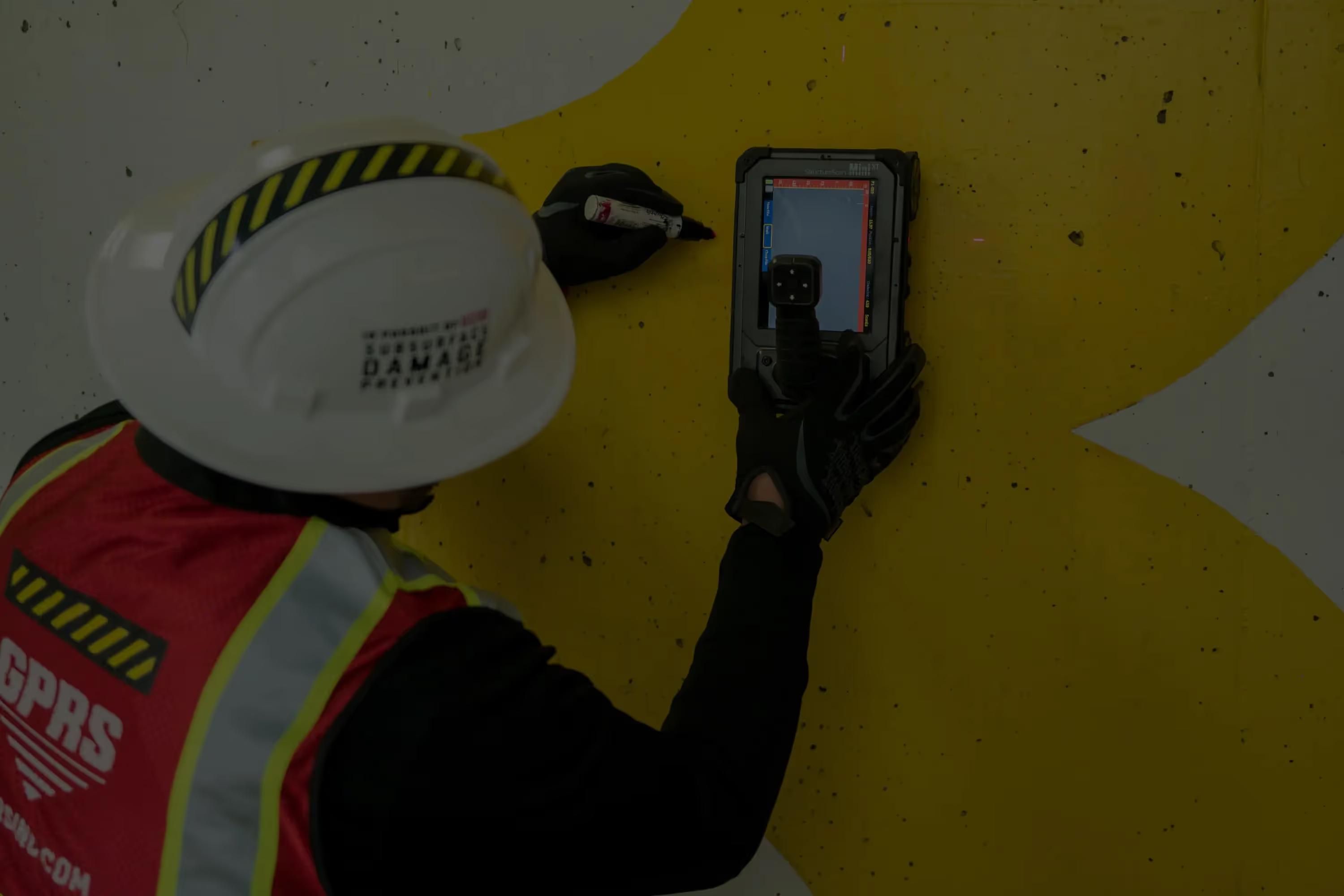
How & Why Do You Scan Concrete?
Concrete scanning, or concrete imaging, is a vital step to take when preparing to cut, core, or drill into a concrete structure.
This process primarily involves the use of ground penetrating radar (GPR) technology. This non-destructive detection and imaging method involves sending a radio signal into a structure and reading the “bounce” that occurs when the signal encounters a material. An experienced GPR technician interprets this reading to determine the type of material located.
