Voids in the concrete floor of a food processing plant provided an avenue for pests to enter the facility.
GPRS was called in to help locate these defects so they could be repaired quickly and efficiently.
Project Manager Jesse Halverson and Area Manager Shaun Ashley deployed ground penetrating radar (GPR) scanners at the plant, where the slab-on-grade floor was cracking around where it joined with columns that support the facility’s roof.
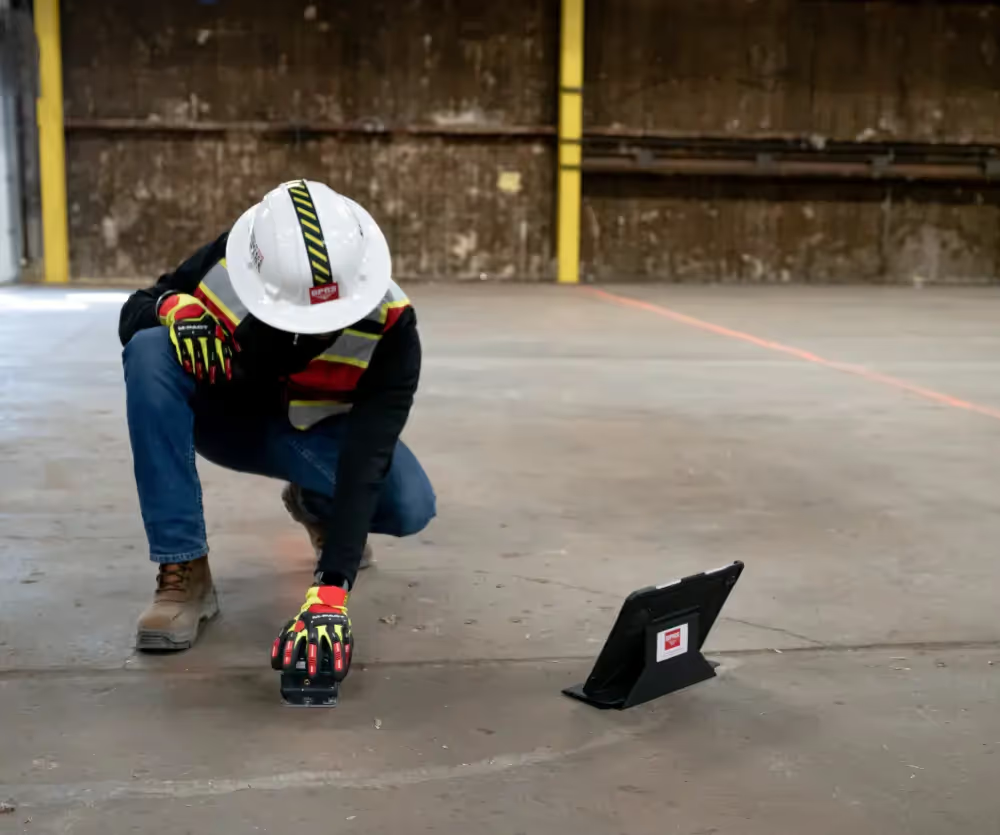
GPR is GPRS’ primary tool for locating areas where voids could be present in concrete slabs. It is a non-destructive imaging technology that utilizes radio waves to visualize the infrastructure within concrete or underground. A GPR unit emits radio waves into the surface being explored, and then detects the interactions between those waves and any subsurface material to create a readout of hyperbolas. These hyperbolas vary in size and shape depending on what type of material has been detected.
A properly trained utility locating/concrete scanning professional can interpret these findings to determine where objects are located underground or within concrete, so they can be avoided while excavating. Additionally, GPR can identify the area where a void could be located and the boundaries of that suspect area.
It’s important to note that GPR cannot measure a void’s depth or determine with 100% certainty that there is a void present in a specific location. However, when deployed by GPRS’ SIM-certified Project Managers, this technology can help you eliminate costly and destructive exploratory excavation – also known as potholing – when you suspect you have a void problem and need to know where to dig to verify the presence of a void and conduct repairs.
Halverson and Ashley identified close to 30 locations within the food processing plant where voids were likely present.
“There were a lot of [potential] voids around the columns,” Halverson said. “…There was a lot of cracking in the floor, and they weren’t huge voids, but there was a lot of them.”
Halverson and Ashley verified their findings by deploying both a concrete scanning and utility locating GPR antenna.
The concrete scanning antenna is handheld and wirelessly connects to a tablet to display findings in real time. The device’s small size and wireless functionality means it can investigate otherwise hard-to-reach sections of a concrete slab.
