Precision concrete scanning and imaging are at the heart of GPRS. We’ve been leading the industry with ground penetrating radar (GPR) and electromagnetic (EM) imaging as a concrete scanning company since 2001, so it’s easy to think when it comes to concrete slabs and rebar, we’ve seen it all.
Then a Project Manager in Watertown, Massachusetts discovers something mind boggling, and we’re reminded that innovation is driven by necessity and can change the scope of history.
THE PUZZLE
Jaime Gamache is now a Boston Area Manager for GPRS. In 2020 he was called in to define the structural reinforcement and rebar pattern in the concrete of a pre-World War I munitions factory for The Richmond Group, so it could be renovated into a sprawling health care facility right on the Charles River in Watertown. Richmond’s architects and engineers needed to be certain of the weight-bearing capabilities of the century-old concrete before they began demolition and construction.
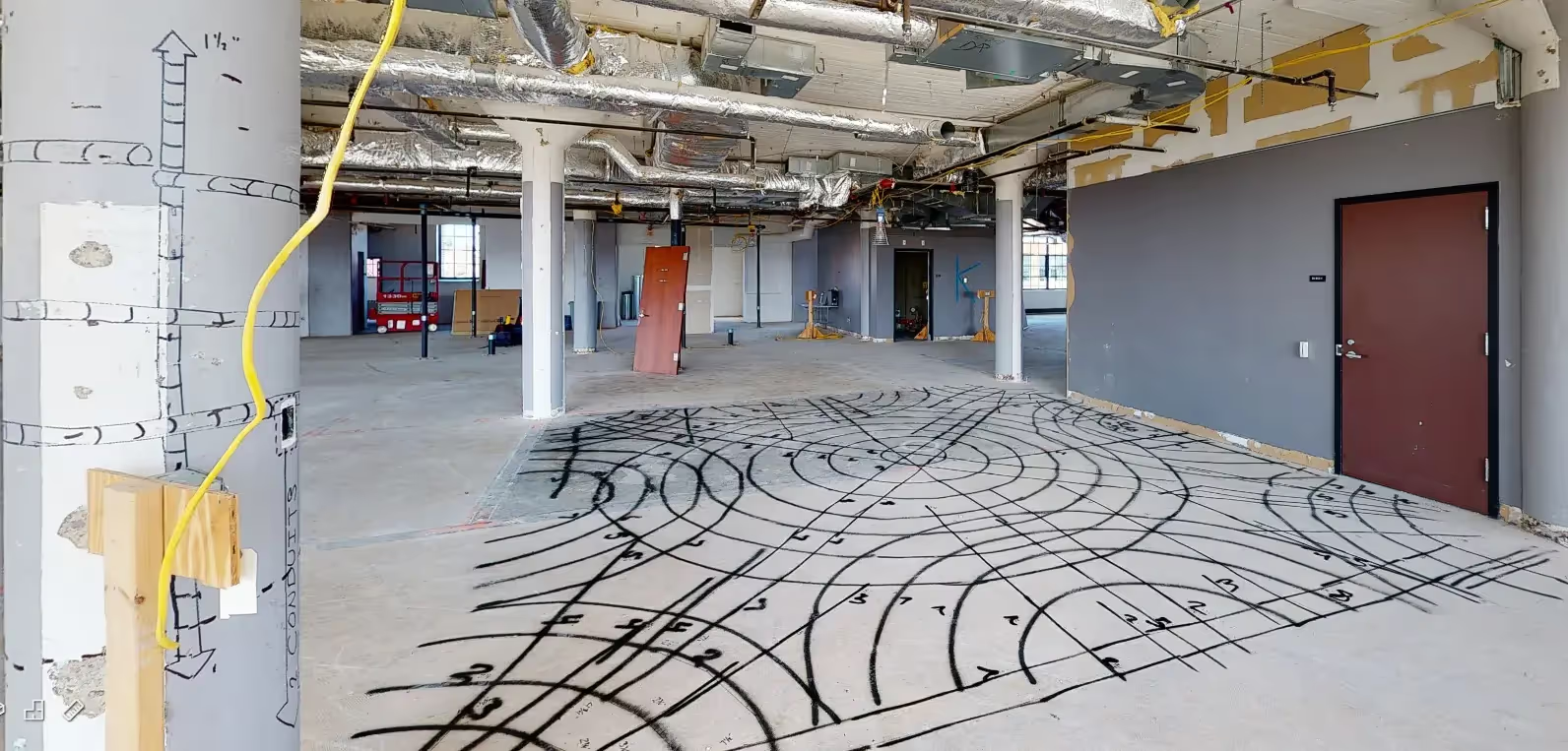
The “cannon factory” Gamache scanned was part of the Watertown Arsenal, one of the first major munitions and manufacturing facilities created by the fledgling U.S. Government, all the way back in 1814. The specific building in question, Building 311, needed to be able to withstand the construction and storage of heavy munitions like carriages for 16-inch seacoast guns, and disappearing, barbette, and railway carriages during WWI, but neither Richmond or Gamache knew that.