By hiring a concrete scanning professional to investigate your concrete slab prior to beginning these destructive activities, you ensure that potentially hazardous obstructions such as embedded utilities, rebar, and post tension cables are located so they can be avoided.
Why is Concrete Scanning Important?
The average cost of a single utility strike is $56,000. But the biggest risk of not scanning concrete prior to coring, drilling, or cutting is not to the pocketbook, it’s to the workers performing the task.
Hiring a professional concrete scanning service to scan your slab ensures all major components within that structure are marked out. This helps prevent damage that could prove costly, and even fatal.
Precision concrete scanning:
- Maintains the structural integrity of the concrete
- Helps you to avoid costly repairs during the project
- Reduces personal injury risk
- Reduces the risk of damage to utilities, rebar, post tension cables, pipes, and conduit
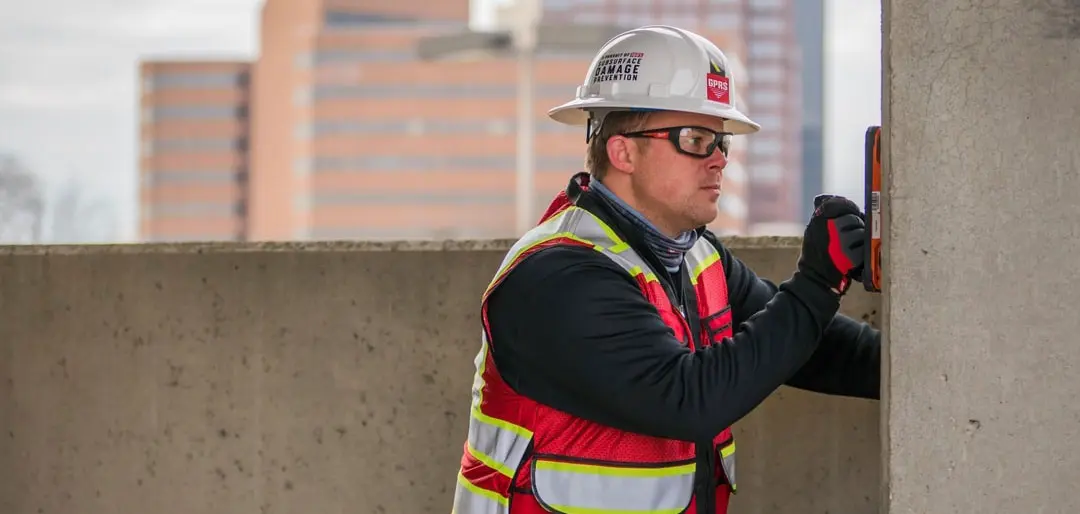
Why Use GPR Instead of X-Ray for Precision Concrete Scanning?
Both GPR and X-Ray are non-destructive ways to see inside a concrete slab. Both can find rebar, conduit, post tension cable, and other buried hazards.
GPR, however, requires access to only one side of a slab or structure. X-Ray requires access to both sides – one side for placing the radioactive material, and the other for placing a receiver.
Today’s GPR units are handheld and wireless, fitting anywhere they’re needed on a job site and able to transmit their findings directly onto an iPad or other digital device for easier scanning and measuring.
X-Ray units are not only larger than GPR equipment, but they also require a significant amount of set-up. A job site also needs to be cleared of all personnel except the X-Ray technician while scans are taking place, to mitigate the risk of irradiating someone.
GPR’s safety, speed, efficiency, accuracy, and cost effectiveness make it the clear choice for precision concrete scanning.
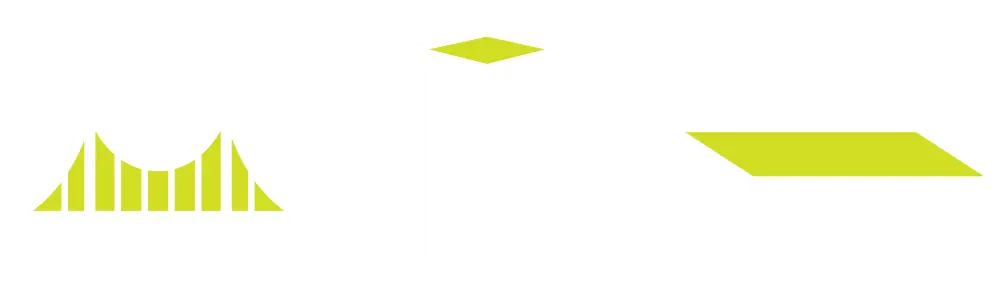
CONCRETE SCANNING IS USED TO INVESTIGATE
Any concrete structure, including beams, bridges, ceilings, columns, decks, floors, pylons, roofs, slabs, tunnels, and walls.
