texas – valued at less than half that at $150 million.
Nick Kaminski, Vice President of Healthcare Construction for Minneapolis-based construction firm, Ryan Cos., told Construction Dive that healthcare systems are continuing to develop and implement strategic growth plans despite the current economic uncertainties that have led other sectors to pause construction planning efforts. Oncology, cardiovascular, and orthopedic care are areas of focus within many of these growth plans, Kaminski said.
“…As part of this effort, many are prioritizing specialty assets like ambulatory surgery centers and freestanding emergency departments as key elements of their broader ambulatory expansion strategies,” he added. “These facility types are attracting targeted investments in both new construction and campus expansions nationwide…”
GPRS supports construction projects across industries, from hospitals to stadiums and beyond. Our subsurface damage prevention, existing conditions documentation, and construction & facilities project management services are designed to help you plan, manage, and build better. Utilizing state-of-the-art technologies such as ground penetrating radar (GPR), electromagnetic (EM) locating, Building Information Modeling (BIM), and more, we Intelligently Visualize The Built World® to keep you on time, on budget, and safe.
What can we help you visualize?
Frequently Asked Questions
What type of informational output is provided when I hire GPRS to conduct a utility locate?
Our Project Managers flag and paint our findings directly on the surface. This method of communication is the most accurate form of marking when excavation is expected to commence within a few days of service.
GPRS also uses a global positioning system (GPS) to collect data points of findings. We use this data to generate a plan, KMZ file, satellite overlay, or CAD file to permanently preserve results for future use. GPRS does not provide land surveying services. If you need land surveying services, please contact a professional land surveyor. Please contact us to discuss the pricing and marking options your project may require.
Can you find PVC piping and other non-conductive utilities?
GPR scanning is exceptionally effective at locating all types of subsurface materials. There are times when PVC pipes do not provide an adequate signal to ground penetrating radar equipment and can’t be properly located by traditional methods. However, GPRS Project Managers are expertly trained in multiple methods of utility locating.
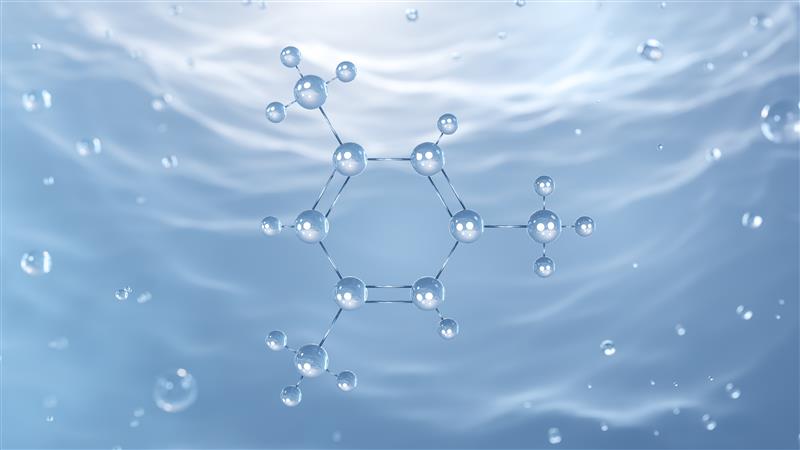
Volatile Organic Compounds Explained
Volatile Organic Compounds, commonly referred to as VOCs, are a broad group of carbon-based chemicals that easily evaporate at room temperature.
Found in a wide range of products and industrial processes, VOCs are a significant focus in environmental science, public health, and regulatory policy due to their potential impacts on air quality and human health.
Despite their ubiquity, VOCs are often misunderstood.
What Are VOCs?
VOCs are organic chemicals that have a high vapor pressure at ordinary room temperature.
This means they can readily transition from a liquid or solid state into a gas, releasing molecules into the air. The term "organic" in this context refers to the presence of carbon atoms in their molecular structure, often bonded with hydrogen, oxygen, nitrogen, or other elements.
The volatility of these compounds is what makes them particularly concerning. Once airborne, VOCs can contribute to indoor and outdoor air pollution, react with other atmospheric compounds, and in some cases, pose direct health risks to humans. These risks, along with the related regulatory requirements and associated operational cost, make VOCs a primary concern of facilities managers.
Common Sources of VOCs
VOCs are emitted from both natural and anthropogenic (human-made) sources. Naturally, they can be released by vegetation, wildfires, and microbial activity in soils. Most of the concern around VOCs, however, stems from human-related sources including:
- Consumer products: Paints, varnishes, cleaning agents, air fresheners, cosmetics, and adhesives often contain VOCs that are released during use and storage
- Industrial processes: Manufacturing, petrochemical refining, and solvent use are major industrial contributors
- Combustion: Vehicle exhaust, tobacco smoke, and burning of fossil fuels release a variety of VOCs into the atmosphere
- Building materials: New carpets, flooring, composite wood products, and insulation materials can off-gas VOCs over time, especially in poorly ventilated indoor environments
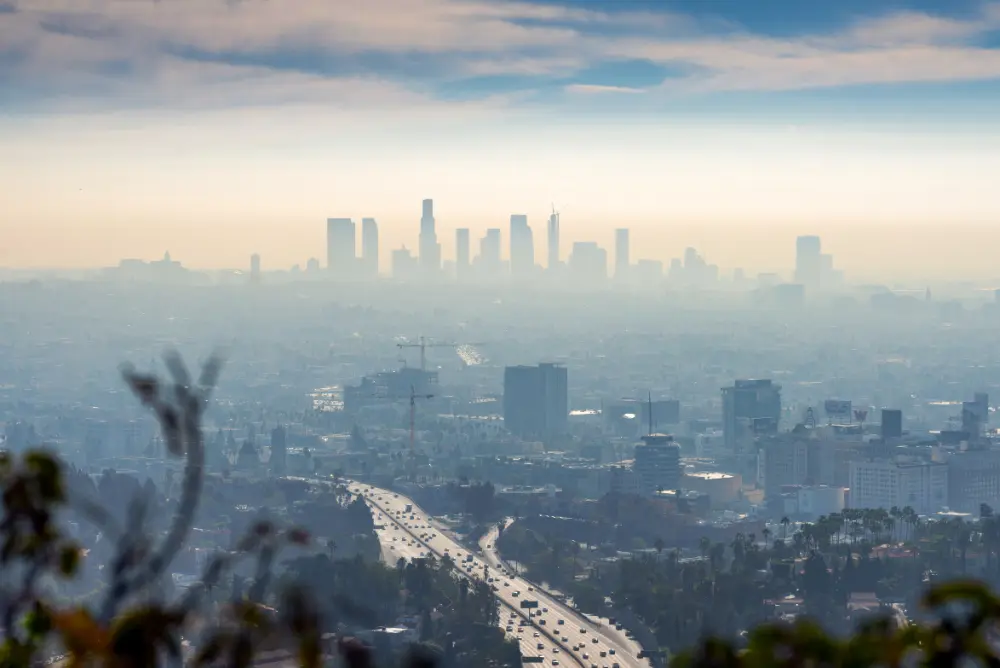
VOCs in Indoor vs. Outdoor Air
While outdoor VOC emissions are a major environmental concern, indoor air quality is often more directly affected by VOCs. In fact, concentrations of VOCs indoors can be up to ten times higher than outdoors, particularly in spaces with limited ventilation.
Indoor VOCs are primarily released from household products and building materials. Because people spend a significant portion of their time indoors – at home, work, or school – exposure to indoor VOCs is a key public health issue.
Health Impacts of VOC Exposure
The health effects of VOCs vary widely depending on the specific compound, concentration, duration of exposure, and individual susceptibility. Some VOCs are relatively harmless at low levels, while others are known to be toxic or carcinogenic.
Short-term exposure to elevated levels of VOCs can cause:
- Eye, nose, and throat irritation
- Headaches and dizziness
- Nausea and vomiting
- Worsening of asthma symptoms
Long-term exposure, particularly to certain VOCs like benzene, formaldehyde, and perchloroethylene, has been linked to more serious health outcomes, including:
- Liver and kidney damage
- Central nervous system effects
- Increased risk of cancer
Children, the elderly, and individuals with preexisting health conditions are generally more vulnerable to the effects of VOCs.
Environmental Impacts
Beyond human health, VOCs play a significant role in atmospheric chemistry. When released into the air, VOCs can react with nitrogen oxides (NOₓ) in the presence of sunlight to form ground-level ozone, a major component of smog. This photochemical reaction is a key driver of urban air pollution and can have detrimental effects on respiratory health, ecosystems, and agricultural productivity.
Some VOCs also contribute to the formation of secondary organic aerosols (SOAs), which are fine particulate matter that can penetrate deep into the lungs and exacerbate cardiovascular and respiratory diseases.
Regulation and Standards
Given their potential risks, VOCs are subject to regulation in many countries. In the United States, the Environmental Protection Agency (EPA) regulates VOC emissions through the Clean Air Act, particularly in relation to ozone formation. The EPA also sets limits for VOC content in consumer products and industrial processes.
The Occupational Safety and Health Administration (OSHA) provides workplace exposure limits for specific VOCs, while the Food and Drug Administration (FDA) and Consumer Product Safety Commission (CPSC) oversee VOCs in consumer goods.
Strategies for Reducing VOC Exposure
Minimizing exposure to VOCs involves a combination of product choices, ventilation, and awareness. Some practical steps include:
- Choosing low-VOC or VOC-free products: Many paints, adhesives, and cleaning supplies are now available in formulations that emit fewer VOCs
- Improving ventilation: Ensuring adequate airflow, especially during and after activities like painting or cleaning, can help disperse VOCs
- Proper storage: Keeping VOC-containing products sealed and stored in well-ventilated areas reduces emissions
- Avoiding unnecessary use: Limiting the use of air fresheners, aerosol sprays, and other VOC-heavy products can significantly reduce indoor concentrations
For workplaces and industrial settings, engineering controls such as fume hoods, air scrubbers, and personal protective equipment (PPE) are essential for managing VOC exposure.
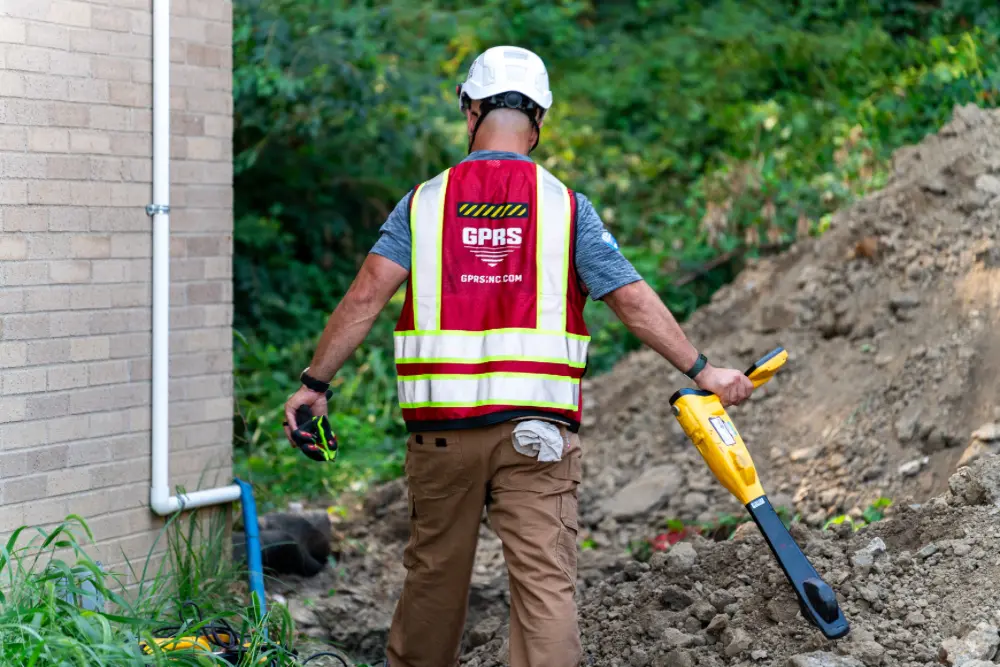
The Future of VOC Management
As awareness of VOC-related risks grows, so does the demand for safer alternatives and better monitoring technologies. Advances in sensor technology are making it easier to detect and quantify VOCs in real time, both in industrial settings and in consumer-grade air quality monitors.
Research is also ongoing into the development of sustainable materials and green chemistry approaches that reduce or eliminate the need for VOC-emitting substances altogether.
GPRS is the trusted leader for damage prevention in the environmental sector. Our project managers deliver results from the beginning of the initial investigation, throughout delineation and remediation, until project completion. With our nationwide network of Project Managers, we are equipped to mobilize to projects across the United States.
From sewer lines to skyscrapers, GPRS Intelligently Visualizes The Built World® to keep your projects on time, on budget, and safe.
What can we help you visualize?
FREQUENTLY ASKED QUESTIONS
What do I get when I hire GPRS to conduct a utility locate?
Our Project Managers flag and paint our findings directly on the surface. This method of communication is the most accurate form of marking when excavation is expected to commence within a few days of service.
GPRS also uses a global positioning system (GPS) to collect data points of findings. We use this data to generate a plan, KMZ file, satellite overlay, or CAD file to permanently preserve results for future use. GPRS does not provide land surveying services. If you need land surveying services, please contact a professional land surveyor.
Please contact us to discuss the pricing and marking options your project may require.
Can GPRS Project Managers distinguish between different underground utilities that they locate?
In most situations, we can identify the utility in question without any problems, although it is not always possible to determine what type of utility is present. When this happens, we attempt to trace the utility to a valve, meter, control box, or other signifying markers to determine the type of utility buried.
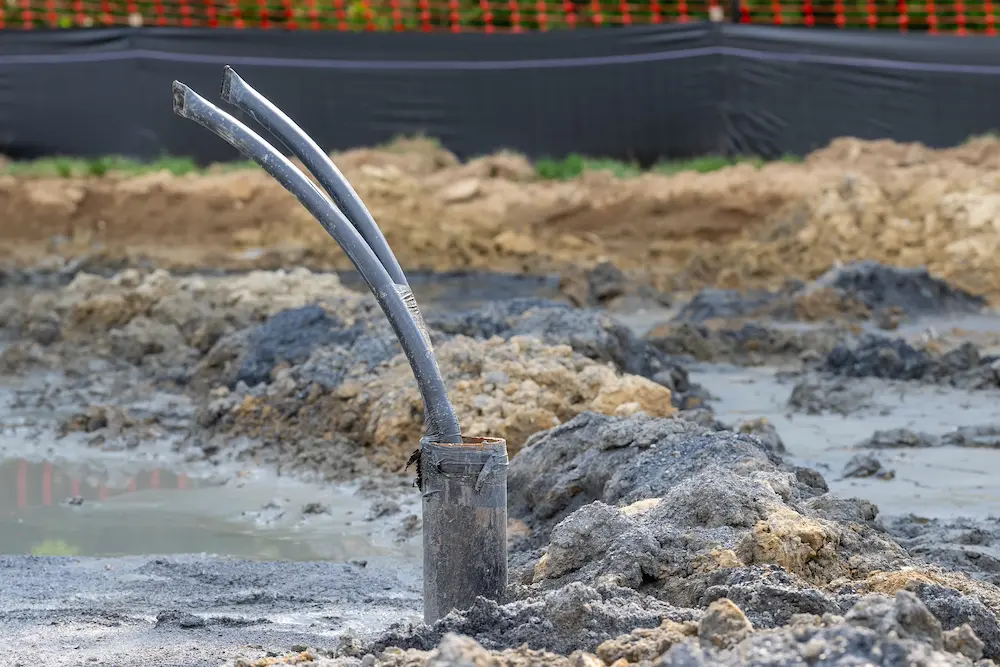
Geothermal’s Rising Heat: A Practical Energy Opportunity for Oil and Gas
The next era of geothermal energy production will likely be shaped by those who have already spent years mastering the underground – the professionals in the oil and gas industries. The rise of clean, renewable energy may be poised to become the rebirth of fossil fuel’s legacy expertise.
What is Geothermal Energy?
Geothermal energy is a renewable energy source that draws on Earth’s internal heat to produce steady, on-demand electricity, a consistency which makes it unique among renewable energy sources. Geothermal energy is unaffected by weather conditions or seasonal fluctuations. And while it currently provides only a small fraction of global energy, new approaches and partnerships could make it a key pillar of tomorrow’s grid.
One surprising catalyst for this shift is oil and gas expertise.
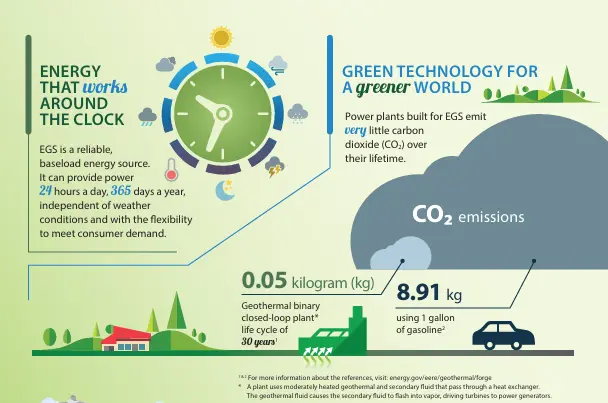
Why Geothermal Matters Now
Geothermal power is not new, but it is newly relevant. Advanced technologies like Enhanced Geothermal Systems (EGS), closed-loop wells, and sedimentary basin applications are expanding geothermal energy’s reach far beyond traditional volcanic zones. These systems can tap heat from deep underground almost anywhere. Geothermal is becoming viable in places like the central U.S., Canada, and Europe where it was once impractical.
According to projections from the International Energy Agency, global geothermal capacity could grow from under 20 gigawatts today to nearly 90 gigawatts by 2050. This would require significant capital, infrastructure, and workforce development. These are areas where fossil fuel firms already have decades of experience.
Bridging Sectors: Oil & Gas Meets Geothermal
Instead of viewing renewables as competition, Energies Media reports that oil and gas companies are finding new purpose by supporting geothermal energy production. This shift does not imply the abrupt end of fossil fuels. Rather, it suggests evolution. Many skills, technologies, and assets from oil and gas are directly applicable to the development of geothermal systems.
