The Andersons’ Clymer Indiana Ethanol Plant is the largest ethanol plant east of the Mississippi. The facility began operations in April 2007 and has the capacity to produce 110 million gallons of ethanol and 350,000 tons of distillers dried grain annually. Currently, the plant turns corn from more than 600 farms into 5.5 million gallons of ethanol fuel each year. The Clymer’s Ethanol Plant is strategically located next to The Andersons existing grain facility with access to an abundant amount of corn, utilities, and transportation infrastructure.
Process improvement is the proactive task of identifying, analyzing, and improving upon existing business processes, with the goal of improving process efficiency. The company plans to make improvements to the plant over the next five years to improve operational efficiency, lower plant emissions, maintain a quick product turn-around time, and provide outstanding customer service.
GPRS was hired by TLF Engineers to 3D laser scan the exterior cooler area at the southeast corner of the energy center for process improvements. This 2,500 square foot area includes the existing cooler, drop box, dust collectors, platforms, cooler, stack, and ductwork. Colorized point cloud data was collected of the area and used to create a 3D BIM model at a very high level of detail.
Our client, TLF Engineers, provides professional engineering services to agricultural facilities. They help all types of facilities maintain operations while designing repairs, upgrades, and equipment lines and maintenance for aging structures.
“GPRS 3D laser scanned the site in one day with the Leica RTC360 laser scanner, capturing a full-color point cloud,” said Neville Stringer, GPRS Visualization Consultant. The Leica RTC360 captures two million colorized data points per second with 2–4-millimeter accuracy in less than two minutes and a full-dome HDR image in one minute.
“This means you can complete a full high-resolution scan in less than three minutes per scan location with true HDR imagery,” said Stringer. “The Leica RTC360 laser scanner is a reliable and accurate 3D laser scanner that delivers a high-quality point cloud.”
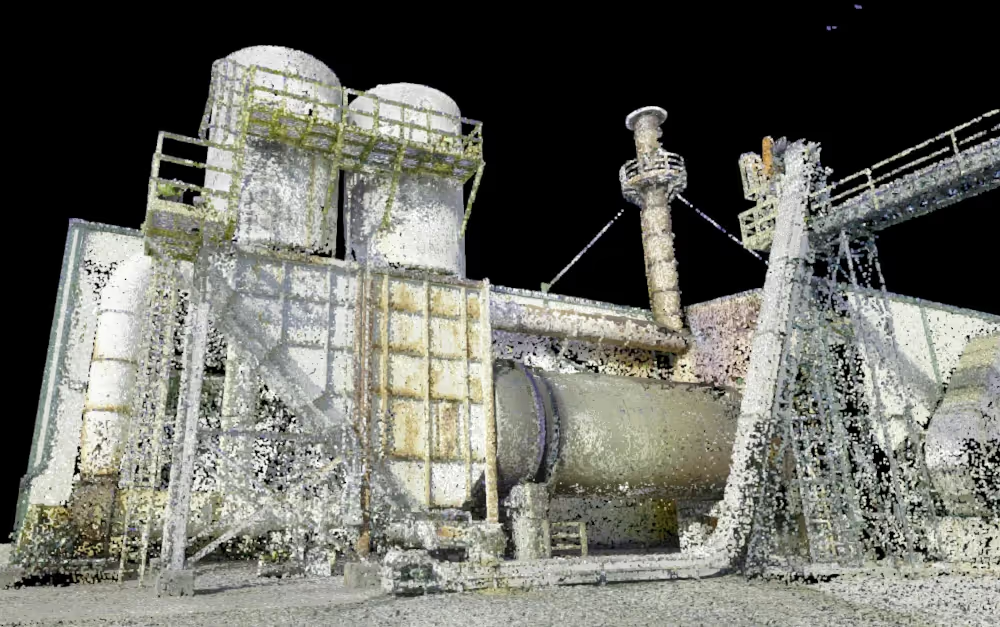
TLF Engineers’ Senior Project Engineer Seth A.R. Gressley, P.E. stated “We were extremely impressed with GPRS in your timeliness on responding to our request, to having crew on site to complete the scan, and in your communication with us through the process.”
Once data was acquired, it was delivered to the GPRS Mapping & Modeling Team to create a 3D BIM model. Katie Sopko, GPRS Senior CAD Technician said, “We used the point cloud to develop a Revit model of the existing site conditions. I created a 3D BIM model at very high detail of the exposed structure, walls, doors, stairs, roof, railings, ladders, columns, beams, bracing, equipment footprints, foundation, plates, bolt patterns, structural footers, platforms, girders, bollards, HVAC equipment, vents, piping, conduit, ducts, valves, Unistrut, cable tray, and pipe flanges.”
