industry insights
Featured Articles
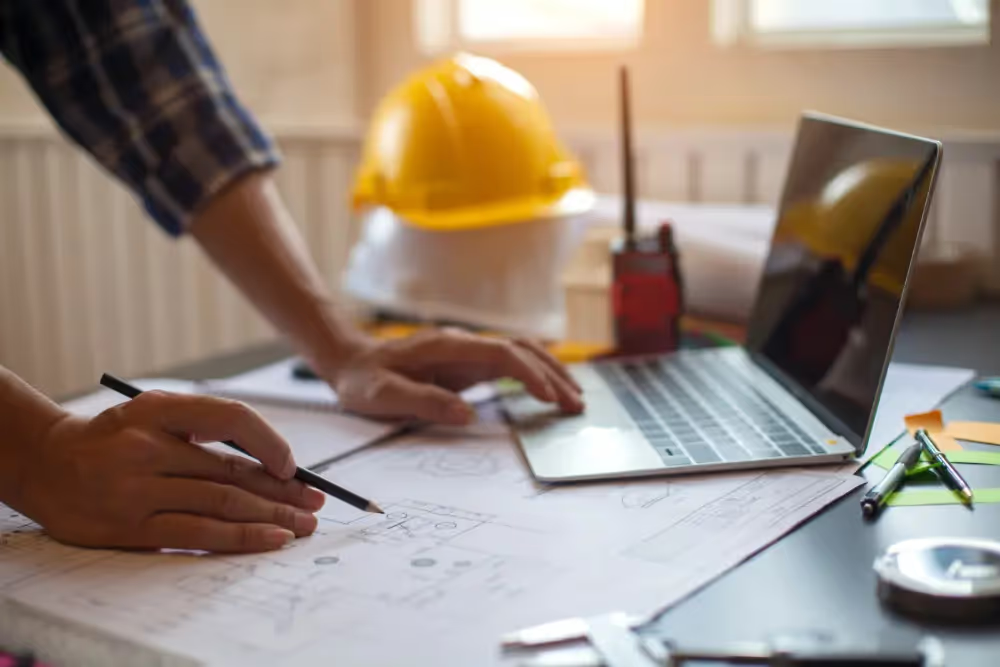
Why Do You Need Updated As-Builts on Your Next Project?
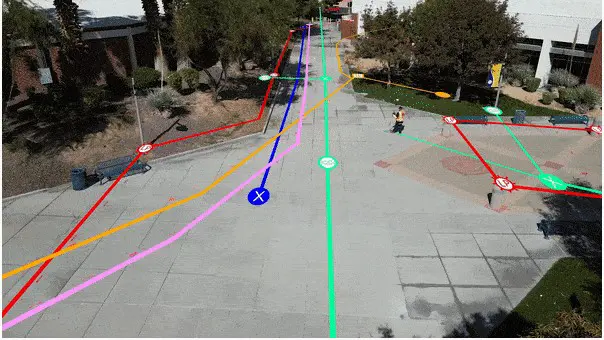
Is Utility Mapping Worth the Cost?
industry insights
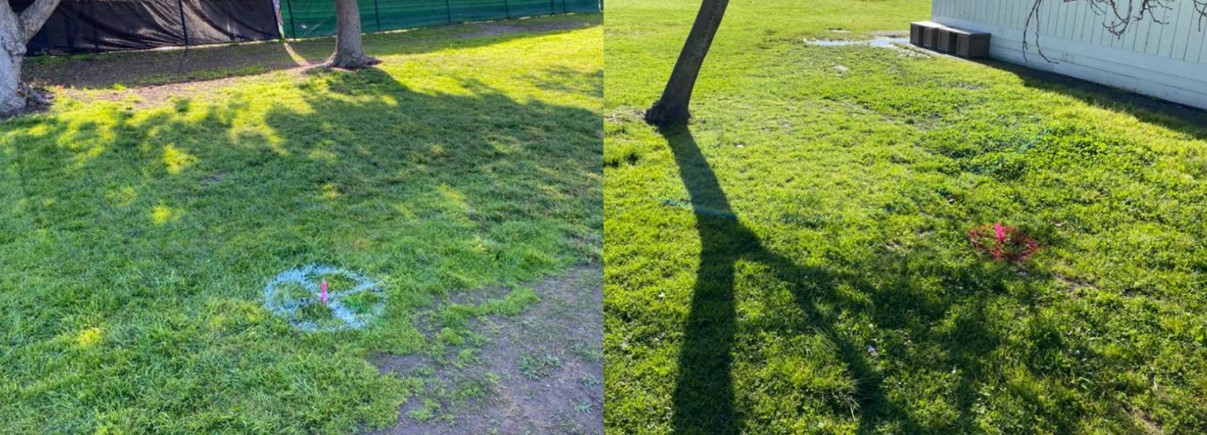
GPRS Discovers the Location of Two Time Capsules from the 1940s
GPRS utilized ground penetrating radar (GPR) to help locate buried time capsules from the early 1900s before a school’s planned demolition.
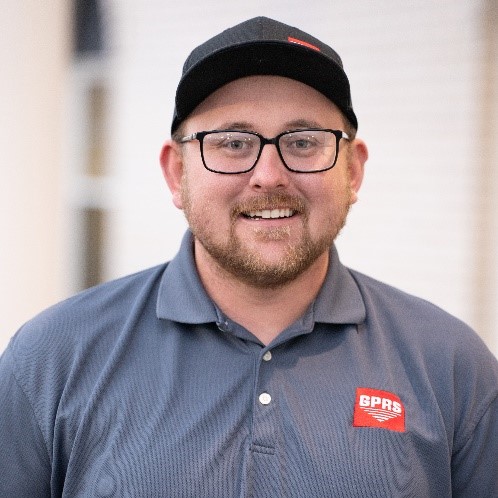
GPRS Project Manager Dillon Malang was called out to an elementary school in California to help narrow down the search for these time capsules.
“Our sole task was just to try and find these time capsules that were from, I want to say like the 1930s or 40s,” Malang explained.
The school was set for demolition, and members of the community recalled that time capsules were buried somewhere on the property. However, there was no documentation indicating where these capsules were – or if they truly existed at all.
“So, they pretty much narrowed it down to us for like 250-300 square feet areas just to scan with [ground penetrating] radar,” Malang explained.
When GPRS SIM-certified Project Managers utilize GPR for utility locating or concrete scanning, they rely on the imaging that displays when emitting radio signals into the structure. The radio waves “bounce” off any material it encounters and those bounces are displayed as hyperbolas.

To the untrained eye, it may be unclear what these hyperbolas represent. Our experienced GPRS Project Managers can use this reading to determine the type of material located.
When conducting his investigation, Malang encountered two areas with distinct responses.
“We're able to find two reactions, one in each area, for them to possibly dig up to try and investigate,” Malang explained.
Malang marked the area with spray paint and flags, so the client will be able to investigate whether any of the responses are the missing time capsules without unnecessary, large-scale potholing.
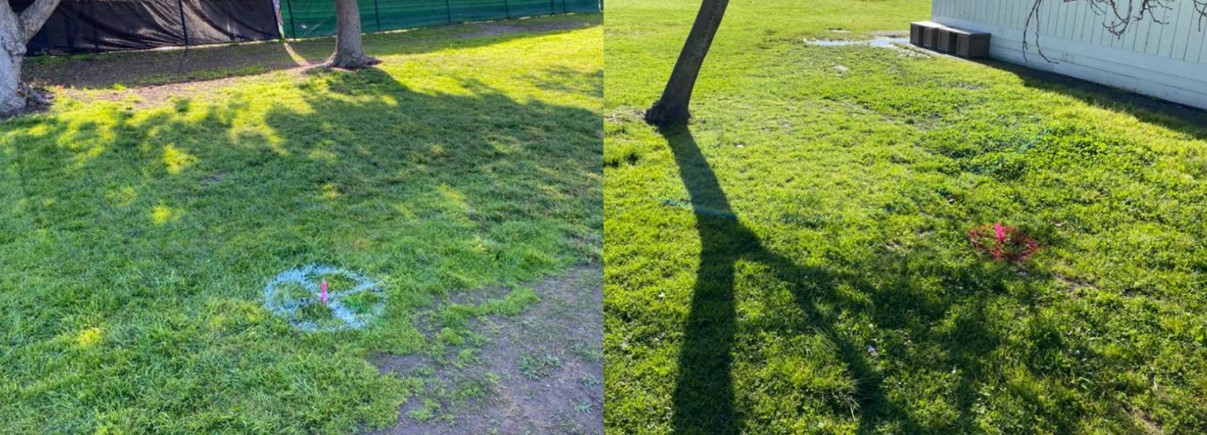
Locating time capsules isn’t an everyday type of job for GPRS’ nationwide team of Project Managers. Whether we’re helping you preserve a community’s history, or assisting with your commercial construction project, our aim is to give you the accurate, actionable data you need to stay on time, on budget, and safe.
Does GPR Have Any Limitations?
Ground and soil conditions, weather, and type of material located are a few of the potential limiting factors.
An experienced GPR technician, like GPRS Project Managers, will be able to assess a site’s condition to determine if GPR is the proper tool for the job. If GPR is limited by the site conditions or other factors, GPRS Project Managers are equipped with complementary utility locating tools to ensure we can still intelligently visualize your built world.
How Can I Determine if GPR is Needed for My Project?
GPR is commonly used to scan and identify subsurface elements. It’s always wise to conduct a GPR scan before beginning any renovation or demolition activities. This typically includes any excavation work deeper than 18”, or any coring, cutting, or drilling of concrete.
The best way to know whether you need GPR is to contact an experienced GPR technician to evaluate your project and its needs. GPRS’ Project Managers not only know how to use GPR properly and efficiently, they also know when it isn’t the best tool for the job and can recommend what works best for the needs of the clients.
With hundreds of GPRS Project Managers stationed all across the United States, you can be sure that there are quality GPR scanning services near you.
What can we help you visualize?
FREQUENTLY ASKED QUESTIONS
What is Subsurface Investigation Methodology?
Subsurface Investigation Methodology (SIM) is a standard operating procedure and set of professional specifications that work as a guide for utility locating experts when scanning for buried utility lines. All GPRS Project Managers are required to achieve SIM 101 certification, which requires 80 hours of hands-on training in a classroom setting and 320 hours of mentorship in the field. For reference, the American Society for Nondestructive Testing’s (ASNT) minimum training recommendation includes eight hours for training and 60 hours practicing GPR to achieve NDT Level 1 certification in ground penetrating radar (GPR) scanning.
SIM requires the use of multiple, complementary technologies, like GPR scanning and electromagnetic (EM) locating, when locating buried utilities or scanning a concrete slab.
What are the Benefits of Underground Utility Mapping?
Having an updated and accurate map of your subsurface infrastructure reduces accidents, budget overruns, change orders, and project downtime caused by dangerous and costly subsurface damage.
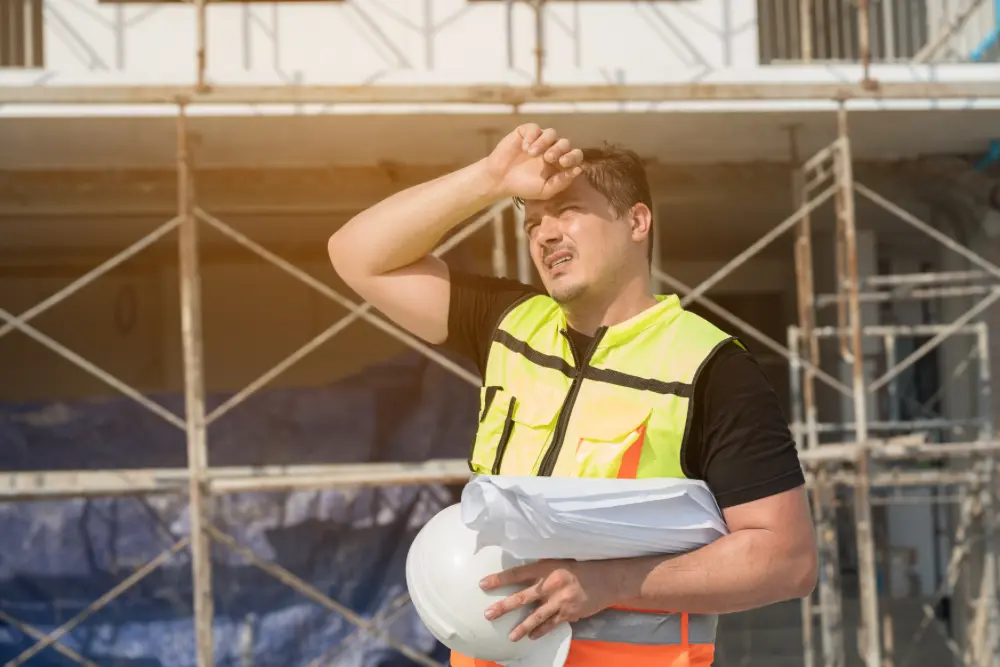
Contractors, Unions Provide Feedback on OSHA’s Proposed Heat Rule
Contractors and unions alike have said their piece about a proposed rule aiming to protect workers in the United States from the health risks of extreme heat.
The U.S. Dept. of Labor Occupational Safety and Health Administration (OSHA) held a multiday virtual public hearing earlier this summer as part of the rulemaking process for possible workplace heat injury and illness prevention standards.
Published last summer, the proposed rule would require employers to identify heat-related hazards and implement both engineering controls and safe work practices, using two distinct trigger thresholds. It would also outline procedures for establishing a heat emergency response plan, conducting training for employees and supervisors, and maintaining proper documentation.
The proposed rule applies to a variety of industries, but construction is perhaps the most important due to it being among the leading industries for workplace heat-related illnesses and injuries. According to Bureau of Labor Statistics data, between 2021 and 2022 there were 620 construction workplace injuries that resulted from exposure to environmental heat and required at least one day away from work, and 29 deaths.
OSHA says those numbers are likely lower than the true statistics due to underreporting.
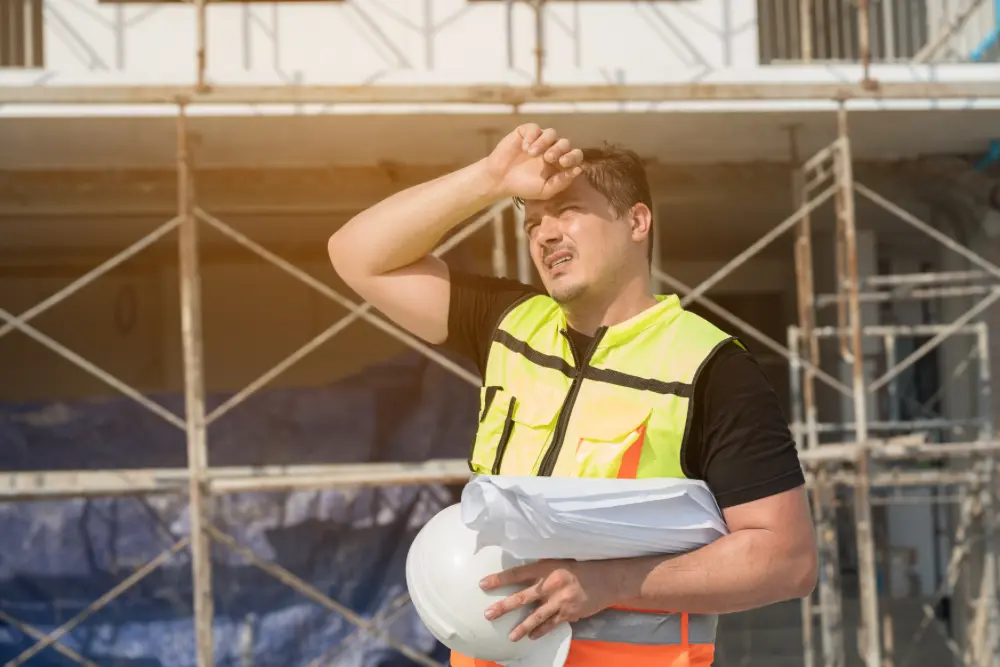
“Heat-related illnesses are significantly underreported for multiple reasons, including a lack of information, communication and fear of retaliation,” Ryan Papariello, safety and health specialist at the Laborers' Health & Safety Fund of North America, told Engineering News-Record. “…We must shift from a reactive to proactive strategy that centers on worker health and safety.”
According to ENR’s reporting, contractor groups have criticized the proposed rule for using what they call “a one-size-fits-all approach” to heat safety. The Associated General Contractors of America and the Associated Builders and Contractors are among the groups calling on OSHA to implement performance-based requirements in the standard, rather than prescriptive measures.
“OSHA should recognize, and I believe has recognized in the past, that the construction industry faces unique challenges compared to those in other industries,” said Kevin Cannon, director of safety and health services at AGC.
Cannon added that construction should be exempt from the temperature record keeping requirements included in the proposed rule.
“Our belief is that this data has limited utility in predicting environmental conditions on future projects and would not necessarily be considered representative sampling or objective data,” he told ENR.
The proposed rule states that employers would need to provide water, a break area and acclimatization for new or returning workers at 80°F. At 90°F, they would also need to provide 15-minute rest breaks every two hours and implement a supervisor or buddy system to observe for heat-related health symptoms.
Joe Xavier, senior director of health and safety at ABC, told ENR that provisions like requiring rest breaks “are impractical and would be exceedingly difficult to manage on construction sites due to time and schedule-based activity interdependencies.” He cited how mandatory breaks for crews placing concrete could cause a strain for contractors managing the timing of trucks, the concrete pour rate and other factors, among other examples of the challenges these types of rules would create.
“ABC recommends that OSHA allows supervisors and employees to work together and coordinate safe approaches for rest breaks focusing on individual employees’ needs, the nature of the work and the specific workplace conditions,” he said.
But Papariello pointed to the seven states that already have some workplace heat standards in place, and the additional ones currently considering them. Like the proposed federal rule, most of the state standards utilize prescriptive approaches to protect workers from extreme heat.
“[They] have shown that feasibility and flexibility are not a barrier,” he said. “In fact, as the more recently developed heat standards illustrate, these can go hand in hand.”
Other states, however, have made moves to reduce the amount of protection they require employers to offer their workers.
And in 2023, Texas legislators passed a bill that, among other effects, eliminated ordinances in Austin and Dallas that established mandatory water breaks for construction workers.
While commenting on OSHA’s proposed rule during a panel in June, Tarn Goelling, international representative at the International Brotherhood of Electrical Workers, shared a story about an electrical worker in Austin, Texas, who returned to his hot jobsite after taking some time off. The worker became pale, confused and dizzy over the course of his workday. He rested in the shade but still felt unwell and left early.
While driving home, the worker passed out and flipped his truck after suffering from heat stroke.
“[The worker was] not properly acclimated to working in extreme heat,” Goelling said at the panel, per ENR’s reporting. “…Many of the injuries and illnesses resulting from exposures to these heat hazards on the job are easily preventable with an appropriate heat illness prevention plan.”
GPRS Is Committed to You & Your Team's Safety
At GPRS, safety is always on our radar.
That’s more than just a catchy tagline; through our sponsorship of safety initiatives such as Concrete Sawing & Drilling Safety Week, Construction Safety Week, and Water & Sewer Damage Awareness Week, we aim to ensure that every employer and employee in the construction industry is equipped with the knowledge and resources they need to stay safe while building for our nation’s future.
Click here to learn more about GPRS’ safety initiatives and partnerships.
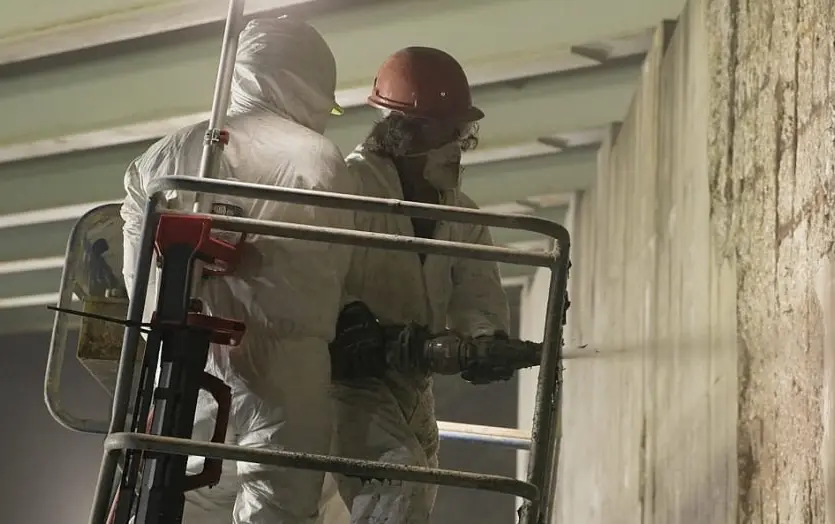
FIU Develops Spray-On Concrete System to Revolutionize Bridge Repair
Researchers at Florida International University have developed a spray-on concrete system that they believe could revolutionize how U.S. bridges are repaired.
According to an article in FIU News, engineers at the school have created a system that sprays Ultra-High Performance Concrete (UHPC) onto structures. This type of concrete has the potential to patch walls, fix pipes and restore drainage culverts – and it can make these structures stronger than they were originally.
According to information on the U.S. Department of Transportation website, UHPC is increasingly being used to build and repair America’s transportation infrastructure. Most of the time, these applications of UHPC involve pouring it into place. This UHPC would either be self-consolidating – filling its forms completely under its own weight – or thixotropic – a UHPC that is vibrated and struck off with a vibrating screed under initial placement.
Existing UHPC applications – such as girder end repairs and the restoration or protection of walls and columns – could be enhanced by the ability to spray UHPC directly into place. Emerging or future uses, including bridge deck soffit repairs and culvert rehabilitation or retrofitting, may also benefit from sprayable UHPC.
In these cases, spraying UHPC is often more economical than traditional pouring methods, primarily because it eliminates the need for formwork. Spray application also offers greater flexibility, allowing UHPC to be applied from any angle. This overcomes the limitations of gravity-based pouring, which can be hindered by structural obstructions like bridge decks.
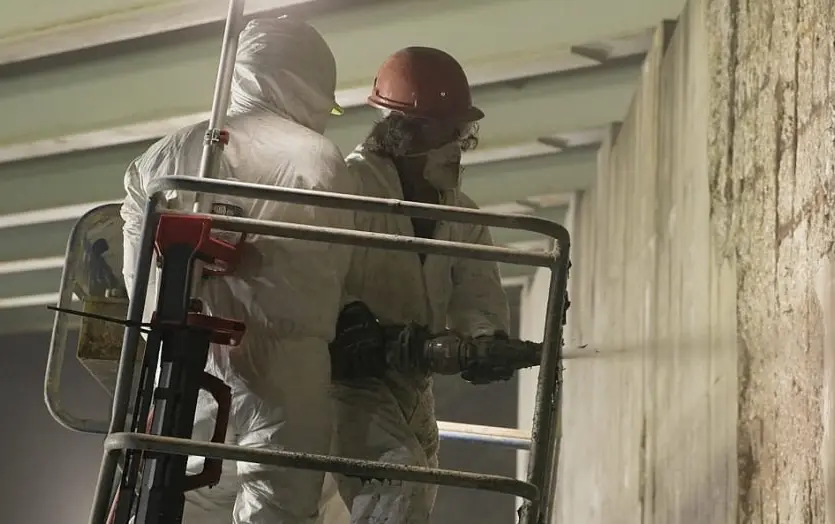
“UHPC has historically been very expensive to use, mainly because most of those available [mixes] on the market have been commercial versions,” said Atorod Azizinamini, a professor of civil engineering and director of a U.S. Department of Transportation-funded research center at FIU. “Even a very thin layer of UHPC can drastically improve the strength of a structure and protect it from water.”
“We have developed an affordable type of UHPC, and a system that can spray it,” Azizinamini continued. “This could become a major tool in repairing or upgrading structurally deficient bridges quickly and efficiently.”
FIU’s UHPC mix comes in at around $500 per cubic yard, which is considerably cheaper than many comparable commercial versions of the product. The school’s application system deposits thin layers of concrete onto surfaces through a nozzle, like how spray paint is applied. These layers can be added, one upon another, in coats. Their light weight doesn’t significantly alter the mass of a structure.
The FIU team used their system and UHPC mix on a bridge in Virginia last year.
“The reason that we invited the FIU team here to Virginia is that we had a bridge abutment wall that had corrosion issues due to the deicing salt that is used here,” said Sam Fallaha, an engineer with the Virginia Department of Transportation. “We liked it because it is easy to apply a thin layer to vertical surface creating a durable solution for problems like these that occur in cold climates.”
The Virginia job was the first-ever application of its kind in the U.S. The Risk and Resilience Tech Hub is investing roughly $1 million into the FIU researchers’ system to commercialize the technology and help the university train more engineers and builders to use it.
"Anyone who has used a glue gun for an arts and crafts project knows how difficult it can be to keep the nozzle from getting clogged,” said Morgan Dickinson, a Ph.D. student in Azizinamini’s lab. “The same goes with our UHPC system. If you don’t know how to clean it, the concrete hardens, and you might have to throw parts away. Fortunately, we are seeing widespread interest in people who want to learn about our system and use it properly.”
Kia Hajifathalian, Vice President and Market General Manager at Baker Construction, told FIU News that he sees the FIU system as a practical way of bringing the benefits of UHPC to more buildings and bridges around the nation.
“This is not just research in a lab that will only have a couple of specific uses,” Hajifathalian said. “I think that FIU has figured out how to utilize UHPC in a way that can be used to repair buildings and bridges at scale.”
"The biggest nightmare of a concrete contractor is pouring concrete, testing it later and finding out that it is not as strong as you thought it would be because something unexpected happened,” he added. “Having that concrete in a pre-bagged system like FIU is doing, where you have quality control, is so important.”
The State of America’s Bridges
There are more than 623,000 bridges across the United States, according to the American Society of Civil Engineers (ASCE) 2025 Report Card for America’s Infrastructure.
The ASCE gave America’s bridges a C in that report card, citing the fact that 49.1% of the country’s bridges are in “fair” condition, 44.1% are in “good” condition, and 6.8% are in “poor” condition.
“Unfortunately, the nation continues to see the number of fair bridges surpassing those in good condition,” the ASCE wrote. “As bridges in fair condition continue to age – presenting the possibility of being further downgraded – they also exemplify an opportunity because they can be preserved at a lower cost than bridges in poor condition.”
Bridges received a significant amount of funding through the Infrastructure Investment and Jobs Act (IIJA), which included $27.5 billion for the Bridge Formula Program and $12.5 billion for the Bridge Investment Program.
“Despite this infusion of federal funding, bridge-related system rehabilitation needs are estimated at $191 billion,” the ASCE wrote. “Therefore, strategic asset management planning and routine maintenance are essential to keeping bridge conditions from further declining and avoiding costly repair or rehabilitation work. While the effects of extreme weather events pose threats to bridges, innovative techniques are improving their security and resilience.”
As we wait to see if innovations like FIU’s spray-on concrete system, or Allium’s stainless-steel-clad rebar truly revolutionize bridge construction and maintenance, it’s important that you know exactly where all reinforcements are within bridge decks and other concrete slabs before you attempt to cut or core that concrete.