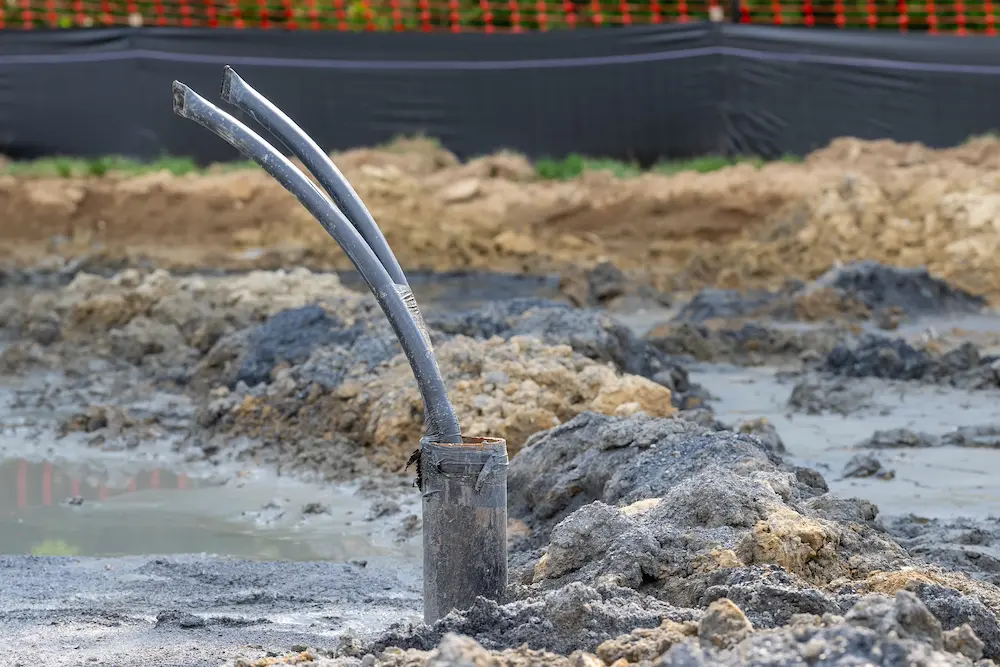
Shared strengths between sectors:
- Drilling Expertise: Oil and gas drillers understand complex well design and deep subsurface conditions. These are essential for geothermal expansion
- Reservoir Management: Monitoring fluid flow, temperature, and pressure underground is common to both disciplines
- Infrastructure Assets: Existing wells, pipelines, and data from fossil fuel projects can be repurposed for geothermal use
- Skilled Workforce: Engineers, geologists, and operations specialists can transition quickly from oil and gas to geothermal without needing new degrees
Several companies are already making the leap. Energies Media highlights firms that are working to blend oilfield engineering with geothermal design to create high-performance systems. Their work shows how subsurface knowledge from oil and gas can fast-track geothermal innovation and help cut costs.
Expanding Possibilities Through Technology
Several next-generation geothermal systems are paving the way for broader deployment:
- Enhanced Geothermal Systems (EGS)
These artificially stimulated reservoirs allow access to deep hot rock in areas that lack natural water flows. Techniques like hydraulic fracturing, which are common in shale oil production, are used to create pathways for heat extraction.
- Closed-Loop Systems Instead of drawing water from underground, fluids circulate in sealed loops through boreholes. This prevents water loss and lowers the risk of earthquakes.
- Hot Sedimentary Aquifers
These systems target deep water-bearing rock formations found in sedimentary basins that are familiar to oil and gas regions. Horizontal drilling increases reach and heat capture.
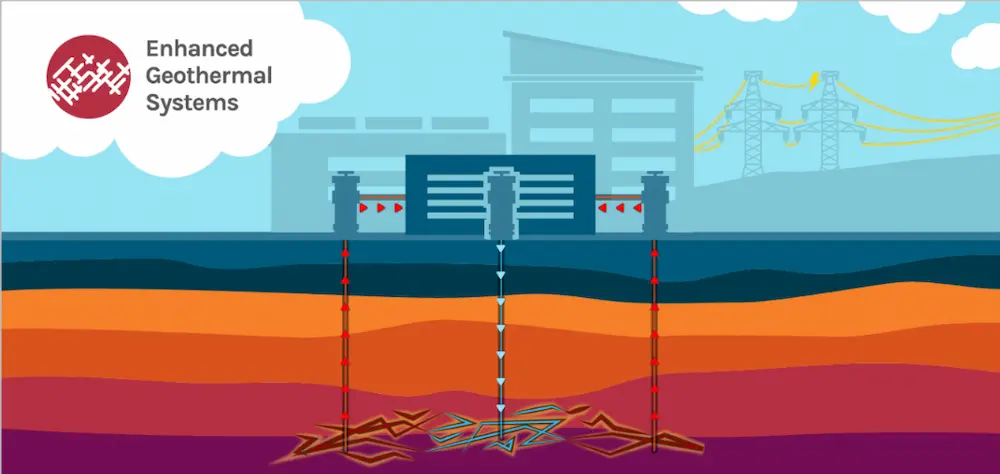
These innovations have major implications. They turn geothermal into a technology that can be deployed virtually anywhere. Potential applications go beyond electricity to include direct heating, industrial uses, and data center cooling.
Regardless of the specific type of system being deployed, it is vital to conduct ecological and environmental surveys of the area, and a comprehensive subsurface utility survey prior to drilling to avoid striking existing buried utilities. GPRS is the only infrastructure visualization company in the U.S. with the ability to locate and map subsurface utilities on a national scale. Plus, our new SiteMap® software platform (patent pending) provides a digital global asset management solution for geothermal, power, and gas & oil, facilities managers to streamline communications, construction, and management of their critical power infrastructure.
Revenue Reimagined
For fossil fuel firms, investing in geothermal is not just about reputation. It is also a smart business move. Revenue streams in this field include:
- Electricity sales from utility-scale geothermal plants
- Thermal energy for heating, manufacturing, or district energy networks
- Technology licensing when companies develop proprietary systems and designs
- Monetizing subsurface data from decades of well logs and seismic surveys
Organizations including major petroleum associations and policy groups are promoting this transition. Presentations like the IOGCC’s 2024 geothermal update encourage producers to view geothermal as a natural extension of their operations. The shared geology and engineering expertise needs make it a logical pivot that aligns with energy diversification and investor expectations.
A Future Built Together
The momentum around renewables does not signal the end of fossil fuel companies. Instead, it presents a turning point. This is a chance to evolve, adapt, and thrive in a changing energy landscape.
Geothermal energy gives oil and gas professionals an opportunity to apply their talents in new ways. They can help solve climate challenges without abandoning their identity. For many firms, this is not a break from tradition. It is a strategic expansion.
GPRS Intelligently Visualizes The Built World® for customers nation-wide.
What can we help you visualize?
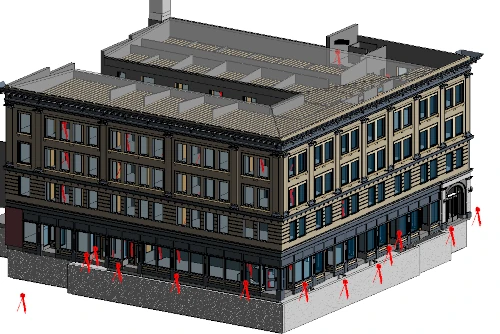
What Is Scan to BIM and How Much Does It Cost?
Scan to BIM is a cutting-edge reality capture process that transforms real-world buildings and infrastructure into intelligent digital models. It begins with 3D laser scanning, where millions of data points are captured to create a highly accurate point cloud of a site.
The point cloud is converted into a building information model (BIM), a data-rich, 3D representation that includes architectural, structural, mechanical, electrical, and plumbing (MEP) systems. Other scan to BIM deliverables can be created, such as 2D CAD drawings, 3D mesh models, TruViews, and virtual tours in formats like Revit, AutoCAD, Navisworks, Civil 3D, and more.
“Scan to BIM transforms real world conditions into accurate digital models: this streamlines design, reduces rework, and improves coordination from start to finish on any project,” says Tyler Zac, Market Segment Leader – GPRS Reality Capture Services.
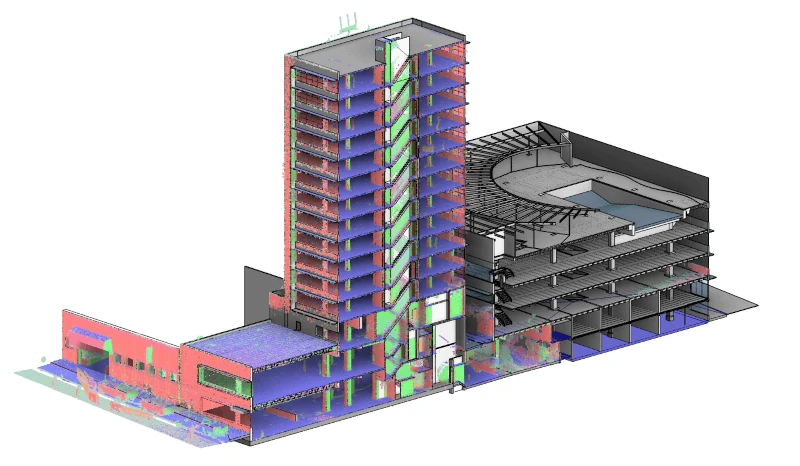
What are the Benefits of Scan to BIM?
Scan to BIM improves how architects, engineers, and contractors plan, renovate, and manage buildings. Scan to BIM provides these benefits:
- Captures precise site conditions with millimeter-level accuracy, minimizing measurement errors and guesswork
- Accelerates data collection and reduces manual work, helping shorten timelines and reduce project costs
- Collects millions of data points in minutes to streamline workflows and speed up project delivery
- Aligns teams in a shared digital model, ensuring consistency and coordination
- Detects design clashes early to prevent rework, delays, and on-site conflicts
- Documents historic buildings for restoration without damaging original features
- Supports long-term facility management through digital twins for maintenance, upgrades, and renovations
These benefits make scan to BIM a powerful tool for AEC professionals. As noted in a recent Research Gate article, titled BIM and Automation in Complex Building Assessment, “using Building Information Modeling (BIM) during early design stages helps improve building quality by enabling the evaluation of different design options and structural systems.”
Whether you're renovating a courthouse, expanding a manufacturing plant, or retrofitting a stadium, scan to BIM provides the foundation for intelligent design planning and construction execution.
How Much Does Scan to BIM Cost?
The cost of scan to BIM can vary depending on your project. First, project size and scope play a major role. Larger buildings require more time to scan and process, and sites with multiple floors, complex MEP systems, or multiple roof sections typically increase the overall cost due to the added intricacy and data volume.
The second factor is the level of detail (LOD) specified for the deliverables. LOD 100 to 200 models provide basic mass and geometry and tend to be more affordable. LOD 300 includes structural and architectural elements, falling into a mid-range price bracket. LOD 400 to 500 delivers highly detailed BIM models with full mechanical, electrical, and plumbing (MEP) integration and are higher in cost.
Structural complexity is another important consideration. Simple warehouses or open layouts are less expensive to model compared to ornate historic buildings or facilities packed with dense MEP systems, which demand greater scanning resolution and scan to BIM modeling effort.
Site accessibility can also influence pricing. Remote or hard-to-reach locations might require specialized equipment or incur travel expenses, both of which add to the project total.
Lastly, the type and quantity of deliverables required determine the final budget. Basic point cloud data is the most cost-effective option, while 3D BIM models and advanced analysis involve additional processing and modeling work, increasing the cost. Below is a list of common scan to BIM deliverables.
What are the Types of Scan to BIM Deliverables?
Scan to BIM deliverables are the outputs generated from converting laser scanned point cloud data into usable digital formats for design, construction, and facility management.
Point Cloud Files: Raw 3D data captured from laser scans, typically in formats like .rcp, .e57, or .las. These serve as the foundation for the deliverables mentioned below.
2D CAD Drawings: Floor plans, elevations, sections, details, isometric drawings, and reflected ceiling plans (RCPs) extracted from the point cloud, delivered in .dwg, .dxf, .dgn, or .PDF formats.
3D BIM Models: Intelligent models built in software like Revit, AutoCAD, Microstation, Solidworks, Navisworks, representing architectural, structural, and MEP systems.
Mesh Models: Polygonal representations of surfaces, useful for visualization or simulation, often exported in .obj, .stl, .fbx, and .ply.
TruViews: Interactive, 360° photo-realistic views linked to laser scan data, allowing users to navigate the site virtually.
Virtual Tours: A collection of panoramic rotating images, stitched together to form a full, 360° view of a location.
Advanced Analysis and Calculations: Custom analysis and calculations with high precision can be created, such as dimensional callouts, tank calibration analysis, prefabrication of panels, accident analysis, floor flatness and levelness analysis, deviation analysis, deformation analysis, new construction verification, volume calculations, wall plumb analysis, staircases, elevator shaft analysis and more.
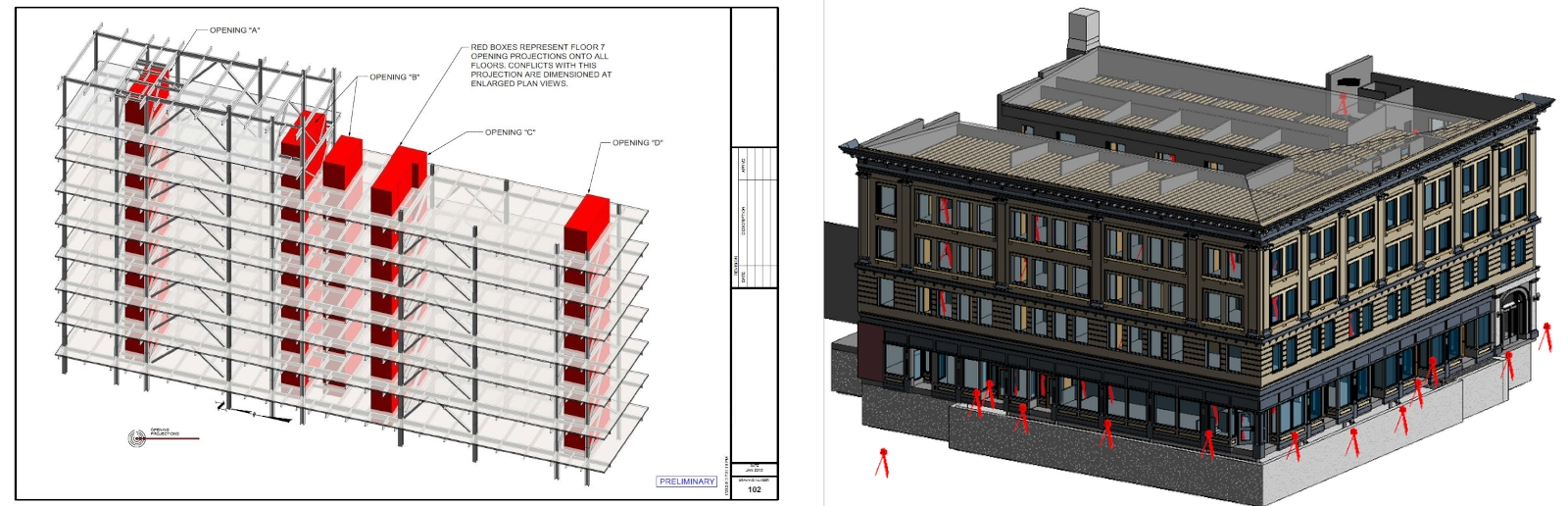
Does GPRS Perform Scan to BIM Services?
GPRS is a national leader in 3D laser scanning and reality capture services, using survey-grade Leica scanners to perform scan to BIM with exceptional precision. Our Mapping & Modeling Team delivers a full suite of deliverables that are produced in-house to ensure technical accuracy and consistency across platforms.
Here is a list of items a GPRS Project Manager will use to determine the cost of your scan to BIM project.
- Location
- Scope of work
- Square footage
- Site images
- Site plans
- Building or site complexity
- Building or site access and occupancy
- Deliverables required
- Level of detail (if CAD drawings or 3D modeling is needed)
- Project timeline
- Special requirements, such as night or weekend scanning
Every project is unique. That’s why GPRS tailors our scope of work to meet the specific demands of each project – to ensure you get exactly what you need, with deliverables customized to your specifications. Our expert team can model within your template and to your standards, and will adhere to naming conventions, on request.
For scan to BIM pricing, request a quote here, call 419-843-7226, or email Laser@gprsinc.com.
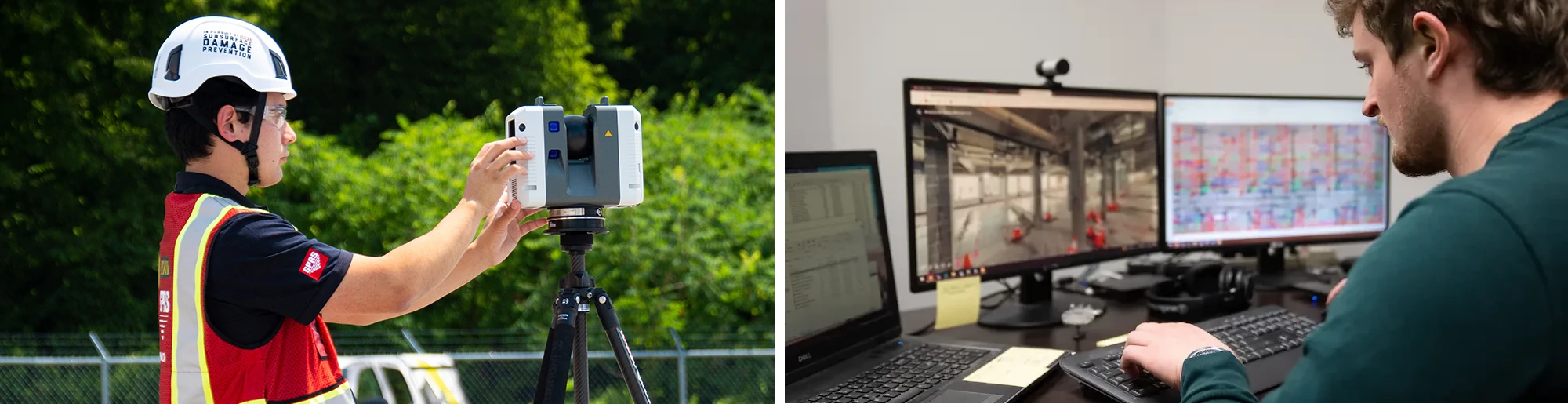
GPRS Scan to BIM Project Examples
Scan to BIM for Renovations at Arizona University Laboratory Building
A general contractor was tasked with renovating four laboratory rooms at an Arizona university, totaling 19,000-square-feet. To ensure a seamless renovation process, the team required a precise 3D Revit model, detailing the locations of structural elements, HVAC systems, and piping.