GROUND PENETRATING RADAR
GPR has established itself as the primary tool for precision concrete scanning. This non-destructive detection and imaging method helps construction professionals identify what lies within and under a concrete structure before conducting any excavation or renovation activities on that slab.
GPR involves sending a radio wave from a receiver into a concrete structure, where the wave will “bounce” off any material it encounters. Those bounces are then displayed in a reading as parabolas, and a professional concrete scanning technician can interpret that data to tell you what was found and where exactly it is located.
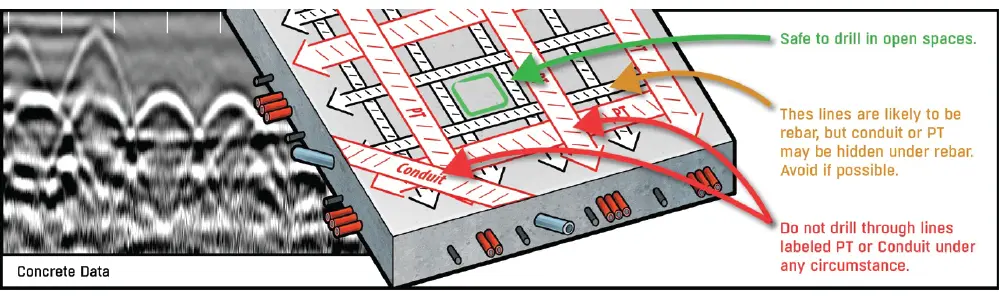
The effective range of GPR is determined by the electrical conductivity of the earth or concrete being scanned, the transmitting frequency, and the radiated power. Higher frequencies offer higher resolution, but they can’t penetrate the ground or concrete slab as deep as lower frequencies, and vice versa.
Additionally, GPR can scan deeper in old concrete than in a newly poured slab or structure. This is because the moisture present in newly poured concrete is more difficult for GPR to penetrate.
The effectiveness of GPR equipment still relies heavily on the knowledge and experience of its operator.
The best concrete scanning professionals complete an intensive, months-long training regimen. They receive 320 hours of mentored field training. They log 80 hours of classroom training, where they tackle real-world scanning scenarios in a safe and structured environment. All this training ensures that these professionals can properly interpret the readings provided by a GPR unit.
How Much Time Does Concrete Scanning Take?
The time required for a concrete imaging project depends on various factors including the amount of space to be scanned, the client’s needs, the type of slab and amount of reinforcement present, and more.
Typically, however, GPR scans are fast. Data is sent from the receiver to a wirelessly connected iPad or other tablet instantaneously, and a GPRS Project Manager can interpret that data immediately and provide same-day deliverables to the client.
Can GPR Identify the Difference Between Subsurface Obstructions?
Not on its own. The data provided by a GPR scanner needs to be interpreted by a qualified technician, such as a GPRS Project Managers.
Each member of our elite team of over 400 Project Managers has completed the industry-leading Subsurface Investigation Methodology (SIM) program. This standard operating procedure includes specifications for underground utility locating and concrete scanning.
SIM focuses on a three-step approach to achieve the most accurate results when performing non-destructive subsurface testing:
- The need for experienced technicians
- The understanding and proper utilization of applicable technology
- The adherence to proven methodologies
SIM establishes the industry standard that concrete scanning currently lacks. The use of SIM ensures site safety, and limits damage to subsurface and structural elements.
SIM-certified GPRS Project Managers receive a minimum of four weeks of field mentoring and then 80 hours of classroom training followed by an additional four weeks of field mentoring prior to being released into the field under the supervision of a Senior Project Manager.