Striking rebar, post tension cables or other support systems within concrete can lead to catastrophic structural failure that endangers you and your workers, and anyone else in the vicinity of your job site.
GPRS provides precision concrete scanning and imaging services designed to keep your concrete cutting and coring projects on time, on budget, and safe. Utilizing state-of-the-art ground penetrating radar (GPR) scanners and other, complementary technologies, we visualize where you can and can’t safely penetrate the slab, providing you with accurate, actionable information that helps you plan, build, and manage better.
Our SIM-certified Project Managers have achieved and maintain a 99.8%+ rate of accuracy when scanning concrete slabs for buried rebar, post tension cable, electrical conduit, and any other types of embedded obstructions that could compromise the safety and success of your project. We’re so confident in their abilities that we introduced the Green Box Guarantee, which states that when we place a Green Box within a concrete layout prior to you cutting or coring that slab, we guarantee that the area within will be free of any obstructions.
If we’re wrong, we agree to pay the cost of the damage.
From bridges to skyscrapers, GPRS Intelligently Visualizes The Built World® to keep your projects on time, on budget, and safe.
What can we help you visualize?
Frequently Asked Questions
How is GPR used to identify tendons vs. rebar in a post-tensioned slab?
In post-tensioned structures, we typically find one mat of support rebar near the base of the slab. This mat is generally consistently spaced and remains at a constant elevation.
Post-tension cables are generally found above this support mat and “draped” throughout the rest of the structure. The elevation of the cable is usually high near the beams and column lines and drapes lower through the span between beams and column lines. Knowledge of these structural differences allows us to accurately differentiate between components. Our Project Managers will leave you feeling confident in our findings and in your ability to drill or cut without issue.
What types of concrete scanning does GPRS provide?
GPRS provides two specific but different scanning services: elevated concrete slab scanning and concrete slab-on-grade locating. Elevated concrete slab scanning involves detecting embedded electrical conduits, rebar, post-tension cables, and more before core drilling a hole through the slab. Performing a concrete slab-on-grade locating service typically involves scanning a trench line for conduits before conducting saw cutting and trenching to install a sanitary pipe, water line, or something similar.
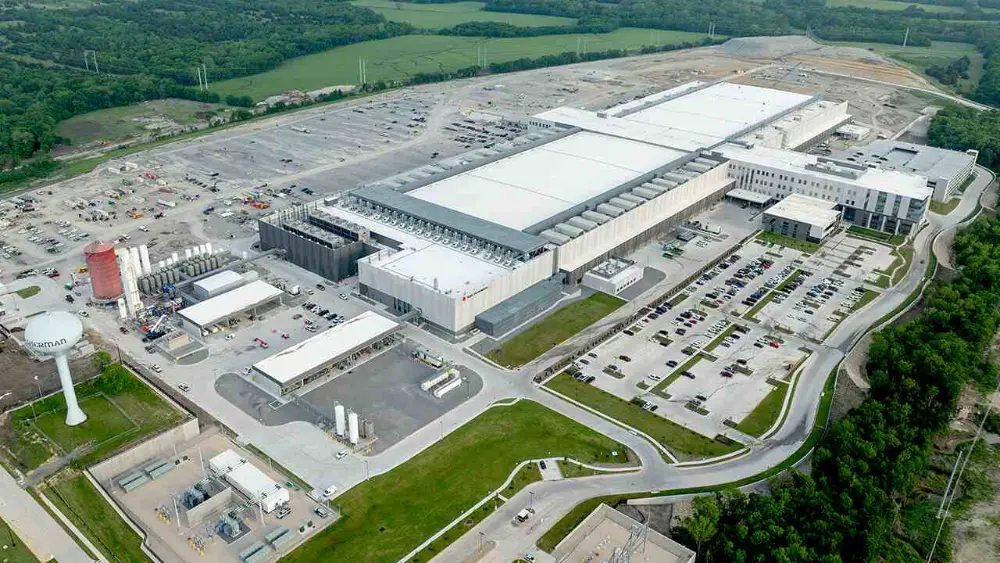
TI to Invest Over $60B in U.S. Semiconductor Fabs
Texas Instruments (TI) is investing more than $60 billion across seven U.S. semiconductor fabs, marking the largest investment in foundational semiconductor manufacturing in U.S. history.
In a press release on the company’s website, TI said it is expanding its U.S. manufacturing capacity to supply the growing need for semiconductors that will advance critical innovations from vehicles to smartphones to data centers.
As part of this investment, TI is building and ramping seven, large-scale, connected fabs – specialized factories for producing semiconductors – across three manufacturing mega-sites in Texas and Utah. The sites are expected to support more than 60,000 jobs and produce hundreds of millions of chips daily.
“TI is building dependable, low-cost 300mm capacity at scale to deliver the analog and embedded processing chips that are vital for nearly every type of electronic system,” said Haviv Ilan, president and CEO of Texas Instruments. “Leading U.S. companies such as Apple, Ford, Medtronic, NVIDIA and SpaceX rely on TI’s world-class technology and manufacturing expertise, and we are honored to work alongside them and the U.S. government to unleash what’s next in American innovation.”
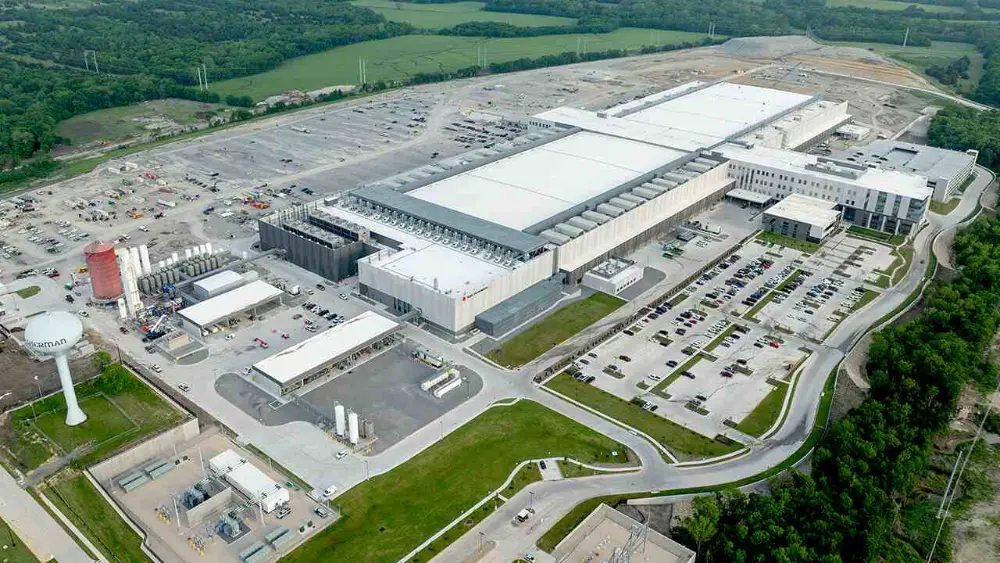
TI’s first new fab in Sherman, Texas will begin initial production this year, just three years after breaking ground. Construction on the exterior shell of a second new fab in Sherman is also complete, with two more fabs currently in the planning phase.
TI’s second fab in Richardson, Texas continues to ramp up to full production alongside the world’s first 300mm analog fab, which opened in 2011.
In Lehi, Utah, TI is currently ramping its first 300mm wafer fab with construction on a connecting fab well underway.
“For nearly a century, Texas Instruments has been a bedrock American company driving innovation in technology and manufacturing,” said U.S. Secretary of Commerce, Howard Lutnick. “…Our partnership with TI will support U.S. chip manufacturing for decades to come.”
TI is the largest foundational semiconductor manufacturer in the U.S., producing analog and embedded processing chips for everything for nearly every electronic device in use today. The company said that it is expanding its U.S. manufacturing presence to meet the steadily growing demand for these chips and help its customers pioneer the next wave of technological breakthroughs.
“Texas Instruments' American-made chips help bring Apple products to life, and together, we’ll continue to create opportunity, drive innovation, and invest in the future of advanced manufacturing across the U.S.,” said Apple’s CEO Tim Cook.
Besides Apple, TI provides semiconductors to major companies such as Ford Motor Company, Medtronic, and NVIDIA.
“At Medtronic, our life-saving medical technologies rely on semiconductors to deliver precision, performance, and innovation at scale,” said Geoff Martha, Medtronic chairman and CEO. “Texas Instruments has been a vital partner – especially during the global chip shortages – helping us maintain supply continuity and accelerate the development of breakthrough therapies. We’re proud to leverage TI’s U.S.-manufactured semiconductors as we work to transform healthcare and improve outcomes for patients around the world.”
“NVIDIA and TI share the goal to revitalize U.S. manufacturing by building more of the infrastructure for AI factories here in the U.S.,” added Jensen Huang, founder and CEO of NVIDIA. “We look forward to continuing our collaboration with TI by developing products for advanced AI infrastructure.”
Whether you’re building a semiconductor fab or a skyscraper, ensuring the success of a construction project always starts with ensuring you have accurate data of what’s already on your site.
GPRS provides a comprehensive suite of subsurface damage prevention, existing conditions documentation, and construction and facilities project management solutions to keep your projects on time, on budget, and safe. We’re with you every step of the way, from initial design to O&M, Intelligently Visualizing The Built World® to ensure you can plan, build, and manage better.
What can we help you visualize?
Frequently Asked Questions
What do I get when I hire GPRS to conduct a utility locate?
Our Project Managers flag and paint our findings directly on the surface. This method of communication is the most accurate form of marking when excavation is expected to commence within a few days of service.
GPRS also uses a global positioning system (GPS) to collect data points of findings. We use this data to generate a plan, KMZ file, satellite overlay, or CAD file to permanently preserve results for future use.
GPRS does not provide land surveying services. If you need land surveying services, please contact a professional land surveyor.
Please contact us to discuss the pricing and marking options your project may require.
Can GPRS locate PVC piping and other non-conductive utilities?
GPR scanning is exceptionally effective at locating all types of subsurface materials. There are times when PVC pipes do not provide an adequate signal to ground penetrating radar equipment and can’t be properly located by traditional methods. However, GPRS Project Managers are expertly trained at multiple methods of utility locating.
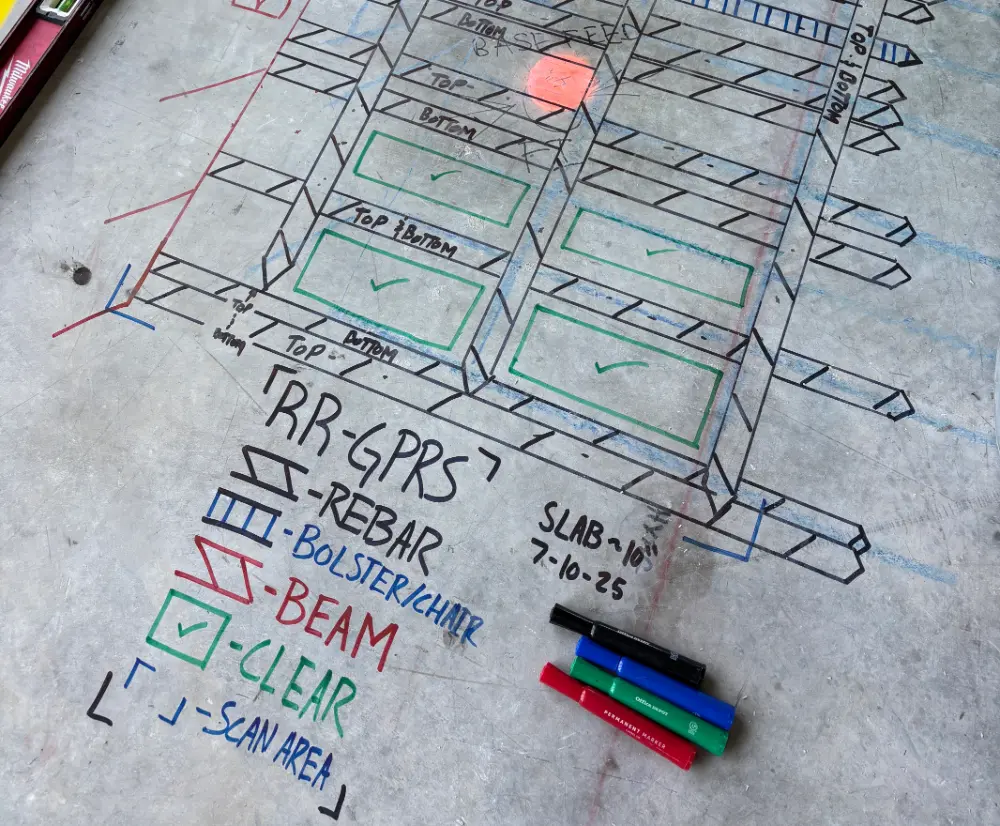
GPRS Clears Up Confusion With Accurate Concrete Scans at DFW High-Rise
A general contractor in the Dallas-Fort Worth area wasted $30,000 on two sub-par concrete scanning and imaging investigations of what they were told were post-tensioned concrete slabs inside a high-rise office building.
The building engineer on the renovation project initially required the slabs be inspected with concrete X-ray to clear safe coring locations. The X-ray company told the GC and their concrete corer that the slabs were post-tensioned – but they did not trust that information, or the data they received indicating where they could and could not safely drill into the slabs.
While concrete X-ray can be a reliable way to obtain information about infrastructure embedded within concrete slabs, GPR has proven to be the superior technology for these types of investigations.
GPR scanning is safer, faster, and cheaper than X-ray. Unlike X-ray, GPR scanners emit no harmful radiation and can visualize the infrastructure inside a slab without needing access to both sides. And GPR scanners are less bulky than X-ray and require little set-up time, meaning an investigation into your project’s slabs will not cause delays to your schedule.
But even the right technology for the job isn’t going to give you accurate results if the operator isn’t properly trained.
After the X-ray scan failed to provide accurate results, a GPR investigation of the high-rise’s slabs by a local company yielded a similar result: neither the contractor, nor the subcontractor, felt confident in coring based on the data they received.
“Between the other GPR and the X-ray company, the coring company and GC were still not confident in their markings and information provided,” said GPRS Area Manager Zack Walter.
GPRS stepped in to solve the problem, providing precision concrete scanning services that put the project back on track.
Project Manager Reynaldo Rodriguez demonstrated the accuracy of GPRS’ concrete scanning – utilizing GPR in conjunction with electromagnetic (EM) locating – to the building engineer, general contractor and subcontractor, and eventually re-scanned all the areas that the other two companies had previously investigated.
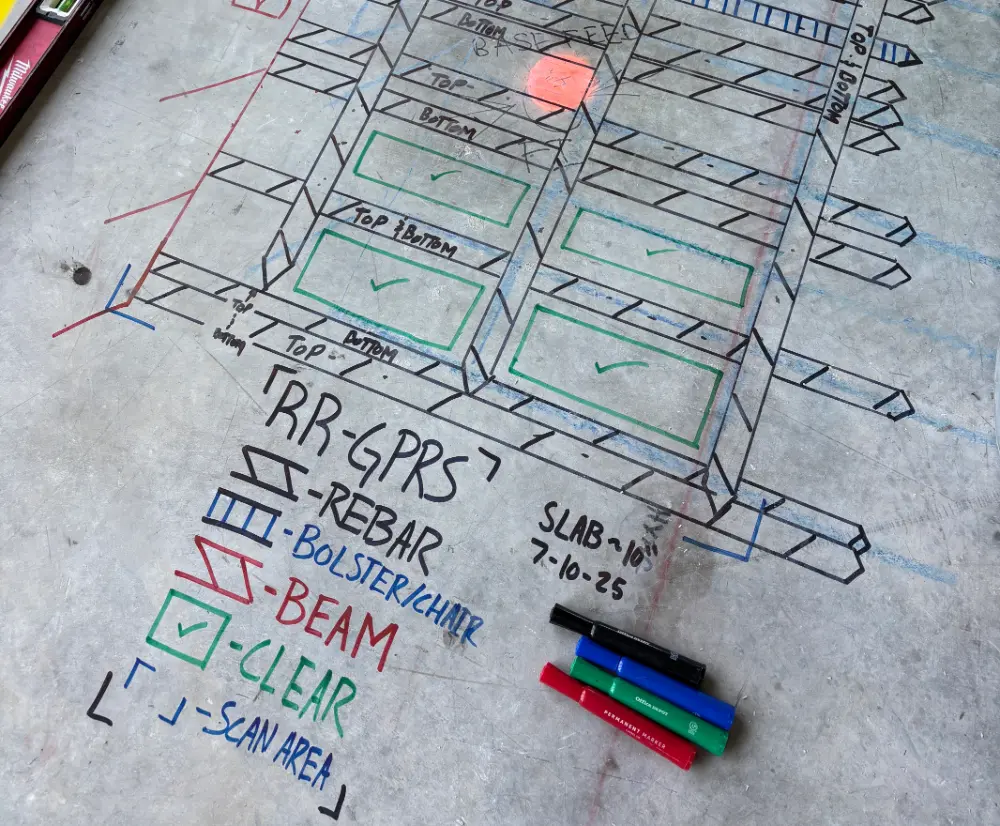
How GPRS Provides Industry-Leading Concrete Scanning
Using complementary technologies during our subsurface investigations is just one of the ways GPRS’ SIM-certified Project Managers have achieved and maintain a 99.8%+ rate of accuracy when scanning concrete slabs and locating underground utilities.
GPR scanners emit radio waves into a surface such as concrete or into the ground, then detect the interactions between those waves and anything below the surface. These interactions are displayed on a readout as a series of hyperbolas that vary in size and color depending on what type of material was detected. GPRS Project Managers are specially trained to interpret this data to indicate the location and approximate depth of these buried items and help you avoid the costly – and potentially dangerous – consequences of damaging them while breaking ground.
EM locators are a perfect complementary technology to GPR scanners because they detect the electromagnetic signals radiating from metallic pipes and cables, rather than the utilities themselves.
These signals can be created by the locator’s transmitter applying current to the pipe, or from current flow in a live electrical cable. They can also result from a conductive pipe acting as an antenna and re-radiating signals from stray electrical fields (detected by the EM locator functioning in Power Mode) and communications transmissions (Radio Mode).
Signals are created by the current flowing from the transmitter which travels along the conductor (line/cable/pipe) and back to the transmitter. The current typically uses a ground to complete the current. A ground stake is used to complete the circuit through the ground.
Using complementary technologies such as GPR and EM locating allows GPRS to create a redundant confirmation, ensuring the repeatability of our process and the accuracy of our findings.
When scanning concrete, our Project Managers will mark safe places to cut or core with green boxes. The GPRS Green Box Guarantee is a proprietary program stating that, if you cut or core within one of these green boxes and damage an embedded item, GPRS will pay the cost of any damage that occurs.
What We Found
Not only did Rodriguez discover major discrepancies between what he found embedded in the slabs and what the previous companies said was there – he also confirmed that the slabs were not post-tensioned after all.
Rodriguez walked the general contractor and concrete coring company through his findings, ensuring they understood the data and knew how to proceed safely with their work.
From skyscrapers to sewer lines, GPRS Intelligently Visualizes The Built World® to keep your projects on time, on budget, and safe.
What can we help you visualize?
Frequently Asked Questions
What types of concrete scanning are there?
GPRS provides two specific but different scanning services: elevated concrete slab scanning and concrete slab-on-grade locating. Elevated concrete slab scanning involves detecting embedded electrical conduits, rebar, post-tension cables, and more before core drilling a hole through the slab. Performing a concrete slab-on-grade locating service typically involves scanning a trench line for conduits before conducting saw cutting and trenching to install a sanitary pipe, water line, or something similar.
How is GPR used to identify tendons vs. rebar in a post-tensioned slab?
In post-tensioned structures, we typically find one mat of support rebar near the base of the slab. This mat is generally consistently spaced and remains at a constant elevation. Post-tension cables are generally found above this support mat and “draped” throughout the rest of the structure. The elevation of the cable is usually high near the beams and column lines and drapes lower through the span between beams and column lines. Knowledge of these structural differences allows us to accurately differentiate between components. Our Project Managers will leave you feeling confident in our findings and in your ability to drill or cut without issue.
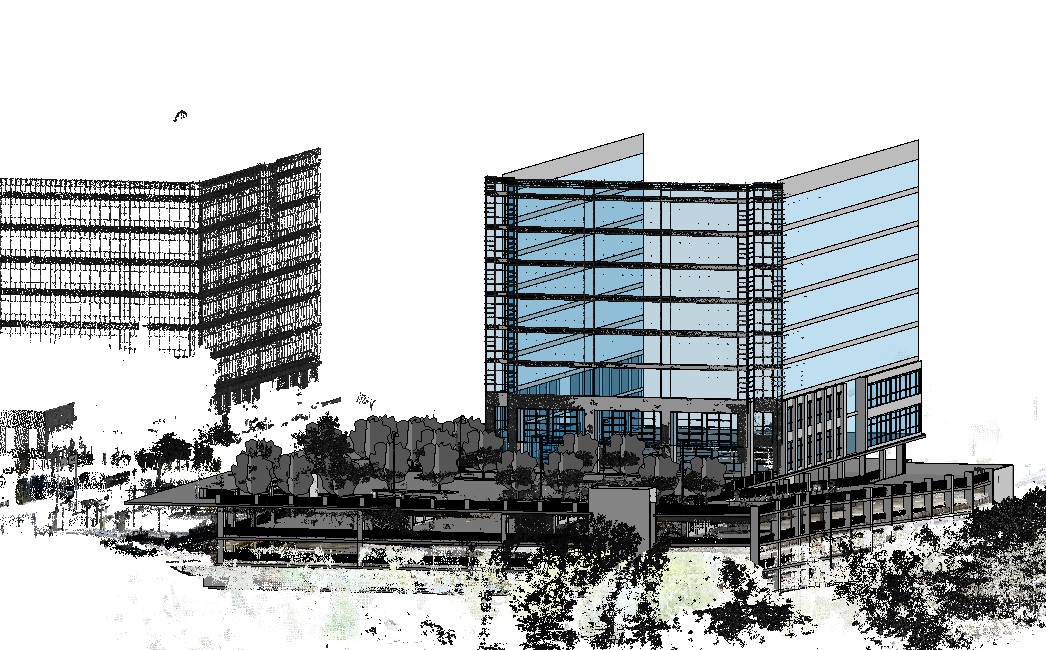
How Reality Capture Powers Mobile Wayfinding Apps and Software
Many people rely on their smartphones to find directions, whether they're driving, walking, or exploring a new city. Most smartphones today come with GPS apps that show where you are on the map and provide turn by turn directions. This dynamic, personalized navigation has become second nature to most users.
To advance digital navigation, wayfinding software companies are leveraging reality capture technology to deliver real-time navigation through complex buildings and campuses, helping users orient themselves and move efficiently.
Reality capture provides accurate data for wayfinding, capturing accurate details of complex indoor and outdoor environments. It delivers digital representations of real-world spaces that can be used by software companies to develop intuitive and efficient navigation systems.
According to Conquest Creatives, “Good wayfinding systems significantly enhance the user experience by reducing stress, saving time, and ensuring safety. In complex environments like hospitals, airports, and campuses, effective wayfinding can be critical to the smooth operation of these spaces. It supports accessibility, ensuring that everyone, including those with disabilities, can navigate easily.”
What Is Wayfinding?
Wayfinding is the process of navigating a physical site and finding an optimal route to reach a destination, whether it be a specific room or building. Wayfinding technology provides real-time navigation through unfamiliar or intricate layouts across both indoor and outdoor environments.
Many companies are developing wayfinding platforms to help users reach their destination in complex spaces, such as hospitals, airports, shopping centers, and corporate campuses. Customized software and apps can be installed on a user’s smartphone and interactive kiosks on site.
These applications calculate routes between specific points or areas of interest and display them on interactive maps. When integrated with indoor positioning systems, they replicate the “blue dot” experience familiar from outdoor navigation tools like Google Maps. This allows users to locate themselves and navigate accurately without relying on GPS.
Vince Palko, GPRS Marketing Director, has spent many years in the digital geolocation realm, and has seen this evolution firsthand, “As digital interaction becomes more embedded in daily life, wayfinding apps have emerged as an innovative tool to help people navigate complex environments.”

Who Benefits from Wayfinding?
According to WaveTech, the key features of interactive wayfinding systems are designed to make navigating complex facilities more straightforward and efficient.
Wayfinding technology supports a wide range of users.
- Visitors who are unfamiliar with a location gain confidence and clarity in finding their way.
- Individuals with visual or hearing impairments can navigate more independently.
- Users speaking different languages can receive instructions in their preferred language to help navigate spaces.
- Emergency services can be assisted by providing real-time navigation and location tracking, enabling faster and more coordinated response efforts.
- In disaster planning, these tools help map evacuation routes, identify critical infrastructure, and visualize risk zones to enhance preparedness.
- By alerting users to hazards and guiding safe movement, wayfinding technology plays a key role in risk mitigation, including managing crowd flow to reduce congestion and panic.
Even those familiar with a location benefit from real-time information that improves efficiency and engagement, particularly in healthcare settings where it can strengthen patient loyalty and satisfaction.
According to UC Santa Cruz professor of Computer Science and Engineering Roberto Manduchi, "apps will enable blind people to navigate indoor buildings with spoken directions from a smartphone app, providing a safe method of wayfinding where GPS doesn’t work.”
Data Types Needed for Wayfinding Apps
Wayfinding apps provide precise step-by-step navigation using detailed 3D maps. They offer a complete navigation experience that begins at home, continues through parking, and ends at the destination. Routes can be tailored to meet individual needs, including accessibility requirements. Real-time updates and location-aware guidance reduce frustration and help prevent missed appointments by adjusting routes dynamically based on current conditions.
Wayfinding apps rely on a variety of data types to function effectively. Here's a breakdown of the key data types they typically need:
Spatial Data
- Floor plans and site maps to show accurate layouts of buildings and campuses
- 3D models using reality capture technology such as LiDAR and photogrammetry to create digital twins
- Geospatial coordinates to define locations and routes
Positioning Data
- GPS data to support outdoor navigation
- Indoor positioning systems to locate users with Bluetooth beacons, Wi-Fi signals, inertial measurement units, or magnetic field mapping
- Real-time location tracking to update user position dynamically
Routing & Navigation Data
- Pathways and connections to provide information on walkways, corridors, elevators, stairs, and ramps, etc.
- Accessibility features to support users with mobility challenges
- Points of interest to locate restrooms, guest services, entrances, and exits
Environmental & Operational Data
- Live updates on construction zones, temporary closures, and detours
- Traffic flow in busy environments like airports and hospitals
Visual & AR Data
- Augmented reality guidance onto real-world views
- Preview routes through 3D walkthroughs and visual simulations
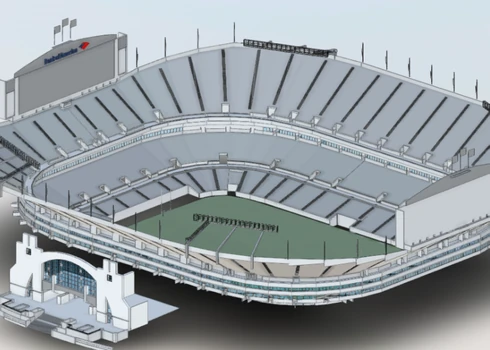
How Reality Capture Technology Supports Wayfinding
Reality capture technologies such as 3D laser scanning and photogrammetry equipment captures detailed spatial data of a site, including the building’s exterior and interior floorplans, sidewalks, parking lots and garages, entrances and exits, accessibility features, stairways, and more. In addition to capturing this spatial data, the scanner captures positioning data, routing and navigation data, environmental and operational data, and visual and AR data.
