Construction Supervisors, Project Managers, and General Contractors have all heard the phrase, “Sweeping the trash forward.” It refers to the practice of pushing problems down the line until they can be dealt with.
For instance, if the concrete was already set before you found out you had to move plumbing fixtures, you would push that problem – the trash – down the timeline, adding time, expense, and the potential for costly damage to your bottom line.
Sweeping the trash forward means that you often end up feeling like the garbage man instead of the leader you were meant to be. But it doesn’t have to be that way.
There are serious, field-tested solutions that can take you off trash duty and return you to being a leader that pulls your project forward. Many of the strategies that can help you are found in Lean building principles.
GPRS is proud to sponsor the Lean Builder Workshops where you can learn “Builder’s Lean” methods to immediately transform your projects.
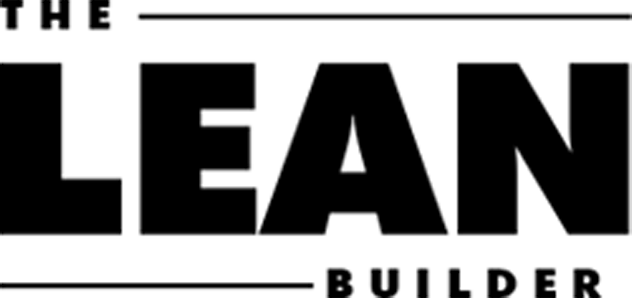
What is Lean Construction?
Lean construction is a set of transparency and accountability strategies that are designed to “maximize stakeholder value while reducing waste on any site” says the Lean Construction Institute. While Henry Ford is often credited as the “grandfather of Lean construction” due to his innovative Model T assembly line technology, the construction industry can look to one of the most famous buildings in the world, The Empire State Building, as the first modern Lean project.
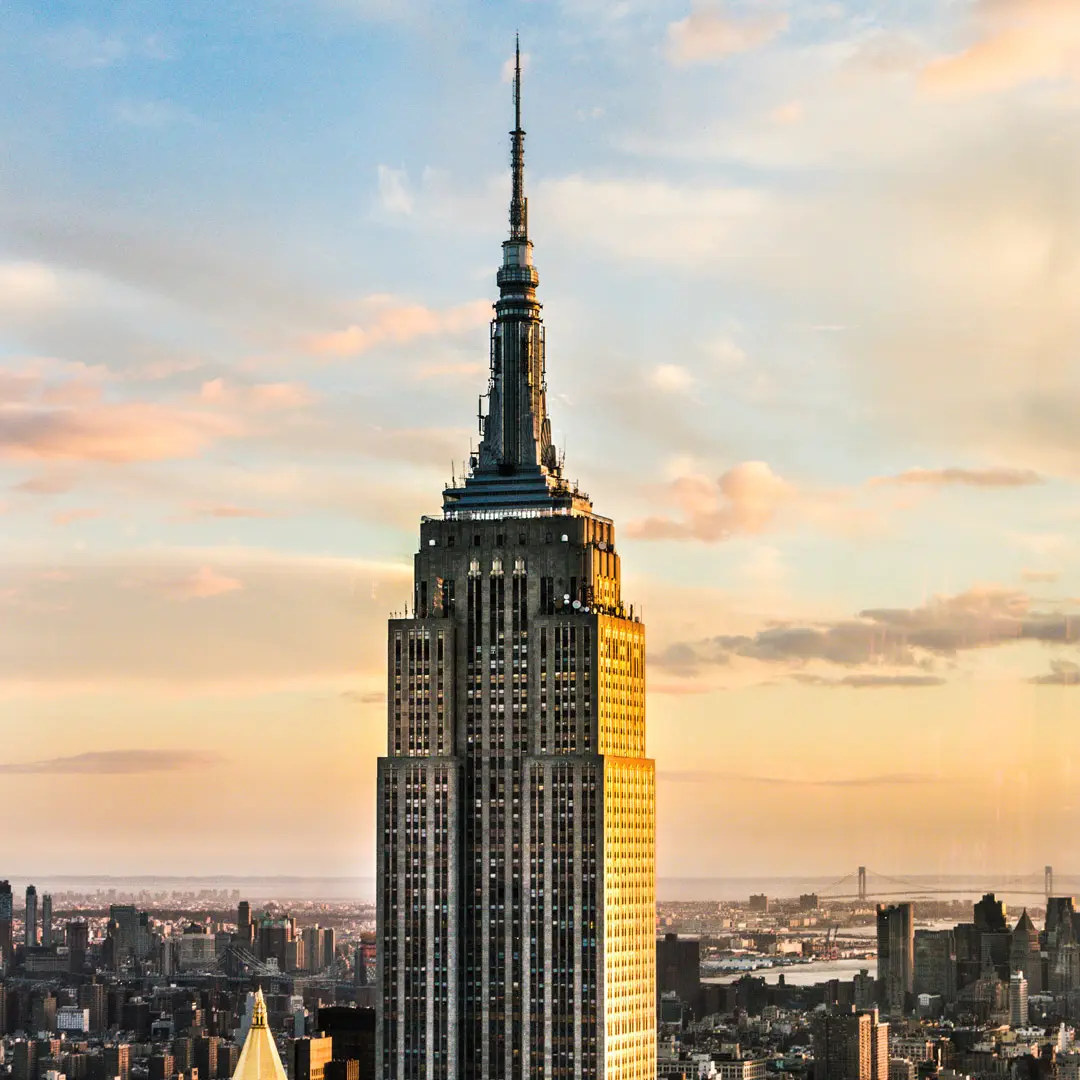
The famous New York City landmark came in ahead of schedule and under budget. When was the last time you could say that about a project? The Lean construction ideal is to create a collaborative environment with all your subcontractors where everyone is as bought in to the outcome as you are.
That sounds nice, but what does it mean. How do you, a person who is trying to wring every ounce of possible production from your team, make that happen?
How Do Lean Construction Principles Work?