TLF Senior Project Engineer Gressley added, “This was the first time we have used GPRS modeling services, and the 3D model your team created was outstanding. We were very impressed with the level of detail and quality of the model, the speed in which your team was able to create it, and all aspects of communication during the process.”
GPRS also delivered panoramic TruView images of the point cloud to the client. TruViews are 360° photographs taken at each scanner set-up location. A TruView can be used to share point cloud data and mark-ups; take basic dimensions; estimate clearances and distances; and print and convert data. “A TruView gives this client the ability to tour the site through these 360° photographs,” said Sopko.
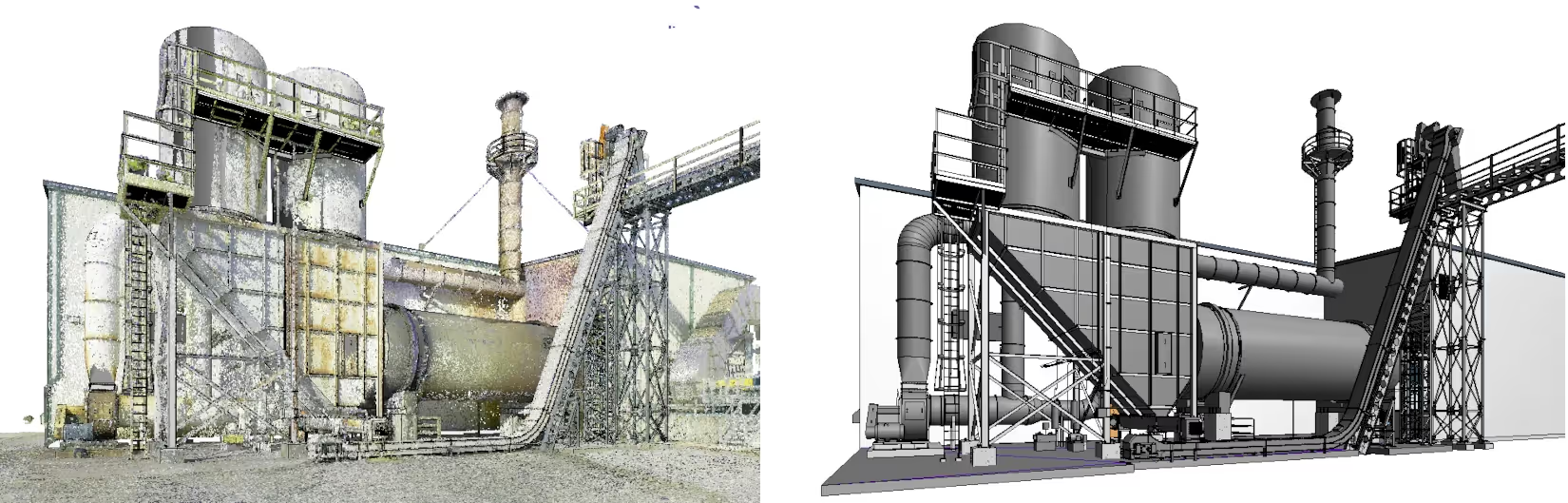
What is Dry-Mill Ethanol?
Dry-mill ethanol refers to the process of producing ethanol from corn without cooking or liquification. It is the most common method of producing ethanol in the United States. According to the U.S. Department of Energy Alternative Fuels Data Center, the United States is the world's largest producer of corn ethanol, having produced over 15 billion gallons in 2021 and 2022.
Dry-mill ethanol, produced from the dry-milling process of corn, is primarily used as a biofuel additive for gasoline. It is blended with gasoline in varying proportions, such as E10 (10% ethanol and 90% gasoline) or E85 (85% ethanol and 15% gasoline).
Dry-mill ethanol is a renewable alternative to traditional gasoline. It is used to reduce greenhouse gas emissions from transportation and the U.S.’s dependence on fossil fuels. In addition to its use as a fuel additive, ethanol is also used in various industries as a solvent, in the production of beverages and pharmaceuticals, and as a component in personal care products.
Ethanol fuel can be created from corn through a process called ethanol fermentation.
What are the Components of the Exterior Cooler Area that GPRS 3D Laser Scanned?