Comprehensive site data is used to create a 3D BIM model and a unified site map, which can be integrated into mobile wayfinding apps to help users navigate the site easily.
These BIM models serve as digital twins, forming the foundation for precise navigation and route planning. In complex indoor settings like hospitals and airports, reality capture ensures that floor plans and spatial data reflect the actual layout.
This technology enables wayfinding apps to map both indoor and outdoor environments with precision, identifying features such as ramps, elevators, stairs, and obstacles. Augmented reality can be layered onto real-world imagery, guiding users visually and intuitively. Users can preview their routes in immersive 3D before beginning navigation, and the app remains reliable even in areas where GPS signals are unavailable.
GPRS Reality Capture Services for Wayfinding Companies
GPRS Reality Capture Services delivers the precise spatial data needed to power wayfinding apps and enable real-time AR navigation to help users confidently navigate complex indoor and outdoor environments.
We have Project Managers in every major U.S. market ready to quickly document accurate site data. Our Project Managers undergo an extensive SIM certification training program to ensure their competence in laser scanning equipment, field knowledge, and providing accurate data for every project.
Our Project Managers use state-of-the-art equipment to document existing site conditions. With Leica 3D laser scanners, we deliver data efficiently and with an accuracy of 2-4 mm and with the Matterport Pro3, updated with LiDAR-based scanning, we can deliver 20mm accuracy.
Scans are taken in multiple positions around a site from varying viewpoints. Millions of data points are captured and processed into a point cloud, creating an accurate 3D as-built data set of the site. This all happens very quickly, with some scanners, like our Leica RTC360, capturing and calculating 2 million points per second with 2-4 mm accuracy.
Reality capture data can be collected as environments change, helping to maintain the accuracy of wayfinding apps. Frequent scans detect layout modifications, construction zones, and temporary barriers, ensuring that navigation data will remain current. This information supports augmented reality solutions that overlay digital directions onto the user’s view of the physical space.
By integrating LiDAR data with GPS, inertial measurement units, and Bluetooth beacons, wayfinding apps achieve greater precision. GPS supports outdoor navigation, while IMUs and beacons provide reliable indoor positioning where GPS signals are weak or absent. These combined technologies allow for accurate turn-by-turn directions and identification of relevant points of interest.
Reality capture provides the essential data needed to build wayfinding apps that are accurate, dependable, and user-friendly across a variety of environments.
Case Study: Reality Capture of Six Hospital Parking Garages for Wayfinding
GPRS captured precise digital representations of six uniquely structured parking garages at a healthcare campus in Atlanta, enabling a software company to build a wayfinding app that improved navigation for patients and visitors. Read the full case study.

Problem:
- The hospital campus featured multiple parking structures with inconsistent layouts, some aboveground, some underground, and some interconnected across levels.
- Patients and visitors frequently experienced difficulty navigating from their vehicles to their medical offices, resulting in frustration, delays, and operational strain on staff.
- The total space reality captured was 1,681,500 SF and included the following parking garages within the scope of work:
- Green Parking Garage - 6 Levels - 510,000 SF
- Blue Parking Garage - 2 Levels - 160,500 SF
- Purple Parking Garage - 5 Levels - 222,500 SF
- Gold Parking Garage - 3 Levels - 271,000 SF
- North Employee Garage - 6 Levels - 285,000 SF
- South Employee Garage - 5 levels - 232,500 SF
Solution:
- Before reality capture began, the team conducted walkthroughs of each parking deck with the client to confirm the scope and develop scanning strategies tailored to the vast and complex layouts, ensuring no disruption to hospital operations.
- Over the course of just one week, a three-person GPRS team used the Matterport Pro 3 and Leica RTC360 laser scanners to capture every parking level, space, stairway, and hospital access point.
- Accurate reality capture data was used to create individual 3D BIM models for each parking garage and a unified campus model, which served as the foundation for generating 2D plans and immersive virtual tours.
- Deliverables were integrated by the software company into a mobile wayfinding app featuring AR capabilities and indoor positioning to guide users through the hospital campus with ease.
Benefits:
- Reality capture provided the spatial accuracy needed to power the app’s real-time AR navigation and location-saving features.
- The 3D BIM model formed the foundation for accurate routing, orientation, and destination mapping.
- Reality capture supported augmented reality (AR) overlays by aligning digital cues, like directional arrows or points of interest, with physical features in real-world spaces.
- Accurate wayfinding reduced staff reliance for wayfinding assistance and improved operational efficiency across the campus.
- Additionally, the CAD and BIM files can be used to support future upgrades and ongoing maintenance.
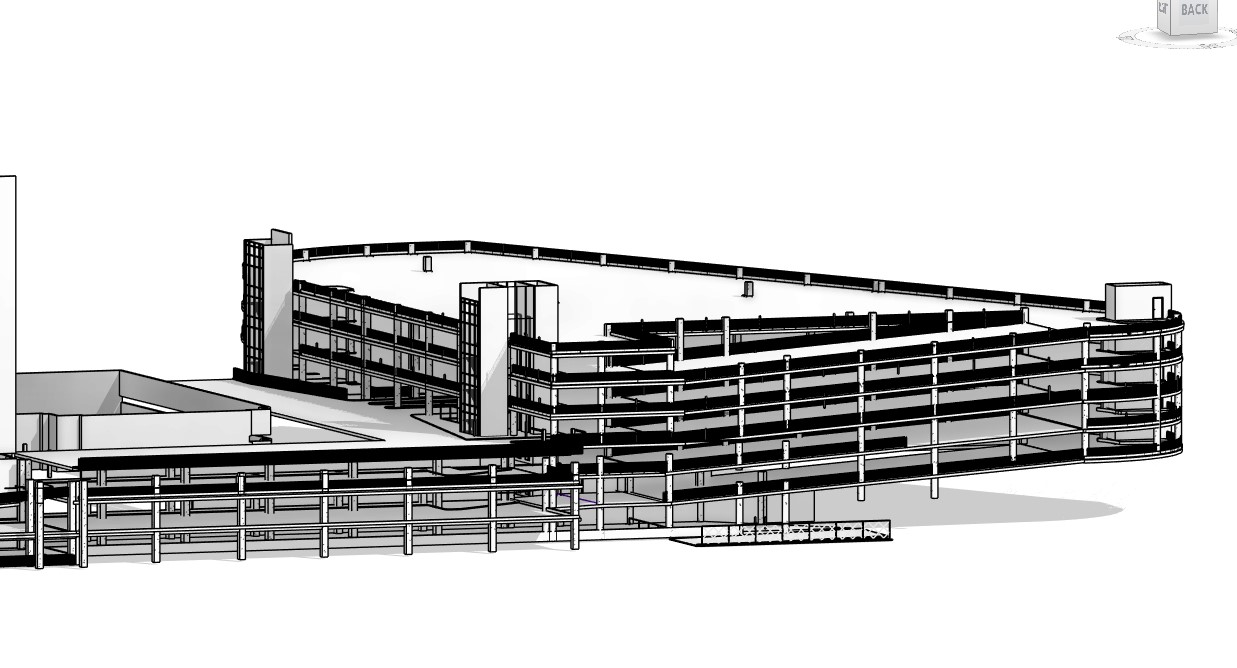
What Can GPRS Help You Visualize?
By delivering precise, real-time spatial data, reality capture empowers wayfinding software developers to build highly accurate navigation tools for complex indoor and outdoor environments. From hospitals and airports to campuses and commercial centers, these innovations enhance user experience, improve operational efficiency, and support inclusivity for all users.
GPRS Reality Capture Services provide the high-resolution 3D data that forms the foundation of these advanced wayfinding systems. In environments where accuracy is critical, GPRS helps ensure your navigation tools are dependable and up to date. Whether you're developing a mobile app or an interactive kiosk, our regularly updated scans and 3D BIM models make it easy to deliver seamless, user-friendly navigation experiences.
With GPRS, you gain a trusted partner in creating intelligently navigable spaces, powered by data you can rely on.
Contact GPRS today for more information on reality capture services for wayfinding companies, software, and apps.
Frequently Asked Questions
What is reality capture?
Reality capture is the process of digitally documenting physical environments using technologies like 3D laser scanning and photogrammetry. It produces accurate spatial data that can be used to create models, maps, and visualizations for design, construction, and asset management.
Why is reality capture better than traditional mapping methods for wayfinding?
Traditional mapping often lacks the spatial detail and real-time adaptability needed for indoor or multi-level navigation. Reality capture provides centimeter-level accuracy and enables features like AR navigation, indoor positioning, and dynamic route updates. This leads to smoother user experiences, reduced confusion, and better operational efficiency in places like hospitals or event venues.
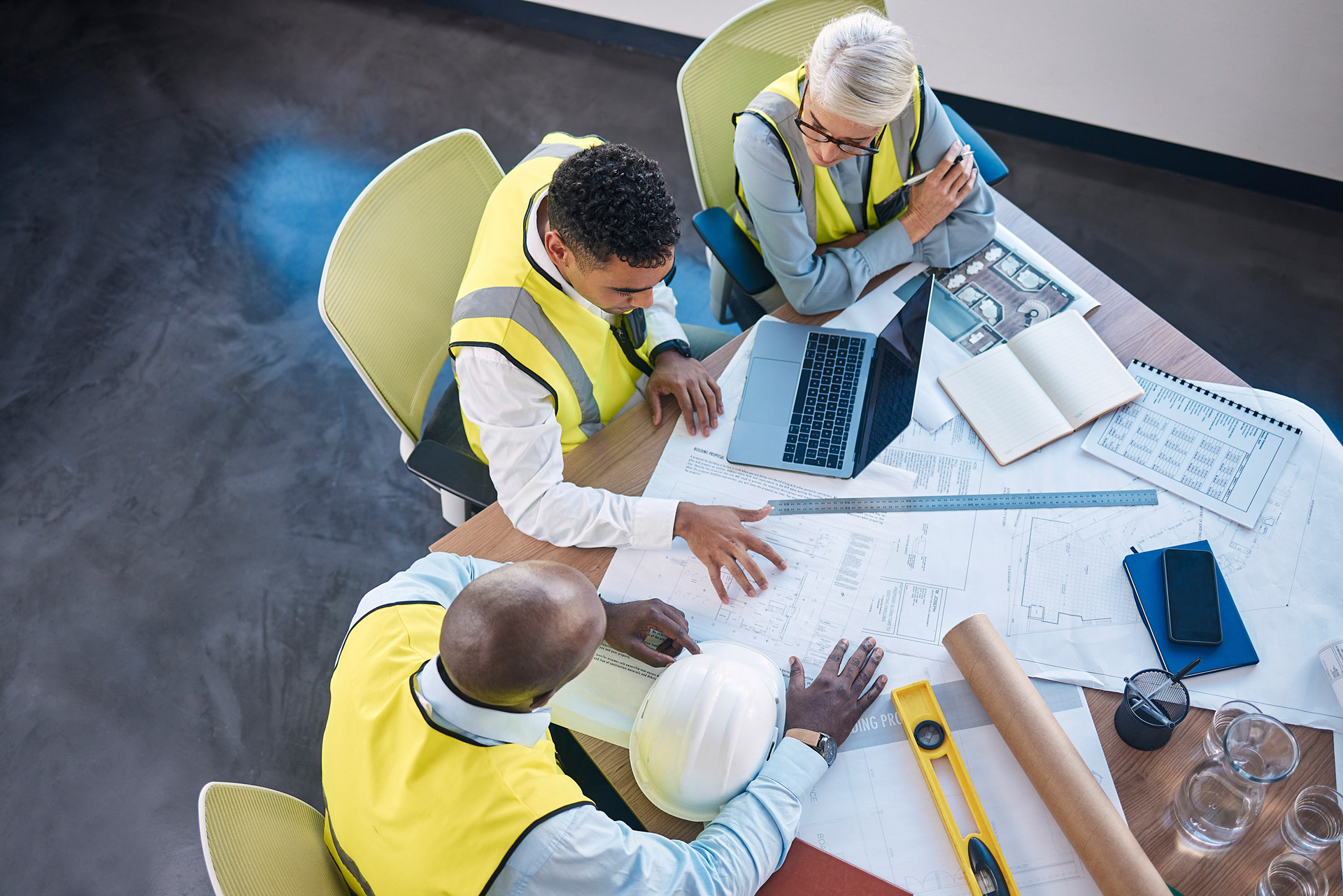
Comparing Construction Manager at Risk and Design-Build
Construction Manager at Risk (CMAR) and Design-Build (DB) are two of the most used construction delivery methods today.
Which method is right for you? The answer could be either – or neither, depending on a variety of factors.
Understanding the subtle differences between CMAR and DB is your first step toward deciding which is right for your project – or if you need to explore another option.
Defining the Models
CMAR is a delivery method where the owner hires a construction manager (CM) during the design phase.
The CM provides input on constructability – the degree to which a building’s design facilitates efficient and effective construction – cost estimating and scheduling. They then assume the role of general contractor during construction.
The CM guarantees the project’s cost through a Guaranteed Maximum Price (GMP), assuming financial risk if costs exceed that threshold.
DB consolidates design and construction responsibilities under a single entity – the design-builder. Communication and accountability are streamlined, because the owner contracts with one party overseeing both design and project execution.
Contractual Relationships and Communication Flow
A major difference between CMAR and DB lies in how their contracts are structured.
CMAR involves three primary entities: the owner, the designer (typically an architect or engineer), and the construction manager. The owner holds separate contracts with the designer and the CM, fostering a collaborative but segmented relationship. This separation allows the designer to act as the owner’s advocate, maintaining design integrity and oversight throughout the construction process.
DB merges design and construction into a single contract between the owner and the design-builder.
This unified structure can reduce adversarial relationships and streamline decision-making. However, it also means the designer is no longer an independent advocate for the owner. This can raise concerns about checks and balances, especially in complex or highly regulated projects.
Risk Allocation and Cost Control
Risk management is a defining feature of both models, but in different ways.
In CMAR, the construction manager assumes risk for cost overruns beyond the GMP. This incentivizes accurate cost estimation and efficient construction practices. The owner benefits from early cost visibility and can make informed decisions during the design phase.
DB shifts more risk to the design-builder, who must deliver the project on time and on budget. There are fewer surprises, but more pressure is on the design-builder to effectively manage both design and construction risks.
Owners must be diligent in defining project requirements upfront, as changes later in the process can be harder to implement.
Schedule and Delivery Speed
CMAR and DB both offer scheduling advantages over traditional Design-Bid-Build.
With CMAR, the CM is involved early. This enables phased construction and the ability to overlap design and build activities, which can speed up project delivery.
DB is typically faster than CMAR, because the integrated team can begin construction before the design is complete. Streamlined coordination and no bidding contribute to significant time savings. This makes DB a good choice for projects with tight deadlines.
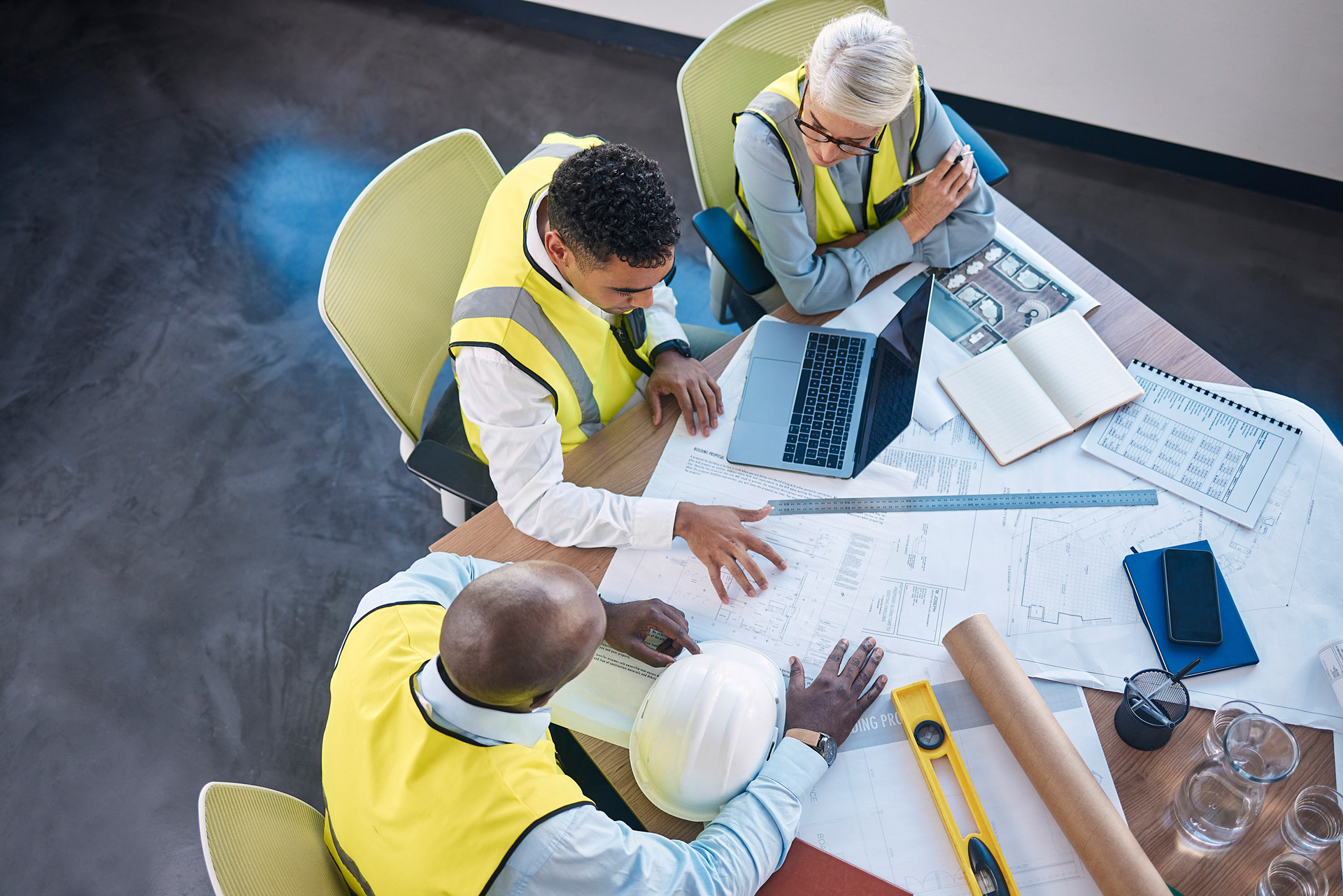
Collaboration and Innovation
With CMAR, the owner, designer, and CM work together during preconstruction. This model encourages transparency and shared decision-making, which benefits projects requiring high levels of customization or technical complexity.
DB can drive innovation through close coordination between design and construction teams. Fewer contractual barriers allow for more creativity and quicker problem solving.
The owner's influence over design decisions may be more limited. This puts more pressure on the design-builder’s ability to balance aesthetics, functionality, and cost.
Quality and Accountability
Quality assurance is another area where CMAR and DB differ.
In CMAR, the designer remains independent and can monitor construction quality on behalf of the owner. This oversight helps ensure that the project adheres to design intent and regulatory standards.
In DB, the design-builder handles both design and construction quality. While this can lead to efficiencies and fewer disputes, it also means the owner must rely on the design-builder’s internal quality controls. Choosing a reputable and experienced design-builder becomes critical to ensuring quality.
Suitability and Project Types
Choosing between CMAR and DB often depends on project characteristics and owner priorities.
CMAR is well-suited for complex projects where the owner desires a high degree of control over design and values the independent oversight of a separate designer. It is commonly used in public sector projects, healthcare facilities, and higher education buildings.
DB excels in projects where speed, cost certainty, and streamlined communication are paramount. It is frequently employed in infrastructure, industrial, and commercial developments, especially when the scope is well-defined and the owner is comfortable delegating design responsibility.
Let GPRS Keep You In Control of Your Projects
Both Construction Manager at Risk and Design-Build offer advantages over traditional delivery methods. But they cater to different project needs and organizational preferences.
Successful project delivery ultimately hinges not just on the delivery method you choose, but on the quality of the team, the clarity of the project vision, and the strength of communication throughout the process.
The best way to ensure strong, clear lines of communication throughout your project’s lifecycle is by ensuring that the data you’re planning, designing, and building off is accurate and actionable.
GPRS provides you with 99.8%+ accurate utility locates and concrete imaging, pinpoint-accurate leak detection, NASSCO-certified video pipe inspections, and construction-grade reality capture services that help you plan, manage, and build better.
All this accurate, actionable data is always at your fingertips thanks to SiteMap® (patent pending), our infrastructure mapping, and construction and facilities project management software application that provides you with 24/7, secure access to the information you and your team needs to stay on time, on budget, and safe.
What can we help you visualize?
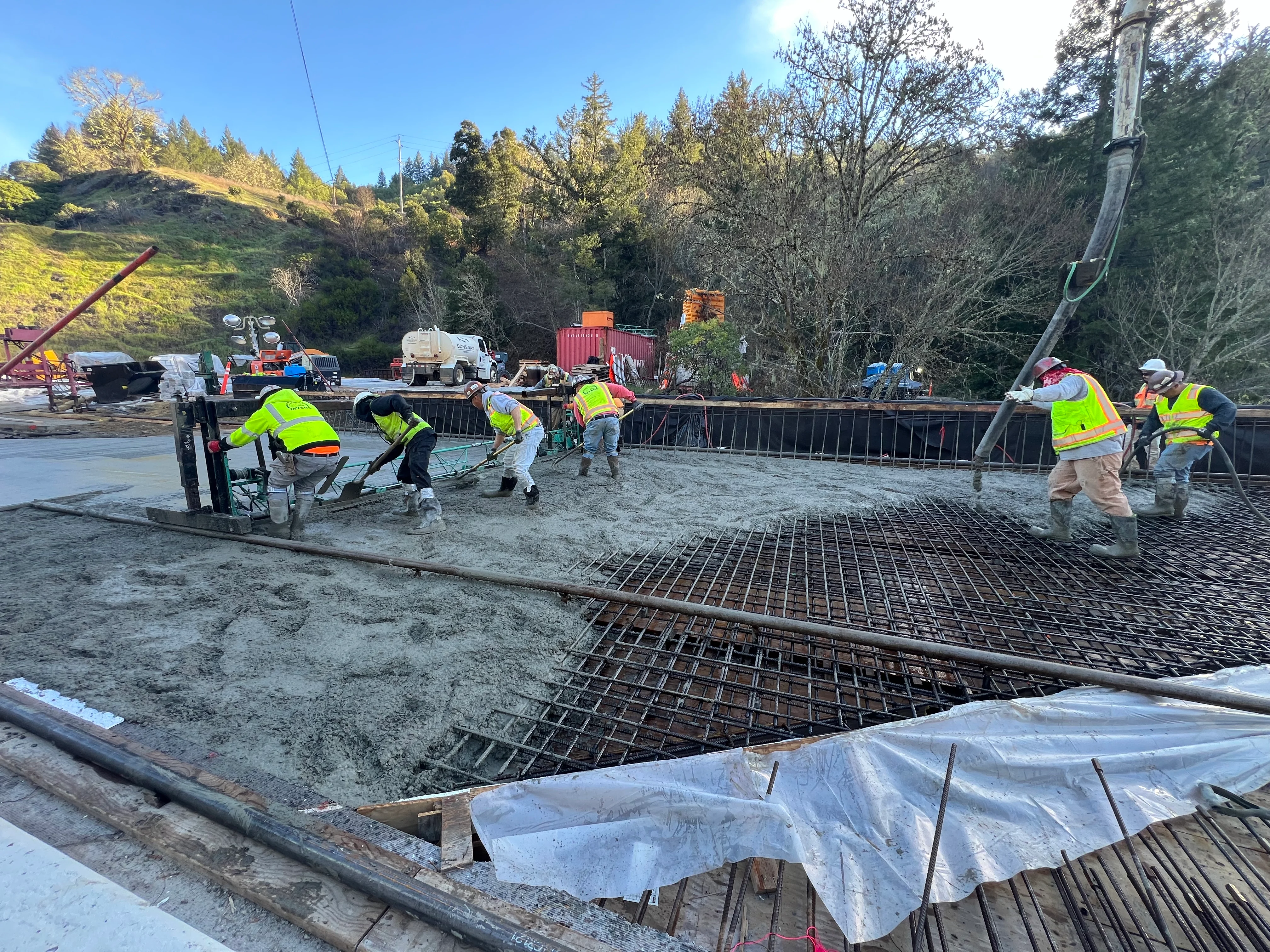
Can Stainless-Clad Rebar Extend the Lifespan of U.S. Bridges?
A Massachusetts startup claims its stainless-steel-bonded rebar can extend bridge deck service life to 100 years or more – and the reinforcements are already being used in California.
Allium Engineering, founded by MIT alumni Steven Jepeal and Sam McAlpine, developed the stainless-steel-clad rebar to be resilient to corrosion.
Rusty rebar can crack the concrete around it, making bridges more susceptible to collapsing. Eliminating the possibility of corrosion means reducing the number of repairs and extending the life of critical infrastructure such as bridges.
“Across the U.S., the typical bridge deck lasts about 30 years on average — we’re enabling 100-year lifetimes,” Jepeal told MIT News. “There’s a huge backlog of infrastructure that needs to be replaced, and that has frankly aged faster than it was expected to, largely because the materials we were using at the time weren’t cut out for the job. We’re trying to ride the momentum of rebuilding America’s infrastructure, but rebuild in a way that makes it last.”