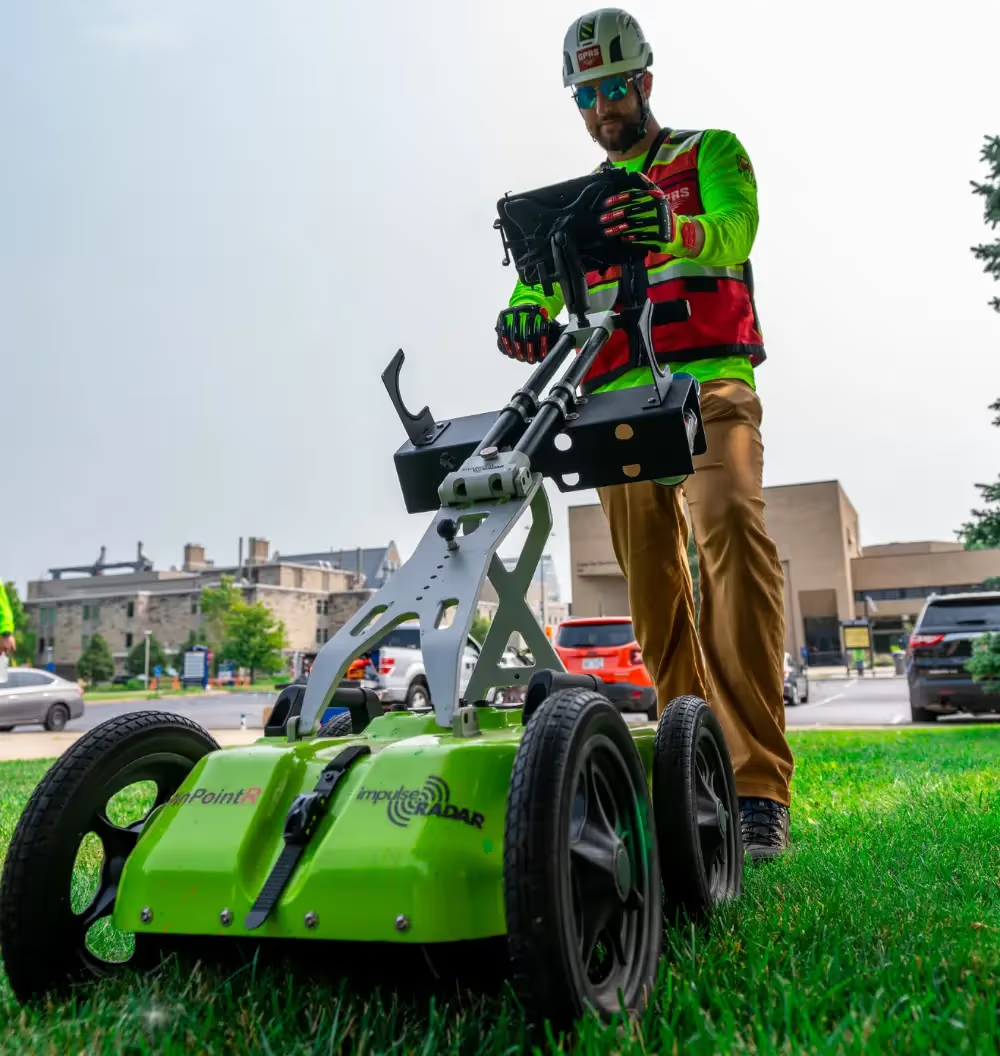
The utility locating GPR scanner resembles a push mower with rugged tires; it’s capable of investigating large sites quickly, regardless of terrain.
“We did both,” Halverson said. “So, I started with the [concrete] scanner, and [Ashley] was behind me to check for anything larger with the bigger GPR [utility locating] cart.”
Halverson said the biggest challenge with scanning the plant was dealing with the stifling heat emanating from its immense ovens.
Additionally, he and Ashley could not leave any permanent marks indicating their findings on the finished concrete floor. So, GPRS’ 3D laser scanning services captured these field markings and provided the client with a permanent record of the potential void locations through our WalkThru 3D product.
With WalkThru 3D, GPRS utilizes rectified 3D photogrammetry to create an orthomosaic 3D image that you can virtually walk through to visualize every aspect of your project. Remotely report existing reality capture to stakeholders, managers, contractors, and trades, so they can walk through the site at their own pace. And rest assured that you have a permanent, portable, and accurate 3D record of your property that your team can reference during operations and maintenance, and future planning purposes.