The Exterior Cooler
The exterior cooler area at the ethanol plant contains heat exchangers, such as air coolers or water coolers, that remove excess heat generated during the fermentation and distillation processes. For example, after the fermentation process, the fermented mash is typically heated to separate the ethanol from the remaining solids. The heat exchangers in the cooler area help to cool down the separated ethanol vapor, condensing it back into a liquid form. The exterior cooler area plays a crucial role in maintaining the optimal operating temperature for different stages of ethanol production, ensuring efficient and safe operation of the plant.
The Dust Collector
The dust collector at an ethanol plant is a system used to capture and remove dust and particulate matter generated during various processes in the plant. Dust collectors are essential for maintaining air quality, preventing the release of harmful particles into the environment, and ensuring the safety of workers.
Dust collectors are commonly used in areas such as grain handling, milling, fermentation, and drying. These areas generate dust and other particulates that need to be controlled to prevent potential hazards and maintain a clean and safe working environment.
Dust collectors typically consist of a blower, filter, and dust collection chamber. The blower creates a suction force that draws dust-laden air into the system, where the dust particles are trapped by the filter. The cleaned air is then released back into the environment, while the collected dust is either disposed of or recycled.
Dust collectors are an important component of ethanol plants, helping to ensure compliance with environmental regulations, protect the health and safety of workers, and maintain efficient plant operations.
The Drop Box
In an ethanol plant, there are two types of drop boxes. In the grain handling section of an ethanol plant, there is a drop box where grains like corn are unloaded from trucks or railcars. This is essentially a large container or bin designed to receive and temporarily store the incoming grain before it is processed further.
In the distillation or dehydration processes, there is a drop box used for collecting the final ethanol product. This is a temporary storage container where the ethanol is collected before being transferred to storage tanks or further processing units.
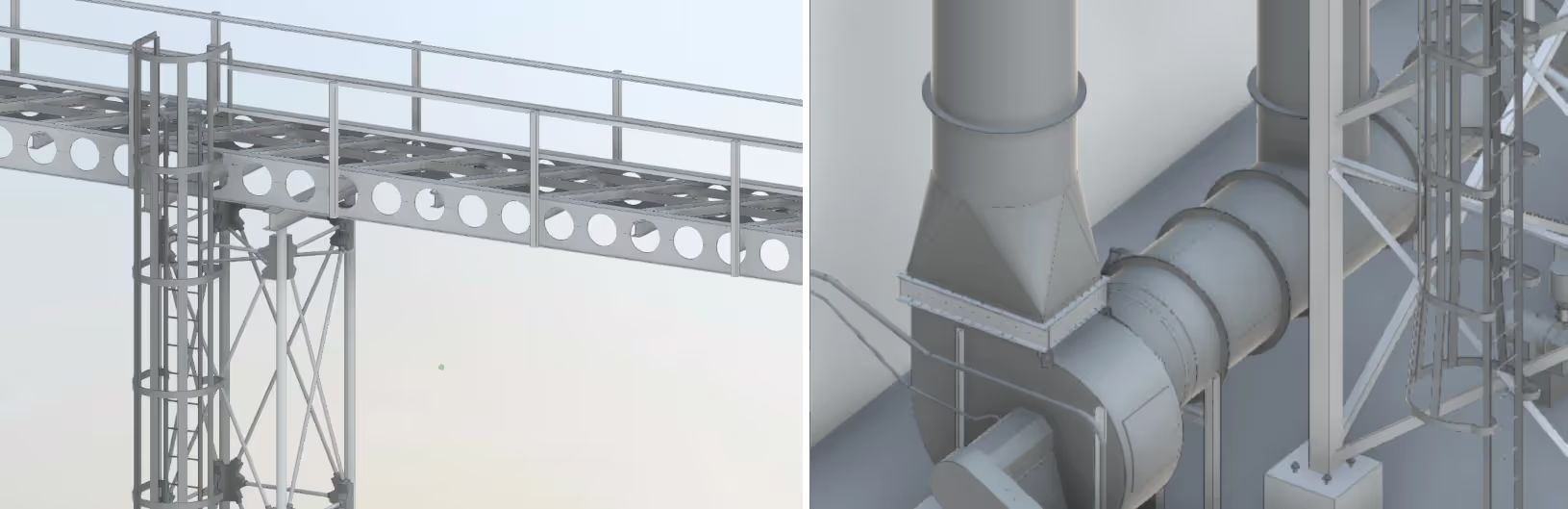
Ethanol Plant Upgrades to Increase Efficiency and Lower Emissions
TLF Engineers will seek to optimize the following processes to help The Andersons' Clymers facility improve their overall efficiency, decrease air pollution, reduce costs, and remain competitive in the market.
