“Probably about 70% of the voids I find are right by the equipment, underneath the concrete…” – Parker Schings, GPRS Project Manager
When GPRS Project Manager Parker Schings first started conducting ground penetrating radar (GPR) scans at a petroleum refinery in Ohio, a worker at the facility told him about an incident that occurred in the 1990s.
A crane was being moved into place to conduct maintenance and renovations. Suddenly, the crane plunged into the ground.
“There was a big sinkhole beneath it, and it collapsed while they were working,” Schings said. “No one was hurt, but it’s still a big deal when that happens.”
Avoiding these potentially catastrophic accidents is exactly why Schings and his fellow GPRS Project Managers are often called upon to identify potential void conditions in petroleum facilities.
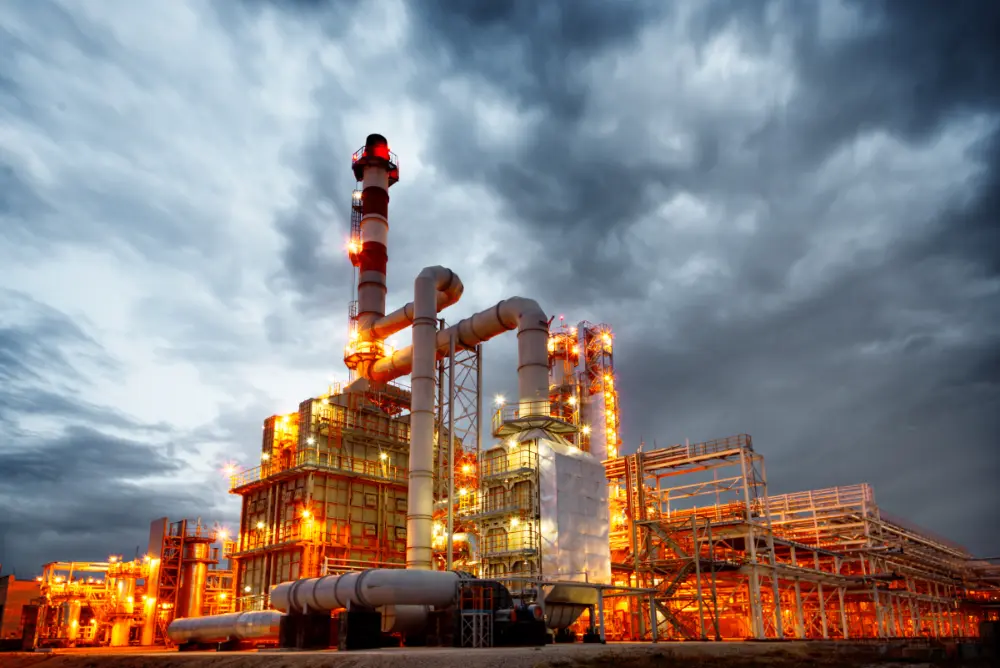
The machinery used to process raw crude oil into the end petroleum products we all rely on – including transformers, engines, motors, generators, pumps, and piping – generates significant subsurface vibrations that can compromise the integrity of surrounding concrete and soil.
While GPR cannot locate voids or tell you their precise dimensions, GPRS Project Managers are specially trained to use this non-destructive imaging tool to locate areas where conditions indicate the potential for a void. This helps these downstream facilities mitigate risk by telling them where to avoid when moving heavy machinery, and eliminates the need for costly, destructive, and time-consuming exploratory excavation (potholing) that would otherwise be necessary to locate these areas.