If there is a watchword for Lean construction, it is integration. The LCI’s Integrated Project Delivery System (IPD) helps align everyone from the stakeholders to the designers to the entire construction and subcontracting team to improve outcomes and eliminate waste.
In fact, if you could boil Lean methodology into two simple principles, they would be:
- Eliminate waste
- Continually improve
That requires a lot of trust from all parties involved, and can result in a Lean contract, in which the parties agree to share profits and savings so that everyone “has skin in the game,” but it is not necessary to commit to a profit-sharing model to embrace Lean Construction on your jobs.
4 Simple Steps to Using Lean Construction on Your Job
Eliminating the “trash” and creating an environment where everyone is invested in pulling the project forward as efficiently as possible can be accomplished in four easy steps.
Step #1: The Daily Huddle: Instead of unproductive and overlong subcontractor meetings where complaining about each other is the theme, you can institute a few simple ground rules to streamline your workflow plan and get everyone on board at the start of each day, and it’s a lot simpler than you may think.
- Keep it short
- Start on time, end on time
- No phones
- Everyone on their feet
- Create a simple 5-question agenda/routine
- Stay on track
- Involve everyone
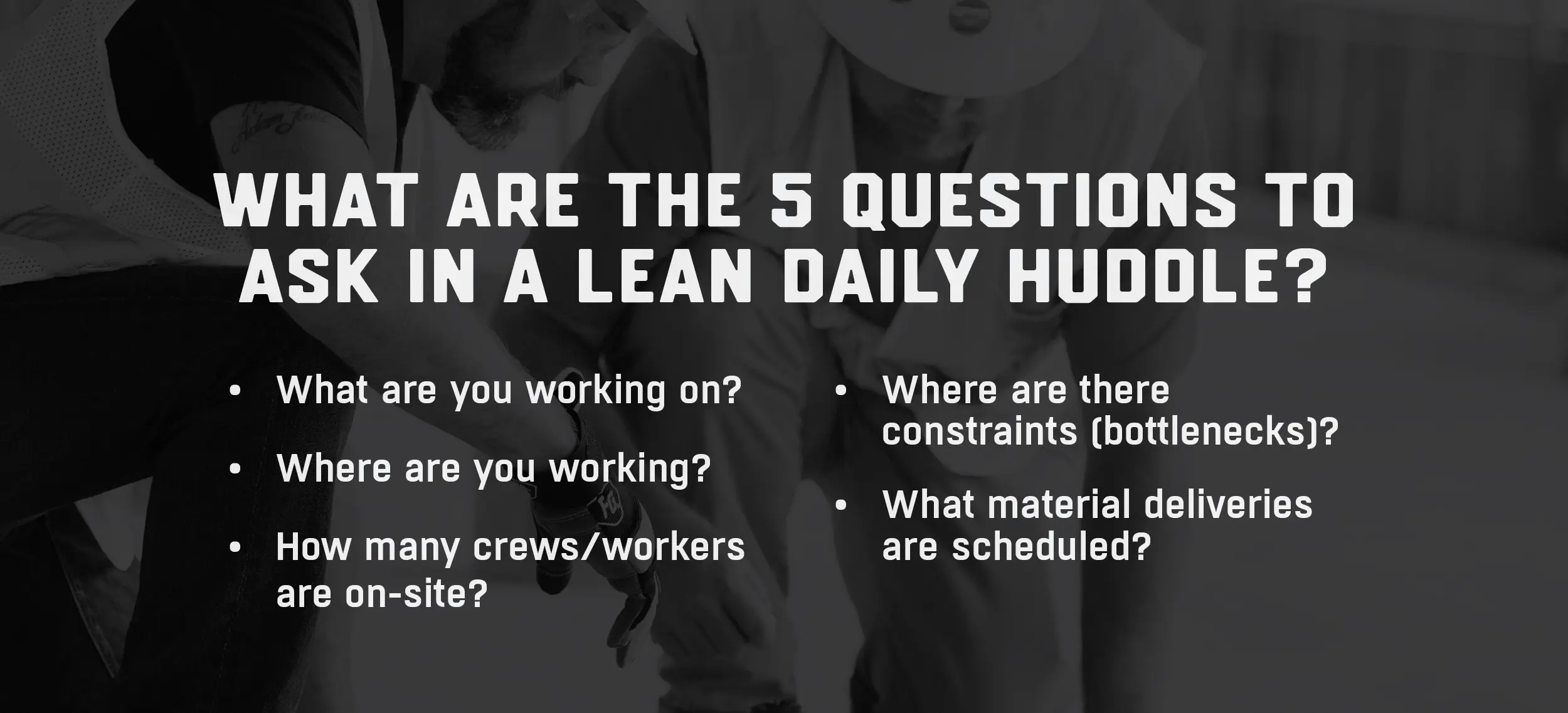
Step #2: Communicate Visually. People learn and retain in different ways, and the surest way to make sure everyone knows what is happening is to create visualizations of the workflow and plan. The simplest way to do this is to create laminated floor and elevation plans, and to outline the flow with dry erase markers so everyone can see where each crew, priority, and delivery will be on any given day. A more advanced version can include an inspection board, deliverables board, and a detailed virtual 3D BIM model that can be shared among teams.