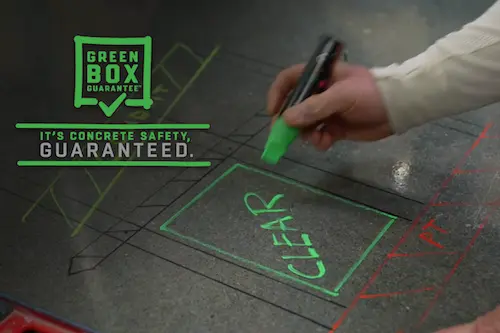
GPRS Green Box Guarantee
It’s our confidence in our SIM-qualified Project Managers that led GPRS to introduce the Green Box Guarantee. When we place a Green Box within a layout before your crew anchors or cores concrete, we guarantee that the area will be free of obstructions. If we’re wrong, we pay the cost of the damage.
SAFETY
- Every time a concrete slab is drilled, cored, or cut into, the equipment operator, nearby team members, and even community members in the surrounding area are at risk of injury or death.
- Striking an electrical line could lead to fatal electrocution. Severing rebar or post tension cable could cause instant structural failure.
- GPRS’ Green Box Guarantee is designed to mitigate these risks, giving you and your team confidence that the area of concrete they’re working in is free of potentially dangerous obstructions.
COST SAVINGS
- Tens of thousands of dollars are also on the line every time concrete is penetrated.
- The average cost of a single utility strike is around $56,000. There’s the initial cost of repairing the damage, then additional hidden costs of the work stoppage and other crew costs.
- These costs can be mitigating by hiring a precision concrete scanning company like GPRS to find these utility lines and other obstructions before you can hit them.
EFFICIENCY
- GPRS Project Managers can clear dozens of cutting/coring areas daily with an exemplary level of accuracy. In fact, our company has over a 99.8% accuracy rate on over 350,000 jobs completed since our founding in 2001.
- Demolition work can occur must faster if cutting, coring, and drilling activities are taking place through concrete that is guaranteed to be clear of obstructions. By preventing the delays caused by line strikes and damaged reinforcement, contractors can keep their schedules on track and reduce the need for change orders and budget overruns.
CLEAR COMMUNICATION
- The Green Box Guarantee is placed directly on a coring location by our Project Managers, who explain the parameters of the guarantee to the client during a walkthrough of the site after our job is completed. We value collaboration in our relationships with our clients; we want to tailor our services to fit your needs, and we want to make sure you walk away confident in the work we completed.
- Cutting or coring concrete poses the inherent risk of striking rebar, conduits, and post tension cables. Strikes are costly to repair, and they can lead to injury or even the death of your employees or community members near the project. GPRS’ Green Box Guarantee helps keep people safe, and your projects on time and on budget.
Frequently Asked Questions About Concrete Scanning
Can Ground Penetrating Radar Scan Concrete Slab-On-Grade?
Yes, and this is another way in which GPR has proven superior to X-Ray for precision concrete scanning. The use of X-Ray scanning is limited to elevated slabs because it requires access to both sides of a slab – one side to place the radioactive isotope, and the other to place a receiver.
GPR only requires access to one side of the concrete slab.
Can GPR Differentiate Between Rebar, Post Tension Cable, Electrical Conduit, and Other Embedded Material?
Not on its own. However, a highly trained and experienced concrete scanning technician – such as a GPRS Project Manager – can interpret the data provided by a GPR scanner to determine what exactly has been found and precisely where it is located.
These findings are then marked onto the concrete slab, so that our clients know what has been found and can make an educated decision on where they will core, drill, or cut.
How Accurate is GPR?
While external factors such as the age of the concrete being scanned can play a role, GPR has proven to be very accurate. Its horizontal accuracy is typically +/- ¼” to the object’s center in concrete, and it can identify the depth of each object in concrete to within +/- 10-15%.
In an abundance of caution, our Project Managers always recommend clients cut, drill, or core one to two inches from any line marked as an obstruction. While GPR cannot typically provide the exact diameter of a subsurface obstruction, skilled technicians such as our Project Managers can provide a very accurate estimate of this measurement.
Is GPR safe to use?
Yes. Unlike with X-Ray, GPRS poses no health risks to the operator or anyone in the surrounding area. GPR scanners operate using radio waves, and typically produce a smaller power output than most cell phones.
GPR is also non-destructive and soundless, making it easy to operate without disrupting any other jobsite activities in the surrounding area.