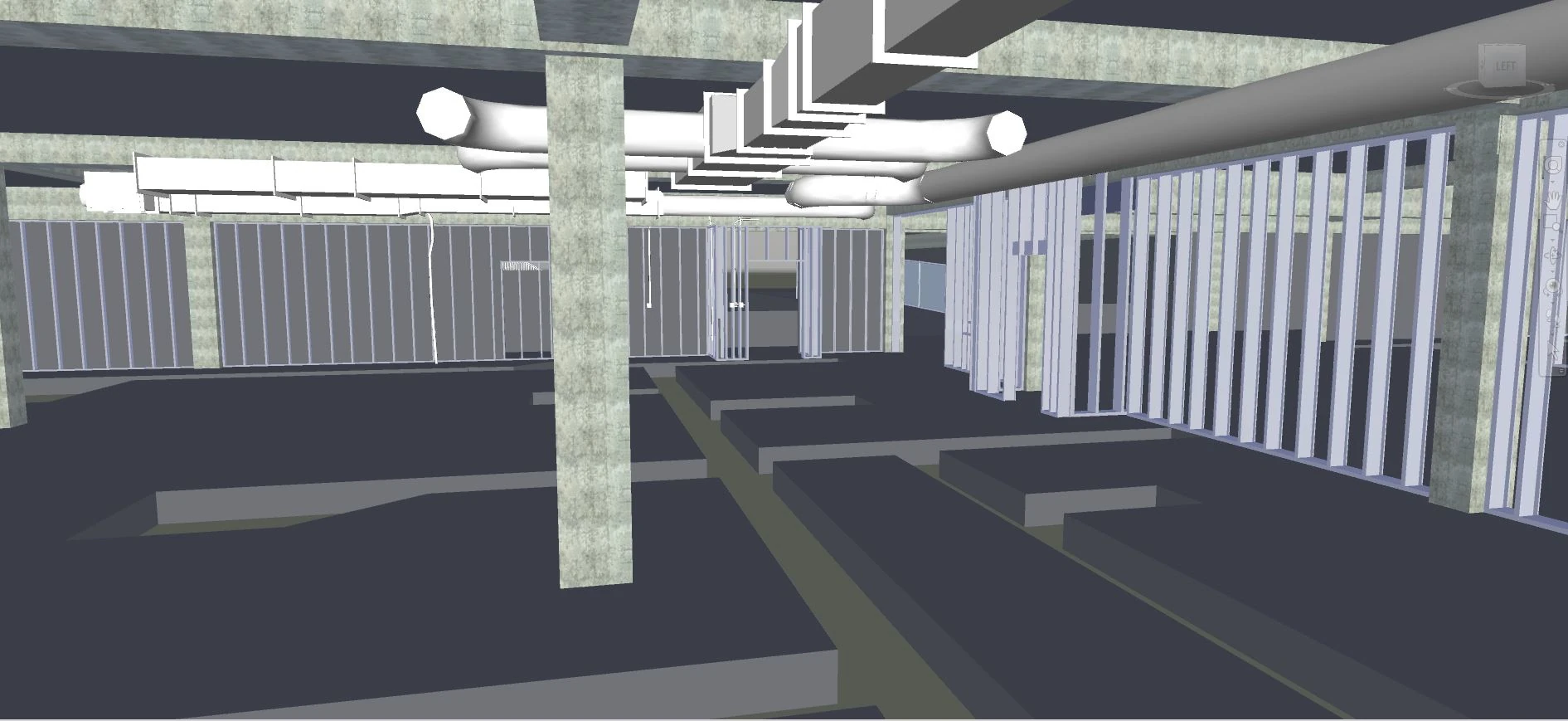
Pharmaceutical Upgrades Completed with the Help of Laser Scanning
GPRS used 3D laser scanning to capture existing conditions across four levels of a pharmaceutical facility undergoing equipment upgrades and MEP rerouting. By delivering a precise LOD 300 Revit model, the client was able to plan layout changes, avoid field rework, and reduce downtime, resulting in faster execution and significant cost savings.
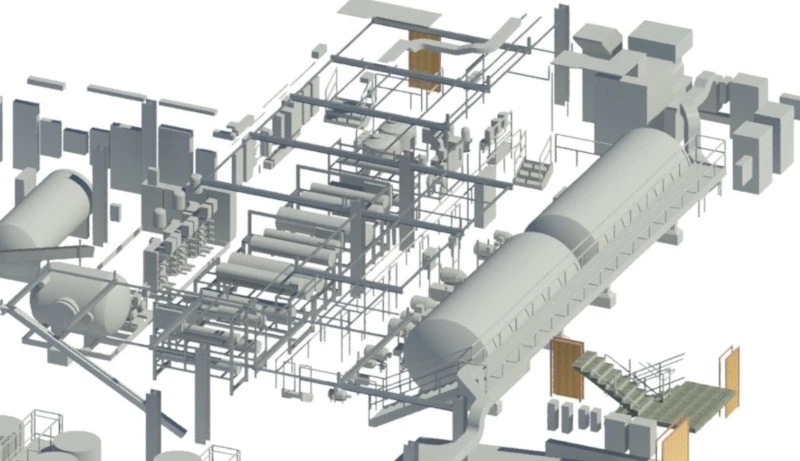
Why Choose GPRS for Scan to BIM Services?
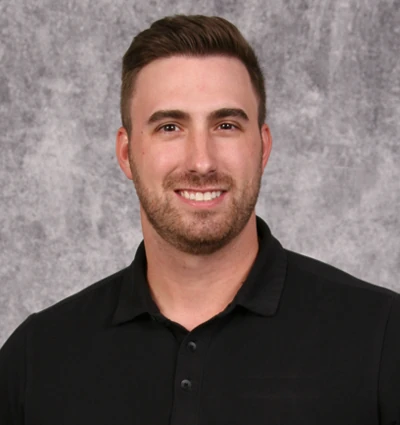
GPRS is a leading scan to BIM service company, having completed thousands of projects across sectors including healthcare, education, manufacturing, and government.
Offering nationwide coverage and fast turnaround times, our team delivers consistent, survey-grade results. Each Reality Capture Project Manager completes the industry-leading Subsurface Investigation Methodology (SIM) certification, which includes 80 hours of classroom training, 320 hours of field mentorship, and 40 hours of specialized LiDAR instruction, ensuring expertise in 3D laser scanning and field accuracy that exceeds industry standards.
GPRS scan to BIM deliverables are uploaded to SiteMap®, GPRS’ secure GIS platform, giving clients 24/7 access to verified as-built documentation to help you plan, build, and manage better.
Tyler Zac, Market Segment Leader – GPRS Reality Capture Services says, “With GPRS, you receive more than a scan, you gain a precise digital foundation to drive project success.”
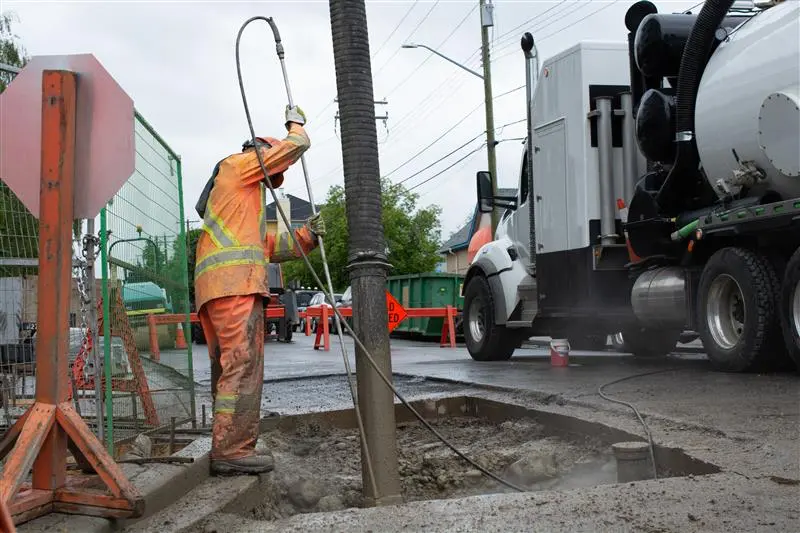
The Benefits of Hydro Excavation in Urban Settings
When you need to excavate within the complex and congested environment of a modern city, traditional digging methods like backhoes or manual shoveling often fall short of the required precision, safety, and efficiency.
Hydro excavation can provide a non-destructive, highly accurate alternative, using pressurized water and a vacuum system to break up soil and remove it. This technique has rapidly become a preferred choice for urban excavation projects, because it provides a host of advantages that align with the demands of modern infrastructure development.
Precision in a Crowded Underground
Urban areas are a labyrinth of buried utilities – gas lines, water mains, fiber optic cables, electrical conduits, and sewer systems. These networks are often poorly documented or inaccurately mapped, making any excavation a potential hazard. Hydroexcavation allows for pinpoint accuracy, enabling crews to expose underground utilities without damaging them. The pressurized water gently loosens the soil, while the vacuum system removes debris, revealing infrastructure with minimal risk.
This level of precision is particularly valuable in cities where space is limited and the margin for error is slim. Hydro excavation provides a more controlled and careful approach to excavation as opposed to mechanical digging, which not only protects critical infrastructure but reduces the likelihood of costly repairs, service interruptions, and safety incidents.
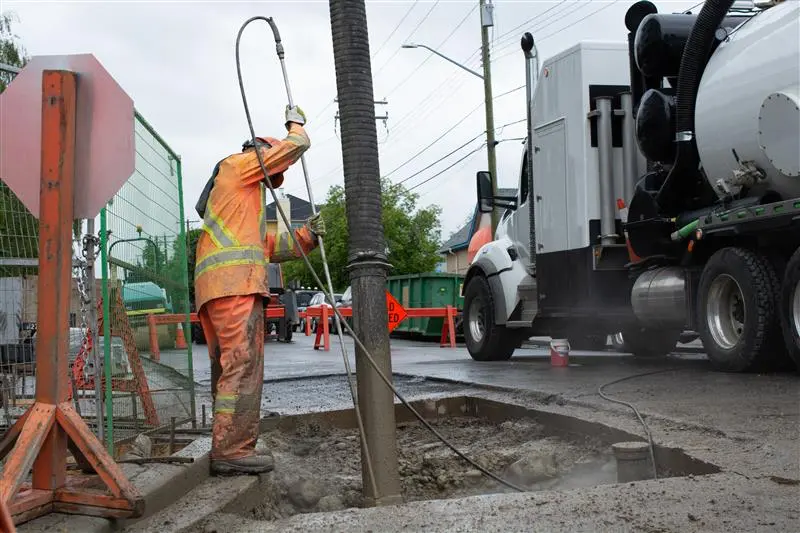
Enhanced Safety for Workers and the Public
Safety is the number one concern in any excavation project, especially in densely populated urban environments. Traditional excavation methods can pose significant risks, including cave-ins, equipment accidents, and utility strikes. Hydro excavation can mitigate many of these dangers by minimizing the need for heavy machinery and reducing the physical strain on workers.
Because it is a non-mechanical process, hydro excavation significantly lowers the risk of accidental contact with live electrical lines or pressurized gas mains. This makes it an ideal choice for projects near sensitive or high-risk infrastructure. Additionally, the reduced noise and disruption associated with hydro excavation can contribute to a safer and more tolerable environment for nearby residents and businesses.
Environmental and Structural Preservation
Urban excavation often takes place near buildings, roads, and landscaping that must be preserved. Traditional digging can cause collateral damage to surrounding structures, tree roots, and pavement. Hydro excavation, by contrast, is minimally invasive. The targeted nature of the process allows crews to dig only where necessary, preserving the integrity of nearby features.
Efficiency and Cost-Effectiveness
While hydro excavation might seem more specialized and therefore more expensive, it often proves more cost-effective in the long run. The speed and accuracy of the process have been shown to reduce labor hours, minimize downtime, and prevent expensive utility damage. Projects can be completed faster and with fewer disruptions, which is especially important in urban areas where time is money and delays can have wide-reaching consequences.
Hydro excavation is also well-suited for a variety of applications beyond utility exposure. It can be used for trenching, potholing, daylighting, debris removal, and even cold-weather digging, thanks to heated water systems. This versatility makes it a valuable tool for municipalities, contractors, and utility companies alike.
Regulatory Compliance and Risk Management
Cities are increasingly implementing strict regulations around excavation to protect public infrastructure and ensure safety. Hydro excavation aligns well with these regulatory frameworks, offering a compliant method that reduces liability. By minimizing the risk of utility strikes and environmental damage, it helps contractors meet legal requirements and avoid fines or litigation.
Insurance providers also recognize the reduced risk associated with hydro excavation, which can lead to lower premiums and fewer claims. For project managers and municipal planners, this translates into a more predictable and manageable risk profile.
The Critical Role of Utility Locating Before Excavation
Despite the many advantages of hydro excavation, one foundational step must precede any digging activity: accurate subsurface utility locating & mapping.
Even the most precise excavation method cannot compensate for a lack of knowledge about what lies beneath the surface. And while calling your local 811 One-Call service should always happen before you break ground, it’s important to remember that not all utilities are owned by companies registered with 811. Hiring a private utility locating company to complement the data you receive from 811 ensures you always know what’s below, whether the lines belong to public utilities or private entities, so you can eliminate the risk of subsurface damage during excavation.
GPRS offers 99.8%+ accurate utility locating and mapping services, utilizing ground penetrating radar (GPR) scanning, electromagnetic (EM) locating, and other technologies to Intelligently Visualize The Built World® below your feet. All this accurate, actionable data is uploaded into SiteMap® (patent pending), our infrastructure mapping software application designed to help you plan, design, manage, dig, and ultimately build better.
What can we help you visualize?
Frequently Asked Questions
Can ground penetrating radar (GPR) verify known measurements?
GPRS Project Managers can use GPR to cross-check the measured depth and location of a located utility with existing as-built plans to verify the accuracy of plans.
Is GPRS able to distinguish between the different underground utilities you locate?
In most situations, we can identify the utility in question without any problems, although it is not always possible to determine what type of utility is present. When this happens, we attempt to trace the utility to a valve, meter, control box, or other signifying markers to determine the type of utility buried.
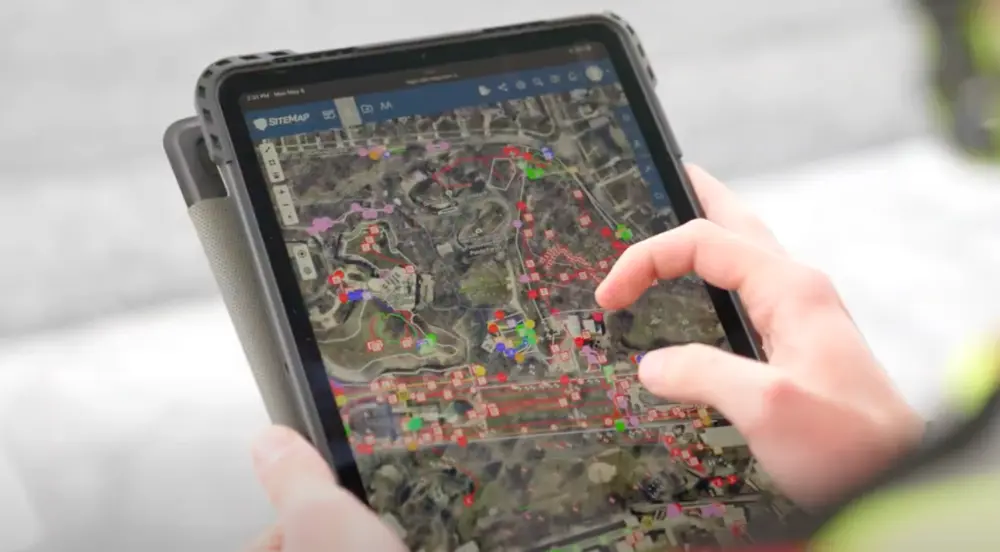
How GIS Technology Benefits AEC Industries
Geographic Information Systems (GIS) have emerged as a transformative force in the rapidly evolving landscape of the Architecture, Engineering, and Construction (AEC) industries.
Once confined to cartography and environmental studies, GIS technologies now play a pivotal role in planning, designing, constructing, and managing infrastructure. By integrating spatial data with design and engineering workflows, GIS empowers AEC professionals to make smarter decisions, reduce risk, and deliver more sustainable and resilient projects.
What is GIS?
At its core, GIS is a framework for gathering, managing, and analyzing spatial and geographic data. It combines location data (where things are) with descriptive information (what things are like there), enabling users to visualize, question, and interpret data in ways that reveal relationships, patterns, and trends.
In the AEC context, GIS is not just about maps – it's about spatial intelligence. It provides a digital twin of the real world, allowing professionals to simulate, analyze, and optimize every phase of a project lifecycle.
Enhancing Planning and Site Selection
One of the most significant advantages GIS brings to AEC is in the early planning and site selection stages. By layering data such as topography, land use, zoning regulations, environmental constraints, and utility networks, GIS helps stakeholders identify the most suitable locations for development.
For example, an engineering firm planning a new transportation corridor can use GIS to evaluate terrain, assess environmental impact, and analyze traffic patterns – all before a single line is drawn in CAD. This spatial insight reduces costly surprises and accelerates the decision-making process.
Integrating with BIM for Smarter Design
Building Information Modeling (BIM) has revolutionized the way buildings and infrastructure are designed and documented. When integrated with GIS, BIM becomes even more powerful. GIS provides the geographic context – such as terrain, climate, and surrounding infrastructure – while BIM delivers detailed design and construction data.
This integration enables a holistic view of projects. Architects can design structures that respond to their environment. Engineers can simulate how infrastructure will perform under different conditions. Urban planners can visualize how new developments will interact with existing communities.
Combining GIS and BIM allows, for instance, for flood risk analysis on a proposed building site, enabling design modifications that enhance resilience. It also supports compliance with local regulations and sustainability goals.
Streamlining Construction and Project Management
GIS technologies also play a critical role during construction. Real-time data collection from drones, sensors, and mobile devices can be fed into GIS platforms to monitor progress, track assets, and manage logistics.
Construction managers can use GIS dashboards to visualize site conditions, coordinate equipment and personnel, and respond quickly to issues. This spatial awareness improves safety, reduces delays, and enhances collaboration among teams.
GIS also supports 4D and 5D modeling – adding time and cost dimensions to 3D models. This allows project managers to simulate construction sequences, forecast budget impacts, and optimize resource allocation.
Supporting Infrastructure and Asset Management
Once a project is completed, GIS continues to deliver value through asset management. Municipalities, utilities, and facility managers use GIS to maintain infrastructure, monitor performance, and plan maintenance.
A city can use GIS to manage its water distribution network, tracking pipe conditions, identifying leak-prone areas, and scheduling repairs. Facility managers can integrate GIS with IoT sensors to monitor building systems and respond to anomalies in real time.
This lifecycle approach – design, build, operate – ensures that spatial data remains a living asset, supporting long-term sustainability and efficiency.
Enabling Resilience and Sustainability
In an era of climate change and urbanization, resilience and sustainability are top priorities for AEC professionals. GIS provides the tools to assess environmental impact, model natural hazards, and design adaptive infrastructure.
Planners can use GIS to identify flood zones, wildfire risk areas, or heat islands, and incorporate mitigation strategies into their designs. Engineers can simulate stormwater runoff or energy consumption to optimize systems. Developers can evaluate the carbon footprint of different site options.
By embedding environmental intelligence into every phase of a project, GIS helps the AEC industry build smarter, greener, and more resilient communities.
Facilitating Collaboration and Public Engagement
GIS also enhances collaboration among stakeholders. Cloud-based GIS platforms allow architects, engineers, contractors, and clients to access and share spatial data in real time. This transparency improves coordination and reduces errors.
In addition, GIS supports public engagement. Interactive maps and 3D visualizations help communities understand proposed developments, provide feedback, and participate in the planning process. This fosters trust, reduces opposition, and leads to better outcomes.
Real-World Applications
Across the globe, AEC firms are leveraging GIS in innovative ways:
- Transportation: Departments of transportation use GIS to plan highways, optimize traffic flow, and manage construction zones
- Utilities: Electric and water utilities use GIS to map networks, monitor outages, and plan expansions
- Urban Development: Cities use GIS to model growth scenarios, assess housing needs, and plan smart infrastructure
- Disaster Recovery: After natural disasters, GIS helps assess damage, prioritize response, and plan reconstruction
Challenges and Future Directions
Despite its benefits, integrating GIS into AEC workflows is not without challenges. Data interoperability, skill gaps, and organizational silos can hinder adoption. Most GIS systems require the user to upload their data, and that data is only as good as their existing as-builts – which are often inaccurate and/or incomplete.
Advances in cloud computing, AI, and open data standards, however, are making GIS more accessible and powerful than ever.
Looking ahead, the convergence of GIS with technologies like digital twins, augmented reality, and machine learning promises to further transform the AEC landscape. As spatial data becomes more dynamic and intelligent, GIS will be at the heart of designing the cities and infrastructure of the future.
