The Critical Path Method (CPM) has been a cornerstone of construction project management since its development in the 1950s by Morgan R. Walker at DuPont and James E. Kelley Jr. at Remington Rand. It gained popularity in the mid-1950’s as the military adopted it to build submarines and other materiel.
Although it has evolved in the intervening 75 years thanks to advancing technology, the fact that it is still a cornerstone of project management – from the construction industry through e-commerce to the military – is testament to its enduring logic. CPM is used to identify the longest sequence of dependent activities in a project and determine the shortest possible duration to complete the project.
The Enduring Logic That Scheduled 10,000 Workers for Five Years
CPM and its counterpart – PERT (Project Evaluation and Review Technique) are still utilized by the U.S. military to this day and are considered some of the most valuable project management tools in business.
In construction, CPM allows managers to optimize schedules, prioritize tasks, and allocate resources efficiently, ensuring that projects are completed on time and within budget.
The earliest high-profile application of CPM in the construction industry was to manage building New York’s World Trade Center’s Twin Towers, circa 1966-1971. The project cost more than $400 million ($3.8 billion adjusted), used 425,000 cubic yards of concrete, and more than 200,000 tons of structural steel.
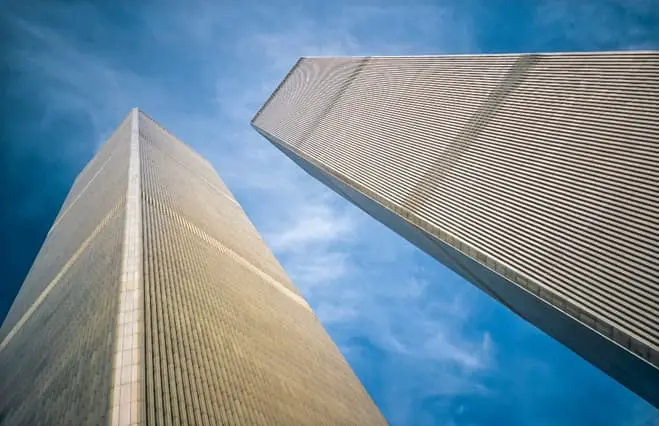
To get an idea of how massive this project was, consider this fact: Almost the entirety of the first two years of construction (1966-1968) occurred underground. You could not see the beginnings of the physical construction of the towers themselves until 1968 and the second tower was not completed until 1971. The project employed 10,000 construction workers, with as many as 3.500 working on site at once.
And the entire project was built utilizing Critical Path Methodology.
One of the key advantages of CPM in construction project management is its ability to provide a clear visualization of the project schedule through network diagrams. In the late 1960s, the calculations to find “the critical path,” and to plan for slack and float in non-critical tasks was done by hand with flow charts.
Visual representation of the critical and non-critical tasks helps managers understand interdependencies, dependencies, identify critical and non-critical activities, and anticipate potential bottlenecks. By focusing on the critical path – the “must have” tasks with little to no slack to bring the project in as planned – managers can allocate resources to the most important tasks, reducing the risk of delays and cost overruns.
How the Math Works
Critical path methodology requires the project manager to:
Identify all tasks in sequence and assign them numeric values for their:
- Earliest Possible Start time (ES)
- Latest Start Time (LS)
- Duration (t)
- Earliest Finish Time (EF)
- Latest Finish Time (LF)
- Float
They then employ a set of algorithms that allow you to identify the “critical tasks”: those with zero slack time available that must be completed for the project to be complete.
The main formula used to determine the critical path is made of two parts. Part 1 is the “forward pass,” and calculates Earliest Start (ES) and Earliest Finish (EF) times. The ES of any activity should equal the EF of the one preceding it. So, the formula is EF = ES + t, with t denoting the duration of the task.
The “backward pass” utilizes the Earliest Finish (EF) of the preceding task as its Latest Finish (LF). This formula gives you the Latest Start time (LS), which is LS = LF - t, with t again denoting task duration.
In addition to its scheduling benefits, CPM is also valuable for jobsite supervision and construction data management. It allows managers to monitor progress, adjust schedules as needed, and ensure that all activities are aligned with the project's objectives. This level of oversight is crucial for maintaining control over complex construction projects, where multiple teams and subcontractors are involved.
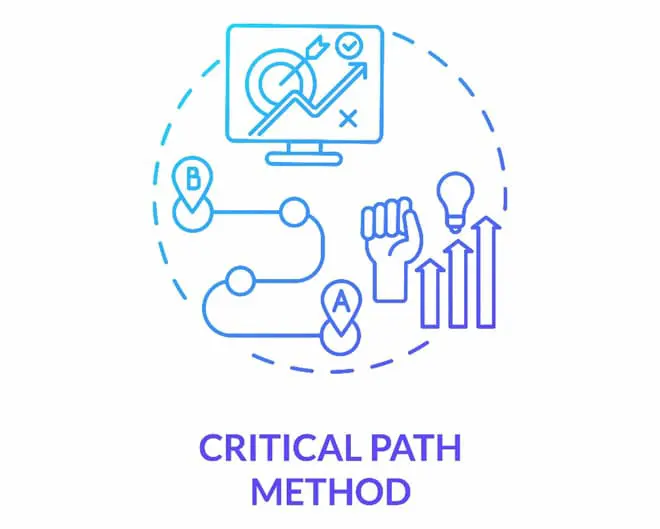
Over the past two decades, the integration of technology has significantly enhanced the capabilities of CPM. Modern construction management software has made it easier to create and update CPM schedules by doing the math for you to provide real-time data and analytics for better decision-making. These tools have also facilitated better communication and collaboration among project stakeholders, improving overall project efficiency.
