2D CAD Drawings Assist with the Engineering of Anchors
Skanska Hired GPRS to Perform Concrete Scanning at an Aircraft Assembly Plant
A commercial airplane manufacturer was planning to install new wing stands in its main aircraft assembly plant. Skanska was hired as the general contractor by the manufacturer to anchor the wing stands to the lid and floor of the building. Existing reinforcements in the concrete slab needed to be located and marked before drilling holes in the concrete for the anchors. Identifying where rebar is located before drilling into the concrete reduces the risk of injuries or anchor failure.
Skanska hired GPRS to scan, locate, and mark the rebar in the concrete around the proposed anchor locations. The scope of work included concrete scanning six 5 ft. x 5 ft. areas on the lid and 1,150 square feet of concrete on the floor. GPRS delivered point cloud data and 2D CAD drawings to assist with the engineering of the wing stand anchors.
To ensure the structural integrity of the anchors, GPRS was asked to differentiate the bottom, middle, and top bar and to provide the thickness of the slab in all areas. Skanska requested precise dimensions from the rebar to the base plates currently installed in the slab and precise dimensions on the drawings locating all embedded items, slab attachments, and anchors in the concrete slab.
The GPRS Project Manager used ground penetrating radar (GPR) to identify the rebar pattern and thickness of the concrete. During concrete scanning, data is displayed on a screen and marked on the surface in real time. The GPRS Project Manager marked the rebar locations, dimensions, and thickness directly onto the concrete slab using wax crayon. The wax crayon is smear-proof, fade-proof, weather- and water-resistant and will remain for a long time, but can easily be removed upon project completion.
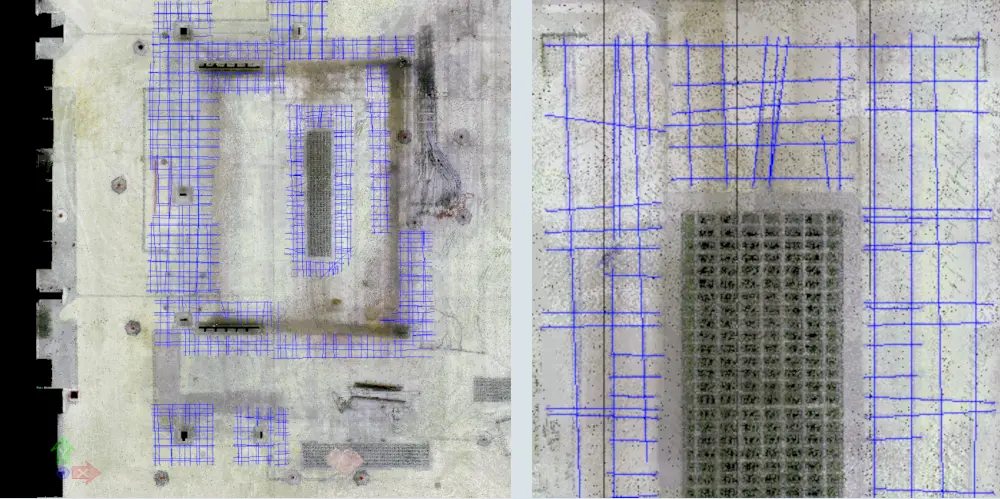
The Skanska engineer wanted critical project information captured in 3D to ensure they could engineer this project safely and to the spec of the facility owner. Once concrete scanning was complete, GPRS 3D laser scanned the concrete markings to document the findings in high detail in the form of a point cloud. The Leica 3D laser scanner used on site captured data at incredible speeds with millimeter accuracy. TruViews were also taken, providing the client a 3D panoramic view of the scan data at each laser scanner location.
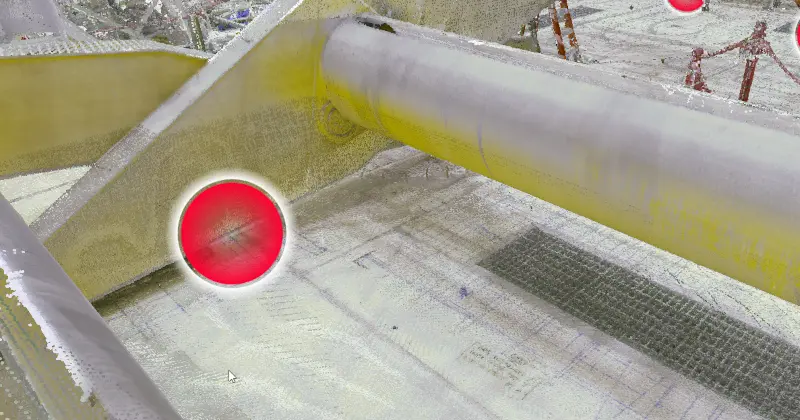
Concrete findings were drafted in CAD using the 3D point cloud data. According to Jayce Vogt, the GPRS CAD Technician on the project, “Using Cyclone 3DR, we captured the linework in an easy to digest, clean 3D view. The program allowed the lines to be sent directly to AutoCAD.” The 2D CAD PDF delivered dimensions for all embedded items, slab attachments, and anchors in the concrete, plus dimensions from the rebar to the base plates currently installed in the slab.