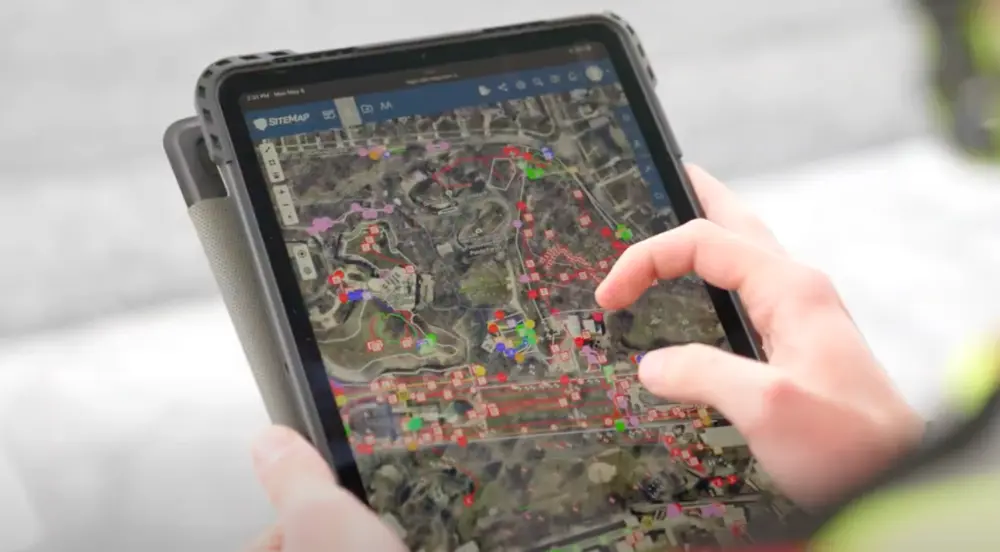
How SiteMap® Represents the Next Generation of GIS Technology
GIS technologies are no longer optional in the AEC industries – they are essential. By providing spatial context, analytical power, and collaborative tools, GIS enables professionals to plan smarter, design better, build faster, and operate more efficiently.
SiteMap® (patent pending), powered by GPRS, is the first-ever GIS infrastructure mapping and facilities management platform that is composed of the accurate, field-verified data collected by SIM-certified GPRS Project Managers. Accessible 24/7 from any computer, tablet or smartphone, SiteMap is a single source of truth for the information you and your team needs to eliminate the mistakes caused by miscommunications. It allows you to plan, design, manage, dig, and ultimately build better.
Click below to schedule a live, personal & free SiteMap demo today!
Frequently Asked Questions
What are the Benefits of Underground Utility Mapping?
Having an updated and accurate map of your subsurface infrastructure reduces accidents, budget overruns, change orders, and project downtime caused by dangerous and costly subsurface damage.
How does SiteMap® assist with Utility Mapping?
SiteMap®, powered by GPRS, is the industry-leading infrastructure management program. It is a single source of truth, housing the 99.8%+ accurate utility locating, concrete scanning, video pipe inspection, leak detection, and 3D laser scanning data our Project Managers collect on your job site. And the best part is you get a complimentary SiteMap Personal Subscription when GPRS performs a utility locate for you.
Does SiteMap Work with my Existing GIS Platform?
SiteMap allows for exporting of data to SHP, GeoJSON, GeoPackage, and DXF directly from any user’s account that either owns or has a job shared to their account. All these file formats can be imported and utilized by other GIS packages if manually imported by the user.
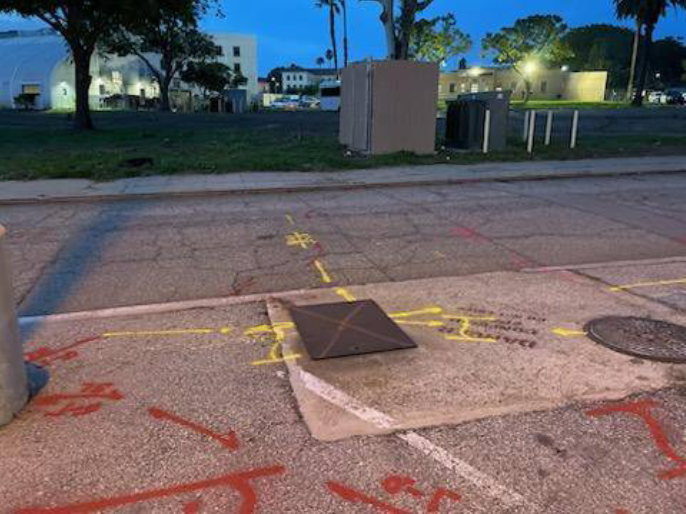
GPRS Aids Parking Lot Renovation Project for California Hospital
By utilizing our 99.8% accurate underground utility scans, GPRS produced surprising results that helped a hospital in Los Angeles, California dig safely and confidently during recent parking lot renovations.
GPRS Project Manager Javier Mendez was tasked with scanning the parking lot of a VA Medical Center in Los Angeles, California. The facility had recently installed solar panels and needed precise scans of the area to update their as-built records and reroute some of the lines.
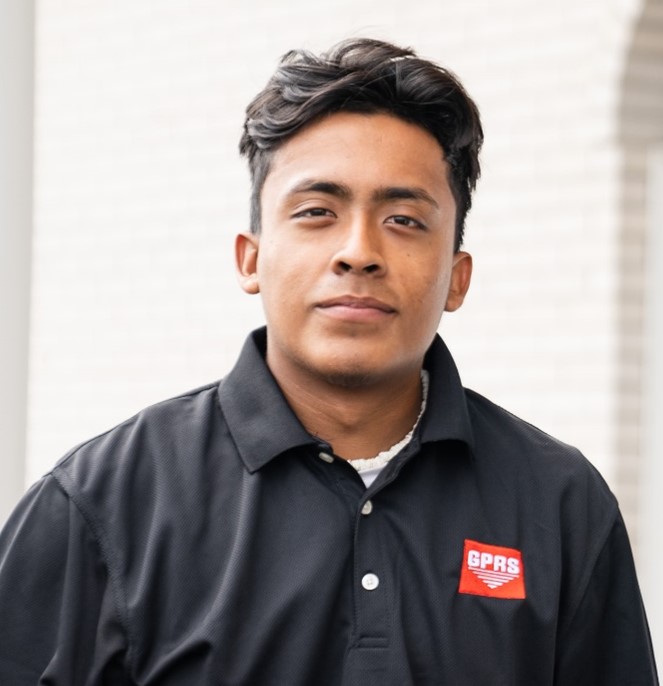
“They needed to know the precise locations of all these utilities, because the parking lot – they already had solar in there – but what they didn't realize is they put the solar within the existing utilities,” Mendez explained. “So, if they ever were to go back and excavate again, they really can't because the solar is in the way. They need to find all these lines, reroute them, and cap some of them off.”
By following one of the main guidelines of SIM, or Subsurface Investigation Methodology, Mendez used multiple technologies, which included ground penetrating radar (GPR) and electromagnetic (EM) locators, to make sure his findings were accurate.
Mendez’s findings were marked out on the parking lot’s surface, geolocated with Real-Time Kinematic Positioning, and uploaded to SiteMap® in minutes. SiteMap® (patent pending) is GPRS’ cloud-based infrastructure platform. With SiteMap, our client’s utilities can go from underground to the cloud, so they can easily reference them throughout the project life cycle.
The client was very surprised by Mendez’s findings. The results of the scans showed more utilities present in that location than the client had expected based on their existing plans. Because of these results, Mendez’s scope of work extended past the parking lot and into the adjacent right-of-way.
“Once they saw [the underground utilities] extended to the right-of-way, they wanted to see where exactly those lines in the parking lot go and where they tie into,” Mendez explained. “They wanted to find the main since they were going to be exposing these lines. They want to see where they could cap it off or where they could cap it or reroute it from. Gladly, we were able to provide them with where all these lines that went into the parking lot were tied into and where they get fed from exactly.”
Every job that GPRS Project Managers undertake is serious business. The same goes for this job, especially with what could have happened if a utility strike occurred near the hospital.
“Because we had just about every utility you could think of, you had fire, water, gas lines, steam lines, and petroleum lines running through that section,” Mendez explained. “So, I think them calling us out definitely did save them a lot of money, a lot of time, and we kept everyone safe. Without us, they would have went in there, crossed their fingers, and wished for the best.”
The data collected by Mendez gave the client the ability to dig with confidence, move and/or cap lines, and avoid utility strikes.
“We never want to stop short for the client, right? So, we always want to go above and beyond and whatever they asked for. We are there to make sure they're satisfied with whatever information we provide for them.”
From skyscrapers to sewer lines, GPRS Intelligently Visualizes the Built World® to keep your projects on time, on budget, and safe.
What can we help you visualize?
FREQUENTLY ASKED QUESTIONS
What type of informational output does GPRS provide when conducting a utility locate?
Our Project Managers flag and paint our findings directly on the surface. This method of communication is the most accurate form of marking when excavation is expected to commence within a few days of service.
GPRS also uses Real-Time Kinematic Positioning (RTK) to collect data points of findings. We use this data to generate a plan, KMZ file, satellite overlay, or CAD file to permanently preserve results for future use. GPRS does not provide land surveying services. If you need land surveying services, please contact a professional land surveyor. Please contact us to discuss the pricing and marking options your project may require.
What are the Benefits of Underground Utility Mapping?
Having an updated and accurate map of your subsurface infrastructure reduces accidents, budget overruns, change orders, and project downtime caused by dangerous and costly subsurface damage.
What is Subsurface Investigation Methodology?
Subsurface Investigation Methodology (SIM) is a standard operating procedure and set of professional specifications that work as a guide for utility locating experts when scanning for buried utility lines. All GPRS Project Managers are required to achieve SIM 101 certification, which requires 80 hours of hands-on training in a classroom setting and 320 hours of mentorship in the field. For reference, the American Society for Nondestructive Testing’s (ASNT) minimum training recommendation includes eight hours for training and 60 hours practicing GPR to achieve NDT Level 1 certification in ground penetrating radar (GPR) scanning.
SIM requires the use of multiple, complementary technologies, like GPR scanning and electromagnetic (EM) locating, when locating buried utilities or scanning a concrete slab.
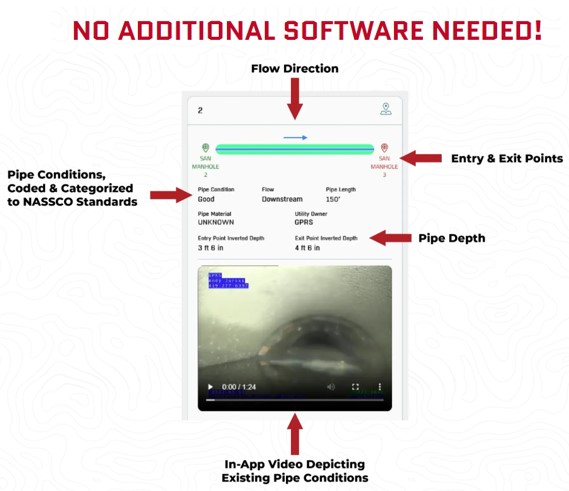
Unlocking Subsurface Clarity: How GPRS’ SiteMap Sewer Layer Shows Facilities Managers Exactly “Where in the World” Their Pipes Are
Facilities managers are all too familiar with the challenges of wastewater systems management. Fortunately, there is a new tool that could take a lot of the stress out of maintaining sanitary and storm sewer lines by allowing you to visualize your subsurface infrastructure from anywhere 24/7. That may sound like science fiction, but it’s now reality thanks to GPRS’ new SiteMap® Sewer Layer.
Accurately locating and managing underground sewer infrastructure traditionally requires a lot of guesswork around incomplete, outdated sanitary or storm sewer as-builts, and expensive, time-consuming, and wasteful potholing as you play a frustrating game of whack-a-mole trying to find the source of a break, blockage, or overflow.
And the worst part is that after all that, you still don’t know the exact location of all your sewer lines, cleanouts, and laterals, let alone any damaging cross bores caused by trenchless technology line installations drilling straight through your sewer system.
That’s why GPRS is pleased to introduce you to the SiteMap Sewer Layer, a transformative solution for facilities and municipal managers. delivering precise, accessible, and actionable sewer mapping data. This innovation enhances everything from daily operational efficiency to risk mitigation, and long-term asset maintenance planning by providing a centralized, single source of truth for sewer systems.
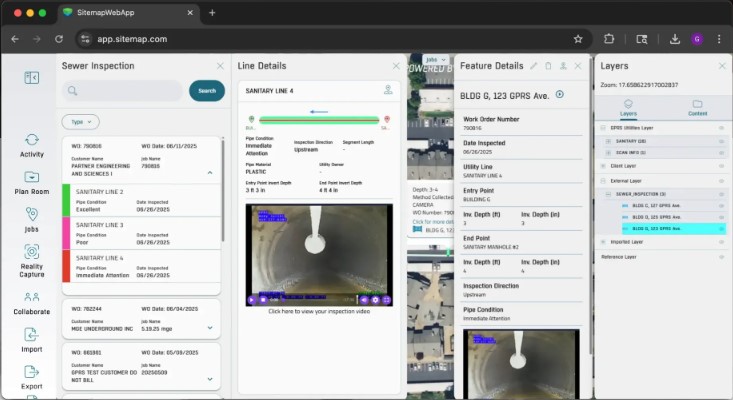
What is the SiteMap Sewer Layer?
The SiteMap Sewer Layer integrates data collected through GPRS’ advanced video pipe inspection technologies, including CCTV robotic crawler cameras and lateral launch “push camera” systems. These tools, used in concert with utility locating technologies like ground penetrating radar (GPR), electromagnetic (EM) locators, tracer wires, and sondes, capture high-resolution imagery and video, enabling detailed condition assessments and precise mapping of sewer lines, lateral connections, and manholes. The resulting data is uploaded to the SiteMap® platform (patent pending), where you can view, analyze, and share it with key team members, subcontractors, and stakeholders in real time.
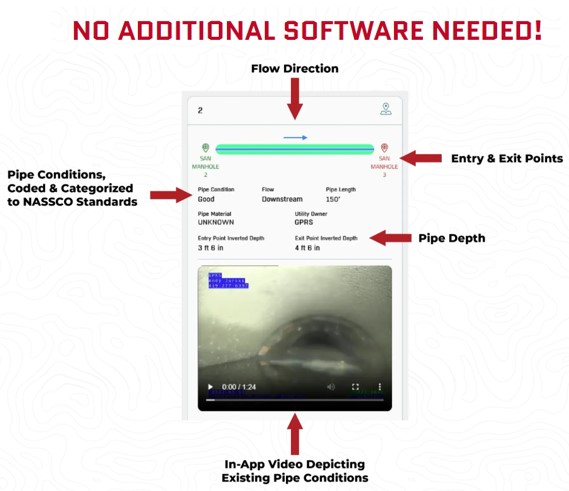
There is no additional software required to see each geolocated pipe segment, the entry & exit points for that segment, pipe material, depth, flow direction, and the condition of the segment, coded and categorized to NASSCO standards. Plus, in-app video depicting your existing pipe conditions, allowing you to proactively plan, maintain, repair and upgrade your sanitary and storm systems to:
• Reduce potholing & destructive excavation
• Reduce utility strikes & service interruptions
• Find damaging cross bores before they compromise your system
Regardless of industry, this new tool is a game-changer. As GPRS Chief Strategy Officer, Jason Schaff said in a recent press release on the subject, “Two of the biggest problems we’ve been trying to tackle for our customers, especially those managing large campuses or municipalities, are how we can give them concrete evidence showing them exactly where in the world their sewer lines are, and what condition they are in, so that they have access to that data in the palm of their hand 24/7.”
“We believe SiteMap’s Sewer Layer update solves both issues; not only can you see direct video of every pipe segment and its condition, each line is geolocated with real-time kinematic positioning (RTK), so you can be certain of the location of every pipe in your wastewater infrastructure. And since it’s all delivered via SiteMap, you have complete access and control of your wastewater system data from anywhere, anytime you need it, to plan upgrades, expansions, and repairs.”
How Does The SiteMap Sewer Layer Help Facilities Managers?
Facilities managers in higher education, health care, manufacturing, municipal wastewater, and virtually every industry could shift to proactive vs. reactive maintenance and repair schedules, provide concrete sewer budget items for capital planning, avoid service interruptions, locate previously unknown sanitary and storm sewer lines, and eliminate construction delays.
University campuses often span hundreds of acres with sewer infrastructure that spans centuries. With SiteMap, operations and facilities managers can identify root intrusions, pipe deformation, or blockages before they escalate into costly emergencies. For example, The University of Toledo now has its entire sanitary and storm sewers, water lines, steam lines, and more, mapped and catalogued in SiteMap for their use.
In manufacturing environments, unplanned downtime due to sewer failures can halt production and compromise safety. SiteMap allows plant engineers to monitor critical sewer lines beneath production floors, loading docks, and chemical storage areas. A Midwest automotive manufacturer leveraged SiteMap to provide a full site scan of its facilities, covering 3,700,000 s.f. and 419 acres while it retooled and renovated.
“One of the biggest issues we were solving [for the auto plant] was scanning and collecting the data proactively ahead of the project rather than waiting until the construction phase. This gave them the subsurface information they needed to design and plan with accurate information that we updated from the out of date and inaccurate as builts.” – Nate Stair, GPRS SiteMap Market Segment Leader & Account Executive
Municipal wastewater departments benefit from SiteMap’s ability to centralize data across multiple sites and teams. With aging infrastructure and limited budgets, municipalities must prioritize repairs based on accurate condition assessments. The City of Fremont, California utilized GPRS’ video pipe inspection & SiteMap to accurately locate and track the remediation of 10 dangerous cross bores caused by directional drilling fiber line installations. The platform’s cloud-based access enabled collaboration between public works, engineering consultants, and contractors, streamlining their repairs.
Municipalities across the U.S. are requiring pre and post-cross bore inspections surrounding fiber line installations to avoid dangerous and costly sewer problems caused by utility line intrusions.
Health care facilities, where sanitation and operational continuity are paramount, gain critical visibility of data with SiteMap.
Hospitals and medical campuses often have complex, undocumented sewer networks. General contractor Rudolph Libbe used SiteMap® to trace sewer lines that were more than 150 years old, and verify the locations of all their subsurface infrastructure prior to building a new central utility plant at Mercy Health’s St. Vincent Medical Center. With precise mapping and video documentation, the facilities team coordinated to locate the CUP much closer to the main hospital than usual. This was only possible with exceptional subsurface as-builts.
What Are The Benefits of SiteMap's Sewer Layer?
Key benefits of the SiteMap Sewer Layer include the ability to:
• Navigate to any individual line, lateral, or feature in your storm or sanitary sewer system
• Access the geolocated, tagged, and annotated video feed of your pipe conditions anytime, anywhere at the touch of a button
• Filter your data based on pipe condition and level of defect
• Securely share any segment of your sewer data with your team, contractors, vendors, and subcontractors to eliminate confusion & miscommunication
• Maintain a permanent record of your sewer data for future planning and proactive maintenance
The bottom line: GPRS’ new SiteMap Sewer Layer gives facilities managers a powerful tool for reducing risk, optimizing maintenance, and extending the life of critical wastewater infrastructure.
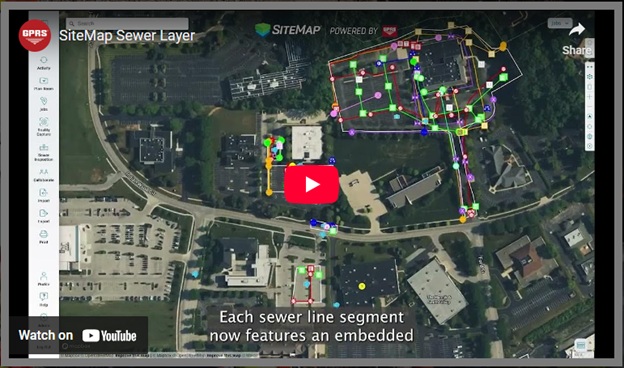
What can we help you visualize? Schedule your personal SiteMap demonstration and view information about the new Sewer Layer, here.