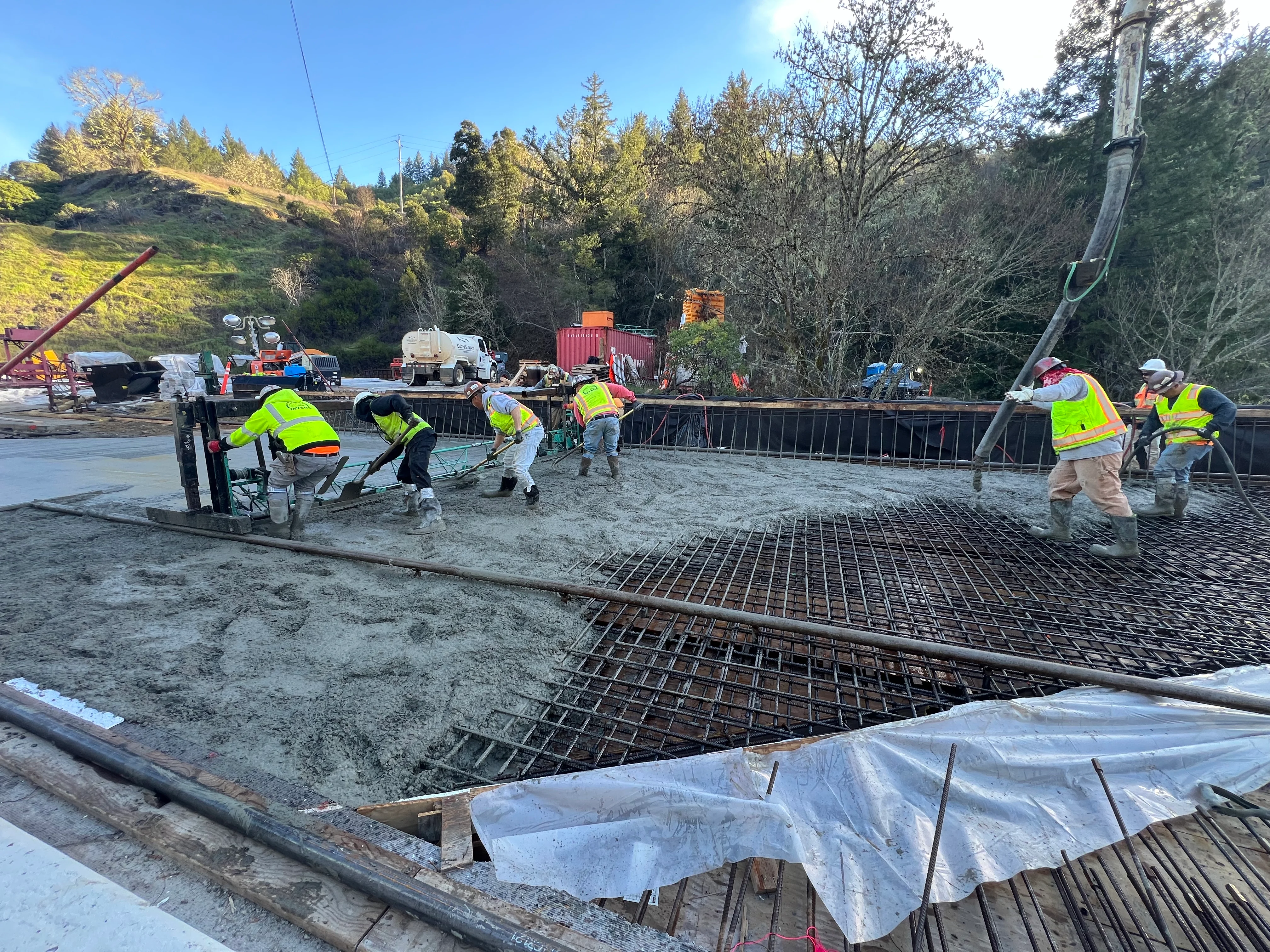
Allium’s process involves adding a thin, protective layer (less than 1-mm-thick) of Type 316 stainless steel on top of traditional ASTM A615/A706 carbon-steel rebar to make it more resistant to corrosion. The resulting mix has no gaps, breaks, or hard barriers between the two materials.
The innovation has already seen significant use, with roughly 100,000 lbs. of the rebar installed as part of construction projects around the U.S.
“We integrate our system into mills so they don’t have to do anything differently,” Jepeal explained. “We add everything we need to make a normal product into a stainless-clad product so that any mill out there can make a material that won’t corrode. That’s what needs to happen for all of the world’s infrastructure to be longer lasting.”
According to a recent Engineering News-Record article, Caltrans installed about 70,000 lbs. of the reinforced rebar on the Long Valley Creek Bridge deck along U.S. 101 in Mendocino County in the spring of 2025. The project – which marked the first use of stainless-bonded rebar on a California bridge – wrapped in April, and the California Department of Transportation continues to evaluate the rebar as it does with all new materials.
“Allium exceeded expectations,” said Gregg Granillo, vice president of fabricator ALTA Rebar, who provided a testimonial about using the product. “…our ironworkers found it familiar and easy to use.”
Allium shared a lifecycle analysis for the Caltrans deck with ENR, which is based on publicly available data from Caltrans and the Federal Highway Administration. The analysis stated a projected 87% reduction in deck ownership cost over 75 years due to savings such as less maintenance cost to replace deck rebar that’s worn down by traffic.
Caltrans has yet to release its project evaluation data, and Allium’s numbers have not undergone independent review.
“We designed it to behave exactly like conventional rebar in the field – same bends, same specs – so engineers aren’t relearning the basics,” McAlpine told ENR. “They’re just gaining corrosion resistance.”
The State of America’s Bridges
There are more than 623,000 bridges across the United States, according to the American Society of Civil Engineers (ASCE) 2025 Report Card for America’s Infrastructure.
The ASCE gave America’s bridges a C in that report card, citing the fact that 49.1% of the country’s bridges are in “fair” condition, 44.1% are in “good” condition, and 6.8% are in “poor” condition.
“Unfortunately, the nation continues to see the number of fair bridges surpassing those in good condition,” the ASCE wrote. “As bridges in fair condition continue to age – presenting the possibility of being further downgraded – they also exemplify an opportunity because they can be preserved at a lower cost than bridges in poor condition.”
Bridges received a significant amount of funding through the Infrastructure Investment and Jobs Act (IIJA), which included $27.5 billion for the Bridge Formula Program and $12.5 billion for the Bridge Investment Program.
“Despite this infusion of federal funding, bridge-related system rehabilitation needs are estimated at $191 billion,” the ASCE wrote. “Therefore, strategic asset management planning and routine maintenance are essential to keeping bridge conditions from further declining and avoiding costly repair or rehabilitation work. While the effects of extreme weather events pose threats to bridges, innovative techniques are improving their security and resilience.”
Whether or not innovations like Allium’s stainless steel-clad rebar truly revolutionize bridge construction and maintenance, it’s important that you know exactly where all reinforcements are within bridge decks and other concrete slabs before you attempt to cut or core that concrete.
Striking rebar, post tension cables or other support systems within concrete can lead to catastrophic structural failure that endangers you and your workers, and anyone else in the vicinity of your job site.
GPRS provides precision concrete scanning and imaging services designed to keep your concrete cutting and coring projects on time, on budget, and safe. Utilizing state-of-the-art ground penetrating radar (GPR) scanners and other, complementary technologies, we visualize where you can and can’t safely penetrate the slab, providing you with accurate, actionable information that helps you plan, build, and manage better.
Our SIM-certified Project Managers have achieved and maintain a 99.8%+ rate of accuracy when scanning concrete slabs for buried rebar, post tension cable, electrical conduit, and any other types of embedded obstructions that could compromise the safety and success of your project. We’re so confident in their abilities that we introduced the Green Box Guarantee, which states that when we place a Green Box within a concrete layout prior to you cutting or coring that slab, we guarantee that the area within will be free of any obstructions.
If we’re wrong, we agree to pay the cost of the damage.
From bridges to skyscrapers, GPRS Intelligently Visualizes The Built World® to keep your projects on time, on budget, and safe.
What can we help you visualize?
Frequently Asked Questions
How is GPR used to identify tendons vs. rebar in a post-tensioned slab?
In post-tensioned structures, we typically find one mat of support rebar near the base of the slab. This mat is generally consistently spaced and remains at a constant elevation.
Post-tension cables are generally found above this support mat and “draped” throughout the rest of the structure. The elevation of the cable is usually high near the beams and column lines and drapes lower through the span between beams and column lines. Knowledge of these structural differences allows us to accurately differentiate between components. Our Project Managers will leave you feeling confident in our findings and in your ability to drill or cut without issue.
What types of concrete scanning does GPRS provide?
GPRS provides two specific but different scanning services: elevated concrete slab scanning and concrete slab-on-grade locating. Elevated concrete slab scanning involves detecting embedded electrical conduits, rebar, post-tension cables, and more before core drilling a hole through the slab. Performing a concrete slab-on-grade locating service typically involves scanning a trench line for conduits before conducting saw cutting and trenching to install a sanitary pipe, water line, or something similar.
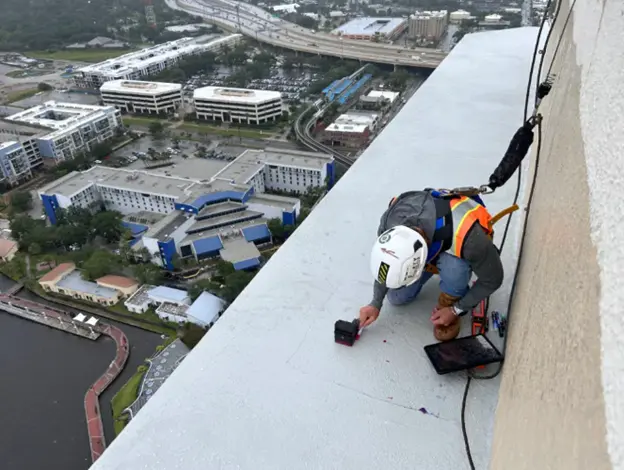
What’s Changed in the American Concrete Institute 318 Code Update?
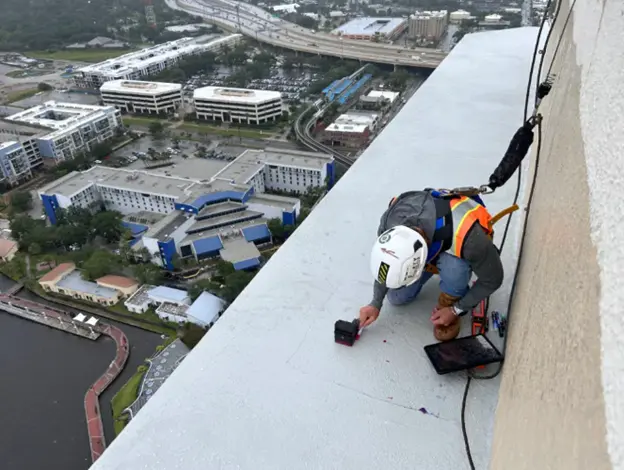
New engineering design processes, updated construction data, and the availability of innovative, sustainable materials have driven the American Concrete Institute to update is structural concrete code, known as ACI 318. The print version of the new code became available on July 9, 2025. The digital version – ACI Plus – is updated “continuously” and is also available.
“As codes evolve, so must our understanding of existing structures. GPRS plays a vital role in this process by delivering accurate subsurface and structural visualization to inform smarter, safer design modifications and rehabilitation projects.” -- GPRS Director of Reality Capture, Matt Mikolajczyk, PE (Ohio & Michigan)
What is ACI 318?
The Building Code for Structural Concrete, published by the American Concrete Institute, sets “minimum requirements for the materials, design, and detailing of structural concrete buildings, and, where applicable, nonbuilding structures.”
The organization refers to ACI 318 as its “flagship document,” arrived at “through an extensive consensus process” that covers cast-in-place, precast, shotcrete, plain, non-prestressed, prestressed, and composite construction and structural systems.
Why was ACI 318 Updated?
The last update to ACI 318 took place in 2019 (ACI 318-19). Prior to the 2019 update, the institute released regular updates approximately every three years. However, the anticipated 2022 update was scuttled when the committee instead opted to reapprove the 2019 version, (318-19 (22)), noting that the necessary updates would result in technical changes to the code itself, and that those changes would be incorporated into a subsequent wholesale update, which became ACI 318-25.
The new update, ACI 318-25: Building Code for Structural Concrete – Code Requirements and Commentary was released exclusively to ACI Plus members in the spring, and is now available for anyone to purchase.
What does ACI 318-25 Change from 318-19?
The main updates in 318-25 include:
- Seismic Design
- Shear Friction
- Deep Foundations
- Sustainability
- Performance-Based Wind Design
Seismic Design:
As is often the case, many of the changes in ACI 318-25 are to provide clarity and update existing sections of the 318 codes. New seismic design information that first made its appearance in 2019 caused a raft of clarification questions from California and the Pacific Northwest – some of the most at-risk areas for seismic activity.
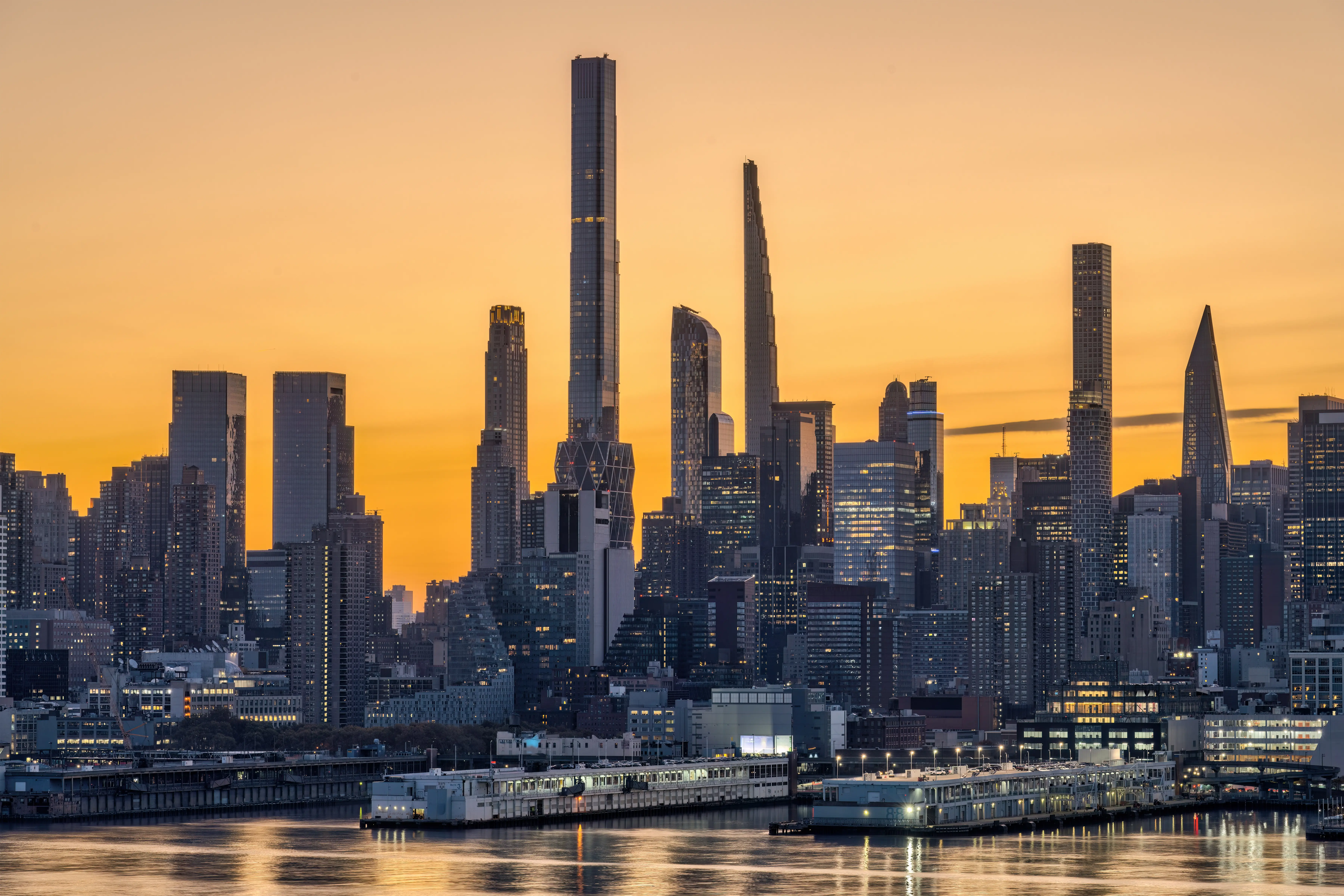
“The changes in seismic design for 318-25 include a great deal of detailed clarifications on what was in 318-19. [A lot of what] we changed in 318-25 will help seismic engineers in those high seismic regions get some designs that are a little more efficient,” Greg Ziesler, senior engineer and ACI 318 committee secretary, told Engineering News-Record.
Deep Foundations:
Concrete professionals, designers, engineers, and developers will also find an expanded section on deep foundations, building on work begun in 318-19, which was the first time deep foundations were mentioned in the code, when the institute attempted to include provisions from the International Building Code. ACI 318-25 consolidates the IBC and ACI deep foundation standards into one document.
Shear Friction:
Another update provides guidance on shear friction. 318-19 prompted a federal agency to reach out regarding the roadblocks it presented, so ACI’s committee strove to clarify the standards to avoid too broad an application and to “address discrepancies,” according to Ziesler.
Structural engineers are hailing the updates to deep foundation and shear guidance, particularly the sections on pile caps and rafts on piles: included in clause 13.4.6.8 with the exemption from the size effect – under specific conditions – for two-way shear, with specifications on center-to-center spacing measurements for rafts on piles and pile caps, 13.4.6.1’s minimum edge distance and 13.4.6.3’s embedment depths for piles. Plus, a simplification of the one-way shear equation in 13.4.6.8.
And Structure Magazine cites important changes in chapter 17 & 25’s concrete anchoring specification updates. They tagged five “major updates” in anchorage:
- Updates to safety factors
- Introduction of a beneficial overturning moment term
- Beneficial separation of concrete and steel failure modes in interaction equations
- Permissible use of new Chapter 25 factors on existing reinforcement
- Clarifications on the use of reinforcing bars as anchor reinforcement
Some items in the anchoring updates are administrative – moving sections and some equations for document consistency, and others update equations for concrete failure modes, and include an important differentiation between redundant and non-redundant fastenings, “providing a capacity benefit for fastenings that are considered redundant.”
There is also a new strength-increasing factor and equation in section 17.6.2.7 regarding concrete breakout in tension to account for “the positive influence of the compressive toe of an overturning connection moment.” While related to concrete strut behavior, its function differs.
And updates to that clarify the use of reinforcing bars as anchor reinforcements allow you to omit concrete breakout calculations by replacing them with steel calculations for special reinforcing bars, and changes in 17.5.2.1.1 and 17.5.2.1.2 create anchor reinforcement subsections regarding tension and shear breakout. 17.5.2.1.3 clarifies requirements for anchor reinforcements that are not parallel to the load, and 17.5.2.1.4 gives specific requirements on when to use shear friction calculations included in section 22.9. There are also multiple changes to the connection between “concrete structural members” regarding design requirements and updated hooked-bar and headed-bar development length equations.
Sustainability:
Perhaps the most talked-about update in ACI 318-25 is the supplemental sustainability guide. Rather than provide guidance for sustainable material use and best practices, the supplement focuses on meeting state and local ordinances and requirements.
“This is more that the local jurisdiction says you must [meet] this GWP [Global Warming Potential], so how do you meet that? We now have a framework to meet those requirements,” Ziesler said.
In the supplement, you will find items about meeting low-carbon, and carbon-neutral goals in the design & planning phase. It also includes additional guidance for building more resilient concrete structures – to withstand natural disasters – and provides suggestions as to which types of structures may be best suited to do so. This guidance varies from what already exists in the code, to provide background for those planning in the maze of sustainability initiatives.
“These are different types of loads, not in the body of the code. So now if someone says you have to do this, you have a body of knowledge to do it,” Ziesler told ENR.
Materials Are Not Dismissed
While ACI-323 (part of the 318-25 update) does cover materials, specifically low-carbon concrete, ACI was searching for a way to provide sustainability guidance that did not require new standards, according to ACI’s Mike Tholen. Tholen told ENR that “We still lean on local jurisdictions to set the limits, but there are some default options in there, based on the size of the project and what sort of targets you have to meet for GWP. One reason it’s in a separate standard is that it’s not the law of the land until a local jurisdiction adopts it.”
Performance-Based Wind Design:
Like the sustainability updates, including performance-based wind design guidance is not part of the code standard, but acts as a primer for those building tall and supertall concrete structures.
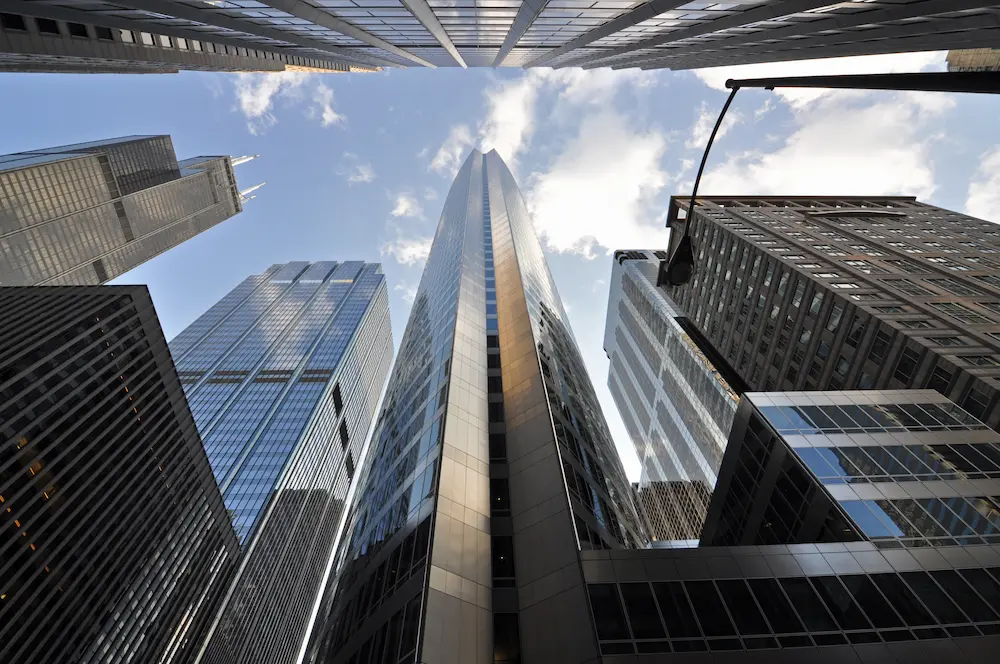
The American Society of Civil Engineers (ASCE) provided a more formal “pre-standard” for the 2019 code, whereas the ACI’s appendix on the matter is less structured. For instance, it does not require wind tunnel or computer simulations, which add costs. Ziesler noted that when you’re putting a tall or supertall design in a wind tunnel, you’re most likely going to pivot to a performance-based design. ACI’s purpose in offering what ENR refers to as “an optional standard for wind,” is making sure everyone involved in a design can feel confident of its ability to perform, specifically regarding detailing requirements that would only come into play for tall and supertall construction.
“Performance-based wind design… is a response to the industry from committee members. We have a lot of committee members who do tall and supertall buildings,” Ziesler shared. It’s not an appendix to the code; it's not in main body of code; it only applies when you do it.”
GPRS’ Mikolajczyk, who is a structural engineer licensed in Ohio and Michigan, shared that, “Structural engineers need to be aware of the information contained in this concise, high-level summary of the critical updates in ACI 318-25: particularly regarding anchorage, seismic detailing, deep foundations, and sustainability considerations.”
The Building Code for Structural Concrete provides you with the specific and technical requirements, specifications, and guidelines for building with concrete. GPRS provides you with the concrete scanning, imaging, and reality capture solutions you need to cut, core, and anchor your concrete structures safely and give you the accurate as-builts you need to renovate, expand, or maintain your buildings through their entire life cycle – from preconstruction through demolition.
Concrete scanning & imaging services are just one of the ways GPRS Intelligently Visualizes The Built World® to help you plan, build, and manage better.
What can we help you visualize?
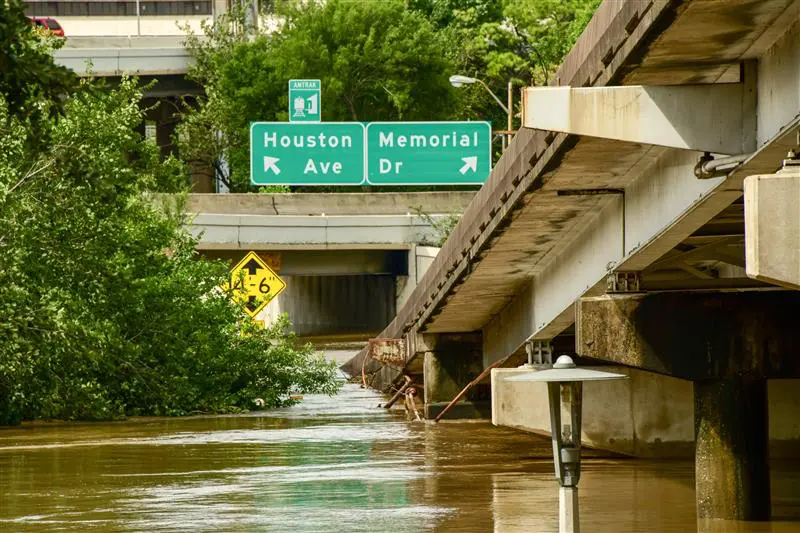
NYC’s $700M Subway Upgrades Depend on $30B Sewer Reworks
A $700 million program designed to protect New York City’s subway system from flash flooding reportedly depends on a $30 billion, multi-decade plan to upgrade the Big Apple’s aging sewer network.
According to a recent Engineering News-Record article, the Metropolitan Transportation Authority is moving forward with its $700 million program to fortify NYC’s subway system against flash flooding. This comes on the heels of a storm earlier this summer that dropped 2.1 inches of rain just one hour, overwhelming the city’s combined sewer system and flooding the subway tunnels.
According to ENR, crews pumped more than 15 million gallons overnight to restore service.
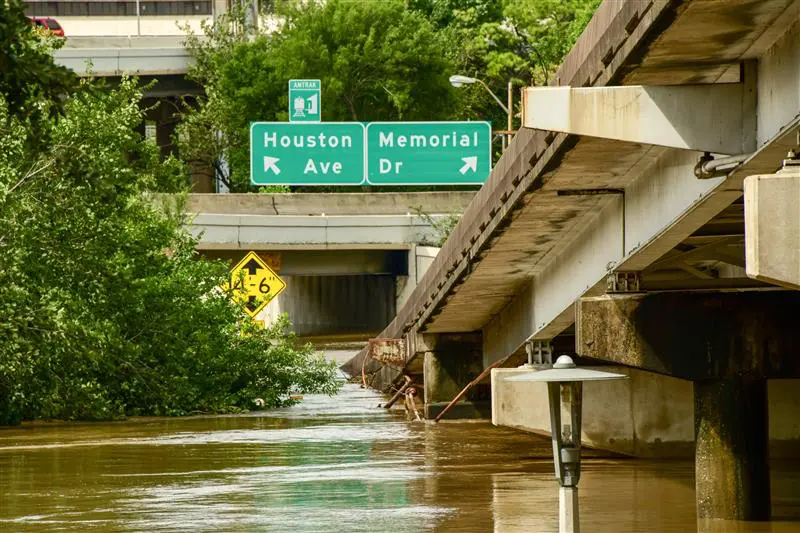
“We pump 10 million gallons on a dry day. Yesterday, we pumped like 15 million plus,” MTA Chair and CEO Janno Lieber said in a July 16 interview on local television news station NY1. “We got 2.1 inches in one hour last night. That’s when the big backups happen.”
The Difference Between Combined and Separate Sewer Systems
Most communities across the U.S. rely on separate sanitary sewer systems. In these systems, one set of pipes collects wastewater from homes and businesses and carries it to a wastewater treatment plant through sanitary sewers. While a separate set collects stormwater from drains at the ends of driveways, around parking lots, and along streets and carries it to a local waterway through municipal separate storm sewer systems.
