March Madness is all about precision, strategy, and execution – just like facility management. Teams that make deep tournament runs rely on accurate scouting reports, efficient game plans, and seamless teamwork. The same principles apply when managing facilities, whether planning renovations, maintaining critical infrastructure, or optimizing space.
Without accurate data, even the best-laid plans can collapse under pressure. That’s where 3D laser scanning becomes a game-changer, providing precise as-built documentation that facility managers, general contractors, and subcontractors need to stay ahead of the competition.
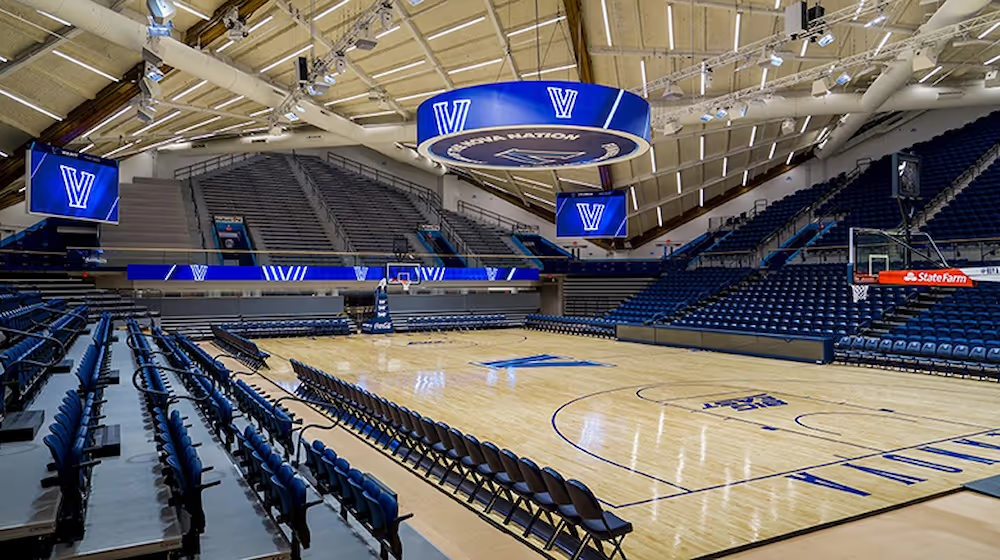
Scouting the Competition: Why Accurate Data Matters
Just as coaches analyze their opponents before a big game, facility managers need reliable building documentation to make informed decisions. Relying on outdated blueprints is like running a full-court press with a team that isn’t conditioned – it leads to costly mistakes, wasted time, and operational setbacks.
Williams College, for example, initially selected Existing Conditions, a GPRS company, to scan a single building. Recognizing the value, the college expanded the project into a comprehensive campus-wide survey covering over four million square feet. The highly accurate 3D laser scan data provided a foundation for renovations, space planning, and long-term facility management strategies.
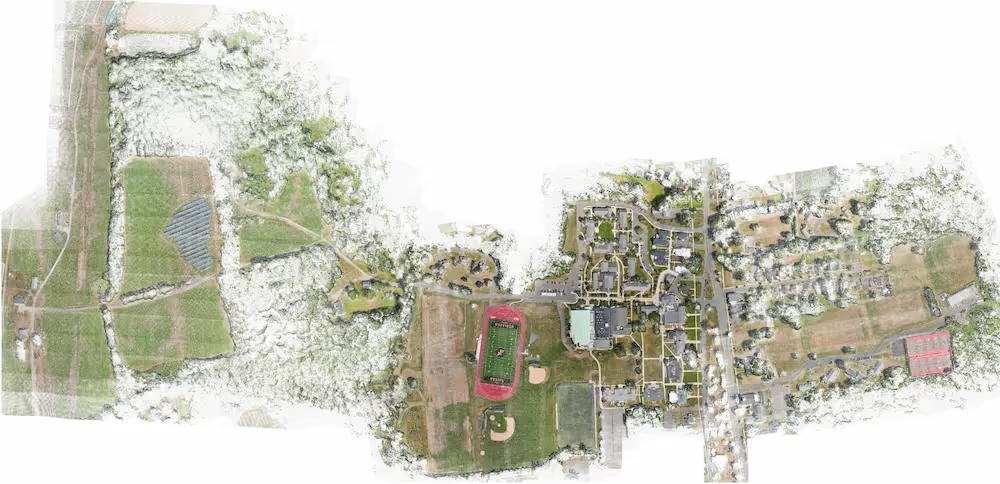
Similarly, Suffield Academy worked with Existing Conditions and Centerbrook Architects to survey eight buildings, including athletic and performing arts facilities. The result? 3D Revit floor plans, reflected ceiling plans, exterior elevations, and roof plans – critical tools for their facility management team.
Game Plan: The Role of 3D Laser Scanning
A successful offense starts with strong fundamentals. In facility management, 3D laser scanning provides a foundation for planning, renovations, and maintenance by capturing millions of precise data points.
- Technology Advantage: Our Leica RTC360 scanner captures and processes two million points per second with 2-4 mm accuracy.
- Data-Driven Decisions: Instead of relying on outdated floor plans, facility managers get real-time, reliable as-built documentation to avoid errors and unexpected obstacles.
