GPRS partnered with two renewable energy companies constructing an offshore wind farm to verify that the prefabricated components of several wind turbines meet the design requirements specified. 3D laser scanning captured the exact dimensions of the components with 2-4 mm accuracy. Component verification eliminated assembly and performance problems and saved re-work, delays, and costs.
A 3D laser scanner maps millions of data points using LiDAR technology to create a high-resolution, geometrically precise point cloud. The result is a complete and accurate set of dimensional information that can be used to verify that the prefabricated components are in tolerance to the design drawings. The definition of tolerance is the acceptable variant for any specified component to achieve a proper function. The wind turbine manufacturer completed this tolerance analysis to verify that the components’ dimensions were correct, so they could be assembled without any problems and function as desired.
“This project really showcases the technical expertise we possess,” said Michelle Colella, Mapping & Modeling Manager for GPRS. “The point cloud from 3D laser scanning provided millimeter-accurate x, y, and z coordinates, the precise data needed to compare the prefabricated components against the design model. We also created 2D CAD drawings and 3D BIM models to document the dimensional details and deviation between the design model and actual component. The critical dimensional analysis eliminated rework and ensured that the components will precisely fit together and the wind turbines will function properly.”
How Are Offshore Wind Farms Constructed?
Both clients on this project develop, construct, and operate offshore wind farms. The goal of this project is to produce enough clean energy to power over two million American homes.
An offshore wind farm is made up of a number turbines spread out over a wide ocean area. Each one is firmly affixed to a concrete foundation on the ocean floor, with a tower that extends up into the air and blades that harness the wind speed.
The construction project is completed by a team of highly skilled wind turbine technicians. To construct a wind turbine, the components are prefabricated onshore and installation crews assemble the components at sea. Vessels carry the components to the ocean site with crews of technicians who will live on the service vessel for two weeks at a time to build the wind turbines.
It is important that the prefabricated wind turbine components will easily fit together during installation. The crews cannot afford to troubleshoot installation or technical problems or add additional travel and time at sea.
The offshore construction begins with the installation of fixed-bottom monopile foundations in shallow ocean water. According to Orstead, a leading U.S. clean energy company, “To install monopile foundations, they’re first loaded onto an installation vessel which sails out to the wind farm site, stabilizing itself using dynamic positioning systems. An onboard monopile crane is used to lower the foundations into the sea, where they’re driven into the seabed using a hydraulic hammer.”
The remaining components are brought out to sea to be added to the foundation. The installation crew uses a crane to place a steel turbine onto the foundation. The nacelle and rotor are installed on top of the turbine tower. Then the blades are lifted and installed one by one by bolting them onto the rotor. Cables are connected from the foundation of the turbines to the substation. Each wind turbine sends the power it collects through cables under the ocean floor to an offshore substation.
The substation is located out at sea within the offshore project site. An offshore substation consists of two parts: the foundation and the topside. The foundation is installed in the same way as the offshore wind turbine foundation. The topside is a steel platform that is constructed and tested onshore, and then transported to the site to be placed on the foundation.
The substation collects the power generated by the turbines through inter-array cables, where it then transforms the power to a higher voltage and sends it to shore through an export cable. The export cable transports the power inland – a process known as making landfall. On land, the electricity is fed into the grid and distributed via power lines to the homes and businesses that need it.
What is 3D Laser Scanning’s Role in Dimensional Verification?
Imagine shipping wind turbine components on a vessel and using cranes to lift and assemble these massive structures at sea amongst high waves. The installation is an intense and massive technical undertaking. That’s where GPRS came in to help. GPRS partnered with the two renewable energy companies to verify that the prefabricated components were constructed in tolerance to the design drawings. With 3D laser scanning, rework can often be avoided with accurate as built data identifying deviations from the design, so components can be altered before assembly.
GPRS Project Managers laser scanned two components of several wind turbines to verify that the prefabricated components were constructed in tolerance to the design drawings. First, the fixed-bottom monopile concrete foundations were 3D laser scanned to confirm that the dimensions matched the design created by the engineers. Second, the substation topside steel platforms were laser scanned to provide the client with accurate as built dimensions. Laser scanning is the most accurate form of measurement available, delivering 2-4 mm dimensional accuracy for the wind turbine components. Dimensional verification reduced delays, clashes, change orders, and other unforeseen challenges for the technical team during installation.