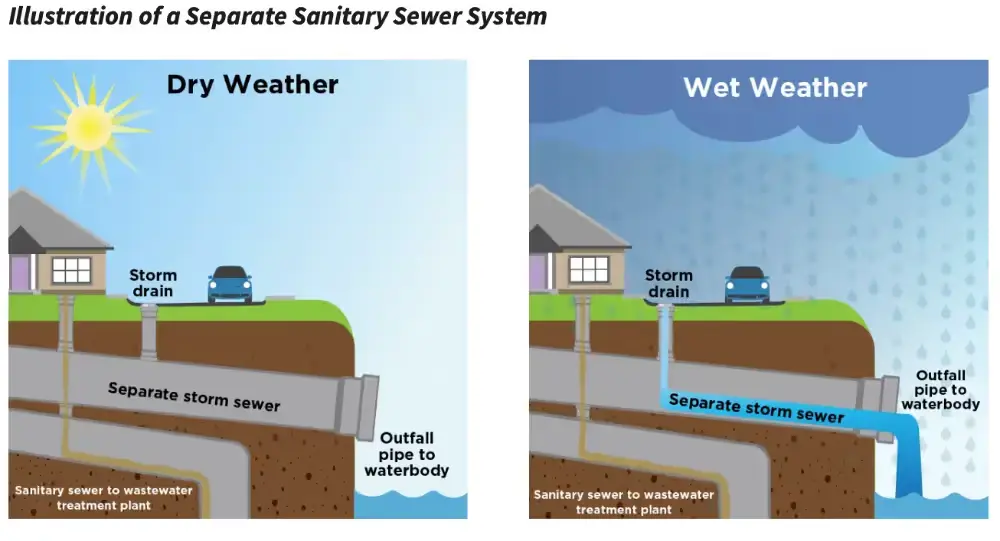
In a combined sewer system, both wastewater and stormwater flow through the same pipes. In dry weather, all wastewater flows to a wastewater treatment plant where it is treated before being discharged to a waterbody. During wet weather, however, stormwater enters the system.
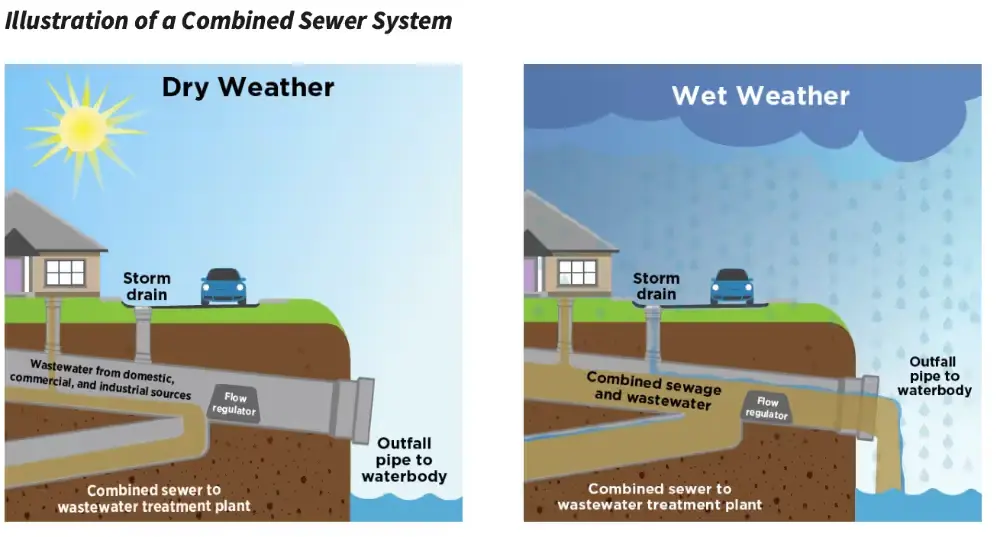
The combined flow of wastewater and stormwater can overwhelm a combined sewer system, which is why permitted outfalls are located throughout the system to act as relief points during wet weather. These outfalls discharge untreated or partially treated stormwater and wastewater into nearby waterbodies. These discharges are called combined sewer overflow (CSO) discharges, and they are a major water pollution and public health concern because they can contain bacteria, debris, and other hazardous substances that can be harmful to people, pets, and wildlife.
Approximately 700 communities across the U.S. currently rely on combined sewer systems and experience combined sewer overflow discharges, according to the U.S. Environmental Protection Agency.
Most of these communities are in the northeast and around the Great Lakes – the source of drinking water for more than 40 million people in the U.S. and Canada, and home for more than 3,500 plant and animal species, some of which are found nowhere else on Earth.
The Clean Water Act (CWA) requires communities with CSOs to put controls in place to address these concerns. But the best way a municipality can mitigate the dangers of CSOs is to overhaul their wastewater infrastructure to separate wastewater and stormwater flow.
Explaining NYC’s Plan to Fortify its Subways – and Upgrade its Sewers
The MTA’s plan to protect New York’s subways from flooding includes raising entrances at flood-prone stations, upgrading nearly 250 pumping stations and reinforcing embankments along Metro-North’s Hudson Line.
Meanwhile, the city’s Dept. of Environmental Protection (DEP) is working to manage stormwater at the street level. The DEP previously unveiled a citywide hydraulic model of its 7,500 miles of sewers, which allows engineers to simulate system performance during extreme weather and prioritize high-risk areas.
DEP estimates that comprehensive sewer upgrades, including larger mains and underground detention systems, could cost up to $30 billion. In an effort to accelerate resiliency, the agency is combining traditional gray infrastructure – traditional stormwater infrastructure in the built environment such as gutters, drains, pipes and retention basins – with green infrastructure – infrastructure such as permeable pavement, rain gardens, bioretention cells (also known as bioswales), vegetative swales, etc. that mimics nature and captures rainwater where it falls.
Nick Nyhan, founder of a grassroots neighborhood resilience effort called The City Sponge, told ENR that distributed solutions are critical alongside larger infrastructure investments.
“Even if you gave DEP $30 billion, they can’t keep up with the water,” Nyhan said. “You need individuals and neighborhoods to adopt small-scale mitigation measures—rain barrels, permeable paving, backflow valves—because the city can’t do it alone.”
“People see a bioswale or rain garden, and it’s beautiful,” Nyhan added. “That matters. Big sewer projects don’t give you that same visible payoff.”
Robert Freudenberg, Vice President for Energy and Environment at New York-based planning nonprofit, the Regional Plan Association, told the publication that coordination between the MTA and DEP, while improved, continues to be hampered by the fact that the two agencies operate under separate capital budgets. The unpredictability of flash flooding adds complexity to planning efforts, and attention is constantly being shifted away from the problem due to the cyclical nature of these events.
“…As soon as those floodwaters disappear, our focus and attention go back to other things,” Freudenberg said.
The State of America’s Stormwater Infrastructure
America’s stormwater infrastructure earned a D+ in the 2025 American Society of Civil Engineers (ASCE) Report Card for America’s Infrastructure.
This represents a modest bump from previous years, but still highlights the fact that these critical systems are largely underfunded, outdated, and increasingly vulnerable to the pressures of climate change and urban growth.
An outdated, defective stormwater system can lead to flash floods, sewer overflows, and water contamination. In its report, the ASCE noted that more than 850 billion gallons of untreated sewage is discharged annually due to combined sewer overflows.
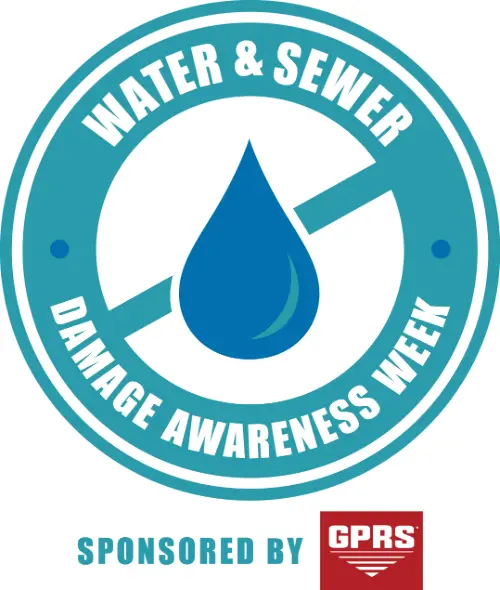
Learn how to better maintain the water and wastewater infrastructure under your care by signing up for a free Water & Sewer Damage Awareness Week (WSDAW) presentation. Each year, GPRS’ safety experts travel across the country to speak with municipalities, engineering firms, facility managers, and property management firms about the best practices they can execute to keep these critical utilities running smoothly.
Click here to sign up for your free WSDAW presentation today!
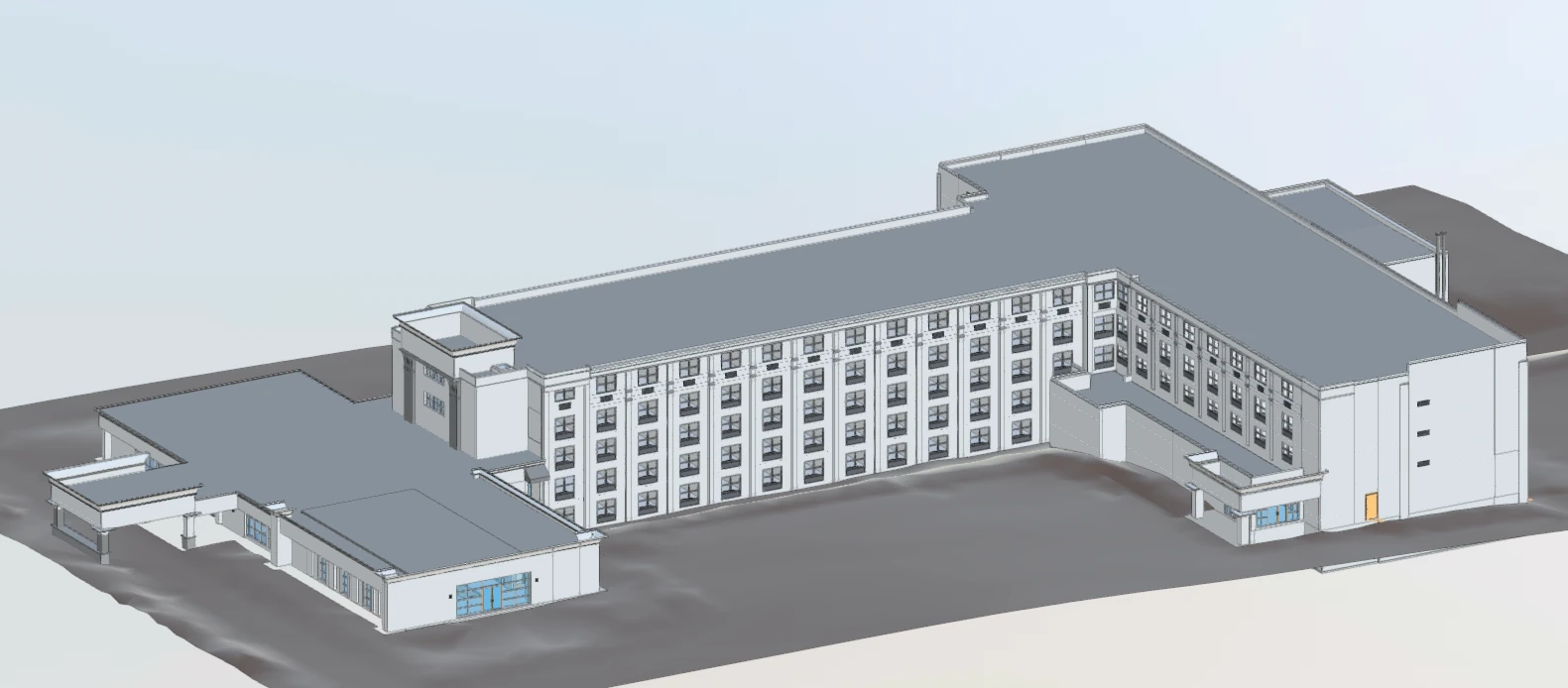
What is the Difference Between Revit and AutoCAD?
Choosing between Revit and AutoCAD is an important decision that can impact your project’s efficiency, collaboration, and final deliverables. Each software offers distinct advantages depending on your project scope, whether you need precise 2D drafting or a comprehensive 3D model for integrated project management. Understanding the strengths of each software helps ensure you select the right solution for your project's goals and team dynamics.
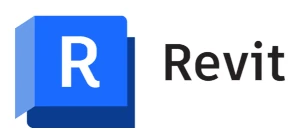
What is Revit?
Revit is a Building Information Modeling (BIM) software developed by Autodesk for designing, modeling, and documenting buildings in a coordinated 3D environment. It enables architects, engineers, and construction professionals to work collaboratively across disciplines using intelligent, data-rich 3D BIM models.
What is a Revit Model?
A Revit model is a comprehensive digital representation of a building or site, created using Autodesk Revit software. A Revit model can be used throughout the building lifecycle, from design and documentation to construction and facility management.
Revit models are created by BIM Specialists, VDC Specialists, BIM/CAD Designers, Architects, and Engineers who have a degree and experience in computer-aided drafting and design (CADD) and BIM.
Each Revit model contains detailed information about all building systems, components, and infrastructure including:
- Architectural elements like walls, floors, doors, windows, and finishes
- Structural systems such as beams, columns, foundations, and load-bearing walls
- Mechanical systems including HVAC ducts, air handling units, and ventilation layouts
- Electrical systems like lighting, power distribution, and fire alarms
- Plumbing systems covering piping, fixtures, and drainage
- Subsurface utility data including public and private utilities, such as gas lines, electrical cables, telecommunication lines, sewer lines, and other buried infrastructure
- Concrete imaging data delivering structural support documentation for concrete slabs, including rebar, post tension cables, electrical conduits, potential voids, and more
A Revit model is a building information model (BIM), meaning it not only contains the 3D geometry of the building, but also includes information about every building element documenting all components, properties, materials, and the spatial relationships between them.
Unlike traditional drafting tools, Revit uses a parametric modeling approach, which means that every element in the model is interconnected. Changes made to one element in the model are automatically reflected in all related views and components, ensuring consistency and reducing errors.
Revit Families and BIM Content
Revit classifies all project components into three primary element types: model elements, datum elements, and view-specific elements. These elements are organized into families, which define both geometry and behavior.
A Revit model is built using these families.
- System families are built-in and include core elements like walls, floors, and roofs
- Loadable families are user-defined or manufacturer-specific components such as doors, windows, and furniture
- In-place families are custom elements created for a specific project context
Each element in Revit is an instance of a family type and has two sets of properties:
- Type properties apply to all instances of a family type. Changing a type property, such as wall thickness, affects every instance of that type.
- Instance properties are unique to each placed element. These control attributes like location or elevation without affecting other instances.
This family structure ensures consistency across the model while allowing flexibility for individual elements.
According to Adam Silbaugh, GPRS Senior Modeling Technician, “Revit models are rich with data – they increase collaboration across disciplines, support clash detection, and facilitate accurate quantity takeoffs, scheduling, and maintenance planning.”
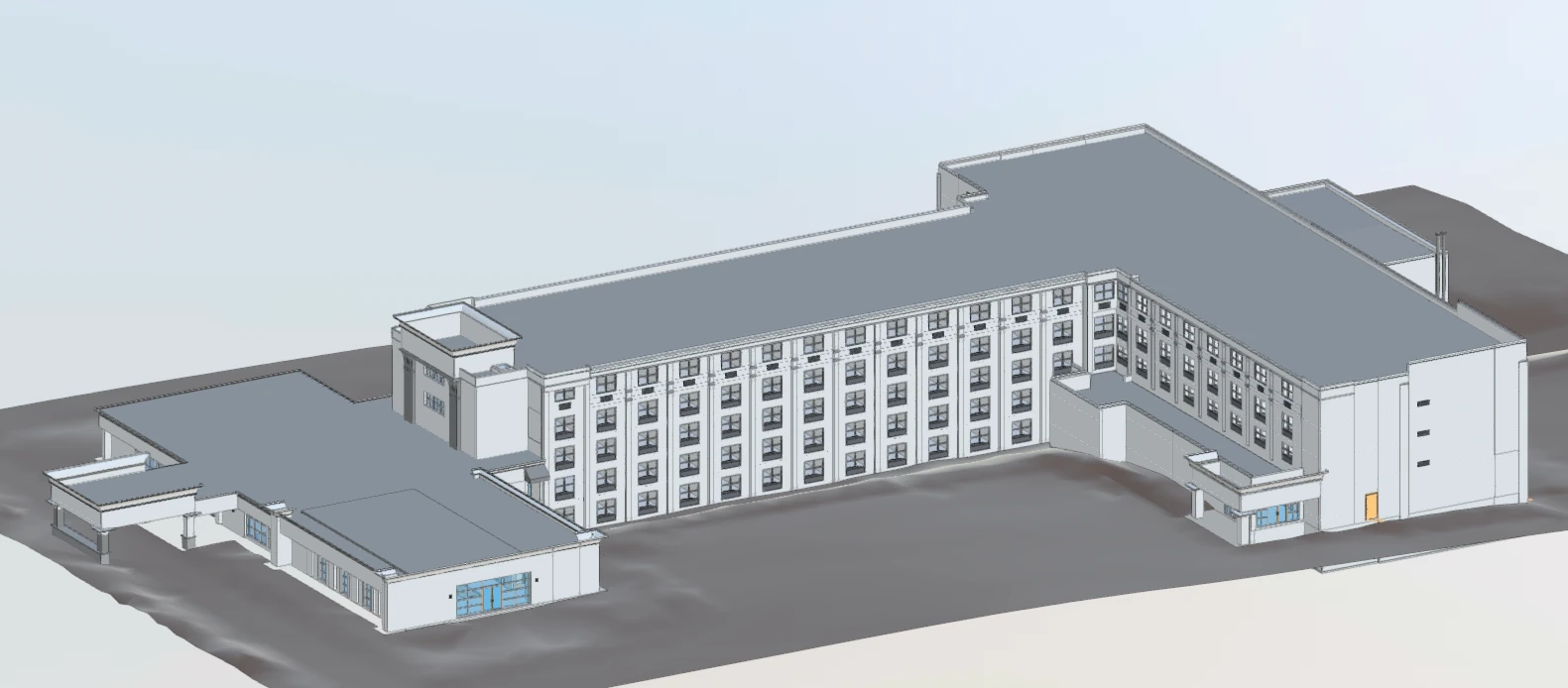
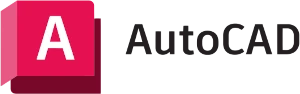
What is AutoCAD?
AutoCAD is a computer-aided design (CAD) software developed by Autodesk, used for creating precise 2D drawings and 3D models to support drafting, annotation, and design planning. AutoCAD operates on a vector-based system, allowing users to define geometry with exact dimensions and relationships. It includes tools for layer management, parametric constraints, and external references, and supports automation through scripting and APIs.
What is an AutoCAD Model?
An AutoCAD model is the digital representation of a design created within the AutoCAD environment. This model can be either two-dimensional (2D) for plans, sections, and schematics, or three-dimensional (3D) for spatial and volumetric representations. The model is composed of objects such as lines, arcs, polylines, solids, and surfaces, each defined by precise coordinates and properties. These models are typically saved in DWG or DXF file formats and can be used for visualization, fabrication, and integration into larger design workflows.
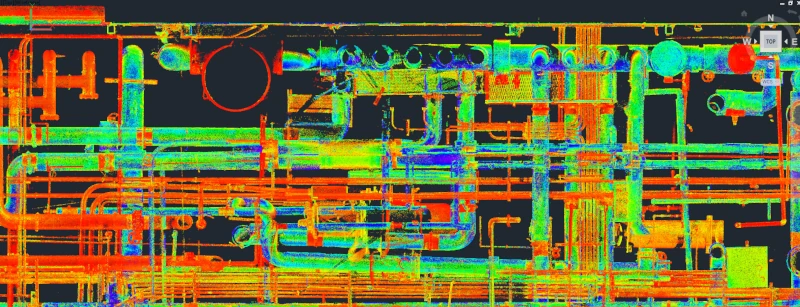
What is the Difference Between Revit and AutoCAD?
The difference between Revit and AutoCAD lies in their fundamental design philosophies and intended use cases. AutoCAD is a design and drafting software, while Revit software provides a more integrated and intelligent BIM environment.
AutoCAD is a general-purpose drafting tool that creates 2D drawings and 3D models using lines, arcs, and shapes. It is widely used across industries for tasks that require precision drafting, such as mechanical design, electrical schematics, and civil layouts. AutoCAD operates primarily in a file-based environment, where drawings are created and edited independently. Changes in one drawing do not automatically affect others unless manually coordinated.
Revit is a software built for the architecture, engineering, and construction industry. It supports BIM workflows, which means it manages not just geometry but also metadata associated with each building component. A Revit model is a comprehensive, data-driven representation of a building project that supports collaboration, automation, and analysis. Every element is part of a larger system, and changes propagate throughout the model. For example, modifying a door size in a floor plan will update the elevation, section, and schedule views automatically. This connection reduces redundancy and improves accuracy.
Another key difference is how each software handles collaboration. AutoCAD users typically work on separate files and rely on external references to coordinate drawings. This approach can lead to version control issues and misalignment between disciplines. Revit uses a central model that multiple users can access simultaneously. Changes are tracked and managed through work sets and permissions, allowing teams to collaborate in real time. This capability is essential for large projects where coordination between architecture, structure, and MEP systems is critical.
Revit also supports advanced features such as clash detection, energy modeling, and construction phasing. These tools help identify conflicts between systems before construction begins, simulate building performance, and plan construction sequences. AutoCAD lacks these integrated capabilities and often requires third-party software or manual processes to achieve similar results.
In terms of output, AutoCAD produces drawings that are primarily used for documentation. These drawings are static and require manual updates when changes occur. Revit produces models that generate drawings dynamically. Views such as plans, sections, and elevations are derived from the model and update automatically when the model changes. This approach ensures consistency across all documentation and reduces the risk of errors.
Revit also integrates with other Autodesk tools such as Navisworks, BIM 360, and InfraWorks, creating a connected platform for design, construction, and operations. AutoCAD does not offer the same level of integration for BIM workflows. It remains a powerful tool for drafting but lacks the intelligence and automation found in Revit.
For firms requiring BIM, Revit offers a more robust platform for managing complex projects. It supports lifecycle management from concept through construction and into operations. AutoCAD remains valuable for tasks that require precise control over geometry or when working in industries that do not require BIM.
Should I Choose Revit or AutoCAD?
The choice between Revit and AutoCAD depends on the specific needs of your project and your role in the design process. AutoCAD excels in 2D drafting and detailed design work, while Revit is designed for Building Information Modeling (BIM) and collaborative, large-scale projects. If your work involves detailed 2D drawings, site plans, or smaller projects, AutoCAD is a good fit. If you're working on complex, collaborative projects like commercial buildings, or if you need to leverage BIM for integrated project management and real-time collaboration, Revit is the better choice.
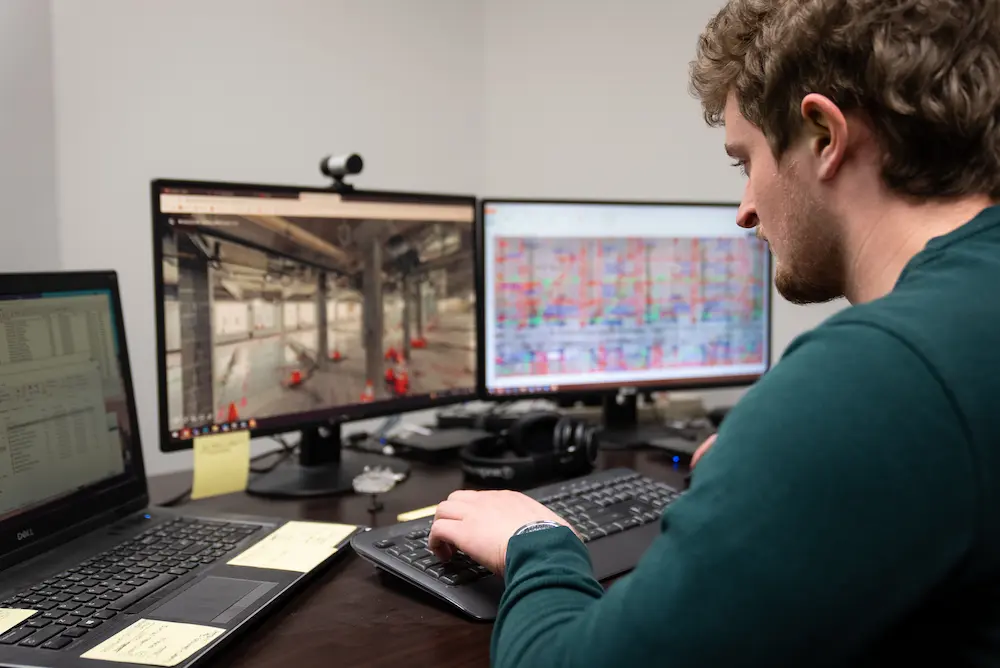
What is GPRS’ Process to Create a Revit Model?
GPRS Project Managers use high-accuracy Leica survey-grade laser scanners to capture millions of data points of a project site, creating a point cloud that represents the existing site conditions.
This point cloud data is then imported into Autodesk Revit, where GPRS's in-house Mapping & Modeling Team transforms it into a detailed 3D BIM model.
“Whether our client is designing, coordinating, or installing, our Mapping & Modeling team produces precise BIM models that align with their standards, templates, and naming conventions,” said Silbaugh.
The Revit models created by GPRS can be used for various purposes, including:
- As-built documentation: Providing a precise representation of existing structures and systems
- Design and planning: Facilitating design modifications, renovations, and construction
- Clash detection: Identifying potential conflicts between different building and MEP systems before retrofits
- Facility management: Creating a digital twin of the facility for ongoing operations and maintenance
We provide existing conditions information to support our client’s architecture, engineering and construction projects. By providing a shared, accurate digital representation of the site, Revit models enhance collaboration among project teams and stakeholders.
GPRS also integrates the Revit models and other data into our SiteMap® GIS platform, providing clients with a centralized, web-based platform for accessing and managing project information.
Whether you're planning, designing, or managing a facility, we deliver intelligent, customized 3D models in Revit or AutoCAD tailored to your project’s exact needs. Our models go beyond basic documentation, they provide the accuracy, clarity, and insight you need to make confident decisions, streamline collaboration, and reduce costly surprises down the line.
Click here to request a quote for Revit modeling services and AutoCAD modeling services.

How to Better Manage Your Subcontractors
Dealing with suboptimal subcontractors is one of the most annoying parts of every general contractor’s life.
Especially today, when GCs are more reliant on subcontractors than ever before.
A recent Construction Dive article even explored ways in which general contractors can protect themselves from, and control problem subs.
Trent Cotney, a partner and head of the construction practice at Tampa, Florida-based Adams and Reese, said in the article that there has been exponential growth in the use of subcontractors on job sites since the onset of the COVID-19 pandemic.
And with that exponential growth has come more instances of GCs seeing their projects implode thanks to problem subcontractors.