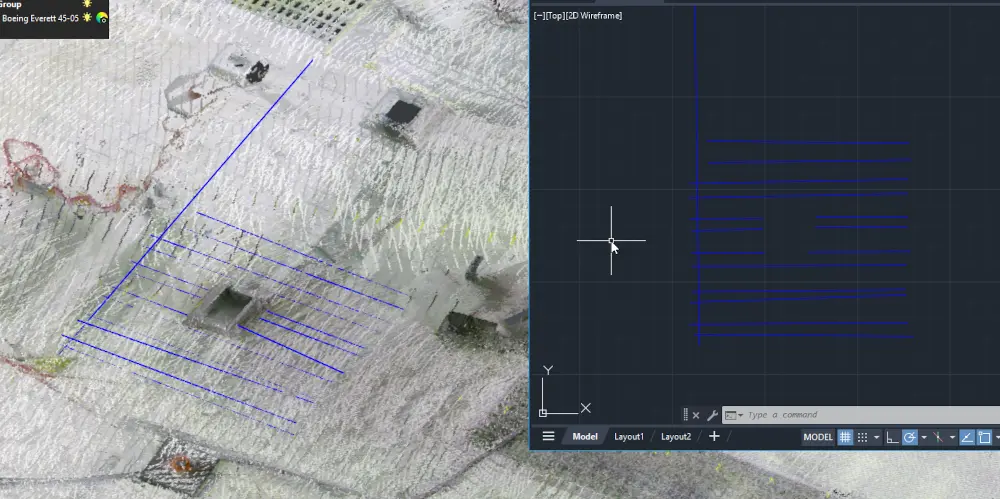
GPRS completed this work in 10 days, giving Skanska the precise information they needed to proceed efficiently and cost effectively. GPRS provided Skanska the required information to meet the spec of the owner and provide them with a detailed and accurate 2D CAD map of their facility.
Skanska is one of the world’s leading construction and development companies. They partner with airports, airplane manufacturers, aerospace companies, and other various companies to design and engineer construction projects. In this project, located in Washington State, they aided the high-tech manufacturing efforts of the airplane assembly and production line.
Why Choose GPRS for Concrete Scanning Services?
GPRS Project Managers can clear dozens of cutting and coring areas daily with an exemplary level of accuracy. We continue to maintain a 99.8% accuracy rate on over 500,000 jobs completed since our founding in 2001.
Ground penetrating radar technology is extremely effective at locating rebar deep within a concrete structure, but the equipment requires extensive training. Each member of our elite team of over 500 Project Managers has completed the industry-leading Subsurface Investigation Methodology (SIM) program. This standard operating procedure includes specifications for underground utility locating and concrete scanning.
The SIM training program consists of 80 hours of classroom and hands-on training and 320 hours of mentorship in the field to ensure Project Managers’ competence in GPR equipment and field knowledge.
GPRS is so confident in our SIM-qualified Project Managers that we provide the Green Box Guarantee, which states that when we place a Green Box marked “Clear” within a layout before your crew anchors or cores, or cuts concrete, we guarantee that the area will be free of obstructions.
GPRS has over 22 years’ experience in concrete scanning. No other company could locate, mark, scan, map, and model a project site with the accuracy and detail as GPRS.
What can we help you visualize?
Frequently Asked Questions
How Does Ground Penetrating Radar Work?
GPRS performs concrete scanning services using ground penetrating radar to clear concrete areas from hidden dangers prior to anchoring, saw cutting, or core drilling. Ground penetrating radar sends a small electromagnetic pulse into the concrete and a Project Manager analyzes the echoes that result from sub-surface objects. The equipment requires extensive training. GPRS Project Managers can locate and document the location, patterns, depths, of a wide range of objects, such as reinforcement and conduit embedded in concrete.
What is 3D Laser Scanning?
A 3D laser scanner is a non-contact digital technology capable of collecting millions of measurements per second by emitting lasers. The scanner will be set up in multiple locations and captures the physical world by sending out pulses of laser light that reflect off exposed objects and surfaces. The individual scans are then merged and the resulting data environment is called a point cloud which represents the size, shape, and orientation of three-dimensional objects.
How Do you Mount Equipment to an Aircraft?
There is a method of mounting equipment to an aircraft. The method comprises attaching components to the fuselage of the aircraft. The fuselage, or body of the airplane, is a long hollow tube which holds all the pieces of an airplane together. As with most other parts of the airplane, the shape of the fuselage is normally determined by the mission of the aircraft.
What are the Consequences to Poor Anchor Installation?
Poor anchor installation may lead to a reduction of safety margins that are built into the anchor design process, or a failure of the anchor during installation or during its service life.
What are the Hazards Associated with Concrete Anchoring?
Some of the hazards associated with concrete anchoring are saw kick back, collapsing walls, blade fracture, and electrocution. Learn more about the dangers of cutting concrete with a GPRS Concrete Cutting and Sawing Safety Presentation.