GPRS held a project kickoff meeting to review the project and discuss objectives before beginning work. Laser scanning was performed onshore before the components were shipped out to sea on vessels for installation to verify dimensional accuracy. The Leica P40 ScanStation and the Leica RTC360 laser scanner quickly captured the 3D geometry of the wind turbine components. The GPRS Project Manager completed many mobilizations to scan the components after they were manufactured and assembled.
Which Wind Turbine Components Were 3D Laser Scanned?
The GPRS Project Manager 3D laser scanned two components of several wind turbines:
1. Fixed-Bottom Monopile Concrete Foundations
GPRS used 3D laser scanning to capture the dimensions of the precast concrete foundations and conduct CAD comparison to verify that they were in accordance with the design plan.
- Data from the laser scans showed that many of the actual dimensions of the turbines’ concrete foundations exceeded the thickness specified in the design model.
- The Mapping & Modeling team used 2D CAD drawings to document the dimensional details of the concrete foundations and Excel sheets to summarize the deviation between the design model and actual concrete foundations.
- While a thicker concrete cross section will make the concrete foundations stronger and will not need adjustment, it does add weight. So, the companies and technicians must assess when shipping on a vessel and lifting it off the vessel to place on the ocean floor.
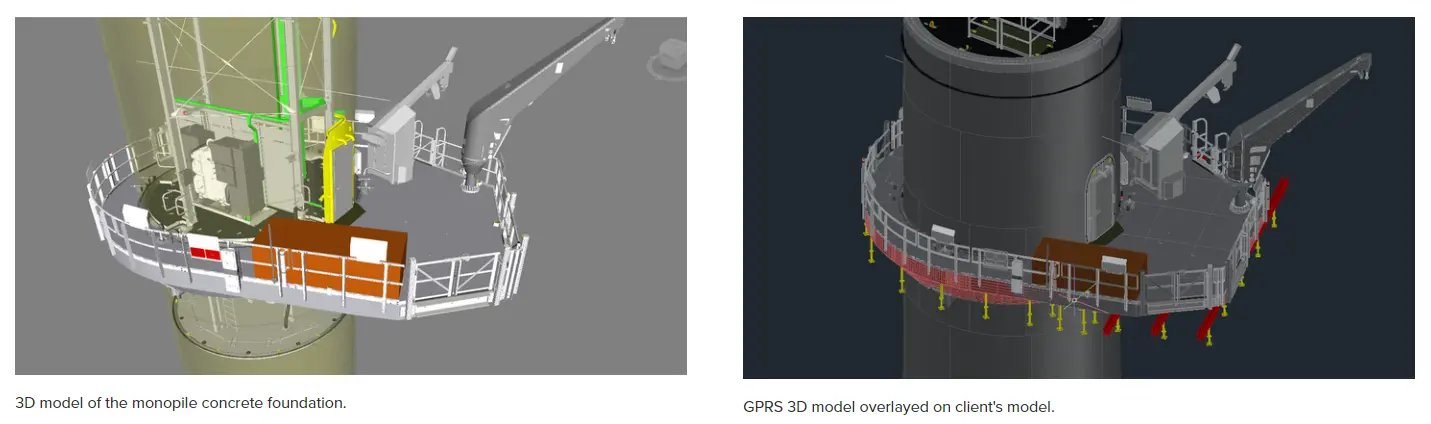
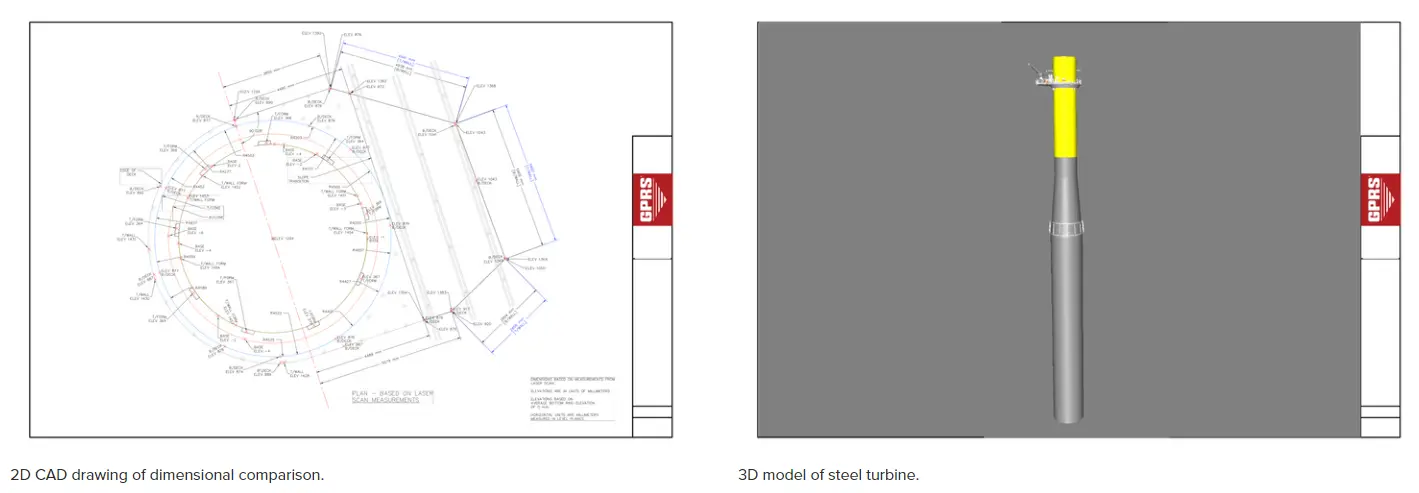
2. Substation Topside Steel Platforms
GPRS used laser scan data to provide the clients with accurate dimensions of the steel platforms for the wind turbine.
- The platform contained three distinct levels separated vertically by steel columns. Each level is constructed of layers of structural steel and topped with a walking surface.
- The clients requested dimensional information for all three levels, and a report of the maximum outside diameter of the structure for each of the three levels.
- For each level, the clients required precise dimensions for the intersecting support centerlines, diagonal values, the vertical distances between the supports, and the horizontal and vertical position of the fixed ladder.
- They also requested dimensions of the lowest possible point of the lower column to the highest point of the upper column.

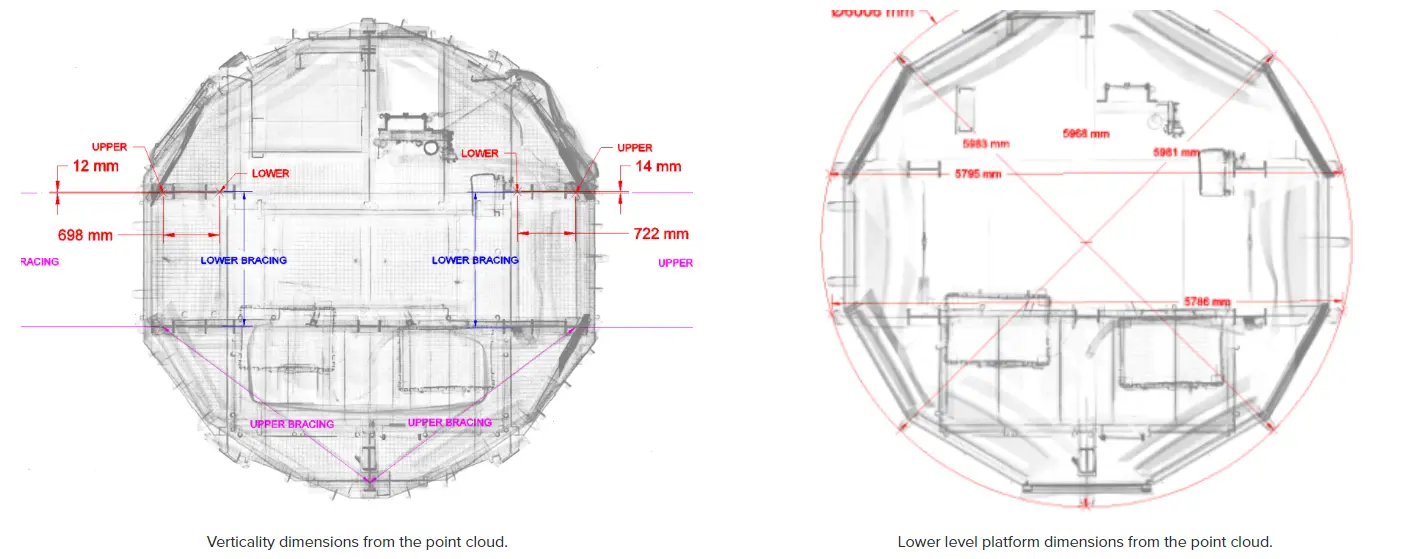
What Did the GPRS Mapping & Modeling Team Provide the Client?