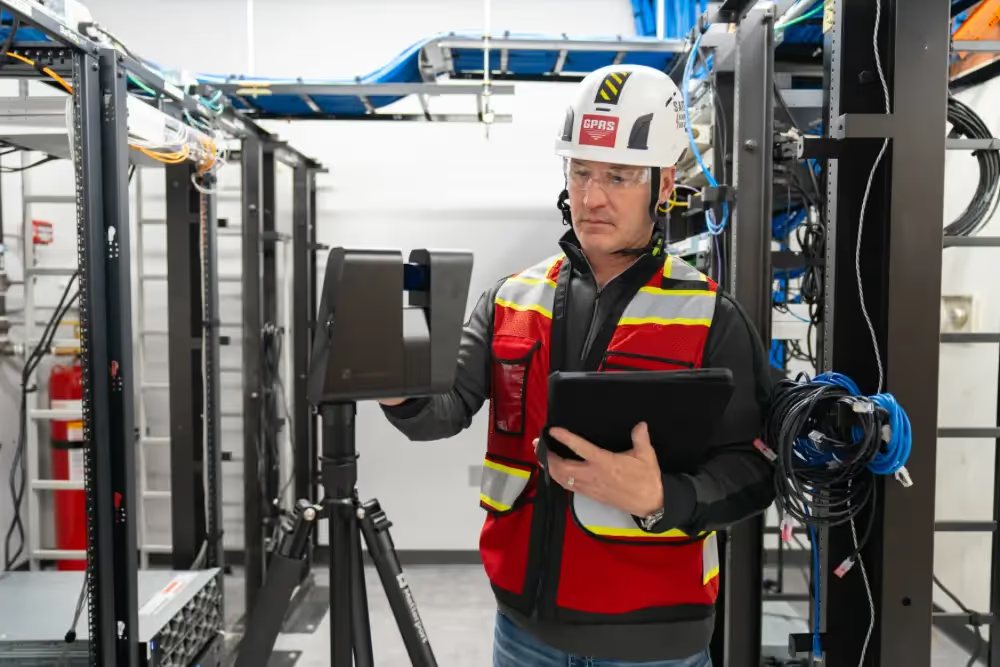
By locating the potential void locations, and creating a permanent record of these findings, via a WalkThru 3D virtual tour and 2D renderings, GPRS ensured that the plant’s structural problems could be rectified quickly and efficiently, bringing an end to the facility’s pest problem.
“We had to use tape and there was so much foot traffic that the tape wouldn’t have lasted very long,” Halverson said. “So, we used a Matterport Pro 3 Scanner [and captured our findings] so they could walk through pretty much everything, and then we told the client that we could also put that data in both a 2D, and 3D model where they’ll have all these potential voids mapped.”
Trust Built on SIM
The process Halverson and Ashley employed to accurately and efficiently investigate the food processing plant’s concrete slab is the same used daily by GPRS field team members across the country.
That process is underpinned by the Subsurface Investigation Methodology (SIM), the industry-leading specification and training program for utility locating, precision concrete scanning, sewer line inspections, and leak detection.
SIM addresses a step-by-step approach to collecting subsurface data to ensure that the results are repeatable and accurate. SIM practitioners must follow a checklist that is designed to ensure optimal results for every situation encountered in the field.
It’s because of SIM that GPRS has achieved and maintained a 99.8%+ rate of accuracy on over 500,000 utility locating and concrete scanning jobs to date.
From skyscrapers to sewer lines, GPRS Intelligently Visualizes The Built World® to keep your projects on time, on budget, and safe.
What can we help you visualize? Click below to schedule a service or request a quote today!
Frequently Asked Questions
What are voids in concrete slabs?
Voids in concrete slabs are empty spaces or air pockets that can form during the pouring and setting process of concrete. These voids can occur due to various factors such as improper compaction, air entrapment, or inadequate consolidation. Voids can weaken the structural integrity of the slab, leading to potential cracking, settlement, or other forms of damage over time.
How can voids in concrete slabs be detected?
Potential locations of voids in concrete slabs can be detected using several methods, including visual inspection, ultrasonic testing, ground-penetrating radar (GPR), and other non-destructive testing techniques. These methods can help identify the presence, size, and location of voids within the slab, allowing for targeted repairs or preventive measures.
What are the common methods for repairing voids in concrete slabs?
Repairing voids in concrete slabs typically involves filling the voids with suitable materials such as grout, epoxy, or polyurethane foam. The choice of repair material depends on the size of the void, the structural requirements of the slab, and other factors. In some cases, additional reinforcement or slab jacking may be necessary to restore the slab's structural integrity and prevent future void formation.