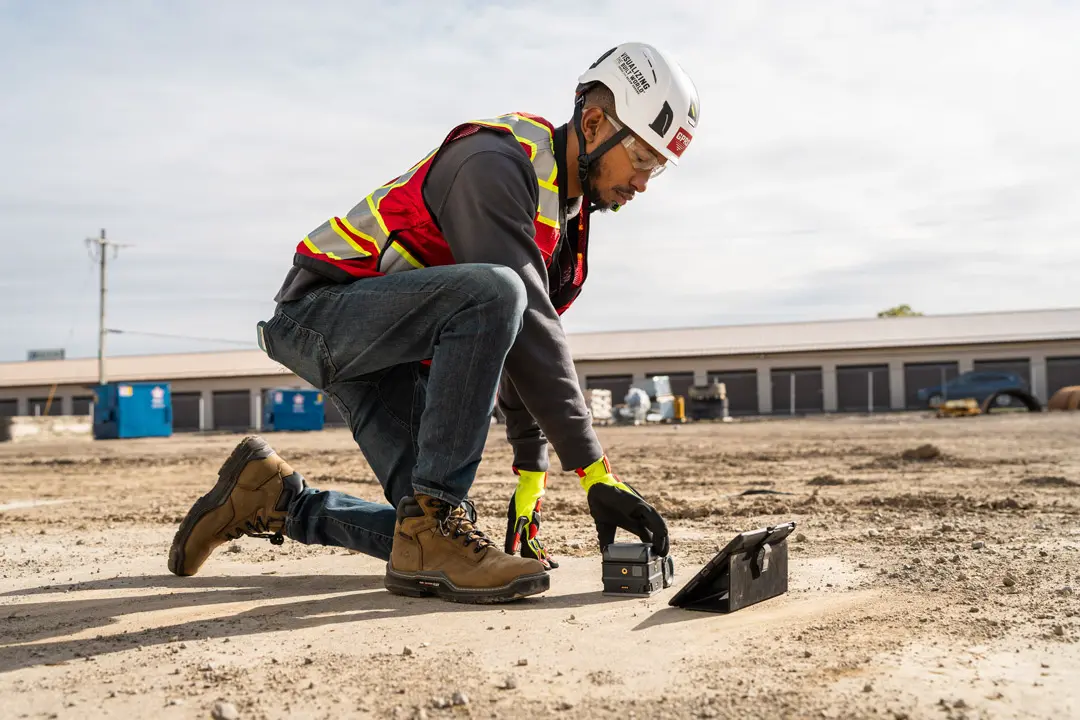
When time, money, and the wellbeing of others are on the line, the kind of imaging technology you choose matters.
The question you must ask yourself when considering whether to hire a ground penetrating radar (GPR) or digital X-ray imaging company to evaluate the interior of concrete that you’re preparing to cut or core is how safe do you want your jobsite to be?
GPR supplanted X-ray imaging decades ago as the most efficient, accurate, and safe method of precision concrete scanning. And digital X-ray imaging – a modified form of the original technology – remains slower, less efficient, and more dangerous than GPR.
Digital X-Rays Explained
Digital X-ray imaging involves placing a radioactive isotope on one side of a concrete slab, and a receiver on the other. Traditionally, the results of X-ray imaging were recorded on film that would have to be developed off site before results could be interpreted. The final image would be high quality, but the time it took for the film to be developed combined with the danger of bringing a radioactive material onto a construction site to conduct the X-ray scan made this process less than ideal.
Newer digital receivers eliminate the delay between scans and results, and other digitized aspects of the process including electronically powered “on/off” switches reduce – but don’t eliminate – the risk of radiation exposure during scanning.
Digital concrete X-ray imaging utilizes the same base technology – a radioactive isotope – involved in traditional X-ray imaging, which means that it still carries with it the same problems as traditional X-ray imaging:
- At least a portion of your site will need to be shut down during the scanning process due to the potentially hazardous, radioactive material used in X-ray imaging.
- X-ray imaging of any kind requires access to both sides of a concrete slab – one side for placing the radioactive material, and the other for placing a receiver.
- X-ray imaging cannot evaluate concrete slab-on-grade.
- X-ray imaging machinery is much bulkier and less versatile than modern GPR scanners, which are wireless and fit in the palm of your hand.