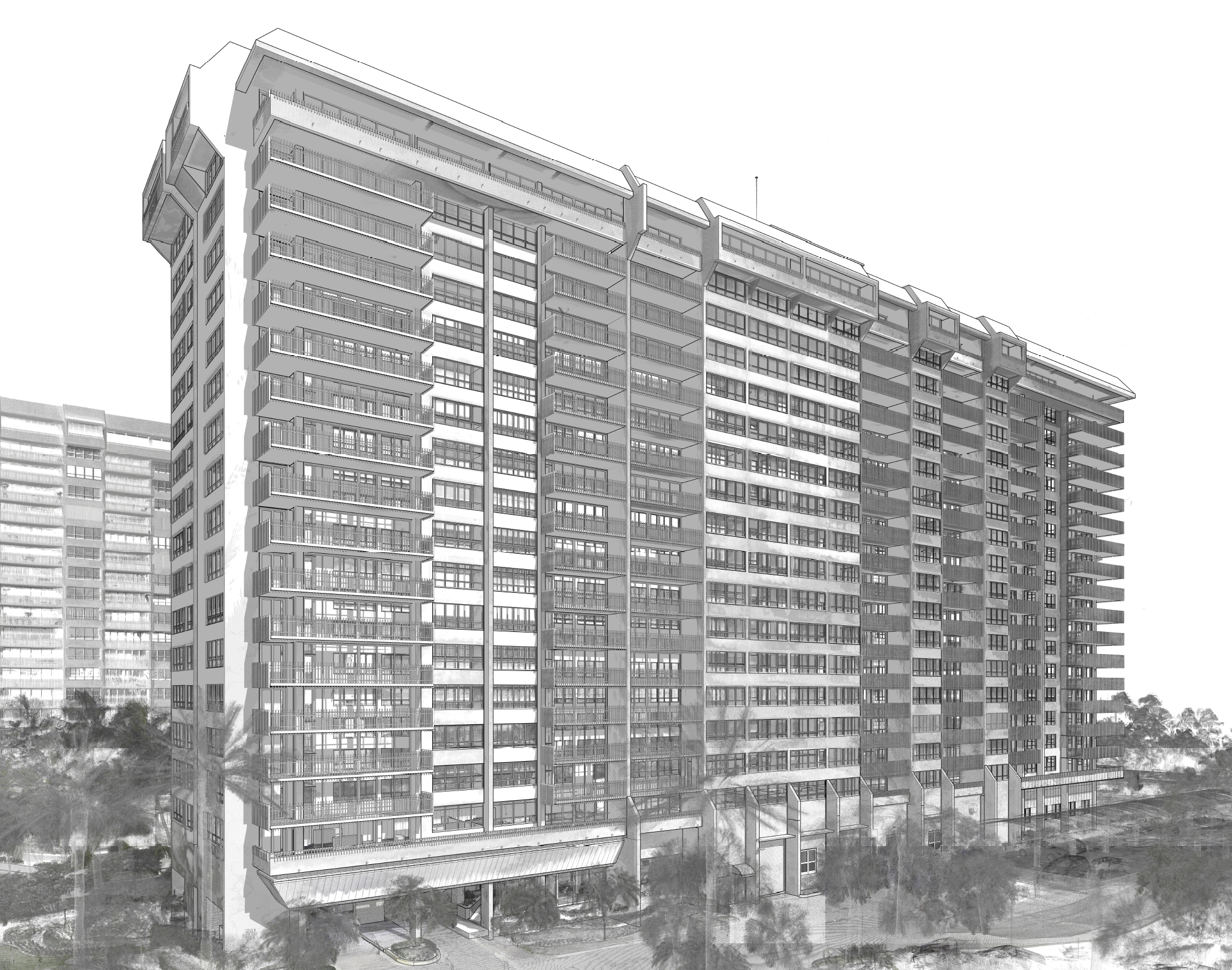
GPRS Reality Capture Services Aid ADA Renovations to Luxury Condos
A decades-old, luxury condominium complex on a man-made island off the southern coast of the United States was set to undergo renovations to bring the buildings into ADA compliance.
The contractor overseeing the project called GPRS to provide reality capture services that ensured their work started accurate and stayed accurate.
Project Manager John Lehaney traveled to the island to conduct 3D laser scans in and around the three existing towers. Our client required accurate floor plans of the first floors, and scans of the exteriors of each of the three buildings to expedite project planning. But data capture needed to be completed without disrupting tenants and while working around the active construction of an additional condo tower on the island.
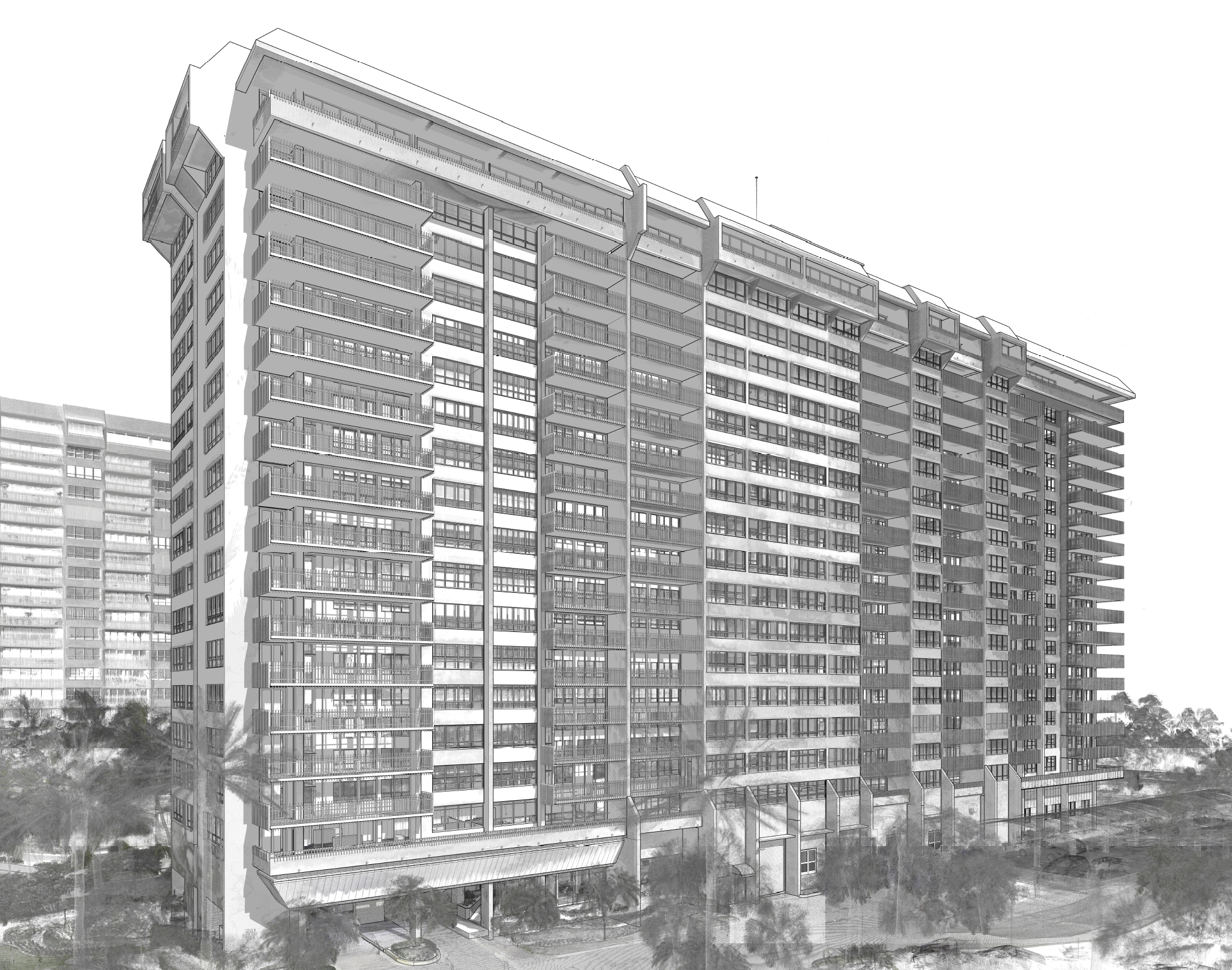
The scope of work also tripled in size as the client came to fully understand what data they required to complete their project.
“It went from being about, I want to say, 9-10,000 s.f. of building [scanning]… to around 30,000 s.f. of building,” Lehaney said. “So, it consisted of the lobby, the carports, community spaces, storage lockers, staff housing, and then one of the buildings, instead of staff housing, [we needed to scan] what was actually a tenant’s condo unit. So, we had to get special access to get in there from security.”
What Does it Mean to be ADA Compliant?
The Americans with Disabilities Act (ADA) is a federal law that prohibits discrimination based on disability and ensures equal access and opportunities for individuals with disabilities in various area, including employment, transportation, public accommodations, and communications
For buildings, ADA compliance means physical accessibility through the inclusion of features like ramps, accessible restrooms, and clear pathways.
How GPRS Helps You Comply with ADA Requirements
GPRS offers reality capture services that can be used to inspect ramps and cross slopes – the angle of a road’s surface perpendicular to the direction of travel, designed to allow water to drain away effectively – to ensure they comply with ADA requirements.
When you need to renovate to achieve compliance, our laser scanners collect the accurate, actionable data that our in-house Mapping & Modeling Team needs to create floor plans, virtual walkthroughs, BIM models, and whatever other deliverables you need to get the job done right.
At the condos, Lehaney deployed the Leica RTC360 and P50 ScanStation to obtain the desired point cloud data.
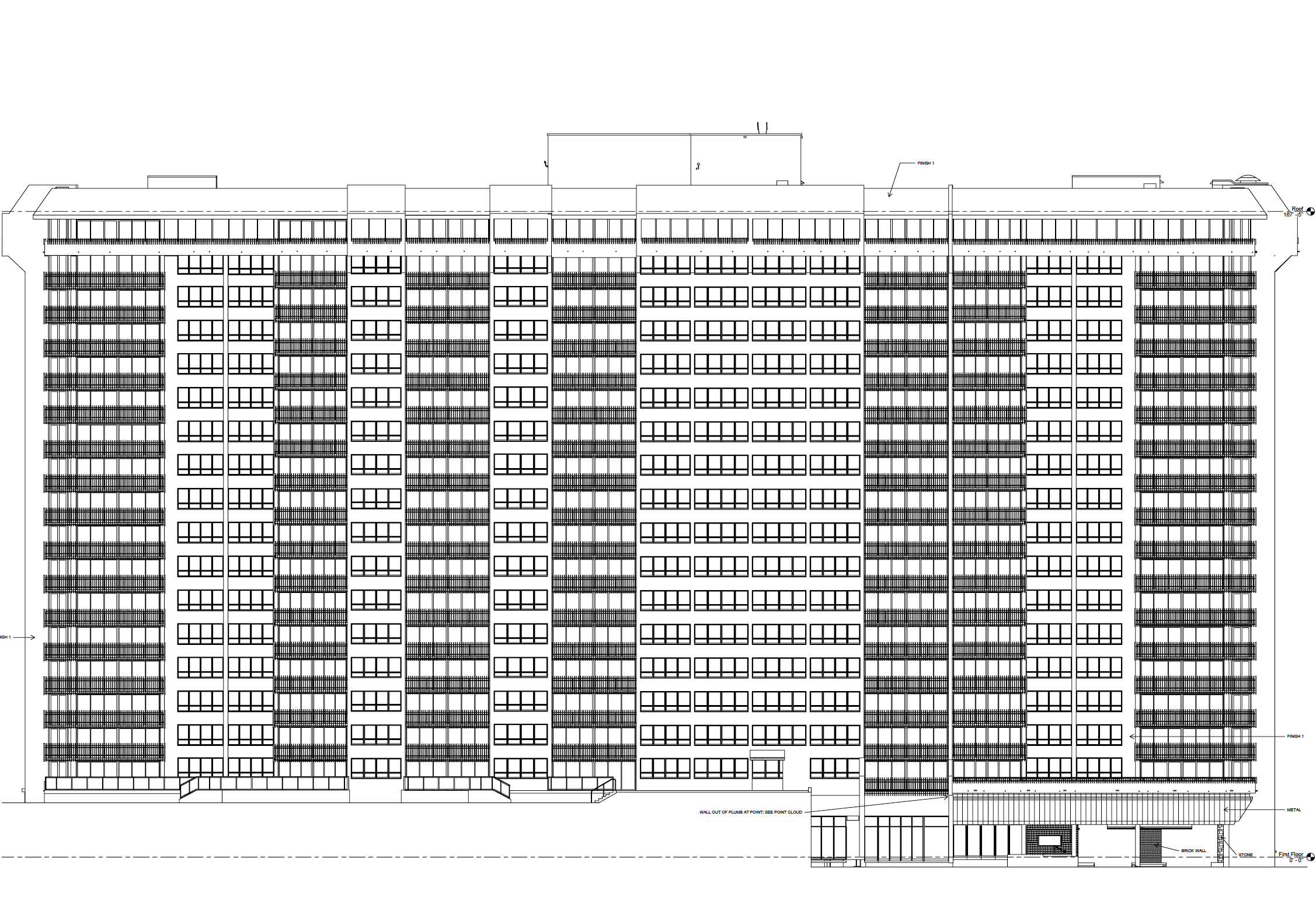
The Leica RTC360 3D laser scanner combines a high-performance laser scanner with Cyclone FIELD 360, a mobile-device app on a tablet computer, to capture and automatically pre-register scans in real time. With a measuring rate of up to 2 million data points per second and advanced HDR imaging system, you can have 3D colorized point clouds with 2-4 mm accuracy in under 2 minutes. Automatic targetless field registration (based on VIS technology) and the seamless transfer of data from site to office reduces time spent in the field, maximizing project productivity.
Leica P-Series ScanStations deliver the highest quality point cloud data and HDR imagery at an extremely fast scan rate of up to 1 million points per second and ranges of more than 1 kilometer. The P-series Leica laser scanners can tie to survey control, achieve 2-4mm accuracy and have real-time liquid filled dual axis compensators to help mitigate movement and ensure level scans. These scanners deliver highly detailed point clouds mapped in realistic clarity.
With this equipment, Lehaney was able to collect the data needed for GPRS’ Mapping & Modeling Team to create the floor plans and other deliverables the client needed to complete their work efficiently, and without the delays and mistakes they would have incurred without accurate as-built information.
“Overall, it was a pretty smooth project,” he said. “[The data] came out nice and clean… It’s just good data for them to have, including the hardscape information outside the building too.”
From condo towers to municipal sewer systems and everything in between, GPRS Intelligently Visualizes The Built World® to keep your projects on time, on budget, and safe.
What can we help you visualize?
Frequently Asked Questions
How do I know if 3D laser scanning or other reality capture services are right for my project?
Almost any project that requires as-built information can benefit from a laser scanning survey. Talk with our experts and start your 3D laser scanning survey project today.
What deliverables can GPRS provide when conducting reality capture services?
We can provide 3D modeling in many formats such as:
- Point Cloud Data (Raw Data)
- 2D CAD Drawings
- 3D Non-Intelligent Models
- 3D BIM Models
- JetStream Viewer
Customizable Deliverables Upon Request
- Aerial Photogrammetry
- Comparative Analysis
- Deformation Analysis
- Digital Drawings of GPR Markings
- Floor Flatness Analysis/Contour Mapping
- New Construction Accuracy Analysis/Comparative Analysis
- Point Cloud Modeling Training Webinars
- Reconciliation of Clients 2D Design Drawings
- Reconciliation of Clients 3D Design Model
- Structural Steel Shape Probability Analysis
- Template Modeling
- Volume Calculations
- Wall Plumb Analysis
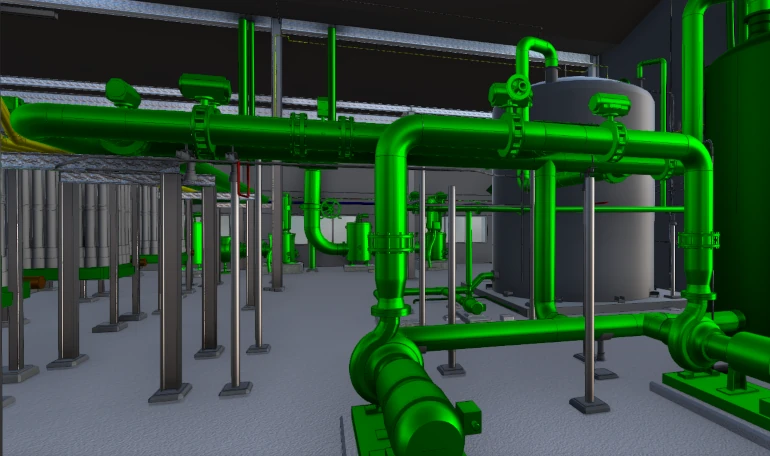
How Does 3D Laser Scanning Aid MEP Design and Layout?
For an engineer managing MEP design and execution, precision and coordination are imperative. Successful design, fabrication, and installation depend on the knowledge of existing site conditions, and reality capture via 3D laser scanning delivers just that.
With a single 3D laser scan, millions of site dimensions are captured in a point cloud, providing the data needed to create accurate 3D BIM models. BIM models allow MEP engineers to design HVAC layouts, plan electrical runs, and route plumbing systems with confidence. Plus, they help to avoid clashes, improve spatial planning, and streamline installation.
Scan-to-BIM workflows reduce human error, enhance coordination across trades, and save time during prefabrication and field installation. With advanced features like clash detection and construction sequencing, BIM technology helps MEP engineers visualize complex systems and streamline execution.
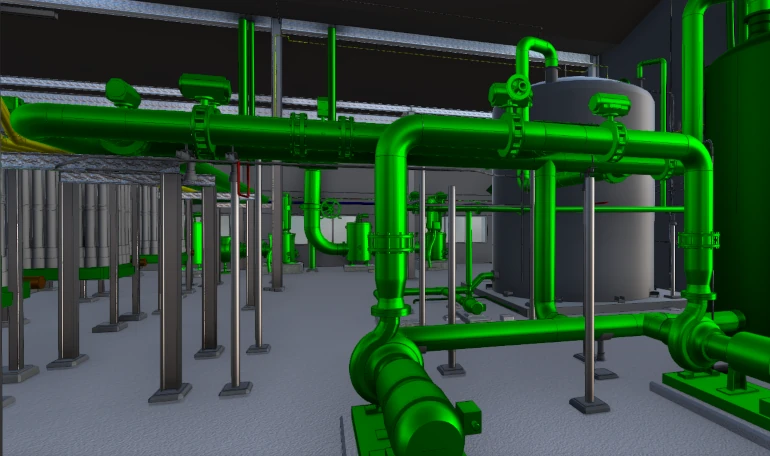
How Does 3D Laser Scanning Benefit Mechanical Contractors?