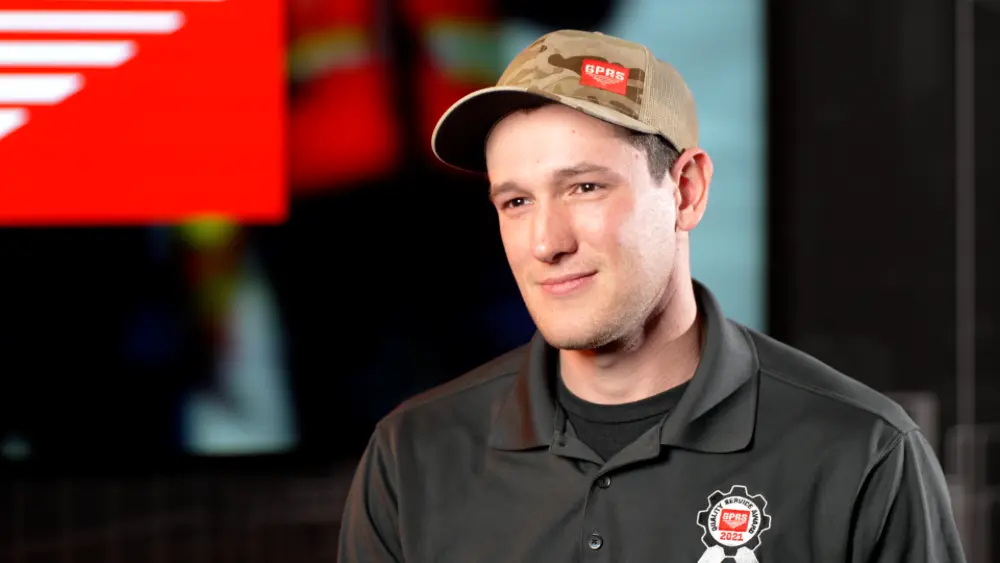
“We’ll go in, scan for where voids could be present, and let [the refinery] know where these areas are,” Schings said. “So, when they place their cranes [for maintenance, repairs, or renovations], they just stay away from those areas of concern.”
There were 129 operable petroleum refineries in the United States as of January 1, 2023, according to the U.S. Energy Information Administration.
These refineries are constantly undergoing renovations and maintenance to compensate for ever-increasing consumer demands. Domestic oil production has nearly doubled since 2008, according to data on Statista.com, with the U.S.’s oil refinery capacity amounting to approximately 18.1 million barrels per day in 2022.
The nation’s refineries are under more pressure than ever before to operate at full capacity. And to reach full capacity, refineries must undergo near-constant maintenance, which means moving heavy machinery like cranes into place as often as several times a week.
“They’re always working on something, and every unit, every time I’m at a refinery, there’s just a ton of work going on,” Schings said. “It’s very infrequent that I’m working and don’t have to work around scaffolding.”
GPRS is the trusted leader for damage prevention in the power industry – upstream, midstream, and downstream. From locating pipelines, flowlines, and water lines associated with drilling, to mapping the complex maze of subsurface infrastructure inside an oil refinery, petrochemical plant, or LNG facility, our Project Managers will be with you from planning and permitting, to operations and maintenance (O&M).
Ground penetrating radar (GPR) is GPRS primary tool for conducting utility locates and scanning concrete for subsurface voids, rebar, post-tension cable, and more.
GPR scanners emit radio waves into concrete surfaces or underground. These radio waves interact with any anomalies they may find, including buried utilities, underground storage tanks, and potential voids. The GPR scanner then collects this data and displays these interactions as a series of hyperbolas that vary in size and shape depending on what was located.
GPRS Project Managers interpret this data to report their findings, so that refinery and safety managers can take the appropriate safety precautions when excavating or transporting heavy machinery through a site.

Schings utilizes both a utility locating GPR unit and a concrete scanning GPR antenna when investigating for potential voids at refineries. The concrete scanning antenna is smaller and can be maneuvered around machinery and in other hard-to-reach areas, while the utility locating unit is attached to a four-wheel cart for easy travel over large distances.
“The refinery crews tell me that the scariest places for them to place heavy equipment on is concrete, because that’s usually pretty close to the refinery equipment and that equipment is always vibrating,” Schings said. “Probably about 70% of the voids I find are right by the equipment, underneath the concrete, so I’m definitely using the concrete scanning antenna.”
The Right Training for the Job
Just as with every job GPRS completes, Schings’ ongoing work at these refineries is underpinned by SIM: the Subsurface Investigation Methodology.
SIM is the industry-leading process for conducting concrete scans, utility locates, leak detection, and video (CCTV) pipe inspections. All GPRS Project Managers must become SIM-certified to work in the field, which means completing a minimum of 320 hours of field training and 80 hours of classroom training, where they encounter real-world scenarios designed to prepare them to tackle whatever they may face on an actual job.
