3D laser scanning is a construction, engineering, and architectural tool often used to document the existing conditions (as-builts) of any structure.
3D laser scanners use LiDAR (light detection and ranging) to measure and record precise locations and distances, ultimately producing a point cloud file. These lightweight and mobile scanners produce highly accurate digital measurements and images quickly and easily for use in construction and engineering projects. That data is invaluable in design, prefabrication, asset management, and facility modifications.
Precision as-built laser scans have huge benefits for construction companies, and industrial LiDAR scanners are portable, can be automated, and are accurate within millimeters.
How Does 3D Laser Scanning Actually Work?
The primary way a laser scanner works is to send light pulses at high speed which reflect off objects and return to the scanner’s sensor (LiDAR). For each pulse, the distance between the scanner and object is measured by determining the elapsed time between the sent and received pulses. Each data point is converted to a pixel with a known x, y, and z coordinate.
Laser scans are taken in multiple positions around a site from varying viewpoints. Millions of data points are captured and processed into a point cloud, creating an accurate 3D as built data set of the site. This all happens very quickly, with some scanners, like our Leica RTC360, capturing and calculating 2 million points per second with 2-4 mm accuracy.
The simplest way to break down how laser scanning works is to talk about what happens when a Project Manager takes a scanner into the field to walk you through the process.
Know What You Need and Why You Need It
Before anyone walks onto the site to be scanned, it is vital to have a clear idea of what the data will be used for. Because while mobile laser scanning is the most efficient way to generate data points for mapping and modeling, it still requires a highly skilled and trained technician and hours or a few days on site to capture the needed data before our engineers can then create custom deliverables like 3D virtual tours, 3D flythroughs, Revit BIM models, CAD BIM models, Mesh models, 2D CAD drawings, and as-built drawings to suit your needs.
For instance, when GPRS is called on to bring our 3D laser scanning services to a historical building for an accurate as built survey, we need a very high-resolution scan to produce a 3D model documenting precise building details for a complete update and restoration project, as we did for the 100-year-old residence hall you see here.
But for a recent survey of a hospital in Marysville, Ohio, the client required a simple 2D CAD drawing of the façade so that their roofing contractor had accurate measurements to fabricate needed soffits and fascia before coming on site. This saved the client and the contractor a lot of time and money by eliminating the need for hand measuring.
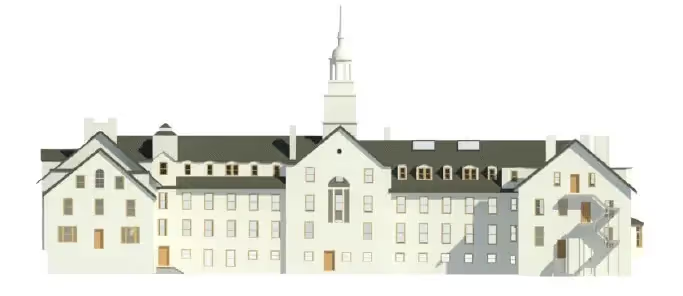
A low-resolution scan of something like the residence hall’s façade would not capture the level of historical detail the client needed, whereas a high-resolution survey turned into a detailed CAD BIM model of the hospital would have been a waste of everyone’s time and resources.
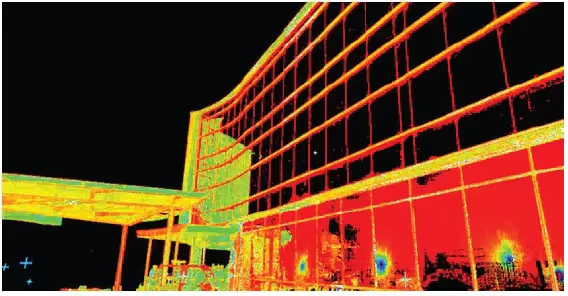
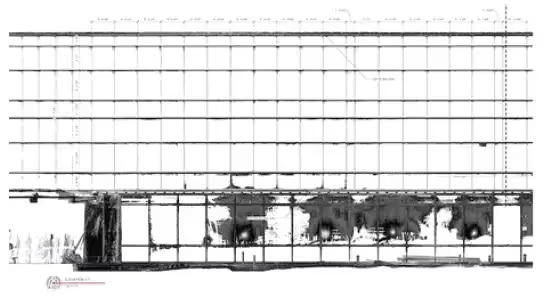
What Are the Applications of 3D Laser Scans?