“The engineer wanted us to establish the rebar pattern so they could determine how much weight the slab could hold and establish what their process would be with saw cutting and pouring moving forward.” Gamache said.
What he found he described as “putting together a puzzle when you can’t see any of the pieces,” and turned a quick 40x40 scan into a four-day marathon to achieve an accurate measurement of a 20x20 area. Once the pattern was established, there was no need to keep scanning because it was clear the concrete slab could hold nearly anything the new owners might throw at it.
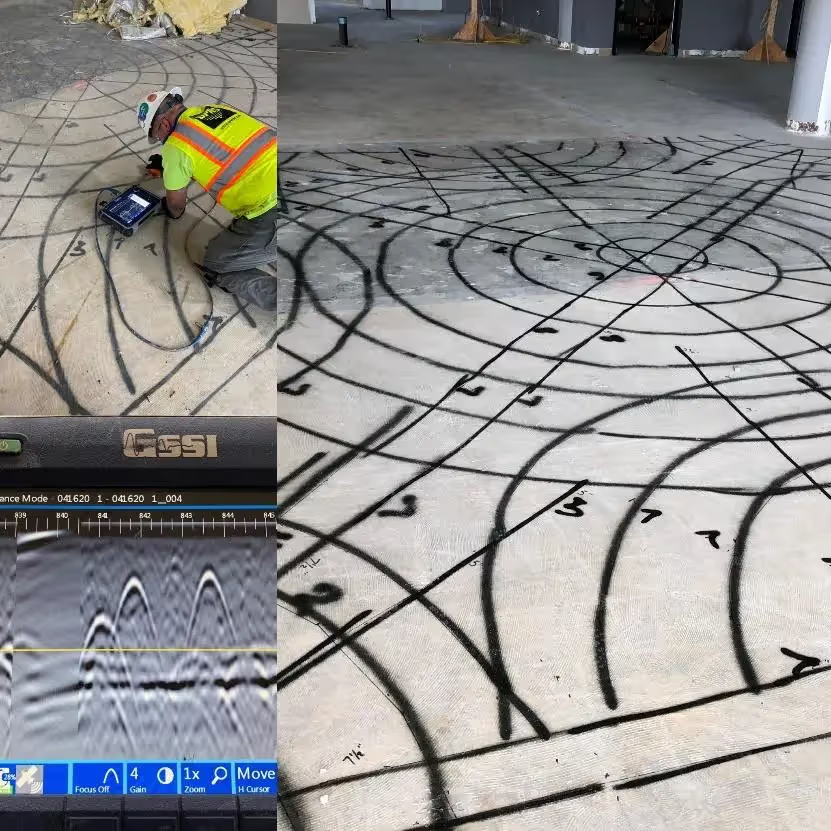
“It took me about a day and a half just to establish the basic pattern, because for three quarters of the first day, I would chase a line that would all of the sudden swerve off to the side. It was actually curving, but I was jumping onto another bar because some were straight and some were curved. I ended up picking one anomaly and chasing it continuously around a circle, attempting not to get lost in the next circle, which was a problem when they crossed. There were actually some places where three rings crossed in the same point,” said Gamache.