“A ‘problem subcontractor’ would be any person or entity who consistently causes issues that would negatively impact a construction project,” Cotney told the publication. “Common problems include work delays, miscommunication or non-communication, lack of proper equipment or expertise or manpower, a failure to comply with safety regulations, or payment issues and delays – all of which affect project continuity.”
As a GC, you can’t be everywhere all the time. You can’t keep one eye on your subcontractors throughout the entire project lifecycle.
Or can you?
SiteMap® (patent pending), powered by GPRS, is an all-in-one infrastructure mapping and facility management platform that provides you with a single source of truth for the accurate, actionable data you need to plan, manage, dig, and ultimately, build better. It grants you an unprecedented level of control and oversight, whether you’re on-site or half a world away, allowing you to eliminate the risks caused by miscommunications – and stop problem subcontractors from hampering your project.

The Challenges of Managing Subcontractors
Lack of real-time visibility into a subcontractor’s work is one of the biggest challenges that contractors face.
Without a standardized process of documentation and reporting, GCs risk communication breakdowns, scheduling conflicts, and mistakes that lead to budget overruns and safety issues.
If you don’t mandate who your subcontractors hire to obtain as-built infrastructure data, you can’t ensure the quality of the information they’re receiving. And building off bad data is a recipe for disaster.
SiteMap Explained
SiteMap is an infrastructure mapping, and facility and construction project management solution that serves as a digital storage platform for blueprints, as-built drawings, geolocated subsurface utility maps, sewer inspection data, and more.
SiteMap grants a unified view of all users’ information – whether they’re overseeing one construction project or multiple projects across the United States. What sets it apart from other cloud-based GIS platforms is that it’s backed by the field-verified, accurate data collected on-site by GPRS’ SIM-certified Project Managers.
That’s 99.8% accurate utility locates and concrete imaging, 2-4mm accurate 3D laser scans, pinpoint accurate leak detection surveys, and NASSCO-certified video pipe inspections. And it’s all secured in one place, accessible 24/7 from any computer, tablet or smartphone.
SiteMap offers a range of benefits and features that can be customized to meet your needs and resources.
How SiteMap Enhances Your Control Over Your Projects
- Real-Time Visibility: With 24/7, secure access to accurate, complete project data, you’ll know what work has been completed and what still needs to be done.
- Improved Communication and Coordination: You and your team – including all your subcontractors – can work off the same data, eliminating the chance for communication siloes that lead to costly, and potentially dangerous, mistakes.
- Accountability and Documentation: Safeguard the accuracy of your project’s data by controlling the single source of truth for that data. With SiteMap, nobody can claim they didn’t have the right information to do their job.
- Safety: When a subcontractor needs to core into a concrete slab or excavate, SiteMap tells them where they can do so safely. Mitigating the risk of subsurface damage keeps your project on time, on budget, and safe.
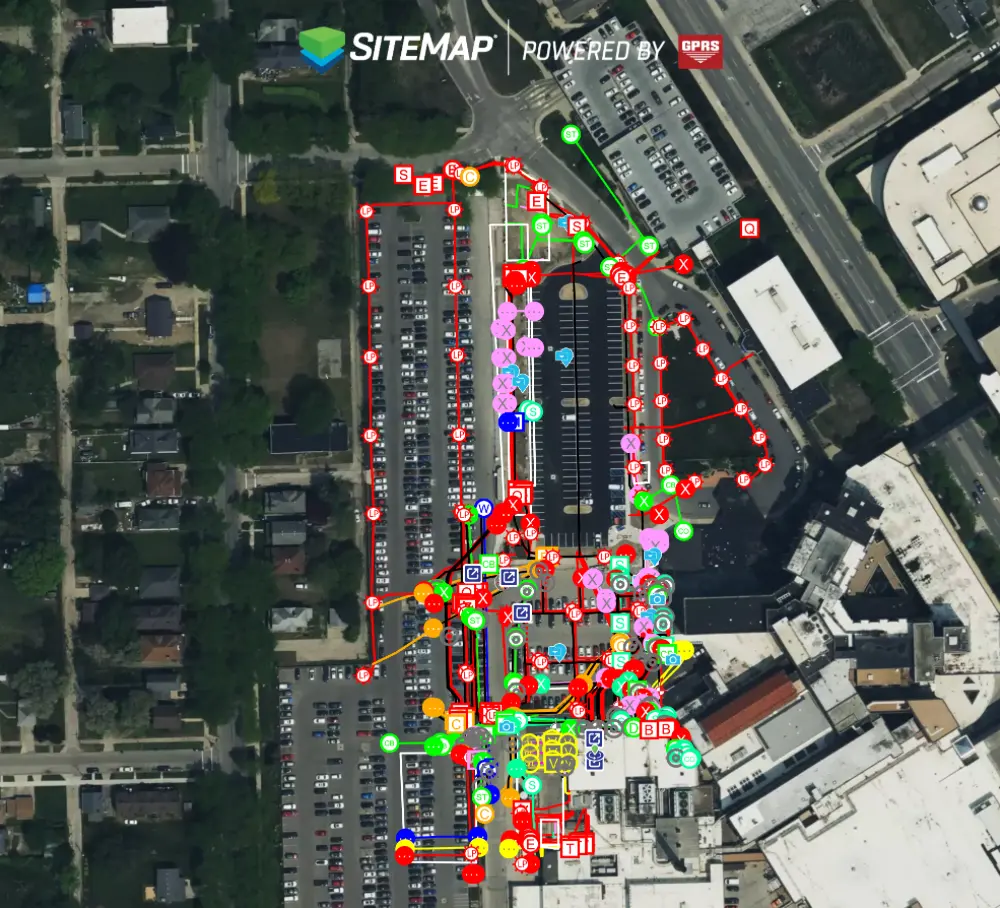
Case Study: SiteMap Helps Rudolph Libbe Control Data During Hospital Addition
Longtime GPRS safety partner Rudolph Libbe was the general contractor overseeing an expansion project at a historic hospital in Northwest Ohio. With parts of the medical center’s campus dating back to the mid-1800s, inaccurate as-built data and unknown subsurface obstructions could jeopardize construction planning.
It was essential that the proposed foundation and utility locations aligned with existing site conditions. Traditional exploration methods typically include “soft” excavation methods over the entire building footprint – which would have been expensive, time consuming, and required tremendous coordination between the various project stakeholders.
Rudolph Libbe also wanted 3D as-builts to plan and complete the building addition.
GPRS utilized ground penetrating radar (GPR) scanning and electromagnetic (EM) locating to map the hospital’s utilities, and remote-controlled sewer inspection crawlers and push-fed sewer scopes to map and inspect its wastewater infrastructure.
We also utilized 3D laser scanning to document as-built site data and utility maps to create 2D CAD drawings and a 3D BIM model for virtual design and construction.
All this data was available to the entire project team throughout the project lifecycle via SiteMap, ensuring seamless communication and collaboration.
As a result, Rudolph Libbe was able to precisely design and plan the building addition during preconstruction. The data provided by GPRS via SiteMap revealed clashes and deviations – including a long-forgotten, buried concrete slab right in the middle of the project area – before they could cause expensive rework.
"No one has gone to this extent to map a site above and below ground,” said GPRS Field Support Director, Jaime Althauser. “It was imperative that Rudolph Libbe had accurate as-built site data and utility maps with critical structural and utility tie-in information.”
From helping you manage your subcontractors, to helping you build a skyscraper, GPRS Intelligently Visualizes The Built World® to keep you on time, on budget, and safe.
What can we help you visualize?
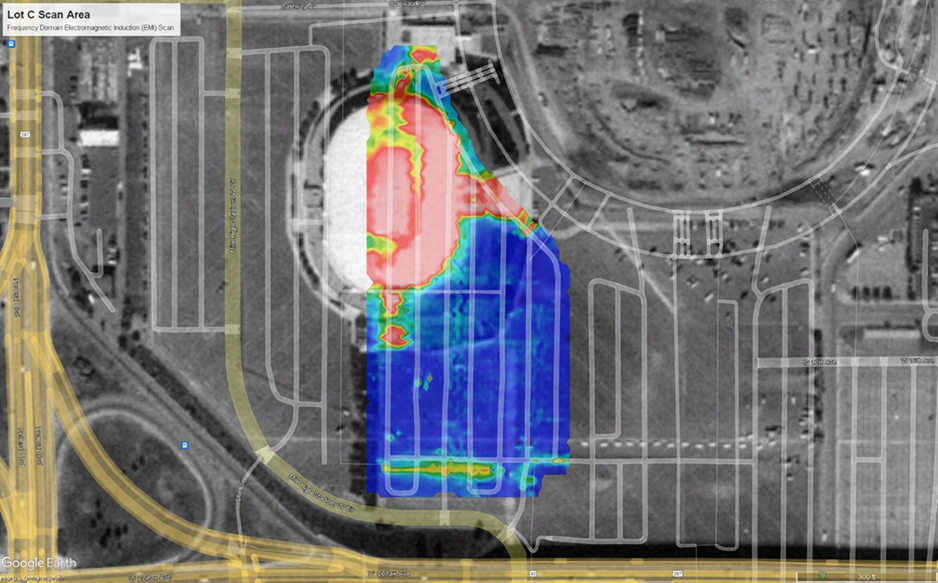
GPRS Helps Mile High Stadium Tackle Parking Lot Issue in Colorado
GPRS helped their client in Denver, Colorado tackle an issue that has been plaguing them for years. GPRS Project Manager Matthew Pudimott and Area Manager Ryan Shannon were tasked with scanning a seven-acre parking lot outside of Empower Field at Mile High, the home stadium of the Denver Broncos.
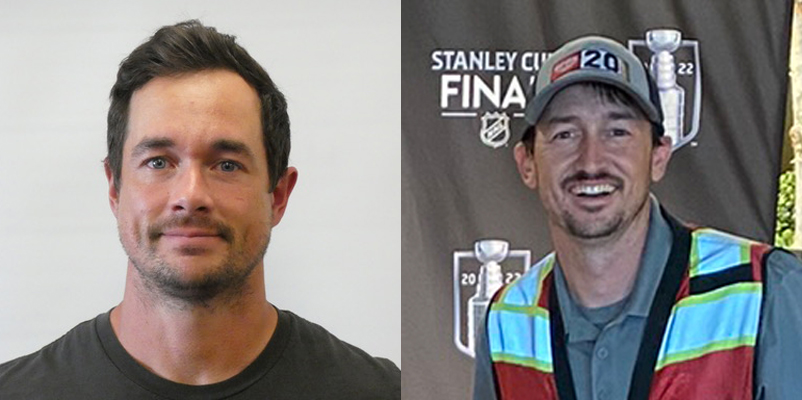
The pavement in the parking lot had been continuously cracking despite repeated attempts to repair it.
The parking lot was built where a former Denver arena once stood, McNichols Sports Arena was built in 1975. It held hundreds of concerts and was the home of the Denver Nuggets from its inaugural year until it officially closed in 1999. McNichols was also the home of the Colorado Avalanche for the final four years it was in operation. In January of 2000, it was demolished to make way for the construction of Empower Field at Mile High.
The initial purpose of the project was to search for underground tunnels or possible buried remains from the former arena. Pudimott and Shannon got to work and began scanning the area using ground penetrating radar (GPR).
The results were not as conclusive as they expected, so they implemented one of the main guidelines of Subsurface Investigation Methodology (SIM): the use of multiple complimentary technologies. They scanned the same area using electromagnetic (EM) locators and found what they were looking for.
“We initially were searching for voids, so we ran the GPR cart, took a whole day to get all the data together, and there was just no evidence of voids,” Pudimott explained. “We started to get worried that we actually weren't going to have meaningful results for the client, but the next day we ran EMI and that was kind of interesting. Same thing, collected the whole result, took a full day, and I was hoping we'd have something for him. And when the post processing data came back, I mean, it blew up.”
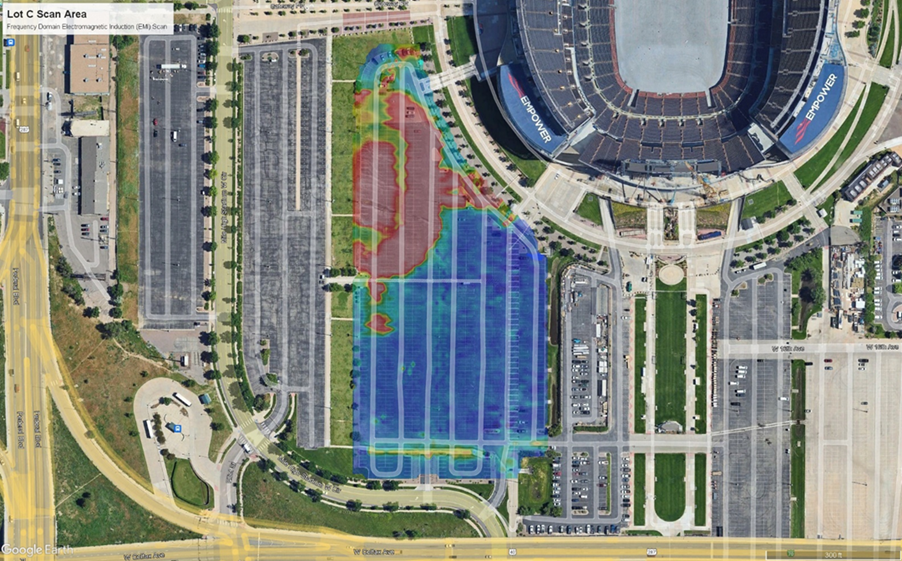
EM locators are used to detect electromagnetic signals radiating from metallic pipes and cables. Signals are created by the current flowing from the EM locator’s transmitter which travels along the conductive materials and back to the transmitter. Signals can be created and registered by the equipment when:
- The EM locator’s transmitter applies current to the pipe
- An electrical cable is live with current flow
- A conductive pipe acts as an antenna and re-radiates signals from stray electrical fields and communication transmissions
Once they saw the unusual results from the scan data, Shannon had an idea that allowed them to properly tell the data’s story.
“We definitely found a huge reaction and I knew that [McNichols] stadium was built there and that's probably the reason why we were scanning out there. So I just figured I would look at the old Google Earth data,” Shannon explained. “Sure enough, that popped up there, and then I thought to overlay that data over the historical data. It was most likely old foundations or possibly different backfill. The red, white, and orange reactions on the EMI typically indicate conductive reactions.”
Once Shannon overlayed aerial imagery from October of 1999, the EM data appeared to align with the footprint of the former arena.
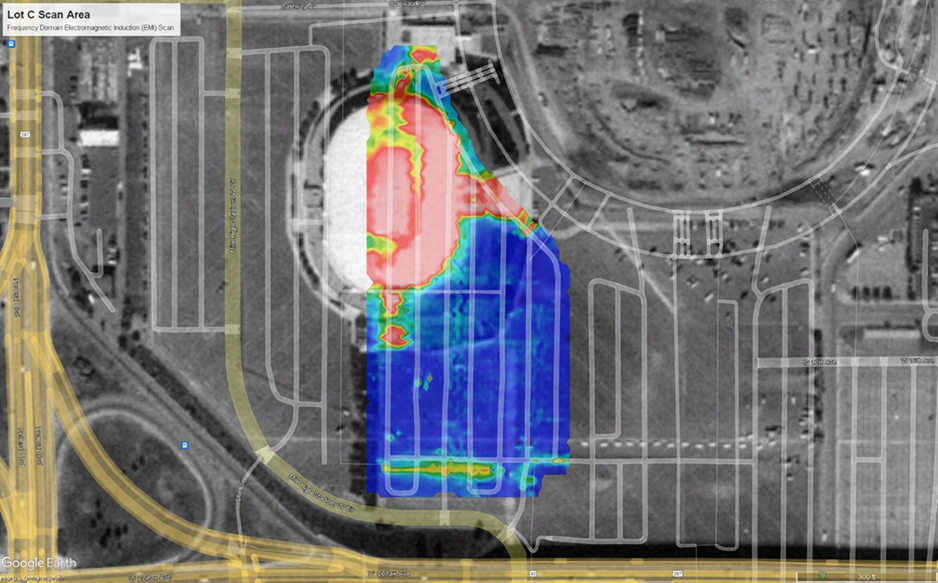
Despite being with GPRS for over a decade, Shannon couldn’t help but be amazed at the uniqueness of this job and the capabilities of utility locating equipment.
“This is definitely once-in-a-lifetime data, for sure,” Shannon said. “It’s not a common example, but a great example of what the EMI can do to get this data consistently. To find a building footprint like this? Yeah, I've never heard of this before or seen it before.”
With these results now at the client’s fingertips, they can make educated decisions on how to fix the parking lot without wasting more time and money on renovations year after year.
From stadiums to sewer lines, GPRS Intelligently Visualizes the Built World® to keep your projects on time, on budget, and safe.
What can we help you visualize?
FREQUENTLY ASKED QUESTIONS
What is Subsurface Investigation Methodology?
Subsurface Investigation Methodology (SIM) is a standard operating procedure and set of professional specifications that work as a guide for utility locating experts when scanning for buried utility lines. All GPRS Project Managers are required to achieve SIM 101 certification, which requires 80 hours of hands-on training in a classroom setting and 320 hours of mentorship in the field. For reference, the American Society for Nondestructive Testing’s (ASNT) minimum training recommendation includes eight hours for training and 60 hours practicing GPR to achieve NDT Level 1 certification in ground penetrating radar (GPR) scanning.
SIM requires the use of multiple, complementary technologies, like GPR scanning and electromagnetic (EM) locating, when locating buried utilities or scanning a concrete slab.
What are the Benefits of Underground Utility Mapping?
Having an updated and accurate map of your subsurface infrastructure reduces accidents, budget overruns, change orders, and project downtime caused by dangerous and costly subsurface damage.
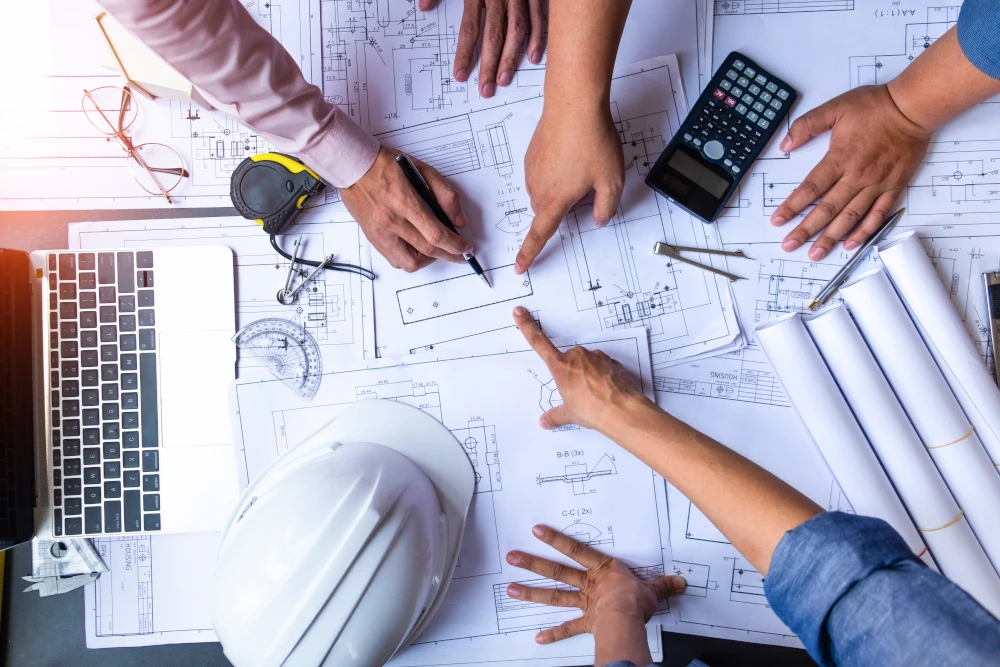
Survey of Construction Professionals Highlights the Need for Better Communications and Data Management
To better understand why and how construction technology decisions are made, Autodesk and FMI Corporation partnered to survey 600 construction professionals about how their teams spend time on the jobsite. The study revealed that the construction industry continues to suffer from outdated data and communication practices.
Autodesk provides software solutions for the architecture, engineering, and construction industries. FMI Corporation is a management consulting and investment firm focused exclusively on engineering, construction, infrastructure, and the built environment.
The data was compiled in an industry report titled Construction Disconnected. Key findings include:
1. Construction workers lose nearly two full working days each week resolving avoidable issues and searching for project information.
On average, each professional spends 14 hours weekly dealing with conflict, rework, and other tasks that detract from higher-priority activities. Respondents reported spending:
- Five and a half hours locating project data, such as revised drawings, material cut sheets, and other information relevant to the job.
- Nearly five hours resolving conflicts among stakeholders, including general contractors, owners, and subcontractors.
- Four hours managing rework, including identifying mistakes, assessing costs, and determining causes.
2. Nearly half of all rework stems from poor communication and inaccurate project data.
- Miscommunication and unreliable data account for 48% of all rework on U.S. construction sites.
- Respondents attributed 26% of rework to poor communication, citing unresponsiveness, ineffective collaboration, and the absence of a shared platform as the top causes.
- Another 22% was linked to poor project data, including incorrect information, limited access, and difficulty sharing updates across teams.
The article emphasizes that many contractors lack the tools needed to effectively manage every aspect of a construction project. Outdated communication and data collection methods fail to deliver centralized, real-time, and reliable information. This leads to inefficiencies, time-consuming tasks, and costly rework.
Reduce Rework and Improve Efficiency in Construction with GPRS and SiteMap
GPRS helps construction professionals overcome data and communication challenges by delivering accurate subsurface information, along with detailed above-ground architectural, structural, and MEP documentation.
All project data is centralized in SiteMap®, a GIS platform that integrates directly into project workflows to support informed decision-making and reduce costly surprises. SiteMap is the solution construction professionals need to centralize real-time site information and reduce rework.
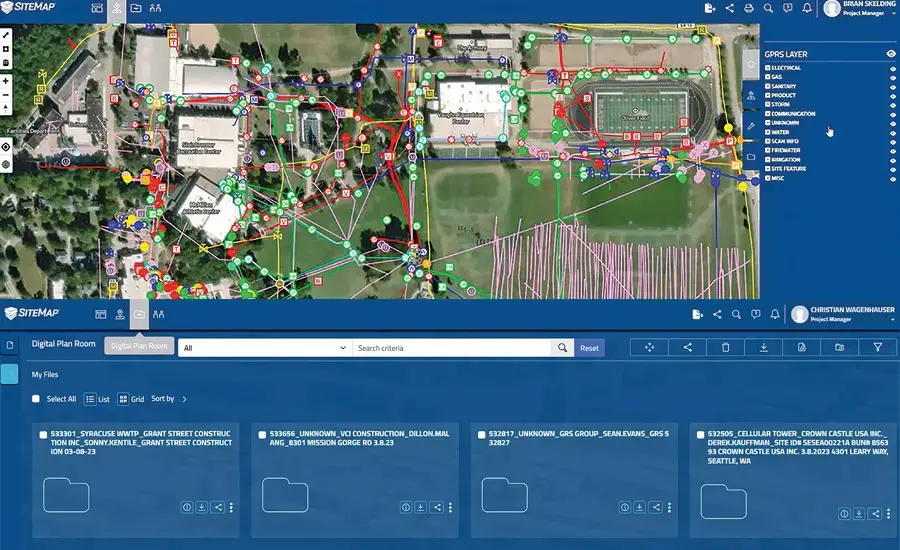
Suite of Aboveground and Below As-Built Solutions
GPRS provides a suite of services that include utility locating, concrete scanning, reality capture, video pipe inspection, and leak detection. These services are supported by advanced digital mapping and modeling solutions that help project teams mitigate risk, improve communication, and streamline construction across all phases.
Utility Locating Solutions
Fact: A utility strike occurs approximately every 90 seconds in the United States, resulting in thousands of injuries and deaths over the past 20 years. These strikes, often caused by inadequate utility locating before digging, cost communities millions of dollars annually according to a report from Michigan Technological University. In 2022 alone, over 163,000 utility strikes were reported according to the Common Ground Alliance.
Accurate utility locating is critical to preventing costly and dangerous utility strikes. GPRS uses ground-penetrating radar (GPR) and electromagnetic (EM) locators to identify underground utilities before construction or excavation. SIM-certified Project Managers mark the location and depth of both public and private utilities, including gas lines, electrical cables, telecommunication lines, sewer lines, and other buried infrastructure using standardized color codes and symbols.
GPRS utility locating provides verified field data, information that is critical during pre-construction planning and excavation. It ensures that crews avoid damaging existing utilities, which can lead to project delays, safety incidents, and regulatory fines.
SiteMap stores geolocated, layered, and securely shareable interactive utility maps, and PDF utility maps. Users can export utility data into drawings, maps, and models to enable seamless communication and collaboration across project teams.
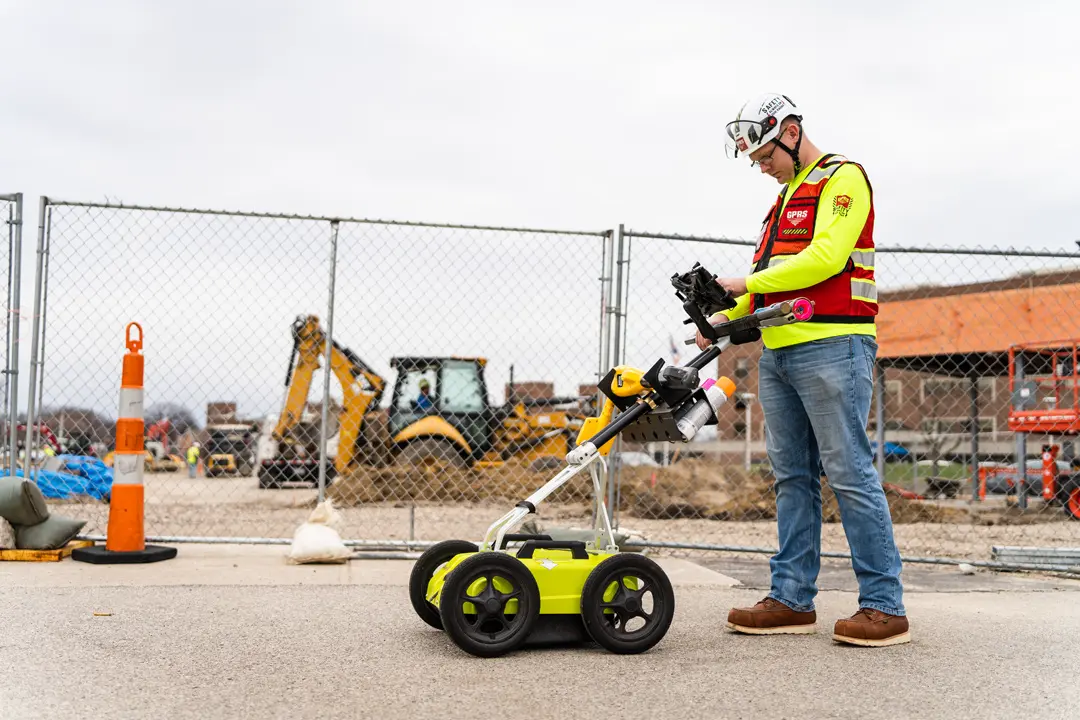
Concrete Scanning & Imaging Solutions
Fact: A single severed post-tension cable can cost upwards of $20,000 to repair/replace, and it can also lead to structural failure that endangers the lives of not only those completing the work, but anyone in the immediate area.