3D laser scanning delivers precise data that helps mechanical contractors improve planning, fabrication, and installation. Here’s how 3D laser scanning helps:
- Digitally capture exact MEP dimensions, layouts, and locations to minimize rework
- Reduce time spent in hazardous, hard-to-reach areas, or clean rooms
- Use BIM models to route efficient paths for HVAC, piping, and mechanical systems
- Overlay data with design models to identify clashes between mechanical systems before installation
- Prefabricate ductwork and piping assemblies with precision
What are the Benefits of 3D Laser Scanning for Electrical Contractors?
3D laser scanning offers electrical contractors a smarter, faster way to plan and execute installations with precision. 3D laser scan technology can:
- Capture exact locations of panels, conduits, junction boxes, and cable trays
- Minimize time spent in hazardous areas by capturing site data quickly
- Overlay laser scan data to build precise electrical design models
- Detect clashes between electrical systems and other trades before installation
- Plan conduit and wiring paths for maximum efficiency
- Speed up large installs with better coordination and data-driven decisions
How Does 3D Laser Scanning Help Plumbing Contractors?
3D laser scanning and BIM provide the precise data plumbing contractors need to plan efficiently, install faster, and avoid costly errors. 3D laser scanning & BIM services can:
- Capture pipe dimensions, slopes, and connections to eliminate guesswork and reduce field errors
- Visualize plumbing systems in relation to structural and MEP elements to prevent clashes and plan optimal routing
- Prefabricate assemblies with confidence in fit and alignment, minimizing rework and material waste
- Coordinate installation steps across teams to avoid delays and ensure systems are installed to spec
Case Study Example: 3D BIM Model Aids Wastewater Treatment Plant Heat Exchanger Upgrades
Faced with dense mechanical and piping systems, ABC Piping Co. turned to GPRS to 3D laser scan the Southerly Wastewater Treatment Plant and create an LOD 300 BIM model of its complex heat exchanger system. The model delivered accurate pipe sizes, routing, and spatial layout, enabling precise MEP design updates without guesswork or costly rework.
“We are delivering an architectural/structural 3D BIM model and MEP 3D BIM model for design and engineering, providing a 3D space for all disciplines to work together to identify and resolve clashes before system integration begins, ensuring a smooth retrofit with minimal rework,” Belinda Thompson, GPRS CAD Technician stated.
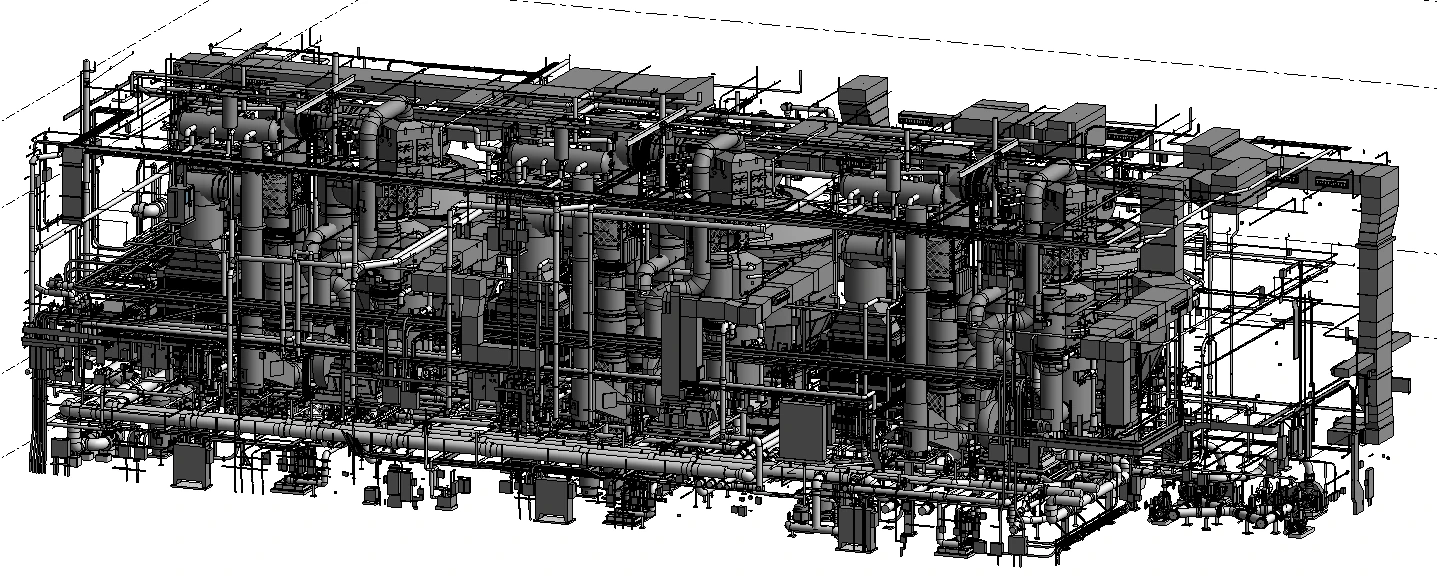
How Does a 3D Laser Scanner Work?
The primary way a laser scanner works is to send light pulses at high speed which reflect off objects and return to the scanner’s sensor, known as LiDAR technology. For each pulse, the distance between the scanner and object is measured by determining the elapsed time between the sent and received pulses. Each data point is converted to a pixel with a known x, y, and z coordinate for accurate reality capture.
Laser scans are taken in multiple positions around a site from varying viewpoints. Millions of data points are captured and processed into a point cloud, creating an accurate 3D as built data set of the site. This all happens very quickly, with some scanners, like the Leica RTC360, capturing and calculating 2 million points per second with 2-4 mm accuracy.
What is Scan-to-BIM?
Scan to BIM is the process of digitally capturing a site with a 3D laser scanner and using the data to create a BIM model. BIM models provide a comprehensive view of a building that can be used throughout its lifecycle – during the design phase, construction phase, and operation phase of the building.
Scan to BIM gives MEP contractors highly accurate, field-verified models that streamline design, eliminate clashes, and ensure systems fit perfectly before installation begins.
Why Choose GPRS for 3D Laser Scanning?
GPRS is the trusted leader in 3D laser scanning and BIM modeling, helping you to design and install MEP systems with precision. Our laser scanning delivers millimeter-accurate site data, capturing the exact layout, dimensions, and locations of existing system elements. This data is expertly converted into custom 2D CAD drawings and 3D BIM models that enable precise engineering, prefabrication, and fit-out. This ensures that MEP system updates are designed to fit precisely within the existing space, reduces errors and rework, and delivers superior results for your project.
Through SiteMap® (patent pending), our cloud-based GIS software platform, clients gain secure, 24/7 access to their drawings, models, and deliverables, all in one place. With GPRS, you get MEP clarity from day one and confidence throughout your build. Every GPRS customer receives complimentary Personal Level SiteMap access as part of our services.
What can we help you visualize?
Frequently Asked Questions
How does 3D laser scanning improve accuracy in MEP design?
It captures millions of precise measurements of existing site conditions, creating a reliable foundation for BIM models that help engineers design systems with confidence and avoid costly errors.
What role does scan-to-BIM play in coordinating MEP systems?
Scan-to-BIM workflows allow teams to visualize spatial relationships, detect clashes early, and plan installations that integrate seamlessly with other building components.
Can 3D laser scanning help with prefabrication and installation?
Yes, by providing exact dimensions and layouts, it enables off-site fabrication of MEP components that fit perfectly on-site, reducing rework and speeding up installation.
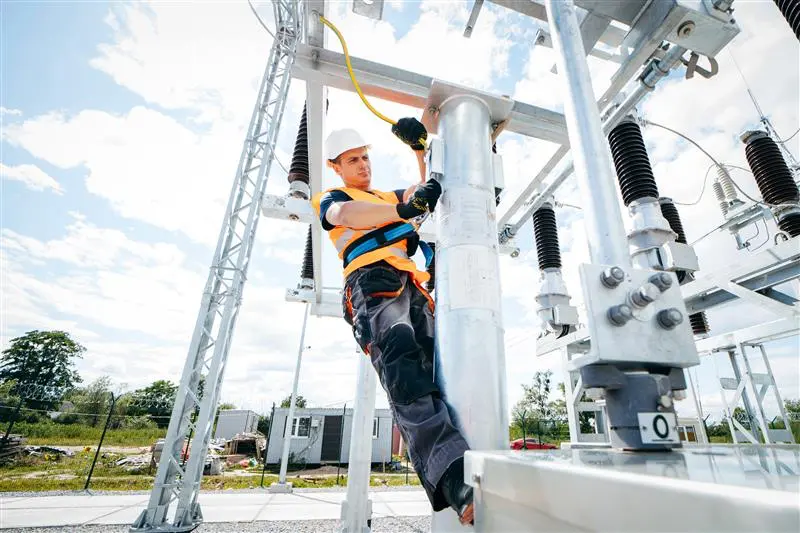
What is a Grounding Grid?
Often hidden beneath power substations, industrial facilities, and large electrical installations, grounding grids play a vital role in protecting equipment, infrastructure, and – most importantly – human life.
A grounding grid is a network of interconnected conductors, typically made of copper or galvanized steel, buried in the earth to provide a low-resistance path for electrical currents to safely dissipate into the ground. These grids are designed to handle fault currents, lightning strikes, and other transient over voltages by directing them away from equipment and personnel.
Grounding grids form the foundation of an effective grounding – also known as earthing – system, which is essential for maintaining voltage stability and ensuring the safe operation of electrical equipment. They are most commonly found in:
- Electrical substations
- Power generation plants
- Industrial facilities
- Data centers
- Telecommunications hubs
- Wind and solar farms
- Hospitals
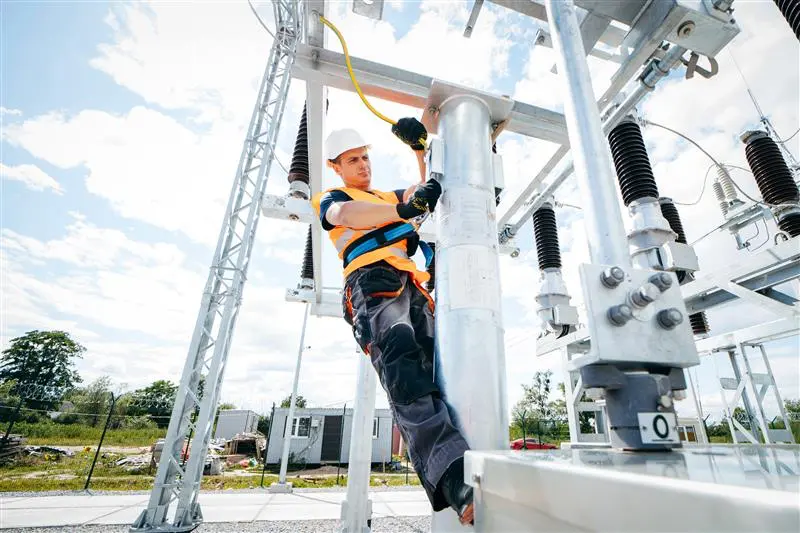
Why Grounding Is Necessary
Grounding serves several critical purposes:
Personnel Safety
In the event of a fault – a failure in the electrical system caused by incidents such as outages or lightning strikes – grounding ensures that dangerous voltages do not persist on exposed conductive parts. This minimizes the risk of electric shock.
Equipment Protection
Sensitive electrical and electronic equipment can be damaged by transient voltages. A grounding grid helps divert these surges safely into the earth.
System Stability
Grounding provides a reference point for system voltages, which is essential for the proper operation of protective relays and circuit breakers.
Lightning Protection
Grounding grids help dissipate the high-energy currents from lightning strikes, reducing the risk of fire or equipment failure.
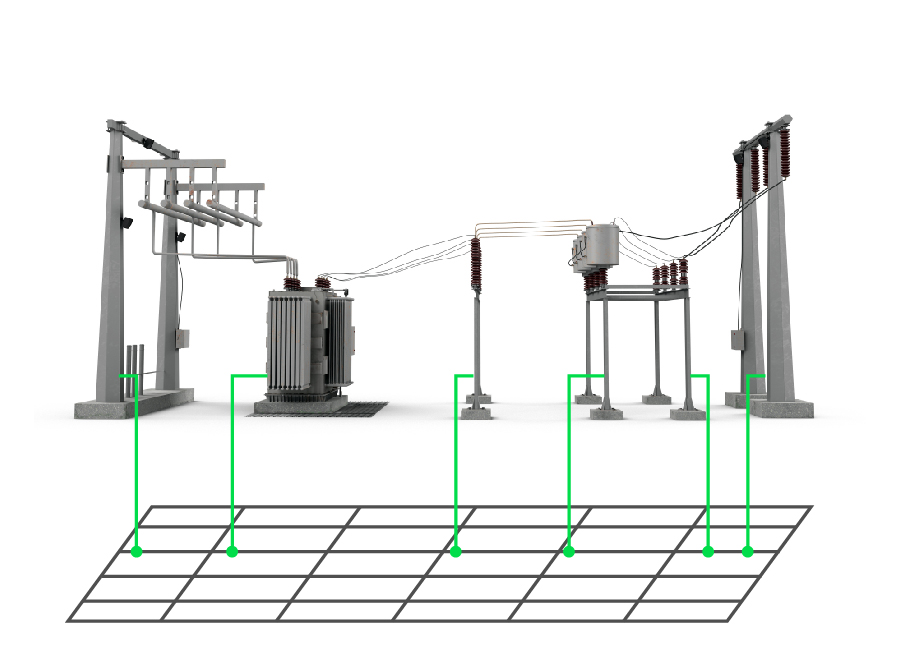
Components of a Grounding Grid
A typical grounding grid consists of the following elements:
- Horizontal Conductors: These are laid out in a grid pattern (e.g., square or rectangular) and buried at a shallow depth, usually one to two feet below the surface
- Vertical Ground Rods: Driven deeper into the earth to improve the overall grounding resistance, especially in areas with high soil resistivity
- Grounding Electrodes: These may include rods, plates, or rings that enhance the contact area with the soil
- Connections to Equipment: All metallic parts of electrical equipment, enclosures, and structures are bonded to the grid
The design of the grid is influenced by factors such as soil resistivity, fault current magnitude, and the physical layout of the facility.
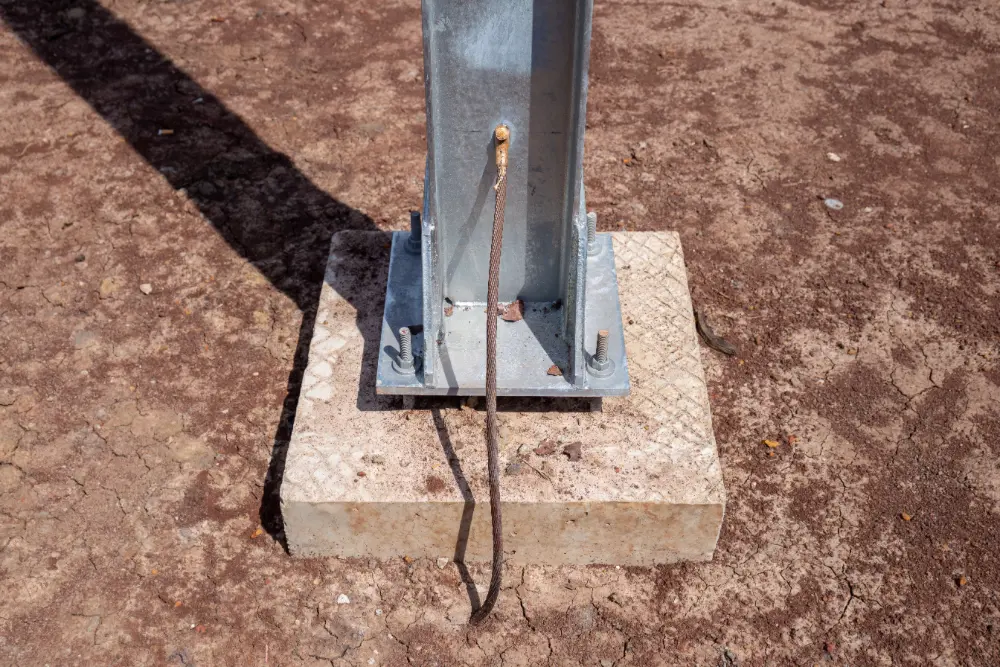
How Grounding Grids Work
When a fault occurs – say, a lightning strike hits a transmission line, or a transformer develops an internal short – the resulting surge of electrical energy must be safely dissipated. The grounding grid provides a low-impedance path for this current to flow into the earth.
Here’s how the process works:
- Current Injection: The fault current enters the grounding grid through the connected equipment or structure.
- Current Distribution: The grid distributes the current across its network of conductors, minimizing localized heating and voltage rise.
- Dissipation into Earth: The current flows from the grid into the surrounding soil, where it is absorbed and neutralized.
The effectiveness of this process depends on the resistance to ground, which is influenced by soil type, moisture content, temperature, and the geometry of the grid.
Key Design Considerations
Designing a grounding grid is a complex engineering task that must balance safety, performance, and cost. Key considerations include:
Soil Resistivity
Soil resistivity is a measure of how easily electrical current can pass through the ground. It varies with soil composition, moisture, and temperature. Engineers often conduct a soil resistivity survey using the Wenner or Schlumberger method to inform the grid design.
Grid Geometry
The layout of the grid – spacing between conductors, depth of burial, and number of ground rods – affects its resistance and current distribution. A denser grid with more conductors generally offers better performance.
Touch and Step Voltage
These are critical safety parameters:
- Touch Voltage: The potential difference between a grounded object and the feet of a person touching it
- Step Voltage: The voltage difference between two points on the ground a step apart
The grid must be designed to keep these voltages within safe limits during fault conditions.
Corrosion Resistance
Materials used in grounding grids must withstand corrosion over time. Copper is preferred for its conductivity and durability, but galvanized steel is often used for cost reasons.
Testing and Maintenance
Even the best-designed grounding grid can degrade over time due to corrosion, soil movement, or construction activities. Regular testing is essential to ensure continued performance. Common tests include:
- Fall-of-Potential Test: Measures the resistance between the grid and remote earth
- Clamp-on Ground Resistance Test: A non-intrusive method for measuring resistance in multi-grounded systems
- Soil Resistivity Testing: Periodically reassessing soil conditions to detect changes that may affect grounding performance
Maintenance may involve replacing corroded conductors, improving soil conductivity (e.g., with bentonite or conductive concrete), or expanding the grid.
How GPRS Helps Protect Grounding Grids During Excavation
Grounding grids are an indispensable element of power infrastructure, providing a vital layer of protection against electrical hazards. By accurately locating and mapping these systems before excavating or trenching near them, we can mitigate risks, protect personnel and equipment, and ensure the continued reliability and resilience of our electrical networks.
GPRS offers 99.8%+ accurate utility locating services designed to mitigate the risk of subsurface damage by providing you with the information you need to break ground safely. Using ground penetrating radar (GPR) scanners and electromagnetic (EM) locating, our SIM-certified Project Managers create comprehensive infrastructure maps to keep you on time, on budget, and safe.
What can we help you visualize? Click below to schedule a service or request a quote today!
Frequently Asked Questions
What does GPRS give me when I hire them to conduct a utility locate?
Our Project Managers flag and paint our findings directly on the surface. This method of communication is the most accurate form of marking when excavation is expected to commence within a few days of service.
GPRS also uses Real-Time Kinematic (RTK) Positioning to collect data points of findings. We use this data to generate a plan, KMZ file, satellite overlay, or CAD file to permanently preserve results for future use.