THE HISTORY OF THE WATERTOWN ARSENAL
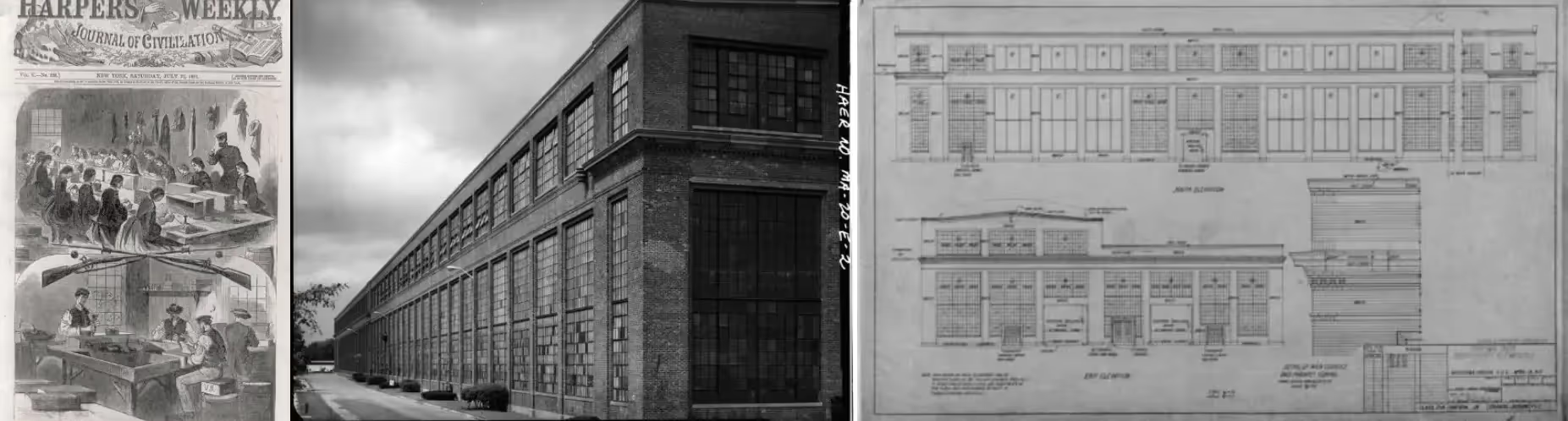
Harper’s Weekly highlighted the Watertown Arsenal during the Civil War • Historical photo of Building 311 • Architectural design for Building 311
During the Civil War, the Watertown Arsenal manufactured cannons and munitions. Building 311 was one of the largest buildings ever constructed when built in 1914 (49 years after the end of the Civil War), and the DOD doubled its size in 1942 to support Allied efforts in WWII with the manufacture and testing of advanced weaponry.
While all of that is fascinating history, what brought it to GPRS’ attention was the incredible rebar pattern embedded in the nearly 12” thick concrete slab. It was unlike anything anyone at GPRS had ever encountered.
HOW TO DEFINE A CIRCULAR OR BENT REBAR PATTERN
The pattern Gamache found in the rebar was an extremely rare example of a circumferential design, also known as the S.M.I. System of flat slab construction. GPRS Field Support Director, Jamie Althauser tracked it down in a white paper on Antiquated Structural Systems and shared it with the Boston Area Manager to confirm his findings.
The S.M.I. System was developed by Edward Smulski, a New York City engineer who patented his rebar pattern in 1916.
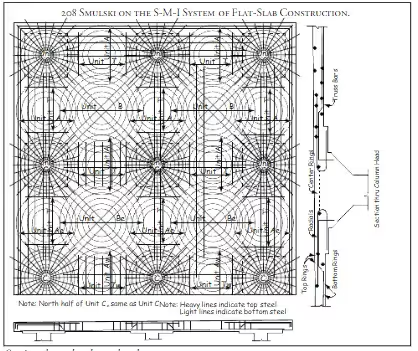
The system is also sometimes referred to as the spiderweb pattern, and combines concentric circles and straight rebar running through them in a starburst pattern. The idea behind Smulski’s system was that it could support more weight than a standard two-way or four-way slab system, where only straight rebar is used.
There is some speculation that his circular bent rebar construction model was “nonsensical,” but the federal government determined it was worthwhile to use in new construction before WWI and used it in Building 311.
Bent rebar is more expensive and complicated to produce, and, according to Kloeckner Metals, almost impossible to remove from the slab when demoing, which may also have led to the downfall of this complex pattern. Another potential reason for its retirement is that it used more rebar than a two-way or four-way pattern, and as the nation veered from WWI into WWII, metals were needed more for munitions than for homeland construction projects.
“It’s supposed to be a pattern that was developed by the military to hold a lot of weight, but it was cost-prohibitive to produce, so that’s why nobody had seen it before and why it wasn’t mass produced,” Gamache continued. He remains the first – and to date the only – GPRS team member to encounter this historic pattern in the field.
If Gamache had not been dedicated to solving the puzzle, The Richmond Group almost certainly would have cut into a whole lot of rebar, causing extensive and expensive damage to the building and their equipment, and endangering the lives of their work crews. It is this level of experienced know-how and dedication that gives GPRS our 99.8% accuracy rate on concrete scanning and imaging and allows us to provide our Green Box Guarantee.
WHAT IS THE GREEN BOX GUARANTEE?
When a GPRS Project Manager scans your concrete slab and provides you with a green box marked “CLEAR,” you know that you can safely cut, core, or drill in that space with 99.8% certainty that you will not hit conduit, rebar, or any other dangerous or costly obstructions.
If you do hit something inside a Green Box, GPRS will pay the material cost to repair it. Period.
It is the professionalism and dedication of people like Jaime Gamache and all our SIM-certified Project and Area Managers that make it possible for GPRS to offer this guarantee as we Intelligently Visualize The Built World™ for our clients and customers.