To provide all the data the clients needed in an accessible format, the GPRS Project Manager laser scanned the fixed-bottom monopile concrete foundations and the substation topside steel platforms. Then, the Mapping & Modeling team compared that dimensional information in areas specified by the design engineers against the models. After reviewing the design engineer’s reporting requirements, GPRS created custom written and drawn reports. Those reports included a write-up detailing the scanning process, a summary of the data analysis, dimensional calculations, engineering drawings and 3D models to illustrate the findings for each concrete foundation and steel platform.
How Does Component Verification Eliminate Rework and Clashes?
Verifying the dimensions of prefabricated components helped to ensure a smooth construction process for offshore wind turbine installation. Verification can reduce delays, clashes, change orders, and other unforeseen challenges for the technical team during installation. By using 3D laser scan technology to verify that the dimensions are in accordance with plan, project risks are mitigated, and labor hours are saved. Crews can confidently place the prefabricated components on the vessel and ship them out to sea, knowing they will fit and perform as needed.
How Many Wind Farms Are in Operation in the U.S.?
As of 2021, there were two operational offshore wind projects in U.S. waters with a total of seven turbines. The Block Island Wind Farm off the coast of Rhode Island became operational in 2016 with five turbines that generate approximately 30 MW of energy. The Coastal Virginia Offshore Wind pilot project — a 12 MW wind farm off the coast of Virginia — became operational in June 2020 and consists of two turbines. Although there are currently seven turbines in U.S. waters, there are 20 proposed offshore wind projects in various stages of development.
How Are Wind Farms Expanding the Construction and Engineering Industries?
There are several offshore wind farms under construction in Rhode Island, Massachusetts, and New York. On July 5, 2023, the Biden-Harris administration approved another major offshore wind project in New Jersey. According to the U.S. Department of the Interior, “the New Jersey wind farm project will have an estimated capacity of 1,100 megawatts of clean energy – capable of powering over 380,000 homes – and is expected to create more than 3,000 good-paying jobs through development and a three-year construction cycle.”*
3D Laser Scanning for the Renewable Energy and Utility Industries
Verifying the critical dimensions of components to ensure a more efficient project with the flawless installation of prefabricated parts are some of the many reasons GPRS Visualizes The Built World for clients in the green energy and utility industries.
Wind, solar, and other renewable energy solutions are generating more opportunities across the engineering, design, and construction sectors. GPRS provides the accurate as built and prefabrication data required for design planning, and the dimensional verification needed to minimize risk, ensure flawless installation, and jobsite safety.
GPRS Project Managers complete roughly 2,500 renewables jobs a year. Whether you’re installing a solar panel, installing a new EV charging station, constructing a wind farm, or renovating an existing structure, GPRS works tirelessly to deliver accurate data for your project. From the renewable energy industry, to power plants, to industrial facilities, and more, our services aid in the planning and efficiency of many industries for construction, renovation, inspection, installation, and maintenance.
Learn how GPRS 3D Laser Scanning services can verify the critical dimensions on your next project to Intelligently Visualize Your Built World™.