GPRS does not provide land surveying services. If you need land surveying services, please contact a professional land surveyor.
Please contact us to discuss the pricing and marking options your project may require.
Can GPR scanning locate PVC piping and other non-conductive utilities?
GPR scanning is exceptionally effective at locating all types of subsurface materials. There are times when PVC pipes do not provide an adequate signal to ground penetrating radar equipment and can’t be properly located by traditional methods. This is why GPRS Project Managers are expertly trained at multiple methods of utility locating, including utilizing electromagnetic (EM) locating, to complement GPR scanning.
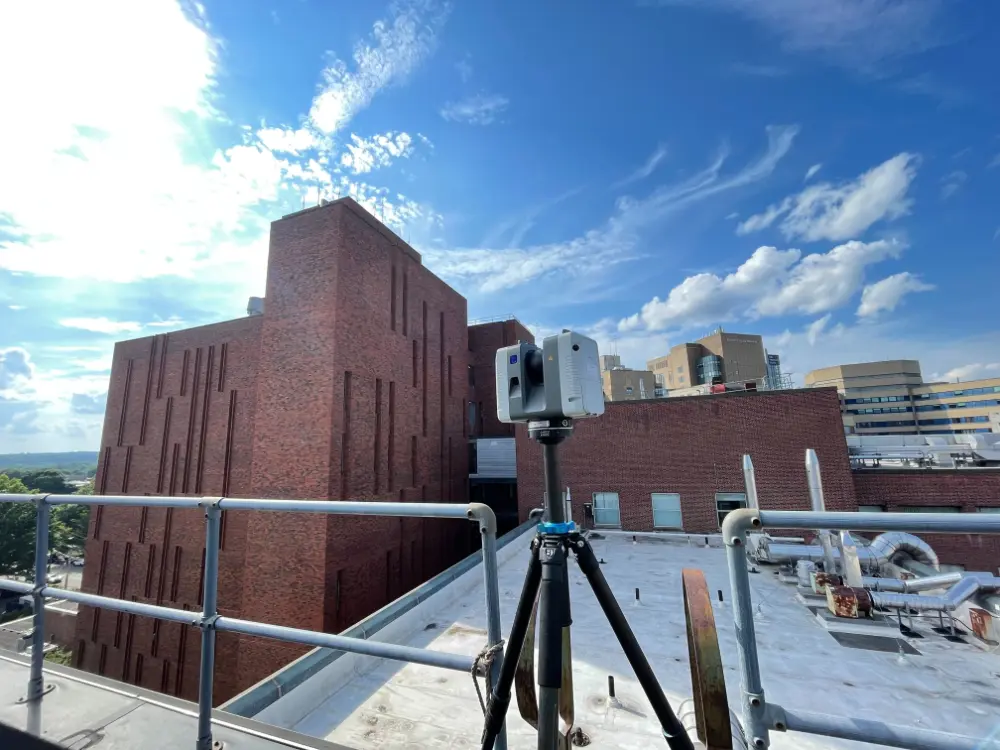
GPRS Reality Capture Services Help University Renovate Medical Research Facility
When one of America’s most prestigious universities was planning to renovate their advanced medical research facility, they relied on reality capture data and deliverables from GPRS to help them start accurate and stay accurate.
A team of GPRS Project Managers 3D laser scanned every inch of the six-story building, including the exterior façade, to capture the accurate existing conditions documentation the university required.
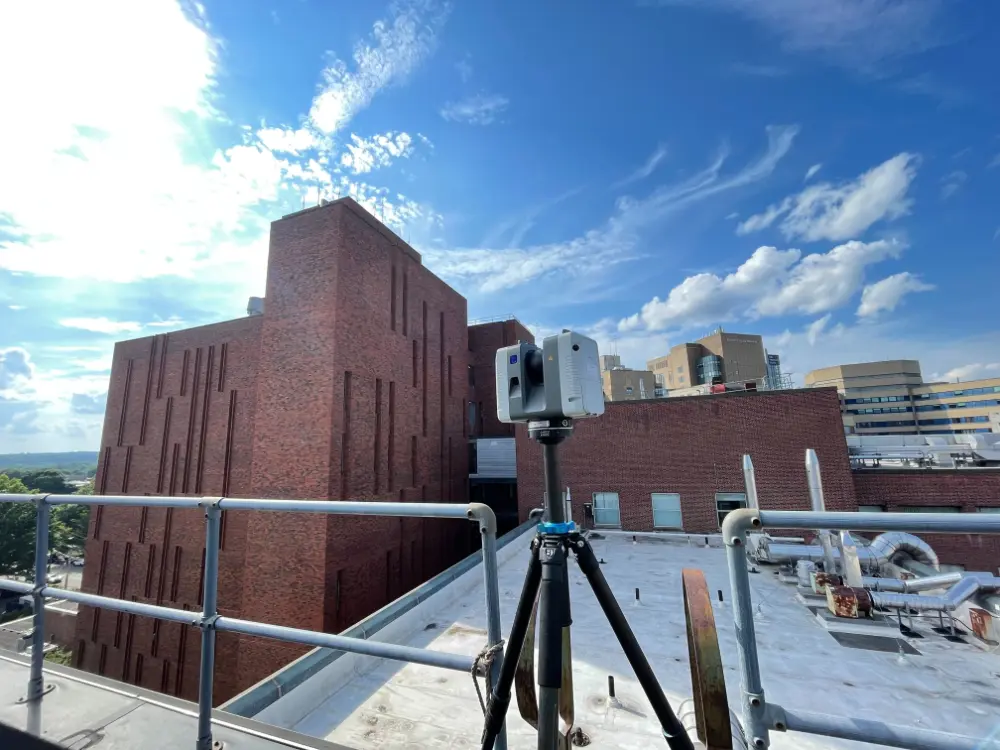
Accurate, real-time as-built data is essential for informed decision-making and seamless collaboration. With precise design plans from the start, architects, contractors, engineers, and facility managers can streamline fieldwork and minimize change orders, plus avoid delays and extra costs.
GPRS Reality Capture Services provide clients with precise as-built documentation of buildings and infrastructure using advanced Leica laser scanners, delivering point clouds, 2D CAD drawings, and 3D BIM models to streamline project planning and construction.
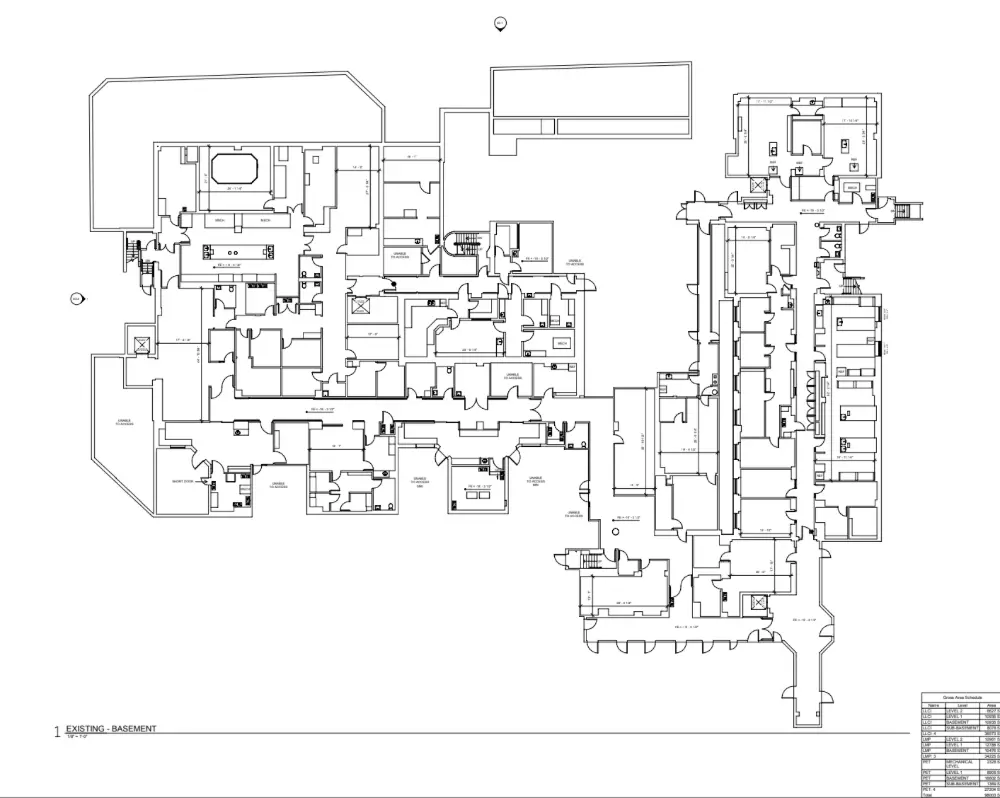
At the university, the GPRS team had to conduct its scans after hours, so as not to disrupt the research being conducted in the facility and so that medical equipment such as MRI machines could be turned off and not interfere with the 3D laser scanning equipment.
“They wanted us in there with as few people as possible, so we’re not disturbing anything,” said GPRS Sales Development Representative John Lehaney, who was a Project Manager on the assignment. “Essentially, we were in there to document everything in sight that they were looking to renovate. They had no existing floor plans.”
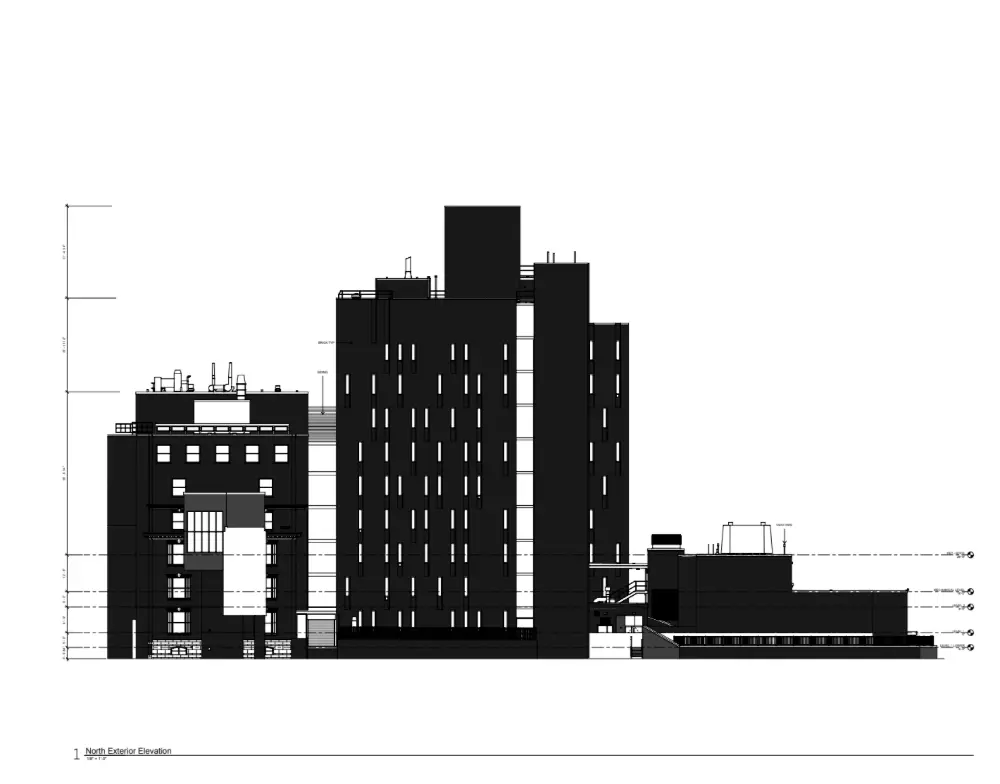
GPRS deployed the Leica RTC360, and NavVis VLX 3D laser scanners to capture 2-4 mm accurate data of the research facility.
The Leica RTC360 3D laser scanner combines a high-performance laser scanner with Cyclone FIELD 360, a mobile-device app on a tablet computer, to capture and automatically pre-register scans in real time. With a measuring rate of up to 2 million data points per second and advanced HDR imaging system, you can have 3D colorized point clouds with 2-6 mm accuracy in under 2 minutes. Automatic targetless field registration (based on VIS technology) and the seamless transfer of data from site to office reduces time spent in the field, maximizing project productivity.
The NavVis VLX captures survey-grade point clouds with two multi-layer LiDAR sensors equipped with SLAM (simultaneous localization and mapping) technology. Four cameras are positioned on top of the device, taking high resolution images in every direction for complete 360º capture – all without the operator appearing in the field of view.
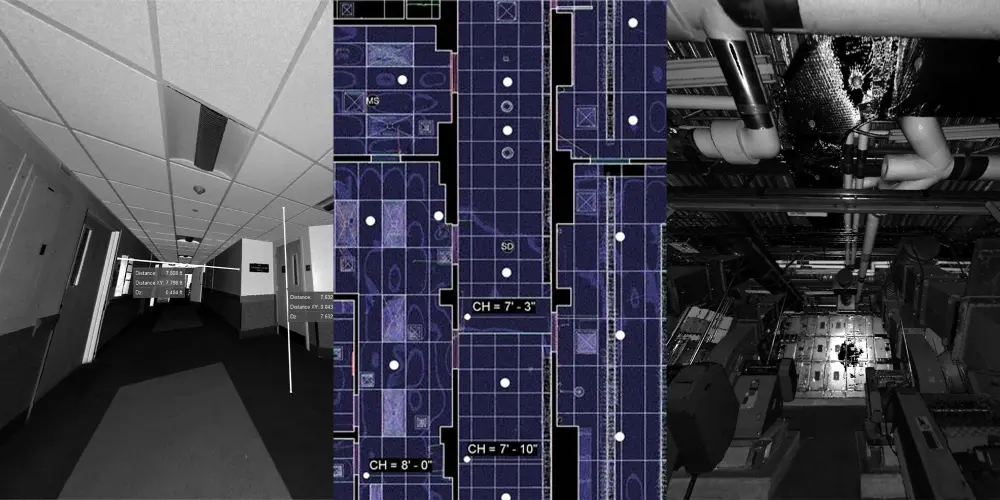
With the RTC360 and NavVis, Lehaney and his fellow Project Managers were able to collect the data needed for GPRS’ in-house Mapping & Modeling Team to create a 3D Revit model, floor plans, a roof plan, a TruView Virtual Site Visit, exterior elevations, and reflected ceiling plans (RCPs) to assist the university in accurate design and planning for their renovations.
The university had the accurate data they needed, and it was obtained without disrupting the vital research being conducted in the facility.
From visualizing school campuses to locating buried utilities and beyond, GPRS Intelligently Visualizes The Built World® to keep your projects on time, on budget, and safe.
What can we help you visualize?
Frequently Asked Questions
How do I know if 3D laser scanning is right for my project?
Almost any project that requires as-built information can benefit from a laser scanning survey. Talk with our experts and start your 3D laser scanning survey project today.
What deliverables can GPRS provide?
We can provide 3D modeling in many formats such as:
- Point Cloud Data (Raw Data)
- 2D CAD Drawings
- 3D Non-Intelligent Models
- 3D BIM Models
- JetStream Viewer
Customizable Deliverables Upon Request
- Aerial Photogrammetry
- Comparative Analysis
- Deformation Analysis
- Digital Drawings of GPR Markings
- Floor Flatness Analysis/Contour Mapping
- New Construction Accuracy Analysis/Comparative Analysis
- Point Cloud Modeling Training Webinars
- Reconciliation of Clients 2D Design Drawings
- Reconciliation of Clients 3D Design Model
- Structural Steel Shape Probability Analysis
- Template Modeling
- Volume Calculations
- Wall Plumb Analysis
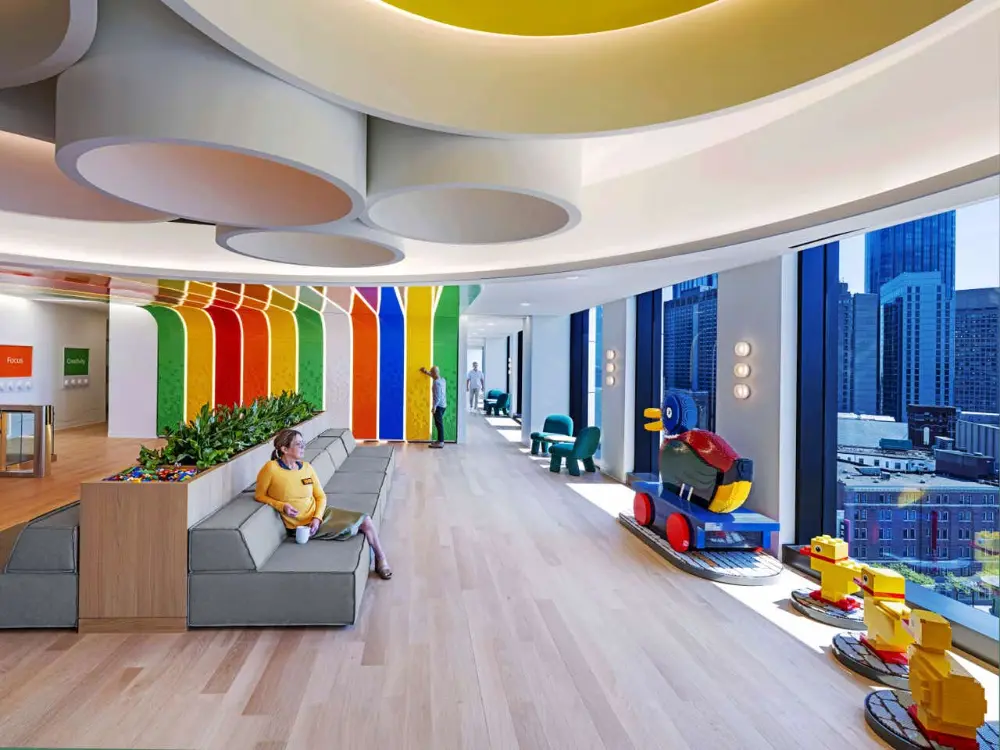
World’s Largest Toy Company Increasing Investment in U.S. Operations
The LEGO Group’s new, 157,000 s.f. U.S. Hub in Boston, Massachusetts is just the latest example of the world’s largest toy company’s increasing its investment in its North American operations.
According to a press release on the LEGO Group’s website, “the new state-of-the-art office will be the company’s new U.S. Hub and support its ongoing commitment to reaching more children across the U.S. with LEGO® play.”
The opening of the Danish toymaker’s new U.S. headquarters signals the beginning of the end for its former Connecticut headquarters, which the company has occupied for more than 50 years.