There is an infinite variety of real-world laser scanning applications. Here are some of the most common ways 3D laser scans are used:
- As-built survey, reality capture, or existing conditions survey
- Construction verification, sequencing, scheduling, and simulations
- Design engineering for facility upgrades or expansions
- 2D and 3D laser map of a building
- Prefabrication
- Clash detection
- Architectural documentation or historical preservation
- Calculating volumes, deformation analysis, and overhead clearances
- Virtual design and construction
- Laser scanning for facility coordination
- Collecting geospatial data
- Creating a digital twin
- Performing advanced analysis to easily aggregate, query, visualize and analyze data in a single 3D model
Knowing which application you need will determine what kind of scan, the necessary resolution of the point cloud and photography, and what kind of maps, models, drawings, or other deliverables your project requires.
How the Technology Works: The Tools of the Trade
GPRS Project Managers use professional grade Leica RTC360 and P-series laser scanners for architectural, engineering, industrial, and construction projects because they offer outstanding range, speed, and data quality.
Leica P-Series ScanStations are accurate within 2-4 mm, can tie to survey control, and have dual axis compensation to help mitigate movement and ensure level scans. The RTC360 is lighter-weight and offers more flexibility of use in the field. Our Project Managers receive formal training from the scanner manufacturer, plus weeks of classroom and field instruction from an experienced scan technician, so they can employ these tools to their full capabilities.
As discussed earlier, most 3D laser scanners work along similar lines. They look a bit like movie cameras on tripods, but they actually contain both a highly sensitive and accurate laser (LiDAR) and a panoramic HD camera to capture the space in real time.
The laser cannot cause harm to the building, people, or animals. It rotates at super-high speed inside its housing, capturing as many as 2 million data points per second, depending on the necessary scan resolution. As the beam interacts with the features of the space relative to the beam, it is recorded as a data point.
The collected data points of a scanned space are called a point cloud. The more points you capture and record, the higher the scan’s resolution and accuracy. But as previously discussed, the resolution is dependent upon the purpose of the scan.
A mobile laser scanner like the Leica RTC360 is capable of complete 360-degree rotation, so it can survey an entire space from a single position or station. However, because the laser is limited by line of sight, it is important to scan multiple stations to ensure you capture every necessary part of a space.
Scan & HD Photography In One
Once the Project Manager has scanned the area, the camera can then be automatically tasked with capturing an almost instantaneous panoramic high definition (HD) photo of the space. The RTC360 can create an HD photo in 60 seconds once the laser is finished with its work. And thanks to Leica’s visual inertia system, when the scanner is repositioned, the laser and camera can adjust automatically to integrate the data from every new location into the survey.
As each position’s scan is completed, a reduced data set that includes a point cloud and image is made instantly available to the Project Manager via a tablet or mobile device where he can then annotate, tag, add additional eld photos, and even record audio messages on to document his eld notes on the point cloud survey, so that nothing is lost or left to memory.
Once the full survey is finished, the higher resolution point cloud, photos, and the Project Manager’s notes are then sent to our talented and skilled engineers who register and process the point cloud data into whatever variety of deliverable best suits your needs.
As GPRS Director of Laser Scanning, Ryan Hacker, shared in a recent interview,
“This technology is the future, and we’ll see more and more uses for it going forward.”
How do you want your future to look? Learn how GPRS can help you Visualize Your Built World™.