These days, a wide variety of software is available to project managers and construction executives who utilize CPM. You can find cloud-based applications via Lucidchart, Asana, Teamwork, Smartsheet, and Hive, among others. What CPM software works best for you and your project(s) depends on many factors, including the user interface, ease of scheduling, and/or forensic discovery for lost labor or budget overruns.
Drawbacks & Industry Concerns
Despite its advantages, CPM is not without its downsides. The method can be complex and time-consuming, particularly for large projects with numerous activities and dependencies. It also relies heavily on accurate data and estimates, meaning that any errors in the initial planning phase can have a significant impact on the project's success. Additionally, CPM does not account for resource constraints, which can lead to unrealistic schedules if not properly managed.
Not all CPM applications are created equal, and there are industry pros who caution that, when undertaking high-level construction projects that could wind up in litigation, some of the algorithms powering the software is “geared not to produce honest appraisals of who or what caused a project delay. Instead they were geared to help parties to a delay disputes win.” – Frederic L. Plotnick of Construction CPM Conference, in Engineering News Record.
Plotnick goes on to state that, “different software can still be manipulated to ‘calculate’ the responsible part – even when liquidated damages may exceed $50,000 per day…”
Whether the fault lies in the software definitions/algorithms or with the users is beyond the scope of this article. We offer the caution to provide a balanced view of the evolution of Critical Path software development.
CPM & Lean Construction: The Push & Pull
In the context of lean construction and workflow management, CPM can be an effective tool for optimizing construction processes and reducing waste. By identifying the most critical activities and ensuring that they are completed efficiently, construction managers can streamline workflows and improve overall project performance. However, it is important to complement CPM with other methods, such as pull planning and/or the Last Planner System, to address its limitations and achieve a more holistic approach to construction project management.
Pull planning is a Lean construction planning and project management method where you start with the end goal and build backwards. That does not make it the opposite of CPM; rather the two planning types can work in concert to create a more seamless workflow.
However, many project managers prefer one variety of management over another, so it is important to understand both CPM’s push planning and Lean’s pull planning to keep everyone on the same page for your project.
CPM & GIS: A Perfect Pair?
Geographic Information Systems (GIS) platforms, such as the one included in GPRS' SiteMap®, can significantly enhance critical path method (CPM) scheduling in construction by providing spatial data and analytics to support decision-making.
By integrating a cloud-based, secure GIS platform with CPM, construction executives and project managers can gain a comprehensive understanding of the project site, including topography, infrastructure, and environmental constraints, which can impact scheduling and workflow.
SiteMap®, for example, offers accurate existing condition visual representation of underground utilities, structures, and other critical site features. This information is crucial for planning excavation, foundation work, and other site-specific activities that are integral to the project's critical path. By having access to this data, project managers can identify potential risks and obstacles early in the planning process, allowing for more accurate scheduling and resource allocation.
Furthermore, such applications can assist in monitoring progress and updating schedules in real time. As construction progresses, SiteMap® and GPRS products like ProCap and WalkThru 3D can provide updated site information, enabling project managers to adjust the critical path as needed. This level of flexibility and adaptability is essential for maintaining project timelines and ensuring on-time completion.
In addition, the integration of GIS with CPM scheduling can facilitate better communication and collaboration among project stakeholders. By providing a shared platform for viewing and analyzing site data, SiteMap® can help align the efforts of contractors, engineers, and other team members, leading to more efficient workflow management and decision-making.
Overall, the combination of infrastructure visualization tools like SiteMap® with critical path method scheduling offers a powerful tool for construction executives and project managers, enhancing their ability to plan, execute, and monitor construction projects effectively.
What can we help you visualize?
Frequently Asked Questions
How can project managers effectively monitor and adjust the Critical Path throughout the course of a construction project?
One of the most valuable features of CPM is that it allows for flexibility. Whether you have available float, or can eat some slack time from non-critical tasks can allow you to keep your team on schedule. Another important tool in defining finish times and progress is to capture and regularly update the project existing conditions. Whether you do so via 2D CAD drawings, 3D photogrammetry, or updated BIM modeling, it is vital to be able to communicate to all stakeholders, subcontractors, and trades where their tasks are in the flow and where there needs to be adjustment.
What is the difference between PERT (Program Evaluation and Review Technique) and CPM?
The main difference between PERT scheduling and CPM is flexibility. CPM relies on a fixed timeline and exact details of each task, whereas PERT can help gauge progress when projects have less certain details. Each has its place, and the two can work in concert as long as everyone on the project can communicate and collaborate smoothly.