By optimizing processes and equipment, the ethanol plant can improve their operational efficiency and lower plant emissions.
- Optimize the milling process to improve ethanol yield and quality
- Optimize the production processes: the milling, fermentation, distillation, and dehydration processes to improve ethanol production efficiency
- Optimize dust collection and filtration systems to reduce air pollution
- Upgrade equipment to improve reliability and efficiency
TLF Engineers stated, “We have a desire to be involved with this unique work and have developed comfort and skill in working in industrial facilities safely and efficiently.”
As for GPRS 3D Laser Scanning Services, “We greatly appreciated all the help and will continue using your services in the future,” added TLF’s Gressley.
Does Ethanol Production Create Air Pollution?
An ethanol plant could contribute to air pollution through various processes and emissions. Some potential sources of air pollution from an ethanol plant include:
- Particulate Matter: Dust and particulate matter can be generated during grain handling, milling, and drying processes. If not properly controlled, these particles can be released into the air, contributing to air pollution.
- Volatile Organic Compounds (VOCs): VOCs can be emitted during the fermentation and distillation processes. VOCs are a type of air pollutant that can react with other compounds in the atmosphere to form smog.
- Carbon Monoxide (CO): CO can be produced during the combustion of fossil fuels for heat and power in the plant. CO is a poisonous gas that can be harmful to human health and the environment.
- Nitrogen Oxides (NOx): NOx emissions can be generated during combustion processes, such as in boilers or engines used for power generation. NOx is a precursor to smog and can contribute to respiratory issues and environmental damage.
- Greenhouse Gas Emissions: While ethanol itself is considered a renewable fuel with lower greenhouse gas emissions compared to gasoline, the production process can still contribute to greenhouse gas emissions. Emissions can occur during the production and transportation of feedstocks, as well as during the energy-intensive processes within the ethanol plant.
To mitigate these potential sources of air pollution, ethanol plants can implement various control measures, such as using dust collection systems, optimizing combustion processes to minimize emissions, and using cleaner energy sources. Additionally, regulatory agencies often impose emission limits and require monitoring and reporting to ensure compliance with air quality standards.
The facilities aim to reduce these toxic chemicals, as exposure to high amounts can cause symptoms like headaches, drowsiness, burning in the nose, throat and eyes, coughing, nausea, vomiting, and trouble breathing.
In an effort to keep the public informed about toxic chemicals and pollution in their communities, the EPA created a program for companies to report the use of toxic chemicals called Toxics Release Inventory Program.
What are the Benefits of Ethanol?
Ethanol produced from corn grain is a renewable, domestically produced transportation fuel. Because of its high oxygen content, ethanol burns more completely than ordinary unleaded gasoline and reduces harmful tailpipe emissions. Ethanol also has a higher-octane number than gasoline, which provides increased power and performance. For example, IndyCar drivers often fuel their race cars with E98 because of its high octane.
Experts at the Department of Energy’s Argonne National Laboratory published a study demonstrating that average corn ethanol reduces Greenhouse Gas emissions by 44 to 52 percent compared to gasoline.
In December 2021, the Biden Administration issued an Executive Order calling for most federal vehicle acquisitions to be zero-emission vehicles by 2035. The Biden Administration and the U.S. Department of Agriculture (USDA) have recently announced incentives and funding for biofuel development and infrastructure.
“Ethanol already cuts carbon emissions in half compared to gasoline; with smart policy measures, ethanol can do even more,” said RFA President and CEO Geoff Cooper. “Ethanol can serve as a zero-emissions fuel for cars and trucks while also helping to decarbonize the aviation, marine, and stationary power generation sectors.”
More About The Andersons’ Clymers Indiana Ethanol Plant
The Andersons’ Clymers Ethanol Plant is a producer and supplier of ethanol, natural gasoline, corn oil, liquified CO2, as well as blending systems.
The facility is located in a high producing corn growing region in Indiana. The facility features 4 million bushels of on-site corn storage, unit train rail loading and unloading facilities, Norfolk Southern mainline access, and existing grain processing infrastructure. The facility is well located to provide ethanol to east coast and southeastern markets, as well as to supply Chicago, Indianapolis, and Gary, Indiana via truck.
Neill McKinstray, Vice President & General Manager, Ethanol Division for The Andersons said, “The Andersons’ Clymers Indiana Ethanol Plant provides an additional market for area corn growers, many of whom have an established relationship with The Andersons, and a local supply of distillers dried grains for area animal farmers.”