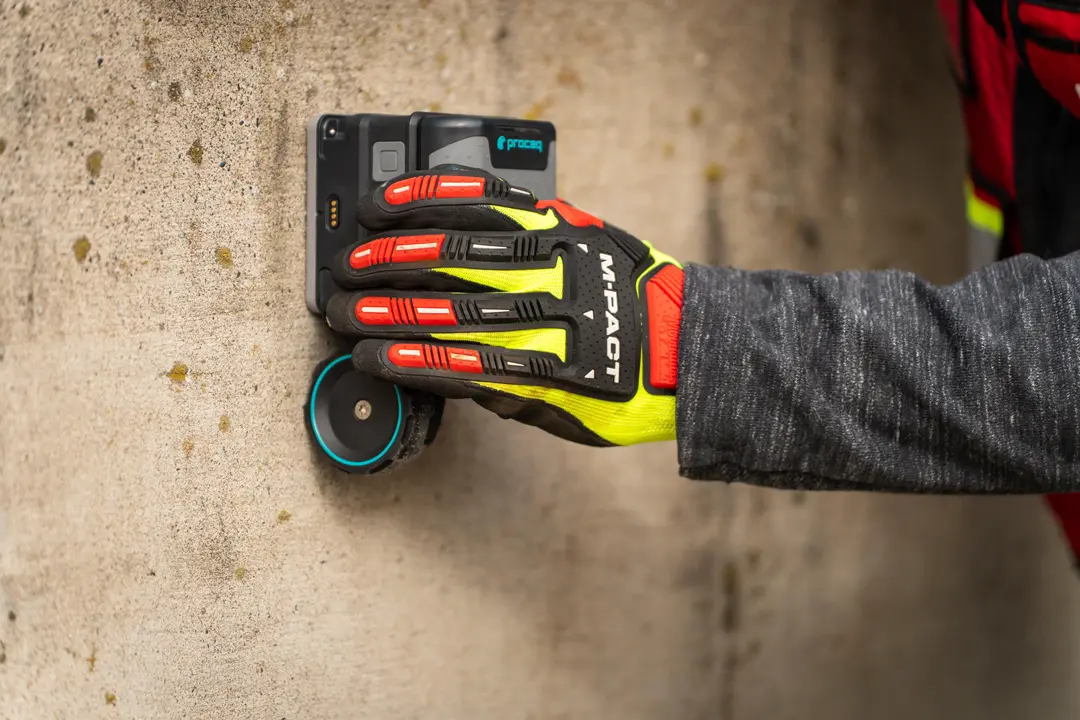
GPR Explained
GPR is a non-destructive evaluation method that involves sending a radio signal into a structure and reading the “bounce” of that signal off any material it encounters. The interactions between the radio signal and these anomalies are shown as hyperbolas that, when interpreted by an experienced GPR technician, indicate what type of material has been located.
Like X-ray, GPR is a non-destructive method for investigating concrete structures.
Unlike X-ray, GPR emits no harmful radiation, which means you don’t need to establish safe zones around where scanning is being conducted.
GPR only requires access to one side of a slab, and it can quickly and easily evaluate large and/or hard-to-reach areas. It can provide clear, definitive imaging of the interior of a concrete slab – but only when operated by a properly trained technician.
GPRS Project Managers are trained using the industry-leading Subsurface Investigation Methodology, or SIM, which requires 320 hours of field training and 80 hours of classroom training in concrete scanning and utility locating processes.
During this training, our Project Managers experience real-world scenarios that prepare them for even the most unique challenges they encounter in the field.
In the hands of GPRS Project Managers, ground penetrating radar can provide you with a clear view inside even the most congested concrete slabs.
It’s our confidence in our SIM-certified Project Managers that led us to introduce the Green Box Guarantee, which states that when we place a Green Box within a layout prior to anchoring or coring concrete, we guarantee that the area will be free of obstructions.
If we’re wrong, we agree to pay the material cost of the damage.
While both GPR and X-ray imaging are considered non-destructive concrete inspection methods, GPR is safer, faster, more efficient, and more accurate than X-rays.
And GPRS has proven that we are the premier company for scanning concrete using GPR.
Our Project Managers take a collaborative approach to their work, tailoring our services to meet your project’s specific needs. In addition to concrete scanning, we also offer utility locating, 3D laser scanning, video pipe inspection, leak detection, and mapping & modeling services to help you fully visualize your job site above and below ground.
All the data our Project Managers collect on your site is uploaded for you into SiteMap®, our industry-leading infrastructure management platform that gives you instant access and control over your vital facility information.
From skyscrapers to sewer lines, GPRS Intelligently Visualizes The Built World® to keep projects on time, on budget, and safe. With over 500 Project Managers strategically stationed across every major U.S. market, our services are always at your fingertips.
What can we help you visualize? Click the links below to schedule a service or request a quote today!