Before renovation, build-out, or excavation begins, existing concrete structures must be scanned to ensure safety and prevent damage. GPRS uses GPR to scan slabs, walls, and columns to detect embedded features such as rebar, post-tension cables, conduits, and potential voids. This concrete scanning service provides precise detection and mapping, helping teams avoid structural damage and maintain compliance with engineering standards.
SiteMap stores LiDAR-captured field markings, 2D CAD files, 3D models, and detailed analysis reports for easy access and integration.
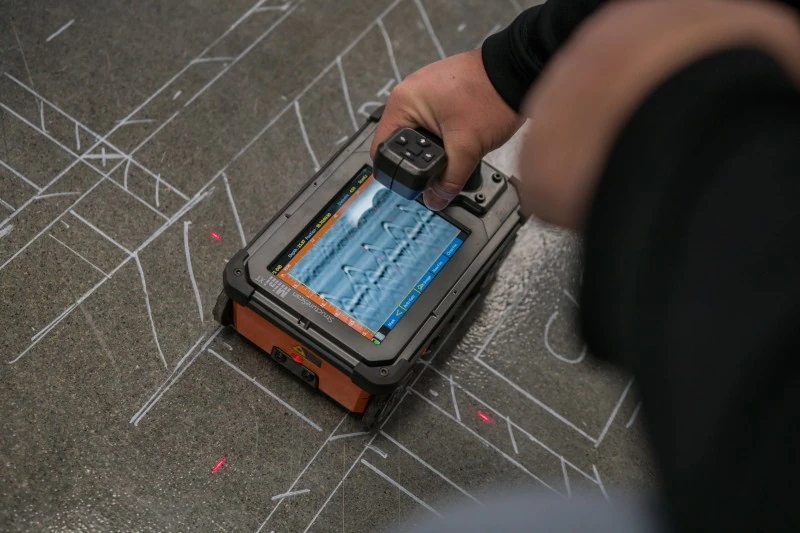
Reality Capture Solutions
Fact: A study from Dodge Data and Analytics, “Measuring the Impact of BIM on Complex Buildings,” found these results from AEC pros:
- 93% said BIM improved the quality and function of the final design
- 88% said BIM led to accelerated job completion
- 85% said BIM resulted in a reduction in the final construction cost
GPRS Reality Capture Services deliver precise as-built documentation of buildings and infrastructure using 3D laser scanning and photogrammetry. Deliverables include point clouds, 2D CAD drawings, 3D BIM models, mesh models, TruViews, and virtual tours that support accurate planning and construction.
Reality capture enhances collaboration by creating a digital twin of the physical site, accessible to all stakeholders. This shared access improves communication, supports better decision-making, and reduces errors. All reality capture data is uploaded to SiteMap, giving clients 24/7 access to verified documentation for planning, building, and facility management.
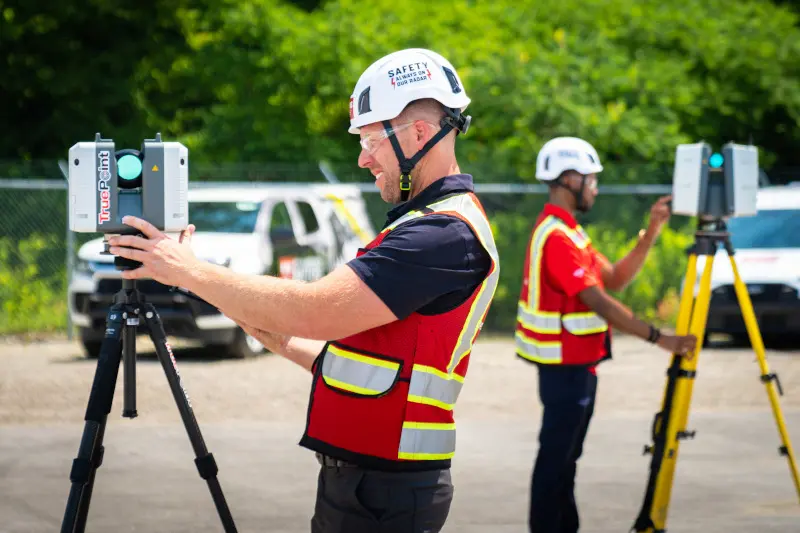
Video Pipe Inspection Solutions
Fact: Video pipe inspection can lead to substantial cost savings by identifying problems early, preventing them from escalating into expensive repairs. Some companies have reported a 90% reduction in maintenance costs after implementing video inspections according to 1st Choice Pro Services.
Most sewer pipe defects occur in buried infrastructure that cannot be inspected without excavation or specialized equipment. GPRS uses robotic crawlers and lateral launch CCTV cameras to inspect water and sewer systems. These video pipe inspections produce high-resolution video and defect mapping, documented in NASSCO-certified WinCan reports. Each defect is located, classified by severity, and integrated into a digital map.
SiteMap includes interactive sewer maps by segment, detailing entry and exit points, pipe condition, flow, length, material, images, and video. Hyperlinks to WinCan reports and footage allow clients to easily locate and assess sewer line conditions and defects.
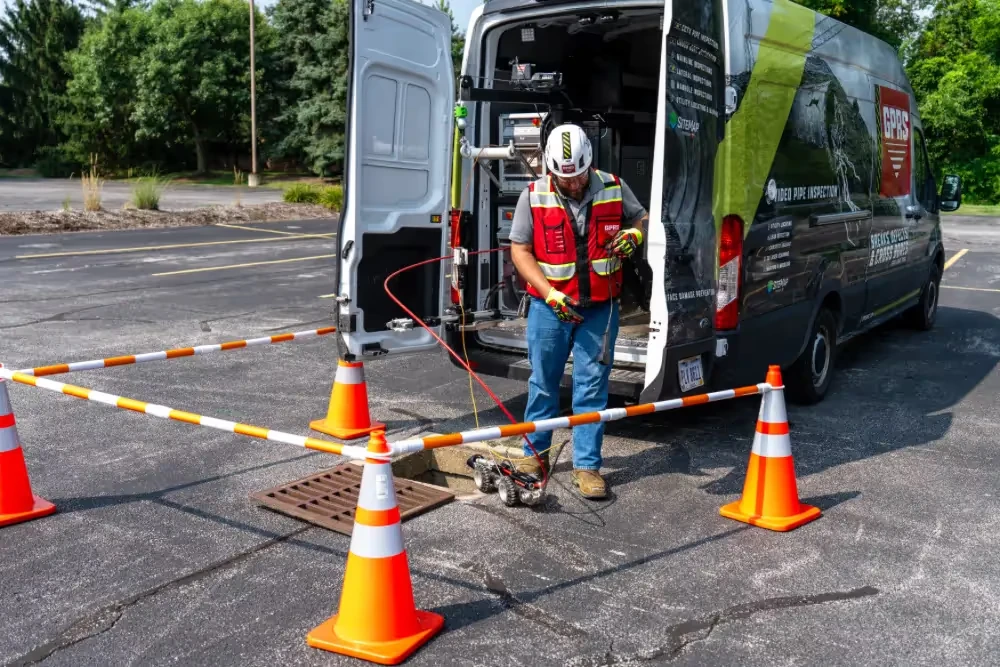
Leak Detection Solutions
Fact: According to the Report Card for America’s Infrastructure, 6 billion gallons of treated water are lost daily to untreated leaks. 2.5 trillion gallons of water are lost annually to pipe defects. That's enough to fill 3.75 million Olympic-sized swimming pools.
Undetected water leaks can cause extensive damage to structures and utilities. GPRS uses acoustic and tracer gas technologies to locate leaks in pressurized water systems without excavation. These methods allow technicians to pinpoint leak sources quickly and accurately.
GPRS leak detection services provides detailed reports and recommendations to help clients resolve issues efficiently and minimize disruption.
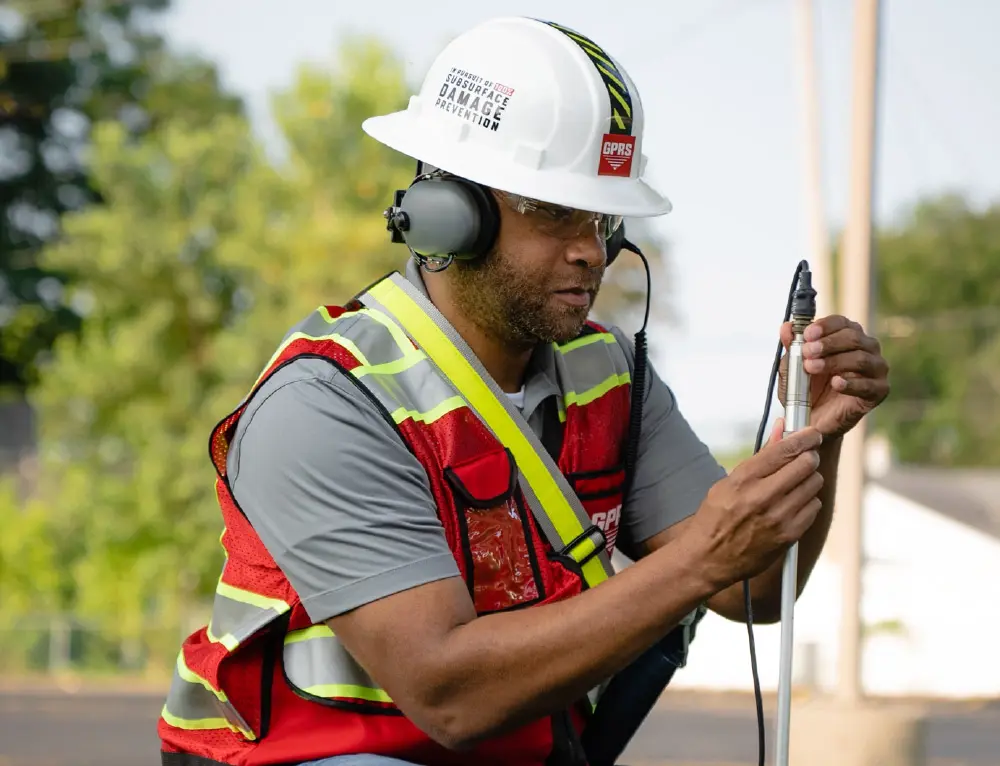
Data Management Solutions: GPRS SiteMap GIS Platform
To unify and deliver the data collected through its services, GPRS developed the SiteMap GIS platform. This cloud-based system stores and visualizes utility, concrete, structural, architectural, MEP system information and VPI reports in a centralized, interactive software. SiteMap allows users to access accurate site information from any device, at any time.
The platform supports project planning, risk management, and compliance documentation. It integrates with CAD and BIM software, enabling seamless data exchange between field and office. SiteMap also includes tools for annotation, measurement, and version control, ensuring that teams always work from the most current information.
By consolidating data into a single source of truth, SiteMap eliminates the confusion and inefficiencies caused by fragmented communication. It empowers project teams to collaborate more effectively, reduce rework, and deliver projects on time and within budget.
How can GPRS help you centralize site data and reduce rework?
Click here to schedule a SiteMap demonstration.
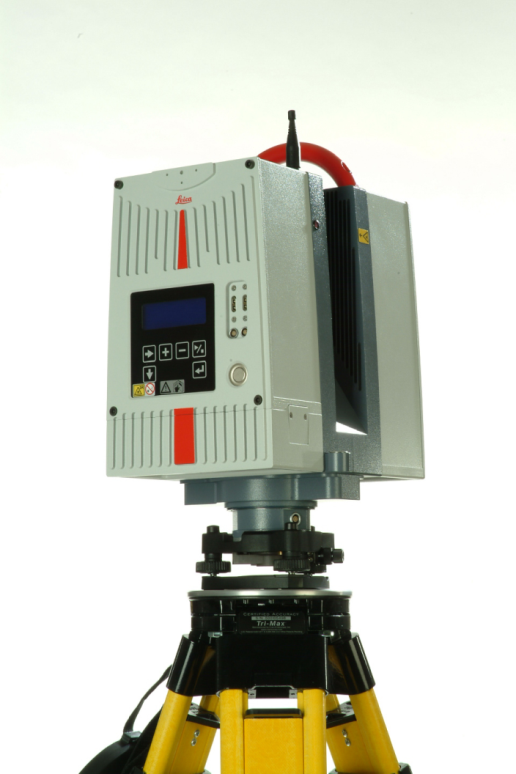
The History of 3D Laser Scanning Technology
From early LiDAR experiments to today’s precise BIM modeling, discover how 3D laser scanning evolved into a crucial element of architecture, engineering and construction
Before 3D laser scanning existed, building drawings were created through a meticulous and manual process that relied heavily on human skill, precision, and time. Surveyors and draftsmen would physically walk through a building or site, using tape measures and levels to manually record dimensions. Rough sketches were made on-site in field notebooks. Drawings were then created at standard architectural scales using graph paper and drafting tools. Once finalized, they were reproduced using blueprint machines. Physical copies were stored in archives and shared among architects, engineers, and contractors. Manual building measurements were often prone to human error, especially when dealing with irregular or hard-to-reach areas, and the process was typically slow and time-consuming.
The Early Days of 3D Laser Scanning
According to the "Timeline of 3D Laser Scanners | By Scantech International," in the 1960s, 3D laser scanning technology was in its infancy and primarily used for experimental purposes to explore how lasers could be applied to capture the profile of surfaces. These early systems used lights, projectors, and cameras to scan objects, but they were extremely slow and produced low accuracy results due to the limitations of the technology. The main goal during this period was to develop a method for automated spatial data collection.
The initial 3D laser scanners were large and bulky, often the size of a desk or small cabinet due to their heavy optical components, separate computing units, and manual setup requirements. These systems were typically mounted in fixed positions and used in labs or field stations, reflecting the technological limitations of the time. These scanners laid the groundwork for what would become a transformative technology.
By the 1980s, 3D laser scanners were still large, stationary, and in the early stages of development. They operated slowly, often taking minutes or hours to scan a single object, and produced low-resolution point clouds that lacked fine detail. While relatively accurate for their time, these systems were limited by computing power and sensor technology, requiring substantial post-processing on powerful workstations to make the data usable.
Military and Scientific Roots
Laser technology saw significant growth in the 1980s, particularly in military and scientific research. As detailed in Robert W. Seidel’s 1987 article "From Glow to Flow: A History of Military Laser Research and Development", scientists used early laser systems for measuring distances, terrain analysis, and geological surveys, to help understand landforms and surface features.
Laser scanners also played a role in space science, helping measure distances to celestial bodies and satellites. In the military, laser scanners were used for rangefinding, providing precise distance measurements for artillery, missile guidance, and battlefield awareness. They were also explored for laser-based radar systems used in aerospace and submarine warfare.
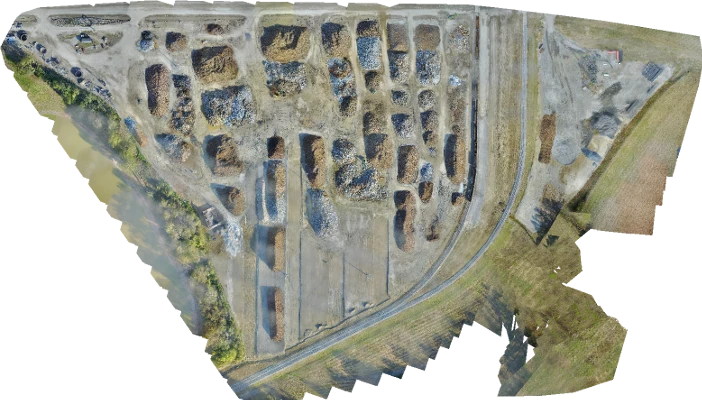
Cyra Technologies Introduces Cyrax
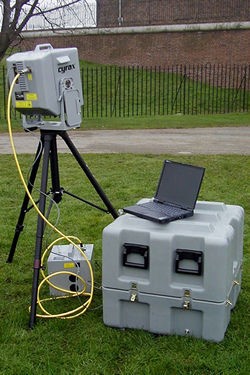
Geoffrey Jacobs wrote about how terrestrial laser scanning gained more traction in the 1990s in The Early Days of 3D Scanning.
Cyra Technologies was founded in 1993 by Ben Kacyra with the goal of developing a high-precision 3D laser scanner. The company introduced Cyrax, one of the first commercially available laser scanners specifically designed for surveying and engineering applications.
The Cyrax 3D laser scanner helped to address the "as-built documentation problem” in industrial plant retrofits. Traditional measurement methods were slow, prone to errors, and sometimes hazardous. Cyrax offered a faster, safer, and more accurate alternative.
The Cyrax system featured advanced components, including a microchip laser from MIT Lincoln Labs and nanosecond timing electronics from Los Alamos National Lab, with Cyra Technologies securing exclusive licenses for both.
Designed as a portable unit powered by a battery and a laptop, it weighed approximately 88 pounds. The scanner could capture data at 1,200 points per second within a 40° x 40° field of view and had a range of up to 50 meters against a flat white surface. Its success relied on precise time-of-flight measurements, requiring picosecond-level timing to detect laser reflections from nearby objects. These innovations gave Cyra a strong proprietary position in the emerging 3D laser scanning market.
Cyra Technologies faced a major hurdle when existing CAD software couldn’t handle the massive point cloud data from its scanner. With guidance from UC Berkeley’s Carlo Sequin, the company shifted to a computer graphics-based approach and developed its own software, Computer Graphics Perception (CGP), gaining a competitive edge as no similar solution existed at the time.
Chevron Field Testing the Cyrax
Chevron was among the early beta testers. The company used the Cyrax laser scanner in oil and gas fields in Kazakhstan. The purpose of this test was to evaluate how well the Cyrax system could capture detailed spatial data of industrial infrastructure.
The Cyrax scanner produced both camera images and point cloud data of vessels and other equipment in the field. This allowed for precise digital representations of the physical environment. The point cloud data helped Chevron create accurate as-built models of the site, which were essential for planning retrofits, maintenance, and safety assessments.
By using 3D laser scanning instead of manual measurements, Chevron reduced the need for personnel to enter potentially hazardous areas, improving safety, and speeding up data collection.
Leica Geosystems Acquired Cyra Technologies
In 2001, Cyra Technologies was acquired by Leica Geosystems, which rebranded the Cyrax as the HDS 2400. This marked the beginning of widespread adoption of 3D laser scanning in both industrial and civil engineering sectors.
Over the next decade, scanners became more compact, faster, and more accurate, with improved range and data quality. Leica introduced new 3D laser scanners like the HDS 2500 (2002) and HDS 3000 (2004), which increased scanning speed, accuracy, and field of view. By 2009, the Leica P20 could capture 1 million points per second, drastically reducing scan times.
Software platforms like Leica Cyclone and Autodesk ReCap also began to streamline point cloud processing and integration with CAD workflows, making reality capture technology more accessible to engineers, architects, and surveyors.
New Companies and Portable Scanners
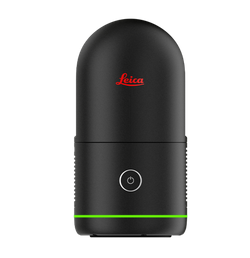
Other companies also played major roles in advancing the 3D laser scanning market. FARO Technologies introduced the FARO Focus series, which brought portability and ease of use to the forefront; Trimble entered the market with high-precision scanners tailored for construction and geospatial applications; and RIEGL developed high-performance LiDAR systems known for their speed and accuracy, especially in airborne and mobile mapping.
By the 2010s, the introduction of mobile mapping systems like the NavVis VLX and handheld scanners, such as the Leica BLK360 and FARO’s handheld Freestyle, made the technology more accessible and easier to use for a wider range of people and industries.
Released in 2018, the Leica RTC360, is capable of capturing up to 2 million points per second, with a range of up to 130 meters, and features VIS technology for automatic in-field scan registration and HDR imaging for detailed point clouds in under two minutes.
SLAM and the Next Generation of Scanning
The integration of SLAM technology enabled real-time mapping in complex environments such as construction sites and complex facilities.
SLAM (Simultaneous Localization and Mapping) is a method used to create a digital map of a space while simultaneously tracking the scanner’s position within it. In simple terms, localization determines where the scanner is, while mapping builds a layout of the environment. In 3D scanning, SLAM uses a LiDAR sensor to monitor the scanner’s movement and position as it moves through an area. This data allows the software to accurately place and align the scanned information, known as a point cloud, within the digital map.
Recent Advances in 3D Laser Scan Technology
From 2020 to 2025, 3D laser scanning technology has advanced rapidly, driven by innovations in hardware, software, and integration across industries. Scanners have become significantly smaller, faster, and more accurate, with many systems now offering real-time data capture and cloud-based workflows.
According to AVEVA’s March 2025 article “The Future of Reality Capture: What’s Next for Laser Scanning?”, the market size for laser scanning surpassed $3 billion in 2020 and is projected to reach $16.66 billion by 2030.
This growth is fueled by several trends. First, the technology is maturing, becoming more powerful, user-friendly, and affordable. Second, the need to modernize aging infrastructure, industrial plants, and other built environments is becoming increasingly urgent as many facilities face structural wear, outdated systems, and rising safety and efficiency demands.
3D laser scanning offers a powerful solution by capturing highly accurate, detailed digital representations of existing buildings and sites quickly and safely. These scans enable engineers and facility managers to create precise “as-built” models, streamline renovation planning, reduce downtime, and improve safety. As industries push toward modernization and sustainability, 3D laser scanning is becoming an essential tool for informed decision-making and long-term resilience.
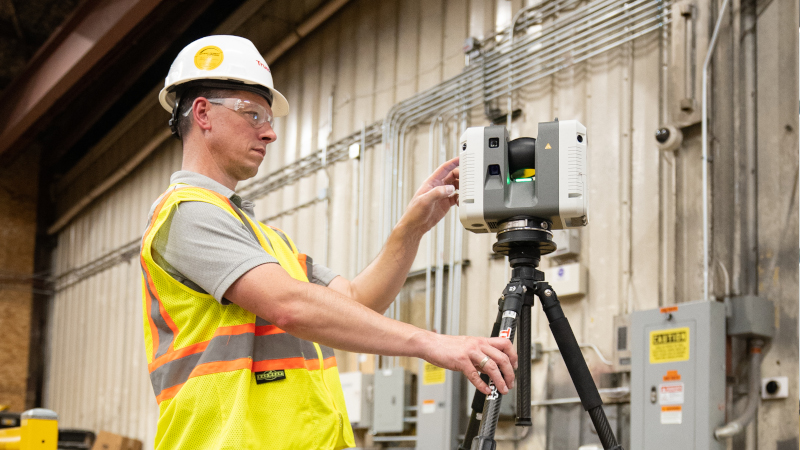
GPRS 3D Laser Scanning Services
GPRS is a leading 3D laser scanning company in the United States, helping clients to successfully complete their most complex architecture, engineering and construction projects. We've been providing reality capture services and excellent customer service for over 2 decades.
GPRS’ elite team of Project Managers efficiently 3D laser scans the exterior and interior of each site with professional-grade Leica laser scanners, capturing the exact layout, dimensions, and locations of your specific project requirements, such as architectural, structural, and MEP features, walls, windows, doors, stairs, roof, railings, exposed columns, beams, equipment, piping, ducts, and more.
Our Mapping & Modeling Team registers and processes the point cloud, removing noise and setting the coordinate system to provide the most precise measurements. Data is then compiled into custom 2D CAD drawings and 3D BIM models and delivered via SiteMap®. SiteMap® is GPRS’ secure GIS platform that delivers point cloud data, 2D CAD drawings and 3D BIM models, giving clients 24/7 access to verified as-built documentation to help them plan, build, and manage better.
What can we help you visualize?
Frequently Asked Questions
How has 3D laser scanning evolved in construction?
In the 1960s, 3D laser scanning technology was in its infancy and primarily used for experimental purposes to explore how lasers could be applied to capture the profile of surfaces. These early systems used lights, projectors, and cameras to scan objects, but they were extremely slow and produced low accuracy results due to the limitations of the technology. Laser technology saw significant growth in the 1980s, particularly in military and scientific research. By the 1990s, LiDAR (Light Detection and Ranging) and ground-based laser scanners became more available and began to integrate with CAD software for design, engineering, and the creation of 2D and 3D models. The first commercial scanners emerged in the early 1990s, improving accuracy and adoption in various industries, such as construction and manufacturing.
Why is 3D laser scanning important in modern construction?
It provides highly accurate, real-world data for design, renovation, and facility management, reducing errors, saving time, and improving coordination across trades through tools like BIM (Building Information Modeling).
What are the benefits of 3D laser scanning?
- Fast, Accurate Data Collection: A single laser scan captures millions of 3D data points per second, providing incredibly rich detail of a building or project site. Datasets are dimensionally accurate, measurable and shareable, expediting project planning and execution.
- Eliminates Revisits and Disruption: Sites are captured in high detail the first time, eliminating the need for return visits. High speed data collection expedites projects that require minimal disruption.
- Reduces Costs and Change Orders: Accurate design plans are produced from the start expediting field work and reducing change orders, delays and costs.
- Safe and Non-Contact: 3D laser scanners collect data on tripods from a distance in hard-to-reach or hazardous locations, keeping workers out of harm’s way. The non-intrusive nature keeps historic sites and artifacts untouched.
- Improves Communication: Communication is improved, teams can discuss plans while each has access to the same information, creating a more dynamic working environment.
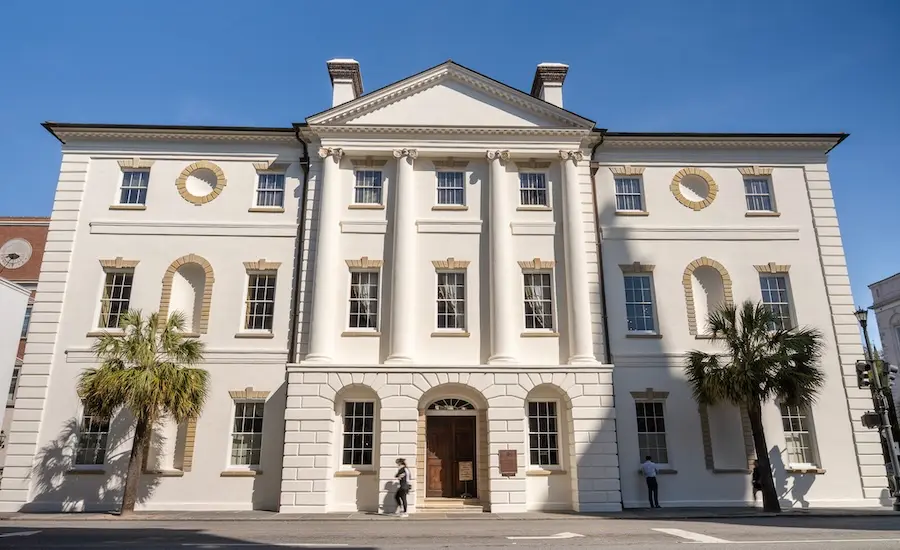
Charleston County Courthouse Undergoes $2.5M Restoration
One of Charleston, South Carolina’s famed “Four Corners of Law” was recently restored to its former glory.