Step #3: Managing Constraints. “Constraints” refers to anything that may slow or stop project progress. Usually, bottlenecks occur because your team has failed to answer one of the following questions about a project phase: What, Where, Who, and When.
You can break each phase of construction down into a simple bottleneck board, where all your team members can see what needs to be done, where it’s being done, who is doing it, and when it is being done/needs to be done by.
Step #4: Pull Planning. This is where all the pieces come together so that you are no longer a slave to miscommunication, delays, and reworks because your leaders in the field – the people actually closest to the work – are who create the plan with you. In short, it moves you from the old model of master scheduling into a Leaner, cleaner, and easier to implement phase scheduling model. You can learn more about pull planning and Lean construction at one of the upcoming workshops GPRS is sponsoring around the country.
Pull planning is at the heart of this streamlined Lean approach. It may seem like a lot to master at first, but once you’ve implemented the pull plan, you can communicate expectations, constraints, and unexpected outcomes much more smoothly.
BONUS! Step #5: The Last Planner System. As featured in the book The LEAN Builder, the Last Planner System in Lean construction is what pulls all the above steps into a streamlined, easy to implement system that can help you get full buy-in from your subs and is sustainable for the life of the project.
All the services GPRS provides, from utility locates to concrete imaging, 3D laser scanning, video pipe inspection, leak detection, and the customized work of our in-house mapping & modeling team support Lean construction initiatives by Intelligently Visualizing the Built World™ above and below ground for our customers. Our work can create the basis of your Lean communications on site, and with a 99.8% accuracy rate and millimeter-accurate precision on 3D laser scans and the drawings, maps, and models they produce, we can work with you from pre-planning through O&M to keep you on time, on budget and safe.