Key Strategies for Facility Management Success
1. Accuracy Wins Championships
A buzzer-beater only counts if it’s precise – just like measurements in facility management. Even small miscalculations can lead to costly errors. 3D laser scanning ensures:
- High-precision data capture
- Optimized workflows
- Minimized costly rework
2. Speed and Efficiency: Beating the Shot Clock
Just like teams must execute plays before the shot clock expires, facility managers work under tight deadlines. Traditional measuring methods take too long and introduce human error. 3D laser scanning:
- Reduces data collection time from weeks to hours
- Minimizes disruptions to building occupants
- Delivers rapid, reliable insights
3. Teamwork and Coordination: A Strong Assist Game
Great basketball teams thrive on communication and collaboration. Facility managers, architects, engineers, and contractors need to be on the same page. Accurate as-built documentation ensures:
- Unified data for all stakeholders
- Reduced miscommunication between teams
- Improved coordination for seamless project execution
4. Risk Mitigation: Avoiding Costly Turnovers
A turnover in the final seconds can cost a team the game, just like unexpected structural surprises can derail a facility project. With 3D laser scanning, facility managers can:
- Identify potential clashes between new and existing infrastructure
- Detect structural issues before construction begins
- Reduce costly change orders and scheduling delays
5. Smart Budgeting: Maximizing Cap Space
Championship teams manage their salary cap wisely – just as facility managers must control costs while ensuring efficiency. 3D laser scanning helps:
- Reduce rework and material waste
- Optimize space utilization
- Streamline maintenance and asset management
6. Future-Proofing Facilities: Planning for Next Season
Winning programs don’t just focus on the current season – they recruit and develop for the future. Facility managers must do the same by ensuring buildings are adaptable for future needs. 3D laser scanning enables:
- Digital twin creation for long-term facility planning
- Sustainability initiatives by reducing unnecessary renovations
- Lifecycle management for long-term cost savings
Building Your Facility Management Bracket: How to Get Started
Step 1: Assess Your Facility’s Needs
Identify areas where precise as-built documentation is most critical:
- Aging buildings with missing or inaccurate documentation
- Spaces undergoing renovations or expansions
- Critical infrastructure requiring accurate records
Step 2: Choose the Right Technology Partner
Not all 3D laser scanning providers have championship-caliber expertise. Work with experienced professionals who specialize in as-built documentation to ensure reliable, high-quality results.
Step 3: Implement Data-Driven Decision-Making
Once you have accurate building data, use it to your advantage:
- Plan preventive maintenance more effectively
- Share as-built models with architects and contractors for seamless execution
- Integrate data into SiteMap® for centralized access
SiteMap®: The Playbook for Facility Management
Just as elite teams rely on detailed scouting reports and analytics, facility managers need a centralized system to manage their data.
SiteMap®, GPRS’ proprietary project management platform, provides:
- Real-time access to building data for all stakeholders
- Improved collaboration across facility management, architecture, and engineering teams
- Efficient decision-making with centralized, cloud-based storage
Its interactive interface ensures that every project – from small facility upgrades to full-scale renovations – stays on track without the risk of miscommunication or data loss.
Final Buzzer: Elevate Your Facility Management Game
Winning in March Madness requires preparation, teamwork, and execution – the same strategies that drive successful facility management.
By leveraging 3D laser scanning, facility managers gain a competitive edge, ensuring buildings are accurately documented, efficiently managed, and ready for future challenges. Start Intelligently Visualizing The Built World® with GPRS and take your facility management game to championship levels.
What can we help you visualize?
Frequently Asked Questions
How should a P&ID be interpreted within the AEC industry?
A P&ID must be analyzed with a detailed understanding of its standardized symbols, which represent piping, valves, instrumentation, and system components. These diagrams provide critical insights into process flow, control mechanisms, and interconnectivity. Engineering teams rely on precise interpretation to make informed design, maintenance, and operational decisions, ensuring compliance with industry regulations.
Can 3D laser scanning generate a complete P&ID?
While 3D laser scanning does not directly create a P&ID, it provides highly accurate as-built conditions that serve as the foundation for developing a Process Flow Diagram (PFD). Engineering expertise is then applied to integrate instrumentation and operational elements, ensuring that the final P&ID reflects the facility's true layout and functionality.
What advantages does 3D laser scanning offer for P&ID accuracy?
3D laser scanning delivers highly accurate data, eliminating the risks associated with manual measurement errors and outdated documentation. By capturing as-built conditions in a digital format, it ensures that P&IDs remain accurate, reducing discrepancies and enhancing efficiency in system design, modification, and compliance audits.
How does P&ID integration with BIM and CAD platforms improve project outcomes?
Seamless integration of P&IDs with CAD and BIM workflows allows engineering teams to work with real-world data, optimizing design accuracy, clash detection, and project coordination. This integration enhances collaboration across disciplines, minimizes rework, and accelerates decision-making processes in construction and facility management.
Why is maintaining up-to-date P&IDs essential for facility management?
Accurate and current P&IDs are critical for ensuring operational safety, regulatory compliance, and efficient system modifications. As facilities undergo changes, integrating 3D laser scanning enables continuous updates to P&IDs, providing a reliable reference for maintenance planning, system troubleshooting, and risk mitigation.