The nearly 275-year-old Charleston County Courthouse underwent extensive stucco repair, waterproofing and masonry work as part of a roughly $2.5-million restoration that took 13 months and was completed in February. According to an article in Engineering News-Record, Greensboro, N.C.-based restoration contractor WxTite oversaw the work and even sourced period brick from a nearby project via Facebook Marketplace.
Constructed in 1753 at the intersection of Broad and Meeting Streets, the courthouse joins the other three buildings located at the intersection and representing the “Four Corners of Law”: municipal, county, federal, and ecclesiastical (church law).
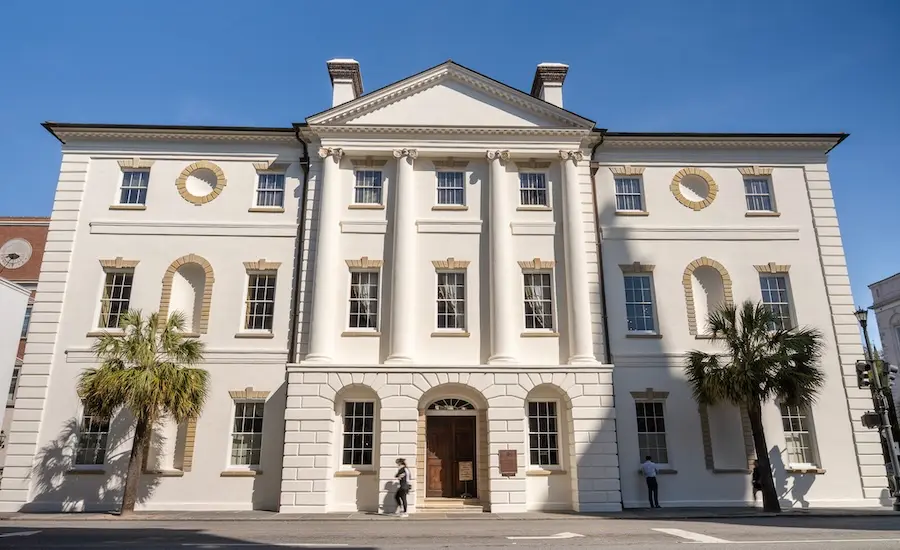
The other three “Corners” are Charleston City Hall, the U.S. Post Office and Courthouse, and St. Michael’s Episcopal Church. According to the Library of Congress, the nickname for the four buildings is believed to have been coined by Robert Ripley, the name and brains behind the Believe It or Not! franchise.
The county courthouse was originally used as a statehouse for the British Royal government for the South Carolina colony. It was partially destroyed in a fire in 1788, but was reconstructed with a third-floor addition and update in 1792.
The courthouse underwent numerous other changes and additions over the decades, before being restored to its historical 1792 Neoclassical appearance in 2001. It currently houses the Charleston County Probate Court.
When WxTite began its work, the courthouse was suffering from extensive stucco delamination, water intrusion, and other issues associated with its advanced age.
“Part of the process of figuring out how to restore this building, it was trying to figure out what has been done in the past,” WxTite Regional Manager Jamie Donaldson said in a video the company released about the restoration project. “That was a big part of our project was trying to figure out what was done, why they did it, how they did it, what they messed up during the process of the original renovation. Because the reason we’re here is because it wasn’t done perfectly, and our goal is to do this renovation perfectly.”
To address the water intrusion, the project team removed bluestone pavers around the building to install subgrade waterproofing installation. The pavers were then returned to their exact previous locations.
700 s.f. of stone surfaces were carefully repaired and cleaned to bring the exterior of the courthouse back to life. And all 83 of the building’s fenestrations – windows, doors and other openings – were restored to preserve the architectural uniqueness of the structure.
To help protect the courthouse from Mother Nature, 3,000 new hurricane anchors were installed.
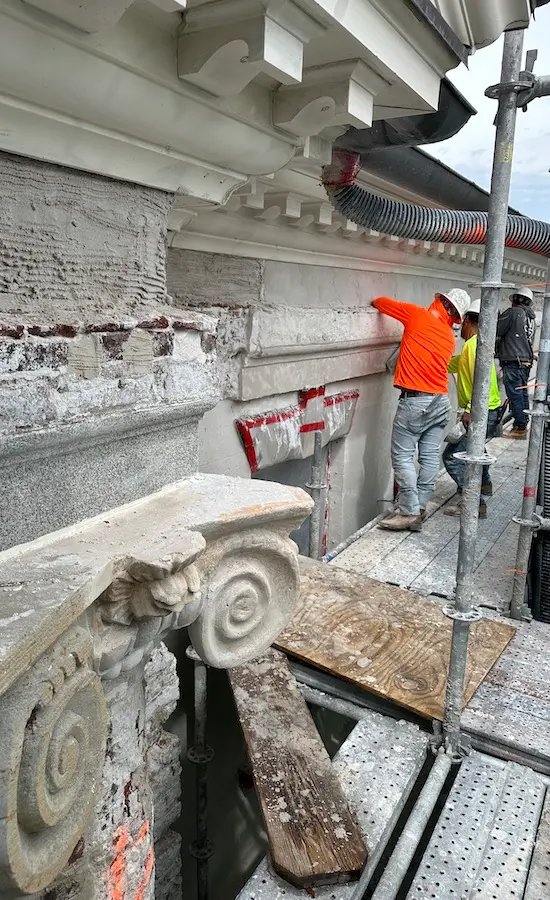
“We had a lot of assumptions about what needed to be done,” said WxTite Superintendent Cole Anderson. “But until we really started with the demolition portion of the stucco, we didn’t know how intense the brick repair was going to need to be. It was a lot of kind of opening things up to find out what depth of repair would be needed.”
Donaldson told ENR that the restoration project presented different challenges throughout the project lifecycle – but safety remained of paramount concern from the first day to the final day on-site.
“It’s a famous, busy intersection, arguably one of the busiest intersections in Charleston,” he explained. “Keeping everybody safe was paramount with what we were having to do out there, and still allowing the courthouse to be open and operational during the whole construction.”
At GPRS, safety is always on our radar. We’re committed to helping you ensure the safety of every project you undertake. Whether you’re restoring a historic structure, building a new facility, or managing the buried infrastructure on a site, we’re with you every step of the way – providing solutions to your problems from initial planning to O&M with our subsurface damage prevention, existing conditions documentation, and construction & facilities project management services.
GPRS Intelligently Visualizes The Built World® to keep your projects on time, on budget, and safe.
What can we help you visualize?
Frequently Asked Questions
Does GPRS Perform S.U.E. Work?
No, we do not. We use SUE Level 2-equivalent methodology and equipment to locate underground utilities with an accuracy rate of 99.8%. While we don’t conduct SUE work ourselves, our services allow a SUE Level 1 investigation to be performed more efficiently, eliminating the need to waste thousands of dollars on exploratory potholing.
What Type of Informational Output is Provided When GPRS Locates Utilities for Me?
Our Project Managers flag and paint our findings directly on the surface. This method of communication is the most accurate form of marking when excavation is expected to commence within a few days of service.
GPRS also uses a global positioning system (GPS) to collect data points of findings. We use this data to generate a plan, KMZ file, satellite overlay, or CAD file to permanently preserve results for future use.
GPRS does not provide land surveying services. If you need land surveying services, please contact a professional land surveyor.
Please contact us to discuss the pricing and marking options your project may require.
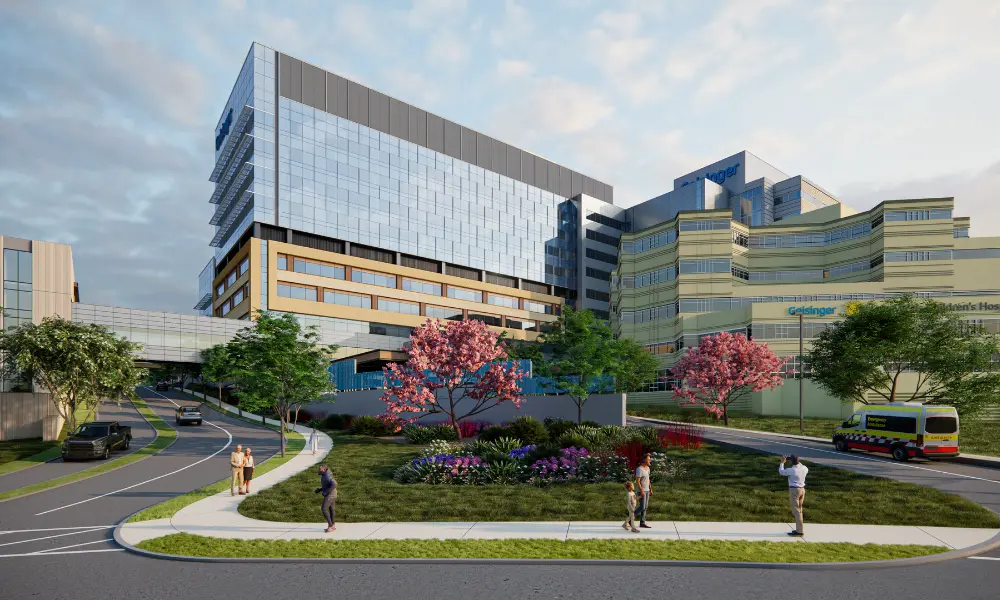
Pennsylvania Medical Center Expansion Highlights Ongoing Industry Trends
Architect EwingCole and general contractor Whiting-Turner are designing and building the $880 million expansion of Geisinger Medical Center in Danville, Pennsylvania.
The Philadelphia-based architect and Baltimore-based GC are working to modernize the hospital campus and the emergency department as part of the most significant expansion in the medical center’s nearly 110-year history, according to a press release issued by EwingCole.
The project includes an 11-story tower with an associated parking deck and renovation to the existing main entrance and drop-off sequence. The tower will feature 192 patient rooms to transition to campus to 100% private rooms on the hospital’s adult medical-surgical units; an expanded emergency department that will double the current space’s square footage; and a new, state-of-the-art operating suite.
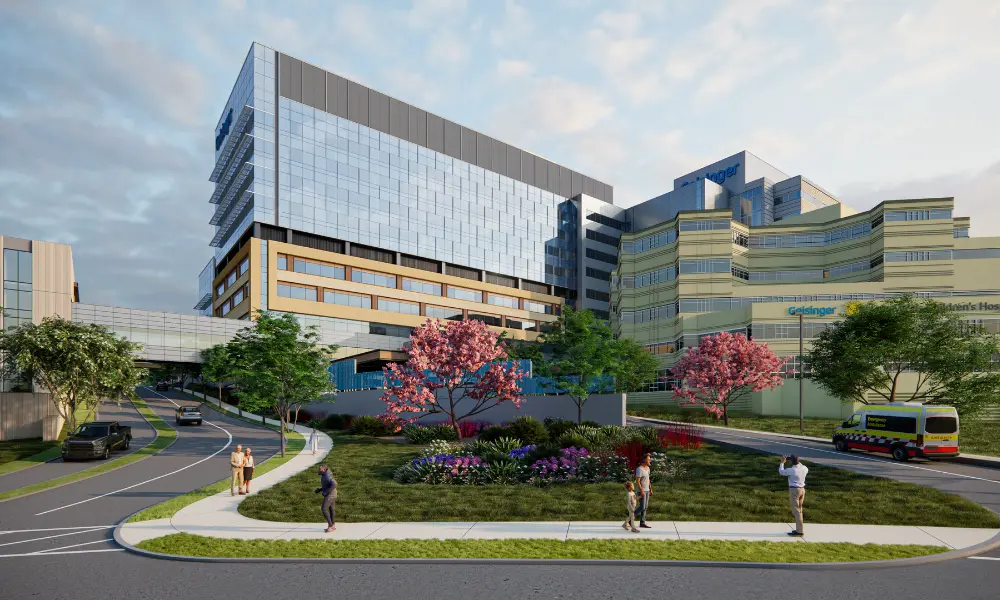
Construction began in May and is expected to be complete and open to patients by 2029, according to reporting by Construction Dive. The medical center’s old Dickey Clinic was demolished earlier in the year to make room for the new tower.
“Our community has depended on Geisinger for world-class health care for more than a century,” Terry Gilliland, M.D., president and CEO of Geisinger said in a press release issued by the healthcare consortium. “We’re continuing that legacy today as we announce the largest expansion project in the nearly 110-year history of Geisinger Medical Center. This project will truly transform care. It’s proof of our commitment to making better health easier for our communities today and into the future.”
The expansion project is part of a larger regional investment initiative Geisinger is currently undertaking. Geisinger Behavioral Health Center Danville, a 96-bed inpatient facility in Mahoning Township, is expected to open this summer, and an expansion similar to the Medical Center project is currently underway at Geisinger Wyoming Valley Medical Center near Wilkes-Barre.
“This project will completely reimagine the Geisinger Medical Center campus to strengthen collaboration among our staff and units for better patient care,” said Megan Brosious, chief administrative officer for Geisinger’s central region. “Our patients will have a modern care environment where they can continue receiving expert care right here in Danville, as they’ve come to expect from us over the past century. And our teams will have the space they need to provide that care.”
Trends in Healthcare Builds
Earlier this month, Construction Dive reported on how healthcare was one of the industries driving growth in construction planning amid struggles in other sectors.
Healthcare-related planning continued to accelerate in June along with warehouse activity and data center planning, according to data from the Dodge Construction Network’s Dodge Momentum Index, which tracks nonresidential projects entering the planning stage.
The $340 million Cleveland Clinic Avon campus expansion in Avon, Ohio was the largest institutional project to enter the planning stage in June, with the next largest project in that category – the McKinney Amphitheatre Building in McKinney, Texas – valued at less than half that at $150 million.
Nick Kaminski, Vice President of Healthcare Construction for Minneapolis-based construction firm, Ryan Cos., told Construction Dive that healthcare systems are continuing to develop and implement strategic growth plans despite the current economic uncertainties that have led other sectors to pause construction planning efforts. Oncology, cardiovascular, and orthopedic care are areas of focus within many of these growth plans, Kaminski said.
“…As part of this effort, many are prioritizing specialty assets like ambulatory surgery centers and freestanding emergency departments as key elements of their broader ambulatory expansion strategies,” he added. “These facility types are attracting targeted investments in both new construction and campus expansions nationwide…”
GPRS supports construction projects across industries, from hospitals to stadiums and beyond. Our subsurface damage prevention, existing conditions documentation, and construction & facilities project management services are designed to help you plan, manage, and build better. Utilizing state-of-the-art technologies such as ground penetrating radar (GPR), electromagnetic (EM) locating, Building Information Modeling (BIM), and more, we Intelligently Visualize The Built World® to keep you on time, on budget, and safe.
What can we help you visualize?
Frequently Asked Questions
What type of informational output is provided when I hire GPRS to conduct a utility locate?
Our Project Managers flag and paint our findings directly on the surface. This method of communication is the most accurate form of marking when excavation is expected to commence within a few days of service.
GPRS also uses a global positioning system (GPS) to collect data points of findings. We use this data to generate a plan, KMZ file, satellite overlay, or CAD file to permanently preserve results for future use. GPRS does not provide land surveying services. If you need land surveying services, please contact a professional land surveyor. Please contact us to discuss the pricing and marking options your project may require.
Can you find PVC piping and other non-conductive utilities?
GPR scanning is exceptionally effective at locating all types of subsurface materials. There are times when PVC pipes do not provide an adequate signal to ground penetrating radar equipment and can’t be properly located by traditional methods. However, GPRS Project Managers are expertly trained in multiple methods of utility locating.
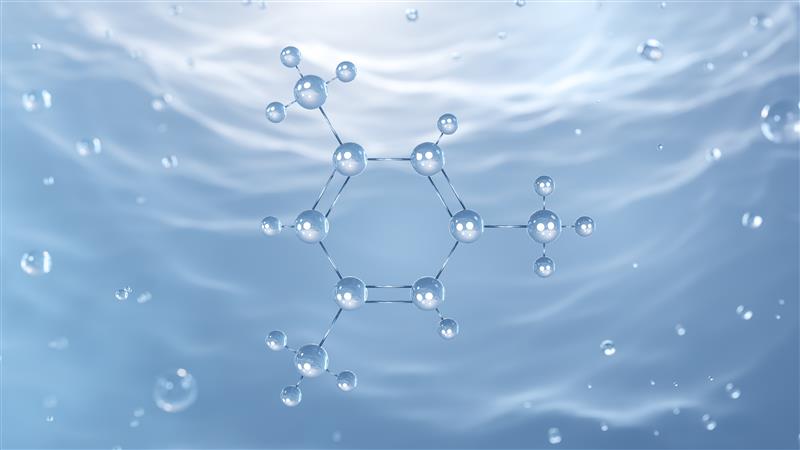
Volatile Organic Compounds Explained
Volatile Organic Compounds, commonly referred to as VOCs, are a broad group of carbon-based chemicals that easily evaporate at room temperature.
Found in a wide range of products and industrial processes, VOCs are a significant focus in environmental science, public health, and regulatory policy due to their potential impacts on air quality and human health.
Despite their ubiquity, VOCs are often misunderstood.
What Are VOCs?
VOCs are organic chemicals that have a high vapor pressure at ordinary room temperature.
This means they can readily transition from a liquid or solid state into a gas, releasing molecules into the air. The term "organic" in this context refers to the presence of carbon atoms in their molecular structure, often bonded with hydrogen, oxygen, nitrogen, or other elements.
The volatility of these compounds is what makes them particularly concerning. Once airborne, VOCs can contribute to indoor and outdoor air pollution, react with other atmospheric compounds, and in some cases, pose direct health risks to humans. These risks, along with the related regulatory requirements and associated operational cost, make VOCs a primary concern of facilities managers.
Common Sources of VOCs
VOCs are emitted from both natural and anthropogenic (human-made) sources. Naturally, they can be released by vegetation, wildfires, and microbial activity in soils. Most of the concern around VOCs, however, stems from human-related sources including:
- Consumer products: Paints, varnishes, cleaning agents, air fresheners, cosmetics, and adhesives often contain VOCs that are released during use and storage
- Industrial processes: Manufacturing, petrochemical refining, and solvent use are major industrial contributors
- Combustion: Vehicle exhaust, tobacco smoke, and burning of fossil fuels release a variety of VOCs into the atmosphere
- Building materials: New carpets, flooring, composite wood products, and insulation materials can off-gas VOCs over time, especially in poorly ventilated indoor environments
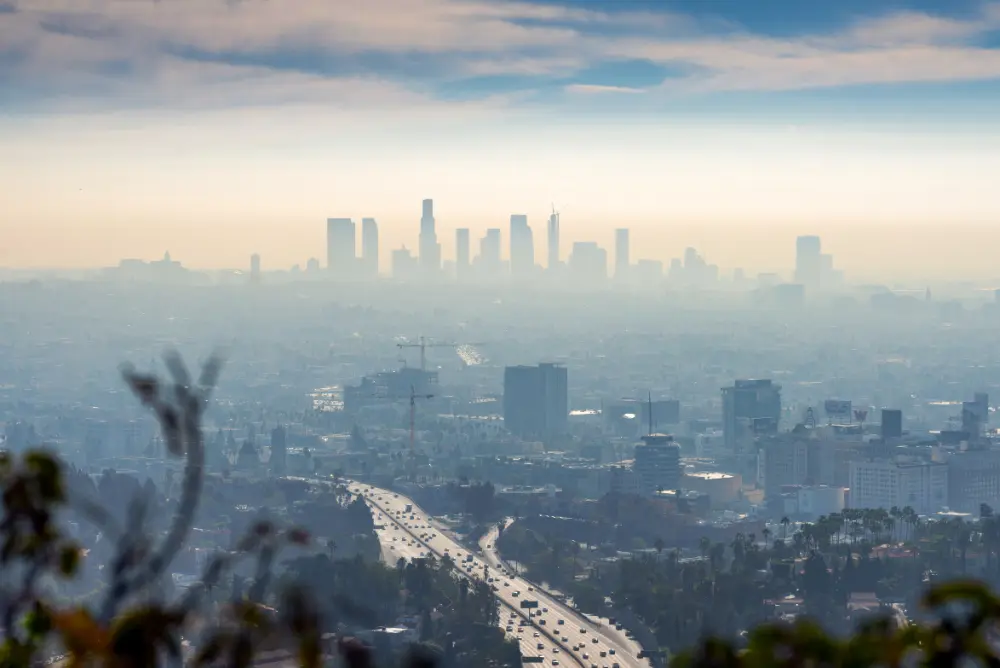
VOCs in Indoor vs. Outdoor Air
While outdoor VOC emissions are a major environmental concern, indoor air quality is often more directly affected by VOCs. In fact, concentrations of VOCs indoors can be up to ten times higher than outdoors, particularly in spaces with limited ventilation.
Indoor VOCs are primarily released from household products and building materials. Because people spend a significant portion of their time indoors – at home, work, or school – exposure to indoor VOCs is a key public health issue.
Health Impacts of VOC Exposure
The health effects of VOCs vary widely depending on the specific compound, concentration, duration of exposure, and individual susceptibility. Some VOCs are relatively harmless at low levels, while others are known to be toxic or carcinogenic.
Short-term exposure to elevated levels of VOCs can cause:
- Eye, nose, and throat irritation
- Headaches and dizziness
- Nausea and vomiting
- Worsening of asthma symptoms
Long-term exposure, particularly to certain VOCs like benzene, formaldehyde, and perchloroethylene, has been linked to more serious health outcomes, including:
- Liver and kidney damage
- Central nervous system effects
- Increased risk of cancer
Children, the elderly, and individuals with preexisting health conditions are generally more vulnerable to the effects of VOCs.
Environmental Impacts
Beyond human health, VOCs play a significant role in atmospheric chemistry. When released into the air, VOCs can react with nitrogen oxides (NOₓ) in the presence of sunlight to form ground-level ozone, a major component of smog. This photochemical reaction is a key driver of urban air pollution and can have detrimental effects on respiratory health, ecosystems, and agricultural productivity.
Some VOCs also contribute to the formation of secondary organic aerosols (SOAs), which are fine particulate matter that can penetrate deep into the lungs and exacerbate cardiovascular and respiratory diseases.
Regulation and Standards
Given their potential risks, VOCs are subject to regulation in many countries. In the United States, the Environmental Protection Agency (EPA) regulates VOC emissions through the Clean Air Act, particularly in relation to ozone formation. The EPA also sets limits for VOC content in consumer products and industrial processes.
The Occupational Safety and Health Administration (OSHA) provides workplace exposure limits for specific VOCs, while the Food and Drug Administration (FDA) and Consumer Product Safety Commission (CPSC) oversee VOCs in consumer goods.
Strategies for Reducing VOC Exposure
Minimizing exposure to VOCs involves a combination of product choices, ventilation, and awareness. Some practical steps include:
- Choosing low-VOC or VOC-free products: Many paints, adhesives, and cleaning supplies are now available in formulations that emit fewer VOCs
- Improving ventilation: Ensuring adequate airflow, especially during and after activities like painting or cleaning, can help disperse VOCs
- Proper storage: Keeping VOC-containing products sealed and stored in well-ventilated areas reduces emissions
- Avoiding unnecessary use: Limiting the use of air fresheners, aerosol sprays, and other VOC-heavy products can significantly reduce indoor concentrations
For workplaces and industrial settings, engineering controls such as fume hoods, air scrubbers, and personal protective equipment (PPE) are essential for managing VOC exposure.
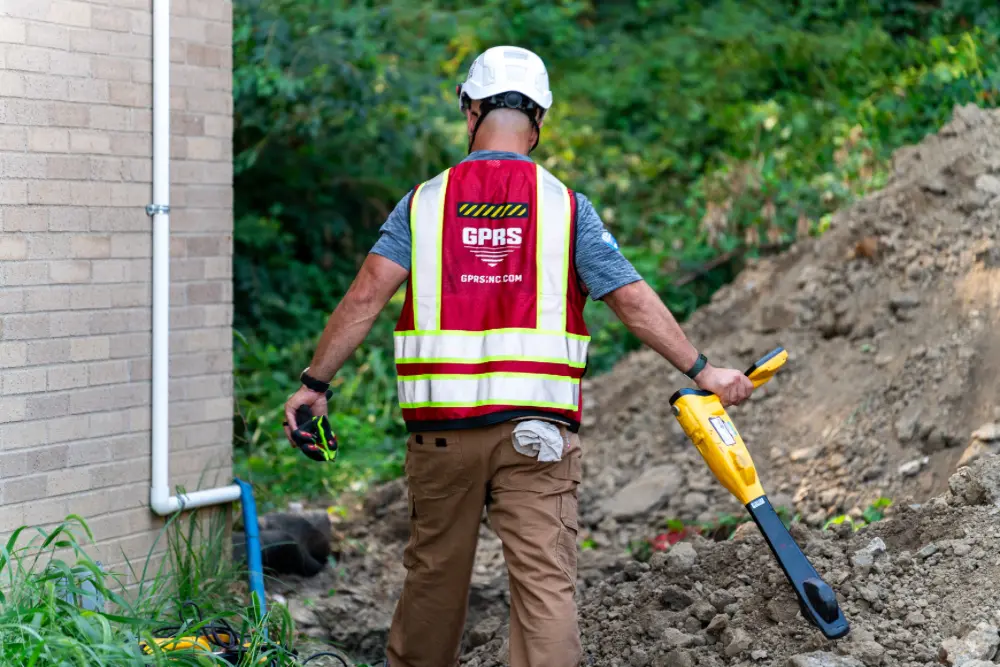
The Future of VOC Management
As awareness of VOC-related risks grows, so does the demand for safer alternatives and better monitoring technologies. Advances in sensor technology are making it easier to detect and quantify VOCs in real time, both in industrial settings and in consumer-grade air quality monitors.
Research is also ongoing into the development of sustainable materials and green chemistry approaches that reduce or eliminate the need for VOC-emitting substances altogether.
GPRS is the trusted leader for damage prevention in the environmental sector. Our project managers deliver results from the beginning of the initial investigation, throughout delineation and remediation, until project completion. With our nationwide network of Project Managers, we are equipped to mobilize to projects across the United States.
From sewer lines to skyscrapers, GPRS Intelligently Visualizes The Built World® to keep your projects on time, on budget, and safe.
What can we help you visualize?
FREQUENTLY ASKED QUESTIONS
What do I get when I hire GPRS to conduct a utility locate?
Our Project Managers flag and paint our findings directly on the surface. This method of communication is the most accurate form of marking when excavation is expected to commence within a few days of service.
GPRS also uses a global positioning system (GPS) to collect data points of findings. We use this data to generate a plan, KMZ file, satellite overlay, or CAD file to permanently preserve results for future use. GPRS does not provide land surveying services. If you need land surveying services, please contact a professional land surveyor.
Please contact us to discuss the pricing and marking options your project may require.
Can GPRS Project Managers distinguish between different underground utilities that they locate?
In most situations, we can identify the utility in question without any problems, although it is not always possible to determine what type of utility is present. When this happens, we attempt to trace the utility to a valve, meter, control box, or other signifying markers to determine the type of utility buried.