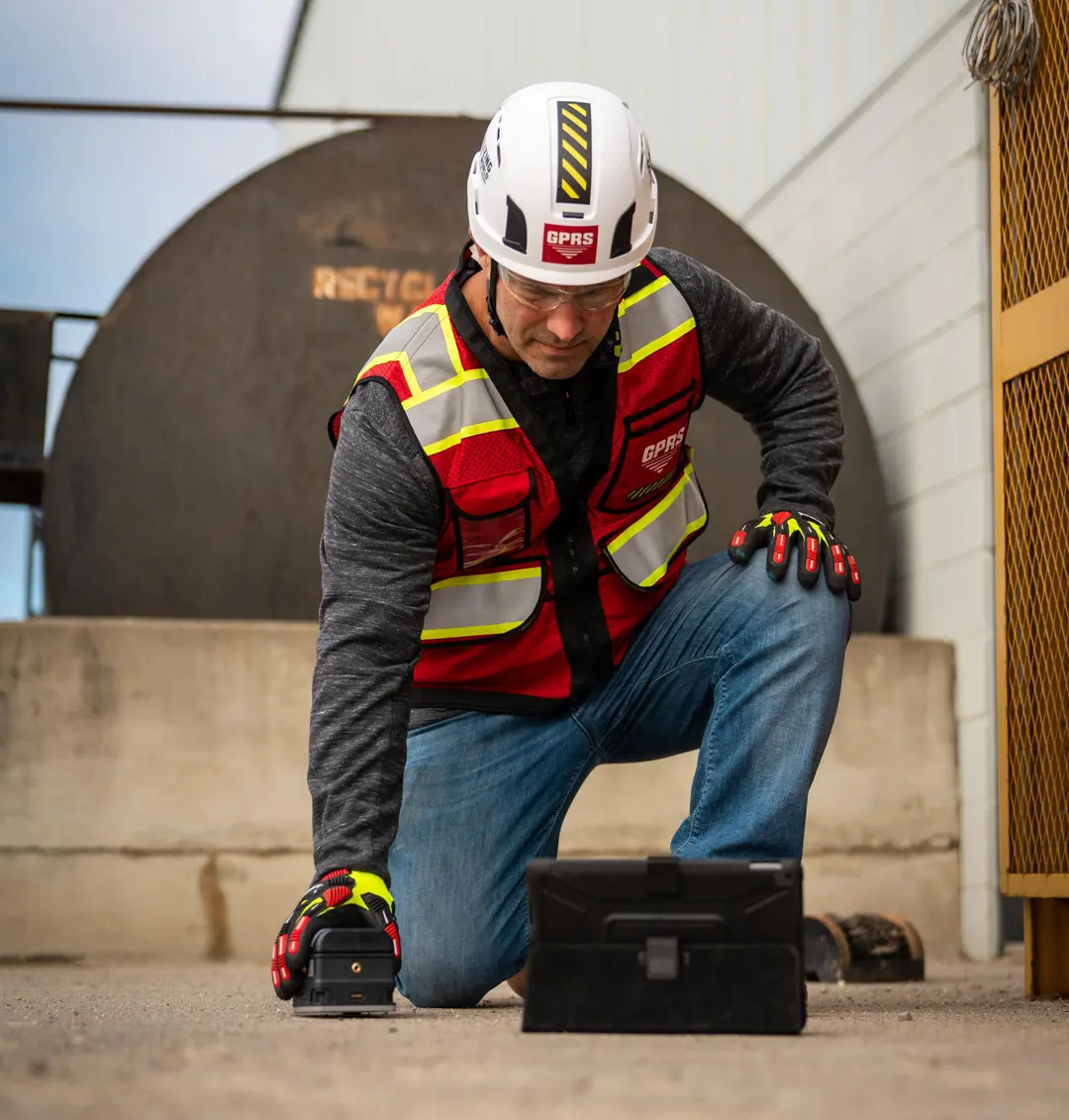
People Also Ask:
How long does it take to scan concrete with GPR?
Large areas can be easily and quickly scanned with the state-of-the-art GPR units utilized by GPRS Project Managers.
Our standard layout for a typical core drilling location is 2’x2’. It usually takes about 10 minutes to scan and mark an area this size.
How accurate is GPR when scanning concrete?
When operated by SIM-certified Project Managers, GPR is proven to be 99.8%+ accurate in determining what is embedded within a concrete slab.
It’s our confidence in the industry-leading accuracy of our Project Managers that led us to introduce the Green Box Guarantee, which states that when we place a Green Box within a layout prior to you anchoring or coring concrete, we guarantee that the area will be free of obstructions.
If we’re wrong, we agree to pay the material cost of the damage.
Why do I need concrete scanning?
There are countless subsurface hazards that need to be accounted for prior core drilling or saw cutting concrete.
Failing to have a concrete scanning company clear the area you intend to cut or core could result in costly and potentially dangerous subsurface damage.
Can GPR determine the difference between rebar and electrical conduit?
Yes, when operated by qualified technicians such as our SIM-certified Project Managers, ground penetrating radar can accurately differentiate between rebar and electrical conduit in most cases.
Additionally, GPRS Project Managers use electromagnetic (EM) locators in concert with GPR to determine the location of conduits in the concrete. If we can transmit a signal onto the metal conduit, we can locate it with pinpoint accuracy. We can also find the conduit passively if a live electrical current runs through it.
The combined use of GPR and EM locators allow us to provide one of the most comprehensive and accurate conduits locating services available.