Through our adherence to SIM, GPRS has achieved and maintains a 99.8%+ rate of accuracy on the over 500,000 utility locating and concrete scanning projects we’ve completed to date.
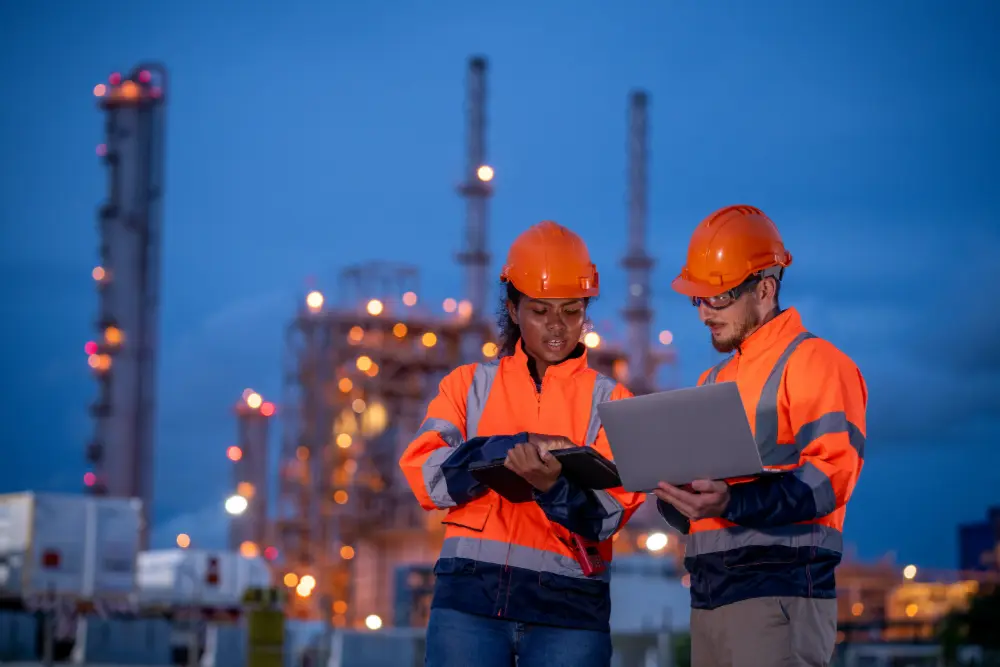
The Right Data: Always at your Fingertips
Accurate, actionable data is key to the success of any project, especially in high-risk environments like petroleum production.
When you hire GPRS, the data we collect on your site and all maps and models we create for you is accessible through SiteMap® (patent pending), our cloud-based infrastructure mapping software solution.
SiteMap® is designed to serve as a single source of truth for your infrastructure data, allowing you to plan, design, manage, dig, and build better. Maps, models, photos, reports, and existing condition as-built documents all exist in one space that is secure, yet easily accessible for you and your team members, 24/7, from any computer, tablet, or mobile device.
Our SiteMap® team members are currently scheduling live, personal SiteMap® demos so you can see for yourself what this software can do. Click the link below to schedule your demo today!
From skyscrapers to sewer lines, GPRS Intelligently Visualizes The Built World® to keep your projects on time, on budget, and safe.
What can we help you visualize? Click the links below to schedule a service or request a quote today!
Frequently Asked Questions
What is a subsurface void, and why are they dangerous?
A void is an empty space or cavity underground or within concrete. Voids pose a significant threat to the structural integrity of the surrounding earth or concrete and can lead to cracks or sinkholes which can endanger the lives of anyone in the area.
Can ground penetrating radar (GPR) determine the exact size of a subsurface void cavity?
No. GPR equipment can identify the area where a void is likely occurring, and the boundaries of that area, but it cannot accurately measure a void’s depth.
Can GPR scan vertical surfaces or ceilings?
Yes! GPRS Project Managers regularly use GPR to scan for the location of rebar in concrete columns and walls, and to examine the underside of a floor to mark out the reinforcing steel and any embedded conduits.