The Andersons, Inc. is a diversified company with interests in the grain, ethanol, and plant nutrient sectors of U.S. agriculture, as well as in railcar leasing and repair, turf products production, and general merchandise retailing. Founded in Maumee, Ohio, in 1947, the company now has operations in seven U.S. states plus rail leasing interests in Canada and Mexico.
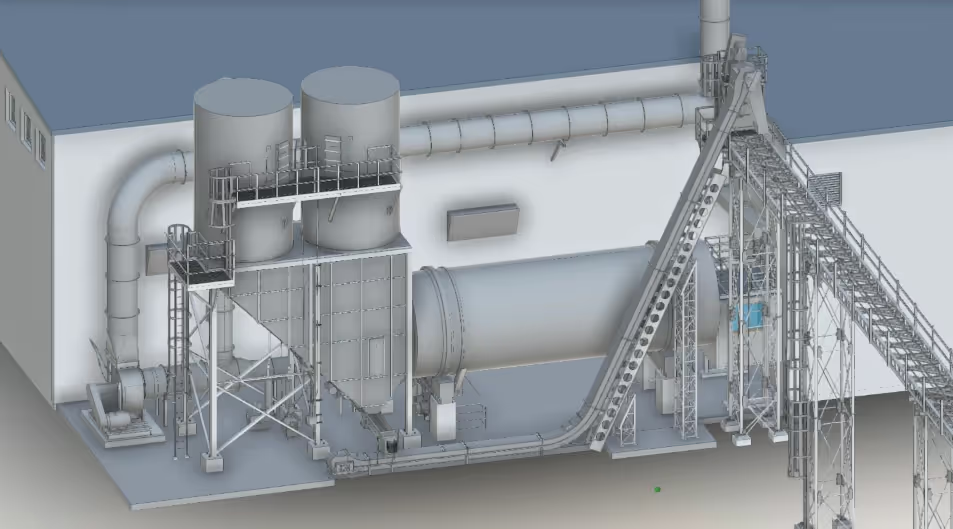
Why GPRS? The GPRS Difference.
The professionals at GPRS have extensive experience 3D laser scanning for the agricultural industry, including grain handling, storage, feed, milling and processing industries. We have 3D laser scanned grain facilities, ethanol facilities, production agriculture, grain processing operations and suppliers to the food corn industry.
From the initial planning and design of a grain silo, to engineering grain intake and distribution towers, to construction of a grain loading dock, to replacing ducts and piping for a grain chute, to analyzing tank farm slab elevation contours – and everything in between – GPRS has the resources to create a solution unique to your business needs.
We have completed scanning projects ranging from small rooms to entire facilities. We have captured precise data of grain intake and distribution towers, tanks, silos, hoppers, conveyors, support cables, structural members, machinery, equipment, rail spurs, catwalks, cleaning houses, grain elevators, drive throughs, and so much more.
GPRS utilizes Leica Geosystems 3D laser scanners to provide a safe and accurate means of collecting site and overhead data from the ground, providing vital detail for design planning and analysis.
What can we help you visualize?
Frequently Asked Questions
Is there any government support for biofuel production facilities?
U.S. Department of Agriculture (USDA) announced that the Department has provided $700 million to help lower costs and support biofuel producers who faced unexpected market losses due to the COVID-19 pandemic. The funds are being made available through the Biofuel Producer Program, which was created as part of the Coronavirus Aid, Relief, and Economic Security Act (CARES Act). The investments include more than $486 million for 62 producers located in socially vulnerable communities. The Program will support agricultural producers that rely on biofuels producers as a market for their agricultural products. By making payments to producers of biofuels, the funding will help maintain a viable and significant market for such agricultural products.
How much does 3D laser scanning cost?
The cost of 3D laser scanning can vary widely depending on your project scope. GPRS customizes every quote specific to your project’s needs. GPRS Project Managers use 3D laser scanners to capture every detail of your site, delivering building dimensions, locations, and layout with 2-4 millimeter accuracy. This can include the aboveground structural, architectural, and MEP features, plus underground utility and concrete markings. Our Mapping & Modeling Team can deliver point clouds, 2D CAD drawings, 3D BIM models, 3D Mesh models, TruViews, and Virtual Tours at any level of detail.
How are 3D BIM models used for clash detection?
A 3D BIM model helps clients evaluate if the new elements fit accurately within the existing structure and enable clash detection to identify conflicts between the design and as-built conditions. With a 3D BIM model, clients can virtually see what conflicts or overlaps in the project design plans. They can inspect each new component, pipe, or system within the as-built conditions and discover clashes.