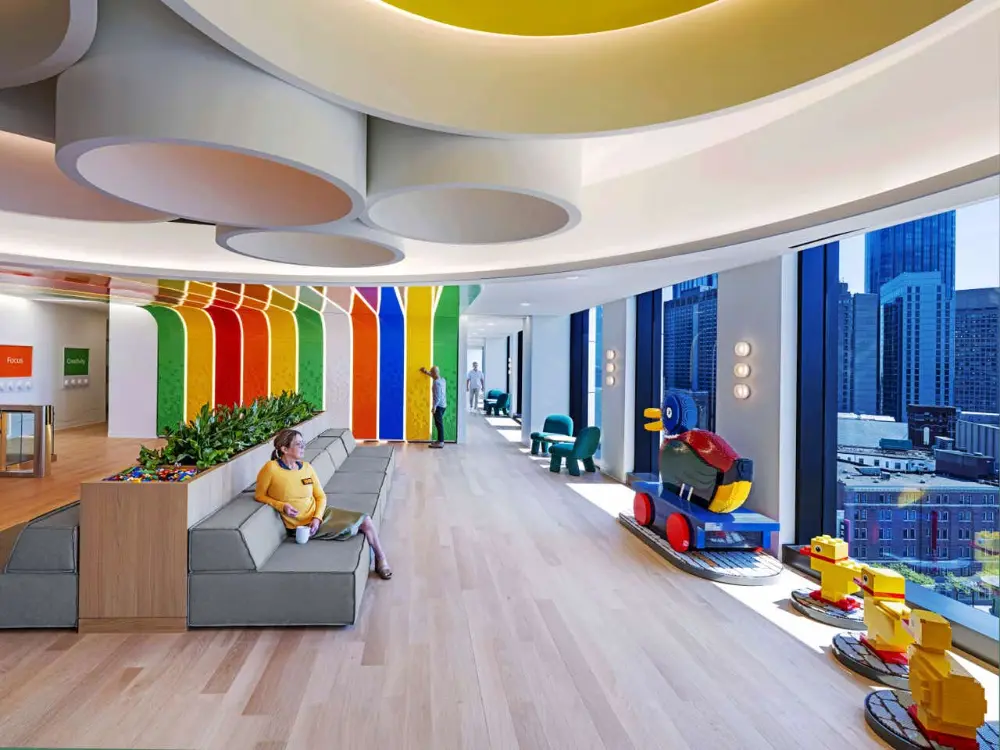
"This fantastic new LEGO® workspace is an important part of our US investment strategy, fast becoming a talent magnet in this important market,” said LEGO Group CEO Niels B. Christiansen. “The Boston Hub will open up new ways for LEGO colleagues to create, connect, and grow as we continue our mission to inspire and develop the builders of tomorrow across the US.”
The LEGO Group’s new HQ is LEED Gold and WELL Gold certified and features over 660 workstations, complimentary gym access, parents’ rooms and flexible wellness areas for employees to engage in activities like medication, prayer and relaxation, playful common spaces, sky terraces, and over 90 meeting spaces.
Over 800 employees will work out of the six-floor office, which was built by Structure Tone and designed by BDG, and is situated in the Lyrik, a 20-story office building completed last year.
Ryan Megenedy, senior account executive at Structure Tone, acknowledged in an interview with Engineering News-Record that building a space for a company like the LEGO Group “required a lot of creativity.”
“Many elements of the design echo the ‘studs’ on the iconic LEGO brick, which means we were working with a lot of curves and radiuses,” Megenedy explained in an email to ENR. “We also built four central staircases across five floors that enabled us to incorporate lots of fun and playful LEGO models throughout the space. We’re incredibly proud of how it turned out.”
In addition to its new U.S. headquarters, the LEGO Group is also opening a 2,000,000 s.f. regional distribution center (RDC) in Prince George, Virginia, which will support a future factory in Greater Richmond. Both facilities are currently under construction and expected to open in 2027.
In a press release announcing those projects, the LEGO Group said they are part of the company’s global supply strategy to locate factories and distribution centers close to major markets and ensure capacity to support future growth in the region.
The RDC will be the second in the company’s Americas network, joining an existing center in Fort Worth, Texas. It will be operated by a third-party logistics partner, creating 305 jobs. The factory will create more than 1,700 jobs with the LEGO Group once fully operational.
“The regional distribution center will bring greater flexibility to our network, ensuring we are well positioned to support long-term growth in the Americas,” said Carsten Rasmussen, Chief Operations Office of the LEGO Group. “Together with our future Virginia factory, the RDC will shorten our supply chain in the region – reducing lead times for our customers as well as our environmental impact. We are grateful for the continued support from the Commonwealth of Virginia.”
Whether you’re building a 2,000,000 s.f. distribution center, a multi-story office space, or a skyscraper, GPRS can support your construction project through our comprehensive suite of subsurface damage prevention, existing conditions documentation, and construction & facilities project management services. We offer precision concrete scanning and utility locating, pinpoint-accurate leak detection, NASSCO-certified sewer line inspections, 2-4mm accurate 3D laser scanning, and in-house mapping & modeling tailored to your project’s specific needs.
All this accurate, actionable data is at your fingertips 24/7 thanks to SiteMap® (patent pending), GPRS’ project & facility management application that provides accurate existing conditions documentation to protect your assets and people.
From skyscrapers to sewer lines, GPRS Intelligently Visualizes The Built World® to help keep you on time, on budget, and safe.
What can we help you visualize?
Frequently Asked Questions
Will I need to mark out the utilities that GPRS locates?
GPRS will locate and mark all utilities for you. We have a variety of tools and markers we can use to highlight the locations of utilities, underground storage tanks and whatever else may be hiding.
What is the difference between a design intent and as-built model?
DESIGN INTENT – deliverables will be shown as a "best fit" to the point cloud working within customary standards, such as walls being modeled 90 degrees perpendicular to the floor, pipes and conduit modeled straight, floors and ceilings modeled horizontal, and steel members modeled straight. This will produce cleaner 2D drawings and will allow for easier dimensioning of the scan area. The deliverables will not exactly follow the scan data to maintain design intent standards. Most clients will want this option for their deliverables.
AS-BUILTS – deliverables will be shown as close as possible to actual field capture. If walls are out of plumb, pipes and conduit show sag, floors and ceilings are unlevel, steel members show camber, etc., this will be reflected in the model. This will produce reality-capture deliverables, but 2D drawings may show “crooked” or out of plumb lines, floors will be sloped or contoured, steel members may show camber, twisting or impact damage. Dimensioning will not be as easy due being out of plumbness/levelness, etc. This option should be used when the exact conditions of the scan area is imperative. Clients using the data for fabrication, forensic analysis, bolt hole patterns, camber/sag/deformation analysis, and similar needs would require this option.
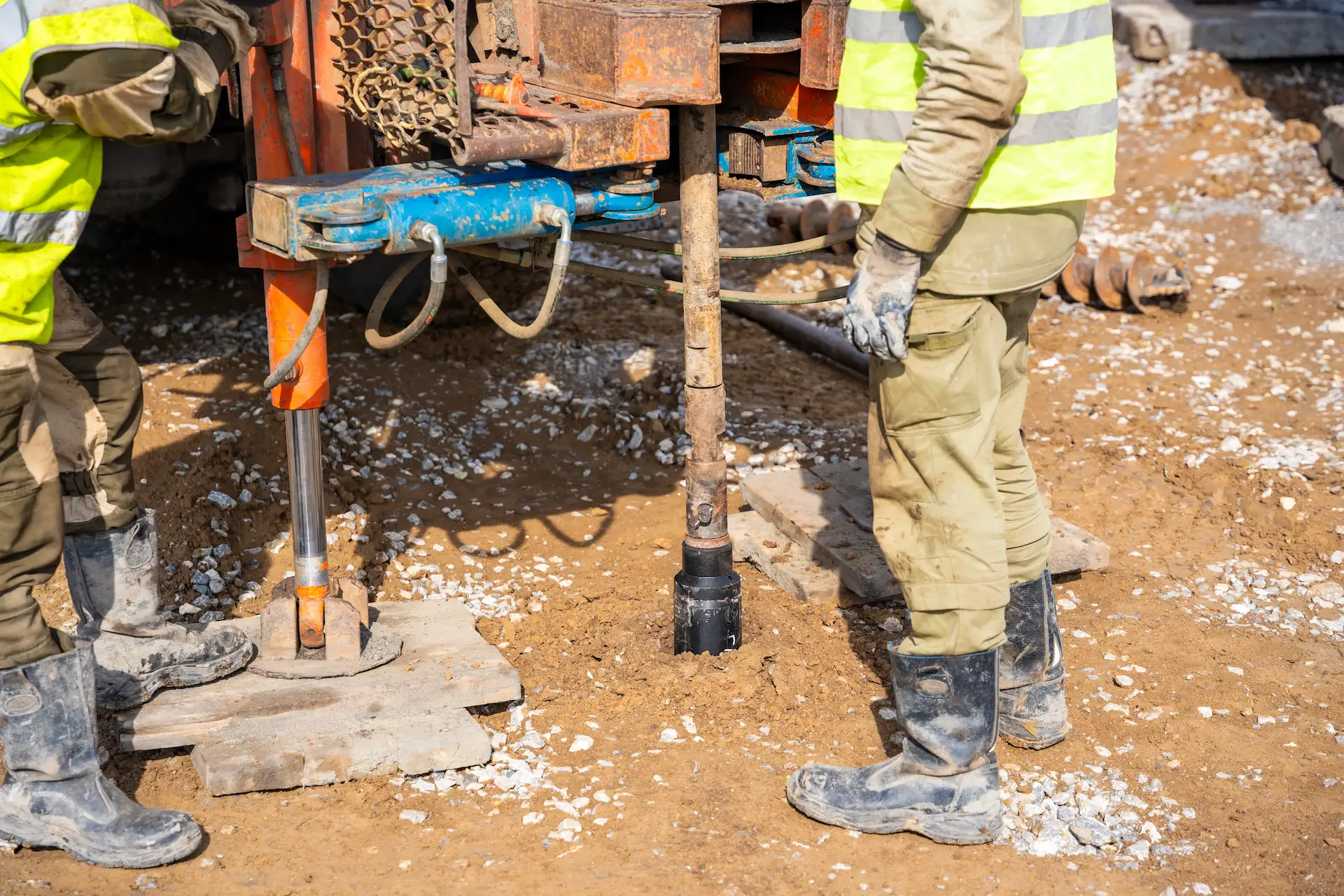
What Are Soil Borings & How Are They Conducted?
Understanding what lies beneath the surface of the earth is a critical piece of planning in the fields of construction, environmental due diligence, and geotechnical engineering.
Conducting soil borings is one of the most reliable methods for gaining this insight. Soil borings provide essential data about subsurface conditions, helping engineers, architects, and developers make informed decisions about site suitability, foundation design, and environmental impact.
What Are Soil Borings?
Soil borings are a geotechnical investigation technique used to collect soil samples from below the ground surface. These samples are analyzed to determine the physical and mechanical properties of the soil, such as composition, density, moisture content, strength, and bearing capacity. The information gathered is crucial for designing safe and effective foundations for buildings, roads, bridges, and other infrastructure.
Soil borings are also used in environmental assessments to detect contamination, monitor groundwater, and evaluate the suitability of land for agricultural or industrial use.
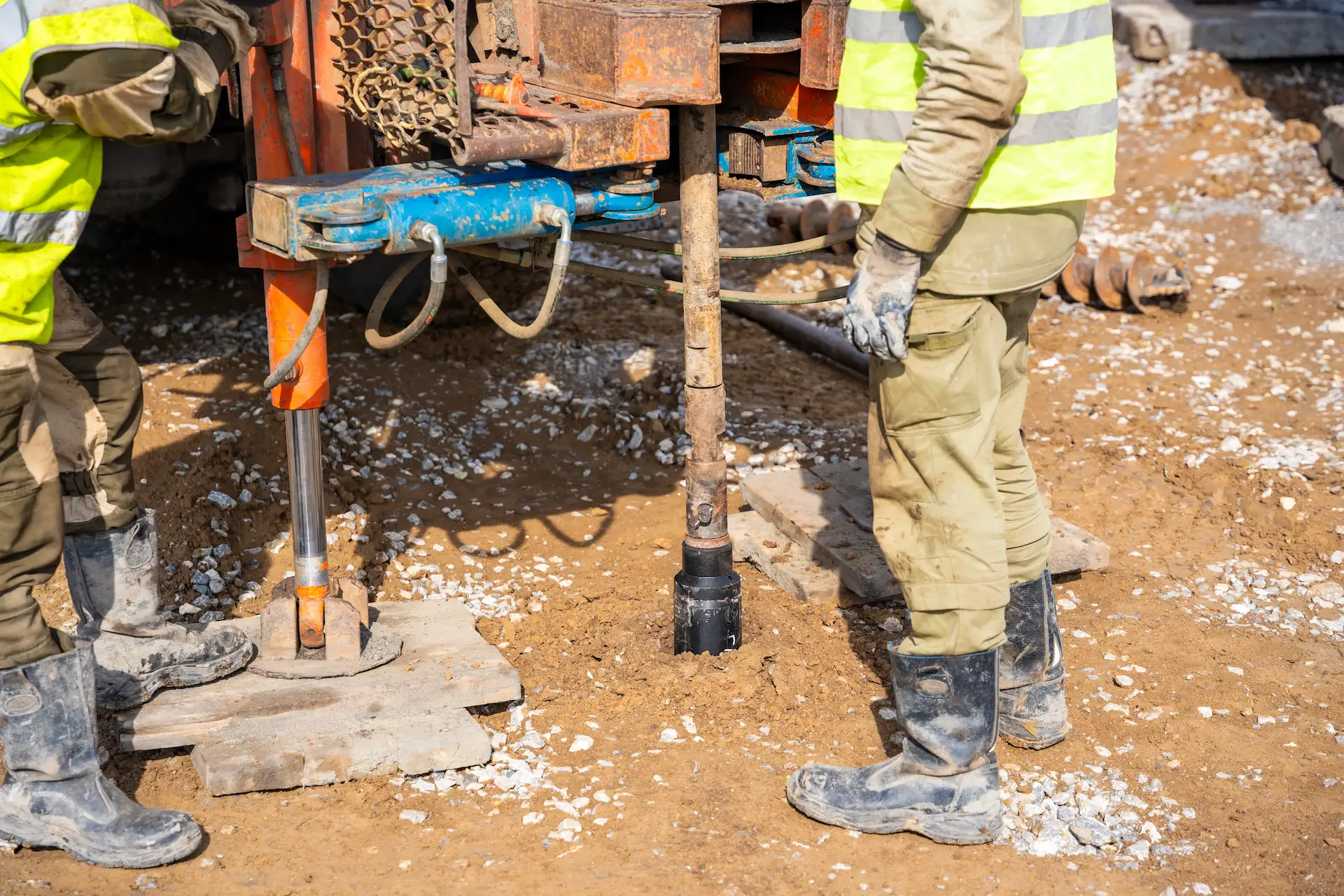
Why Are Soil Borings Important?
The subsurface conditions of a site can vary significantly, even within a small area. Without proper investigation, construction projects risk encountering unexpected soil behaviors such as settlement, liquefaction, or slope instability. These issues can lead to structural failure, costly delays, or environmental hazards.
Soil borings help to:
- Assess soil stability and load-bearing capacity
- Identify groundwater levels and flow
- Detect the presence of contaminants
- Inform the design of foundations and earthworks
- Ensure compliance with building codes and environmental regulations
Types of Soil Boring Methods
Several methods are used to conduct soil borings, each suited to different site conditions and project requirements. The most common include:
Auger Boring
This method uses a helical screw blade (auger) to drill into the ground. It is typically used for shallow borings in soft to medium soils. There are two main types:
- Hand augers are used for depths up to 10-15 feet
- Power augers are used for deeper or more resistant soils
Auger boring is relatively quick and cost-effective but may not be suitable for very hard or saturated soils.
Rotary Drilling
Rotary drilling uses a rotating drill bit to cut through soil and rock. It is often used for deeper borings and can penetrate a wide range of soil types. The drill bit is lubricated and cooled with drilling fluid (mud or water), which also helps to bring cuttings to the surface.
This method allows for continuous sampling and is ideal for complex geotechnical investigations.
Percussion Drilling
Also known as cable tool drilling, this method involves repeatedly dropping a heavy bit to break up soil and rock. The loosened material is then removed from the borehole. While slower than rotary drilling, percussion drilling is effective in hard or boulder-laden soils.
Wash Boring
Wash boring uses a jet of water to loosen soil, which is then removed by a suction pump. It is commonly used in soft soils and for preliminary investigations. However, it does not provide undisturbed samples, limiting its usefulness for detailed analysis.
The Soil Boring Process: Step-by-Step
Conducting a soil boring involves several key steps, typically carried out by a geotechnical engineering firm:
1. Site Preparation
Before drilling begins, the site is surveyed and cleared. The boring locations are selected based on the proposed construction layout and known geological conditions. Permits may be required, especially in urban or environmentally sensitive areas.
2. Drilling and Sampling
The drilling rig is set up at the designated location. As the borehole is advanced, soil samples are collected at regular intervals – usually every 2 to 5 feet or at changes in soil strata.
There are two main types of samples:
- Disturbed samples, which are suitable for classification and basic testing
- Undisturbed samples, which preserve the soil structure and are used for strength and compressibility tests
Sampling tools include split-spoon samplers, Shelby tubes, and piston samplers, depending on the soil type and required data.
3. Standard Penetration Test (SPT)
One of the most common in-situ tests performed during soil borings is the Standard Penetration Test (SPT). It involves driving a split-spoon sampler into the soil using a standardized hammer and recording the number of blows required to penetrate a set depth. The resulting "N-value" provides an indication of soil density and strength.
4. Groundwater Monitoring
As the borehole is drilled, groundwater levels are observed and recorded. In some cases, temporary or permanent monitoring wells are installed to track fluctuations over time.
5. Logging and Documentation
Throughout the boring process, a detailed borehole log is maintained. This log includes:
- Depth and type of each soil layer
- Sample locations and types
- SPT results
- Groundwater observations
- Any anomalies or obstructions encountered
This documentation forms the basis for the geotechnical report.
6. Laboratory Testing
Collected samples are sent to a geotechnical laboratory for further analysis. Common tests include:
- Grain size distribution
- Atterberg limits (plasticity)
- Moisture content
- Shear strength
- Consolidation and compaction characteristics
These tests provide the data needed to model soil behavior under load and design appropriate foundations.
Interpreting the Results
The final deliverable of a soil boring investigation is a geotechnical report. This report synthesizes field and lab data to provide:
- Soil profiles and stratigraphy
- Engineering properties of each soil layer
- Recommendations for foundation design
- Assessment of potential risks (e.g., settlement, liquefaction)
- Construction considerations (e.g., dewatering, excavation support)
This report is a critical tool for engineers and architects, guiding decisions that affect safety, cost, and long-term performance.
GPRS offers nationwide, precision utility locating services to help ensure the success of your soil boring projects.
Utilizing state-of-the-art subsurface investigation technology such as GPR scanning and EM locating, our SIM-certified Project Managers provide you with complete and accurate data bout the built world beneath your project site, so you can excavate without the risk of costly and potentially dangerous subsurface damage.
All this data is at your fingertips 24/7 thanks to SiteMap® (Patent Pending), GPRS’ project & facility management application that provides accurate existing conditions documentation to protect your assets and people.
From soil boring clearances to skyscrapers, GPRS Intelligently Visualizes The Built World® to keep your projects on time, on budget, and safe.
What can we help you visualize?
Frequently Asked Questions
What do I get when I hire GPRS to conduct a utility locate?
Our Project Managers flag and paint our findings directly on the surface. This method of communication is the most accurate form of marking when excavation is expected to commence within a few days of service.
GPRS also uses a global positioning system (GPS) to collect data points of findings. We use this data to generate a plan, KMZ file, satellite overlay, or CAD file to permanently preserve results for future use. GPRS does not provide land surveying services. If you need land surveying services, please contact a professional land surveyor.
Please contact us to discuss the pricing and marking options your project may require.
Can GPRS Project Managers distinguish between different underground utilities that they locate?
In most situations, we can identify the utility in question without any problems, although it is not always possible to determine what type of utility is present. When this happens, we attempt to trace the utility to a valve, meter, control box, or other signifying markers to determine the type of utility buried.